Introduction: Make a Truncated Icosahedron Out of Wood
Welcome to my very first Instructable! Here you will learn how to make a truncated icosahedron (soccer ball) using a table saw to cut the parts with. This setup will let you make very precise beveled convex polygons that can be as small as a coin, or larger up to several inches and could be scaled larger if desired. The precision is top notch thanks to the digital microscope which allows the pattern lines to be adjusted with a hair-splitting level of precision before making each cut. The bevel angles can also be made very precise by using this method to construct a bevel gauge. The patterns for the polygons are printed onto permanent labels, so the resulting pieces are as accurate as the printout (which I assume is very high). I have experimented with different methods of adhering the pattern to the wood and I get the best results using permanent labels. They already have the adhesive so there is nothing that happens between printing and adhering that can shrink or distort them.
This technique is definitely one of those, "why didn't I think of that" kind of things. The simplicity of aligning a single point with the edge of the cut is what makes it work so well combined with the magnification provided by the microscope. Watch the video first, and this will all be easier to understand.
I chose the truncated icosahedron because it is an efficient shape to make a sphere from, but you can also make other polyhedrons with it if you know the measurements for each of the pieces. The truncated icosahedron has two polygon shapes, regular pentagons (12), and regular hexagons (20). Each of the two shapes has a different bevel angle, 16.4722° for the pentagons, and 20.9052° for the hexagons. I went ahead and made it into a sphere on my lathe, but that of course is optional.
Supplies
Tools:
1. Table saw with blade suitable for compound miters.
2. Saw to separate the pieces (hand saw, scroll saw, band saw, etc.).
3. Thickness planer. (Or you can use good quality baltic birch plywood)
4. Drill with various bits.
5. ¼-20 threaded tap.
6. Countersink bit.
7. Printer for printing patterns onto full sheet labels.
8. Scissors
9. Other various shop tools you probably already have (hack saw, screwdrivers, file, grinder, etc.).
10. Digital microscope preferably with built-in screen. This increases precision at least an order of magnitude making this project feasible with excellent results.
Materials: For the table saw sled:
1. A piece of ½” x 18” x 9” Baltic birch plywood for the base. Could also use mdf or other sheet material just as long as it is very flat and stiff.
2. A piece of aluminum plate. I used a piece measuring 3/8” x 6”W x 8”L. Dimensions not critical as long as it's big enough for the clamp and has enough area for the size parts you want.
3. A toggle clamp, plywood spacer to elevate clamp, mounting screws with matching drill and tap.
4. 1.5” thick construction lumber. A piece of 2x4 will be just fine.
5. ¼-20 machine screws with countersink heads.
6. (2) 4” or longer ¼-20 carriage bolts.
7. Wood screws.
8. Spray adhesive.
9. Small piece of coarse sandpaper around 2” square.
10. ¼” flat washers and nuts.
For the coarse reticle:
1. ½” plywood or regular wood. Dimensions or type are not critical.
2. Thin kerf 7.25” blade.
3. Clear colorless glass or plastic.
4. Permanent marker.
5. (2) Carriage bolt and matching nut.
6. T-bolt to fit miter groove of saw. Or make from 5/16” carriage bolt and washer.
7. Diamond bit with sharp edge, piece of fine steel wool (if using glass for reticle).
8. Wood block sized to fit in holder.
For the microscope:
1. T-bolt, nut, washer, or make from 5/16” carriage bolt and washer.
2. A small piece of ¼” plywood same size as microscope base.
3. A short board roughly 2" x 10" with center hole for T-bolt.
3. Clear tape.
Step 1: Making the Adjustable Sled
The table saw sled for this Instructable rides along the fence instead of the miter groove in order to be able to adjust the gap between the edge of the sled and the blade as the bevel angle is changed. I made the clamping portion of the sled out of aluminum so if it accidentally contacts the blade it will be far less likely to cause damage compared to a steel clamp plate. I also decided it was necessary to use the metal plate because the clamping force of the toggle clamp would be enough to warp the base plate if made without the metal plate - and that would mess up the bevel angle among other things. The long edge of the aluminum plate that runs along the blade should be beveled 45° to maximize the support area under the polygons being cut. This is best done with a band saw, but can also be cut with table saw if you have a blade for aluminum. Make the cut in two passes with the first pass cutting almost through the plate so the second pass will have very little metal to remove, and throw fewer hot sharp flakes of aluminum towards you. Wear goggles and a face shield as well as long sleeves.
The aluminum plate will be attached to the base along the middle of the long edge as shown in the photos after the holes are drilled and tapped, see photo for measurements. Drill the aluminum plate with 13/64" holes, then clamp the plate in position on the base and drill through the base using the holes as a guide. Remove the plate and re-drill the holes in the base with 1/4" drill and then countersink the holes on the bottom surface for the machine screw heads. Thread the holes in the aluminum plate with 1/4-20 tap. Alternatively, you could skip the threading of the holes and just use nuts instead.
Adjust the toggle clamp for longest reach and mark the mounting screw locations while the rubber tip is about an inch from the beveled edge of the plate as shown in photos. Drill and tap the holes for mounting the toggle clamp according to the size of the screws you will be using (I used #10 screws with allen head screws, but 1/4-20 will probably fit too. Again, you can skip threading the holes and just secure with nuts. This would require making a hole through the base for access and clearance.
Glue down a piece of coarse sandpaper under the rubber tip of the toggle clamp with spray adhesive. The sandpaper should extend all the way to the beveled edge (overlap the edge, then tear off excess). Attach the toggle clamp with four screws and a plywood spacer, trim the screws so the ends will be flush with bottom of metal plate. Attach aluminum plate to base with machine screws inserting a flat washer between the plate and base on each screw. Finally, trim the screws to be flush with top surface of aluminum plate. The washers create a small gap between the plate and the base to allow for any warping of the metal plate from the force made by the toggle clamp without affecting the base.
Make the threaded wood blocks from wood that is 1.5" square and around 5" long. Pre-drill and countersink two holes through the base for wood screws that will hold each threaded block. The edge of the threaded blocks should be about 1.25" from the right edge of the base. Drill a 3/16" hole horizontally through each block near the top surface, these are the holes for the adjustment bolts. The adjustment bolts are the 4" long 1/4-20 carriage bolts. I chucked a piece of 1/4-20 threaded rod into a drill to form the threads in the undersized hole. Do not use a tap for threading the holes or it will be too loose, the adjusting screws need a little bit of friction. Screw the carriage bolts into the blocks with the round bolt heads facing the saw fence. Screw the bolts in all the way and bend an inch of the ends 90° to form handles. Clamp the threaded blocks onto the base and secure them through the bottom side with countersunk wood screws. Remember the bottom of the base most be flat without any protrusions.
Make the adjusting feet from 1" x 1.5" wood about the same length as the threaded blocks. Drill a vertical 1/4" hole through one of the ends of each for a 1/4-20 machine screw that will serve as a pivot point. Drill 1/4" holes through the base and countersink for the screw heads. Put the feet on the pivots and gently secure with a washer and nut. Put a small wood screw into each foot and threaded block with heads protruding to stretch a rubber band across to serve as a spring holding each foot against the head of the carriage bolt adjusting screws. The feet will then pivot in and out with the adjusting bolts and touch the fence creating a gap between the fence and the edge of the base. There should be enough adjustment between the two feet to rotate the sled a few degrees in relation to the fence.
Step 2: Make the Coarse Reticle and Holder
The coarse reticle is used to roughly align the pattern lines close to parallel before going under the microscope for the fine adjustment. The fine adjustment will be done with the two adjusting bolts on the sled under the video reticle of the microscope.
The reticle holder I made is a partial box made of baltic birch plywood fitted into dado grooves cut into the base board. The sides of the box have thin grooves for the glass reticle to have a sliding fit in. When the bevel angle of the saw is changed, the coarse reticle will need to move sideways to re-align with where the blade path intersects the top surface of the wood being cut. The reticle holder adjusts with a bolt that pushes a wood block that butts up against the edge of the glass. The end of the box with the bolt going through was made as part of the base, and then cut off after the dado grooves were cut. The bolt goes through a nut that is pressed into a hole that is larger than the flat-to-flat dimension of the nut, but smaller than the corner-to-corner dimension. I drilled a shallow hole to loosely hold the end of the bolt in the end of the wood block.
For the reticle itself I used a piece of glass from a cheap picture frame I picked up at a dollar store. I cut the glass to approximately 2" x 5" (measure the distance between groove bottoms of your holder for the exact width), the width should be wide enough to reach the front and back grooves of the holder, but not fall out. Once it's in position the clamping bolt can be tightened gently to pull the sides against the edge of the glass to hold it firmly in place. There are multiple grooves spaced 1/4" apart so the glass can be positioned just above the wood being cut however thick it is. To make the line on the reticle drill a 1/8" hole into the edge of a piece of wood. Insert a 1/8" shank diamond bit with a sharp edge into the hole, it should be a snug fit. The edge of the wood rides on the edge of the glass as the diamond bit scratches a line into the glass parallel to the edge the same way you'd use a marking gauge. The line should be a dashed line, and positioned about 3/16" or so from the short edge. Now use a permanent marker to blacken the scribed line, and then remove the excess ink around the scratch with fine steel wool. The diamond bit is pulled out some in the photo for clarity. You can also make the coarse reticle from clear plastic instead of glass if you prefer. Use a sharp utility blade to make a light dashed scratch.
Make a slot in the base of the holder for a T-bolt to clamp the reticle holder to the saw table. A T-bolt can be made from a 5/16" carriage bolt and a washer. The hole in the washer should be a little too small to fit over the square portion of the bolt under the head. Use a chainsaw sharpening file to make two dents 90° apart inside the washer hole so the square portion will be a press fit into the washer. Tap the square portion in on an open vise to seat the washer under the head. Grind or file the dome of the head until it fits in the T-slot. Make another one for the microscope clamp in the next step.
Step 3: The Microscope.
This handy device has a built-in screen and a metal base and support. There are two screws on the bottom of the base that attach the column to the base. Remove the screws and rotate the base 180° and reassemble so the support arm is opposite from the base plate. There are four rubber feet on the base - remove them and attach a piece of 1/4" plywood cut to size to support the scope and allow the screw heads to protrude without touching the table (or just flip the base over and put the rubber feet on the top side). Make a simple clamp to hold the microscope in place on the table using the T-slot. Drill a hole for the T-bolt in the center of a piece of wood approximately 10-12" long. Use a small piece of wood as a spacer on top of the base so pressure from the clamp presses against the center of the base instead of the edge.
The microscope needs to be protected from sawdust. cover the aperture with a piece of clear tape along with any other holes on the back of the screen. I bought the cheaper version which is adequate for this application, but the screen is not very good because it doesn't have a wide viewing angle. The microscope can be connected to a PC for a much better image and you can turn on the cross hairs (reticle) in options. It can also connect to your smartphone through wifi, but I couldn't find an option to have a reticle on my iphone. The microscope can be powered with an external battery with usb port, but the internal battery is good for 4 or 5 hours of use.
Step 4: Polygon Stock Preparation, and the Hold-Down Shoe.
Before you setup a precise bevel angle you should cut the wood that the polygons will be made from. I recommend using wood that is at least 3/8" thick for the included truncated icosahedron patterns. The patterns are arranged on the page to make (3) 11 inch strips of hexagons, and (2) 11 inch strips of pentagons. The wood for the hexagons needs to be at least1.5" x .375", and the pentagons need wood that is at least 1.25" x .375. Be sure to surface both faces with a thickness planer. All of the wood should be the same thickness. Choose wood types with contrasting colors, I used maple and walnut. Print the patterns on a sheet of permanent label paper, cut the label into strips along the length, and stick the patterns onto the wood. Use a saw to separate the pieces, and remove any splinters or fuzzies from the bottom surface.
Make a "shoe" from hardwood to place between the wood and the end of the toggle clamp. The heel of the shoe should be just a little taller than the thickness of the wood. This piece of wood will not damage the label, and makes it easier to clamp the small pieces without having to be directly under the tip of the toggle clamp. Make sure it does not extend past the edge of the aluminum plate while in use. The wood pieces must sit perfectly flat on the sandpaper lined aluminum plate. The bottom side of a clamped piece of wood is the inside surface, it will become smaller than the top side as the bevels are cut so it's important that the clamp pressure is over the center of the piece. Also realize that thicker wood will produce polygons with a smaller inside face.
Step 5: Making a Bevel Angle Gauge
Now that the sled, coarse reticle, and microscope clamp are made it's time to make a bevel gauge. The gauge is made the same way that the polygons will be cut in the next step, except the bevel gauge is cut with the blade square to the table. Print the patterns and gauge onto label paper and use scissors to cut out the pattern for the gauge and apply it to plywood or whatever you want to make it from that is a little oversize compared to the pattern lines of the gauge. It's very important that the gauge and all the pieces cut for the truncated icosahedron are made from wood that is flat and uniform thickness. Download the two PDF files above. One is the bevel gauge, and the other is the polygon patterns.
Set the saw blade square to the table and move the fence to the left far enough so the aluminum edge is about 1/8" from the blade, and the two adjustments on the sled create a gap between the fence and the base around 1/4" wide or so. Clamp a piece of wood onto the sled and cut it to establish where the edge of the blade is, do not release the clamp. Slide the sled back so the cut piece is near the rear edge of the saw table closest to you. Position the coarse reticle on the cut edge and clamp the reticle holder down and tighten the reticle clamp screw so it won't move if bumped. this sets the coarse reticle. Now slide the sled forward to the microscope and turn the microscope on and focus and set the magnification level. I use the highest magnification level that gives a clear image, and lower the microscope as close as I can to the wood and still have clearance for the toggle clamp. Position the video reticle on the cut edge. Slide the sled back and forth, the cut edge should stay aligned with the video reticle. Tighten the clamp that holds the microscope in place. If this causes the video reticle to move, then tap the edge of the microscope base with a wrench or small hammer to re-position it. This sets the microscope in position. Now you are ready to make the cuts for the bevel gauge.
Move the sled back to the coarse reticle and put the wood with the gauge pattern on the sled and line up the first line with the line on the reticle and clamp it down with the toggle clamp. Move the sled forward under the microscope and observe the position of the line as it is slid back and forth under the video reticle. It will probably move side-to-side from one end of the pattern line to the other. Loosen the adjusting screw on the end of the sled that is left of the video reticle, and tighten the other screw to put the reticle back on the pattern line. Check the side-to-side movement again as the sled is moved back and forth, if you adjusted correctly, then there will be less movement side-to-side. Continue adjusting until the pattern line stays centered under the video reticle as it is moved back and forth. When that is achieved, make the cut. Cut a little bit into the line and back out just to make sure the reticle is exactly on the cut. Complete the cut and then align the next pattern line with the coarse reticle the same way as before. Continue with the rest of the gauge cuts.
After making several cuts you might notice a trend in the adjustments you make while aligning each cut. One end of the sled might get moved farther than the other and you’ll need to re-center the adjustments from time to time. This can be reduced by adjusting the coarse reticle. If the leading end of the sled moves farther left than the trailing end, then adjust the coarse reticle clockwise. If the trailing end of the sled moves farther left then adjust the coarse reticle counter-clockwise. Don’t make too much adjustment at once. With the bevel gauge completed, it’s time to make two test cuts to set the first bevel angle.
Set the bevel angle of the saw to the angle for the hexagons (20.9052°) with whatever you normally use to set the angle. Make a pair of test pieces and cut an edge on each piece using the sled. After cutting the first piece, slide the sled back to the coarse reticle to realign it, and do the same for the video reticle as well. Place the two pieces on the gauge on either side of the "6". The goal is for the bevels to touch without a gap while the test pieces are held flat against the gauge edges as shown in the drawing. If there is a gap at the inside of the joint, then decrease the bevel adjustment of the saw. If there is a gap at the outside of the joint, then increase the bevel setting. Continue adjusting until you get a perfect fit, and then reset the reticles. Once the angle is set, you are ready to begin cutting hexagons.
Step 6: Cutting the Hexagons.
Now that you have set the bevel angle (20.9052°) for the hexagons, it's time to start cutting them. There is an order to which edges are cut first, you want to rotate the piece clockwise after each cut, and the first cut should be across the grain. This will keep any chipping as the blade exits the cuts on the waste portion of the wood. After cutting five hexagons you can do a test fit by taping them together along the outside surfaces with edges touching and corners aligned into a circular arrangement. This will fold up to form a flattened cone with a space in the middle for a pentagon. If all has gone well it should be a good fit where the ends meet. Continue cutting the rest of the hexagons. After they are all cut then set the bevel of the saw to the angle for pentagons (16.4722°). Repeat the procedure for setting the bevel angle with the angle on the gauge marked "5". By the way, the angle of the gauge = 180 - (2 * bevel angle).
Step 7: Cutting the Pentagons
With the bevel angle set for pentagons, and the reticles adjusted to align with the new bevel angle, cut the 12 pentagons with the last cut being along the grain. Test the fit by dropping into the test ring of hexagons. If all went well then it should be a good fit and the edges should line up with the surrounding edges. Now it’s time to tape all the pieces together as a flat net.
Step 8: Assembling the Flat Net
Tape the outside face of the polygons into lines of 2 hexagons and 1 pentagon as shown in the picture and add an extra pentagon to 2 of the lines on the opposite end from the other pentagon. I normally leave the labels on the polygons and use Scotch Super Hold tape. Tape the lines together to form the net. It will be quite floppy so handle it with care. I made a different net in the video, but I think the one shown here is the simplest arrangement. Carefully do a dry fit test to roll it into a ball not only to check the fit, but also to make sure the net is assembled correctly. None of the pentagons should be touching another pentagon. Now unfold the net and prepare to glue the polyhedron together - the fun part!
Step 9: Gluing It All Together.
For gluing polyhedron assemblies this way I recommend using a glue with a long open time such as Tightbond 3 in the green label bottle. You will also want to have a roll of stretch-wrap ready, it is a perfect way to hold the polyhedron together as the glue sets. Finally you'll want to have a large rubber band to wrap over the stretch-wrap. If you have ever wrapped a rubber band a few times around your fingertip, then you have an idea of how much pressure a larger band can put on the ball - a lot! It's important to wrap the ball evenly. Have you seen the crazy video where people are stretching rubber bands around a watermelon and it finally implodes cutting the melon in half? Yeah, let's not do that here. You have a lot of time invested in this project and we want to see a good result.
Step 10: Label Removal and Finish Options.
After the glue has set after several hours or overnight, it's time to unwrap the rubber band clamp and the stretch wrap from the ball. That's easy enough to do, but the labels need to come off too so we can see how it looks underneath. My new preferred method is to use a wire-wheel in a bench grinder, it does a great job without any harsh chemicals. Be sure to wear safety glasses because they do sometimes shed metal bristles while in use - the last thing you want flying at high speed anywhere near your eyes! The wire-wheel makes fast work of removing the labels and the sticky residue from the adhesive. There is an alternative of using rubbing alcohol or nail polish remover (acetone).
Now the question is if you want to finish it with flat faces, or turn it into a sphere on a lathe? I think both options look good. Perhaps you should make a second one so you can do both? I have other polyhedron designs available on my website.
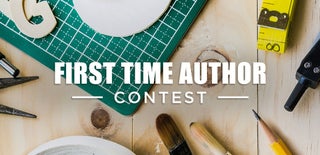
Second Prize in the
First Time Author Contest