Introduction: Make the Stargazer Viking Chair
There are a lot of different versions of the stargazer/viking chair. We fell in love with the design about a year ago and thought that we would take the time to make one (or two) of our own and add our own unique spin to them. The things you might find different in our design is the fact that both seat and back are made using two sections of 2x6 pine each. Rather than solid width lumber, we used separate pieces and glued them into a panel. One other thing that may be unique to ours is the crown that is carved into the head of the back panel and the burnt, weathered and battle-worn look. Other than that, it is a pretty straightforward design and a ton of fun to make.
What we used:
- (2) 2x6" pine (8 feet long)
- Glue
- Tools (table saw, band saw, jigsaw, jointer, clamps, drill, sander, rasps, torch)
- Finish (medium colored stain, dark stain, wipe-on polyurethane)
Make sure you check out the video, it shows a bit more of each step than the images do. Please enjoy and if you make it or something like it, we'd love to see it. Share it with us on here or on Facebook, Google+, etc.
Step 1: Prepping the Boards
Here are the dimensions for the cross cuts.
(2) at 46" (for the back)
(2) at 14" (for the seat)
(1) at 40" (for the seat)
Each of these also got ran through the jointer so we could get a good glue-up. The final width of each one after going through the jointer on both sides was approximately 5".
Step 2: Cutting Bevel for the Seat
On the two shorter boards (14"), before the glue-up, we cut a bevel. This will vary depending on how much you would like the chair to lean back. The best way we found to determine this was by setting up two of the longer boards from the back at the angle we thought we would like and then setting the angle on the bevel gauge. Then we just transferred the angle to the shorter boards. The table saw can then be adjusted and the ends cut off.
Step 3: Seat Glue-Up
This is a really easy step. You could use biscuits or some kind of floating tenon or even dowels in this glue-up, but we decided to just go with a straight edge-to-edge glue-up. We've been using the chairs for about 2 months now and we haven't experienced any splitting at the seams yet. Of course, do what you feel comfortable with. Make sure you use lots of clamps.
Step 4: Making the Back
Taking the two longer boards (46") that we cut, we began to assemble the back. Before gluing these together we did a lot of different stuff. First, we marked out the notch where the seat will slide though. Since we are doing a glue-up it is much easier to mark these out now and cut them separately. This notch begins 11" from the bottom and needs to be cut large enough so that the 40" board that was cut earlier will slide through with ease. Before cutting the notch out, we also marked a "fancy" design on the top that will be translated to both sides. Then, we cut the top piece off on both sides using the band saw.
Step 5: Cutting the Notch for the Seat
The notch was a little bit trickier to cut out, since we couldn't use the band saw, because the boards were too long. So, we drilled two holes at the corners, cut it out with a jigsaw and then cleaned it up with a chisel.
Step 6: Back Glue Up
This glue-up is similar to the first one. We made sure the notch was lined up perfectly and used lots of glue and clamps.
Step 7: Adding Curves to the Seat
To make the seat a little more comfortable we rounded the corners. We also made the rounding a little wavy to give it a little bit neater of a look. We cut one side off and then transferred the shape with that cut-off to the other side. This was all easily done on the band saw.
Step 8: Smoothing Up the Edges
Just so the chair would be a bit more comfortable, we routed the edges with a roundover bit. We also did the same inside the notch for the seat.
Step 9: Carving a Design Into the Back
To make our chairs a little more unique or personalized we decided to add a design near the headrest area of the back. This was just a simple crown design we found online. I carved this into the back using a rotary tool and a bunch of different bits for it. I wasn't too concerned with how nice of a carving this turned out to be and you'll see why in the next few steps. I just made sure I carved it pretty deep.
Step 10: Distressing Part 1
We wanted to make the chair look like it was distressed or battle-worn actually. To achieve this, I started by beating up the edges with a rasp using some controlled chaos. There was no rhyme or reason to how this is done. I just scuffed it, gouged it and generally beat the crap out of it until I was happy. This was done on both the seat and the back and then it was sanded smooth, leaving as much as the wear and tear as possible.
Step 11: Distressing Part 2
For no other reason than us thinking it looks cool, we decided to burn a good portion of the chair. Especially the crown. For this step we just had fun with it. We think burning it leaves a really cool "old" effect to it once it is sanded and finished.
We also hit it with a log chain a few times to add some dents and scuff marks. Then the whole thing was sanded again, but only lightly in most areas; a little more near the crown carving. This left the crown looking like it had been worn away over time.
Step 12: Stain & Finish
Lastly, I haphazardly added a medium colored stain and once that was done I spotted and streaked it with a darker stain. Once the stain was dry, I hit it with a bunch of coats of wipe-on polyurethane.
Step 13: All Done!
That's it. It really is a simple project. Depending how detailed you want to get with any carvings or distressing techniques, this project should only take about a few hours to maybe a day's time. They are a lot more comfortable than they look. That is probably one of the things we were most surprised with. We had initially set out to make these just because we thought they looked cool and would be great to have around a campfire, but now they are our go-to chairs whenever we are outside relaxing.
We hope you enjoyed this DIY project and the video that goes along with it. If you have any questions or comments please let us know, we'd be more than happy to help you out. Thanks for checking out this Instructable.
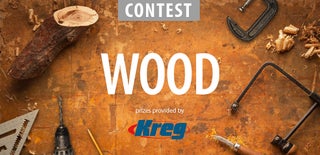
Participated in the
Wood Contest 2016