Introduction: Making Dementia Puzzles for My Dad
I wish I could say that my dad was always there for me when I was a kid, but the fact is he wasn't. The reason why was because he was busy "being there" for others. He, and we his family, spent 21 years in the military. So he was gone at times. The Air Force sent him to Japan shortly after WW2 and it was a while before it was considered safe enough for us to join him there. So before I was even in preschool I was an international traveler. And then there was the year he was stationed on the DEW line, north of the arctic circle helping to man the radar stations that were there watching for anything that might try and sneak in from over the north pole. This was before there were satellites that could do the job from space. When we were stationed in Hawaii I remember the worry he was showing during the Cuban Missal Crisis. He was getting ready for all out nuclear war and it was a real possibility that his family had no future at all. So he wasn't always there for me, because he was busy being there for everyone else. Lately I keep hearing news stories about how important it is to support the families of the military personnel who are deployed. It's something I know pretty well because it's how I grew up. I think we moved every 2 to 3 years. For me that meant new schools, new friends, new cultures, new climates, new adventures. It's how life was for us.
But now time has taken its toll, and the ravages of old age have set in and my dads mind is slipping. Dementia is defined as: a general term that describes a group of symptoms-such as loss of memory, judgment, language, complex motor skills, and other intellectual function-caused by the permanent damage or death of the brain's nerve cells, or neurons. Dementia can affect people of any age. Brain damage from accidents is included in dementia as well as Alzheimer’s, which is another form of dementia. My dad does not appear to have Alzheimer’s, but he is loosing his battle to something that is causing his mind to deteriorate. This project, this instructable, is designed to try and help make what time he has left a little more enjoyable.
My dad has always loved woodworking and when I showed him my 3D floor project he was fascinated by it. I took him a bunch of pieces and wood samples and printed out the instructable for him and we sat on his floor and laid out patterns. He loved it. But for me the reality is that he will never get to see it other than in pictures because he can't leave where he is. So I decided to do the next best thing and make him a set of pieces for his own. He can't work with tools anymore, let alone a saw but he can still enjoy wood. This instructable is what has evolved over the last half year of putting this together.
This is a four part instructable. If there is a particular part that you are interested you can jump to that "step".
The first part is a little history, some more about my parents and how my dad got to where he is today. I don't often share private information but this time I think it is necessary.
The second part is a project on different types of wood. I call it "know your types of wood" , sort of a take off of David Letterman's "know your cuts of meat" that he used to do. I used ten different woods for the dementia puzzles project.
The third part is about making a wall plaque that is for hanging on the wall where my dad is.
And the forth part is about making the actual puzzle pieces.
Step 1: History
When I was a little boy my dad gave me a new leather belt. He said that everyone should have a good leather belt, it could come in handy sometimes and maybe even save your life. It was quite a few years later before I really understood what he said. Among other things my dad was a tail gunner on a flying fortress in World War 2. His turret was hit by shrapnel and pretty much shredded. To survive he strapped himself to what was left of the seat with his leather belt. Its what held him in there until the mission was over. So his belt saved his life. He made sure I had one too. So my dad was one of what they now call "the greatest generation". He fought in Europe and besides the purple heart for nearly getting his ass shot off he was awarded the Distinguished Flying Cross and a bunch of other medals that as a kid I thought looked really cool.
He met my mom in Italy on the isle of Caprice. She was not Italian, she was a WAC in the 5th Army. My mom was born and raised in Hawaii and after Pearl Harbor she was one of the first women from Hawaii to enlist. She ended up in Italy where she eventually met my dad.
One night the barracks my mom was in caught fire. She was the first one to discover it but the last one to get out. She got all the other women up and moving to safety first. The barracks collapsed as she left. She ended up with pretty bad smoke inhalation and singed hair and had asthma for the rest of her life because of it but no one died. She was awarded the the Bronze Star as a result.
So my mom was a war hero.
After the war they got married and mom raised kids while my dad continued his career in the Air Force. And like I said we moved all the time. I eventually had 4 sisters.
Dad retired from the service and joined the corporate world. He lived what most would consider to be a pretty normal life and he and my mom did pretty good for themselves. They stayed fiercely independent for most of their lives.
TO BE CONTINUED ----
I have to get this posted in time for the woodworking contest and everything is finished except for this so I will finish this story in the next few days.
Step 2: Know Your Types of Wood
When I first started developing this project I thought it would be a good idea to use a lot of different types of wood. The more variety, the greater the mental stimulation I thought. So I put together a list of all of the woods that I could use. I wanted to restrict it to mostly hard woods since they are often more durable and finish better. I compiled samples of them and while doing that it dawned on me that I should make a type of key to help in identifying each wood. If I made sample sticks of each one and then labeled them it would make it easy to compare the sample to whatever wood the puzzle piece was and match them up. This way even if someone forgets what kind of wood it is they can refresh their memory with a sample stick, an key to what wood is what. "This is Oak, or this is Ash."
The woods I used are Ash, Elm, Cedar (the only soft wood), White Maple, Buckthorn, Crab-apple, Birch, Mulberry, Oak, and Russian Olive. Ten woods altogether. The pictures show 12 because I use 2 elm and 2 ash.
I have had some fun with these since I finished them. Up until now no one has been able to get all ten types of wood correct. I lay them out on a table with the name side down and then let people try and identify what wood they are. The easiest is usually Oak since most people have seen that. When they guess one right I flip it over and they see in big letters what it is. Then I give hints as to what the ones left are. For instance I divide them into woods that grow here and are common in everybody's yard. Finally we get down to the few exotic ones and we flip those over so they can see what they are. Nobody guesses the Buckthorn or the mulberry, nobody has ever seen the wood from them. So its a little game, "Know your types of wood".
By the way, I have been using pieces with things like knots and bug holes and burl when I find it. Since these don't need strength or consistent clear lengths I can make use of wood that sometimes would be considered as scrap. I think it adds a lot of character to the samples.
Step 3: From Scratch (logs) Again
In my original floor project I started with my own wood from my trees. In order to get all the varieties of wood I wanted for this project I started the same way since many of these woods are not available unless you DIY. Some of the woods are from local trees and some are from other parts of the country that a friend of mine has brought to me to try working with. The oak that I used came from a few large solid oak pallets, that is the only dimensional wood that was used in this project. Because I decided to go with 3/4 inch instead of 1 inch I was able to use smaller branches than I did previously. Again the plainer played a very important part.
If you want to try a project like this you can use standard wood that you can buy or even salvage. it would make the work easier if the lumbar is already dimensional wood. But you will probably not be able to get the variety of woods that I used here.
To plane a small branch that rolls around you can screw a 2x4 to the bottom to hold it steady while going through the planer. Once you have a flat side you can remove the 2x4 and plane that side so you have 2 parallel flat sides.
Step 4: A Video of Processing an Ash Log
Step 5: Processing Stickes
After cutting the various logs with the table saw down to their final dimensions for the sample sticks I processed the sticks into the finished pieces. I decided to cut a notch along each edge so the pieces would overlap when lined up together. I figured it would also make them easier to pick up out of the box.
I used a router to cut the notches along the top and bottom edges. I cut the sticks down to the finished length so they were all uniform in length.
In order to identify each type of wood I used a stencil and wrote the name of each wood on them. Then using a Dremel and a router adapter I carved out the letters so each stick had the name of the wood engraved into it.
Finally I used wood putty colored with food coloring to fill in the engraving and then sanded it down.
I tried adding sine sawdust from the sander to the wood putty to give it color but the results were not that great. I also added glue to the mixed putty along with water. I have no idea if this helped, it just seemed like a smart thing to try. I thought the glue would help the putty stay in the engravings better. I think it did. Using food coloring is interesting. Since the putty is on the yellow side to start with you are not really sure what your end color is going to be. I was looking for anything that would be a contrast to the wood.
Using a belt sander I rounded all the edges so there were no sharp edges or corners. I wanted to make the samples as safe as possible,
Step 6: A Box to Go.
I applied several coats of finish, sanding with progressively finer grits in between coats. The final sanding was with a 600 grit wet/dry paper which gave the sticks a very smooth finish that is feels good to the touch.
I needed a box to keep all the wood samples in. I decided to make one of oak out of the same reclaimed flooring that I used in my socket caddy project. The oak was already prepared so it made things a lot simpler. There were several reason for choosing the oak. One was its durability. It is strong enough that it should survive being dropped. The box itself could even survive being used a a stool so it would protect anything inside. I made it with no lid so it is always open and I made it just high enough so that the sample woods are not sticking out the top. So, my hardwood sample have a hard wood box that they fit in with just enough room to get a finger in to lift the sticks out.
I carved my name into the bottom and filled it with wood putty so there can be no doubt as to who its owner is.
Step 7: Edited --- Added Step About Measurements and Dimensions
A question was asked about the sizes of the pieces I used and I realized that I had not really gone into very much depth about that in this instructable. I did show some of the geometry in another instructable related to this one. Anyway, this is an added step so that if you want to make anything like this you can easily figure out the dimensions.
First you only need one standard measurement. Everything else is determined from that. I used 2 inch wide, 3/4 inch thick sticks. I cut everything to that initial size. You do not have to use 2 inches, you can go either bigger or smaller. I used that size because it looked like a reasonable size for hand held pieces. It was also the size I had used for another project and it worked well. If you go with a different width all the other dimensions will change accordingly. It's geometry.
In the first picture you can see that the block's width is 1/16 of an inch short from being 2 inches. I started with 2 inches but then sanded the sides because they were rough and I lost 1/32 from each edge. As long as they are all the same size that is fine.
For the diagonal cut line you make a line at 30 degrees from the edge, off of a 90 degree perpendicular line. This is the angle you need to cut in order to get the diamond shape. The length of that line, once cut, is determined by the width of the board. That length becomes the measurement down the stick to the next cut. So you don't really do any measuring, you just mark it based on the diagonal cut length since both the diagonal and the side are equal length. This makes things pretty simple as you can mark it on the cutting jig and then just mass produce the diamonds. If you want to use a different width board then this length will change. All the other pieces that are cut smaller are derived the same way. A triangle is just a diamond cut in half. The smaller rhombus pieces were difficult to get the right size to cut but that is because you have to accommodate the kerf of the saw, the amount of wood the blade will remove to make the cut. To get those just right I traced it all out on paper first and then cut the paper out with scissors and put the cut paper pieces on top of the diamonds to get the exact size. It took a few trials to get it correct on the saw but once the width was established I cut them all the same.
It is very important that you get the angle correct. If you are off by even a little the pieces will not all meet in the middle. If you sand them you have to be careful that you only take off a little. On the pieces that were going to be glued together I didn't sand them at all since it didn't matter if the edges were rough and it made sure the angle didn't change.
Step 8: The Wall Plaque
The last time my sister and I visited my dad we put up a large assortment of pictures for him. His room was pretty bare and we wanted to make it more attractive and homey for him. So we mounted a lot of old and new pictures on poster board along with descriptions written underneath them and mounted them to his wall for him to enjoy. We went over them with him and he did really well remembering them all and in fact corrected us several times when we made mistakes as to what car was what. A few months later we found out that all the pictures had been taken down. And they disappeared. We believe one of my sisters was behind it and although she did not take the pictures down herself it appears the staff did at her request and they gave everything to her. Hard to believe someone could be that petty. Anyway, as part of this project I decided to make a large wall plaque that I could screw into the wall so it will be very difficult to remove. It can't be inadvertently taken down. In addition to adding something nice to his room to look at it will also serve as a template to the puzzles. A guide as to some of the things he can do with them.
While doing some research into the rhombus tilings I discovered another tiling that would work right into my project. Geometry is just amazing.
The thing that is the most impressive to me is the 3D look that emerges when you use different colors of wood. And there are many patterns that can be made.
So the basic shapes that everything keeps going back to are the rhombus, the Equilateral Triangle, the trapezoid and the hexagon. Each hexagon can be divided into 3 rhombus. Each rhombus can be divided into 2 triangles and each triangle can be divided into 3 trapezoids. And each trapezoid can be divided into 3 triangles. So each rhombus can be divided into 18 triangles. Getting a headache? I can show you on the wood itself.
By the way, the finished wall plaque is 23 inches from point to point so its almost 2 feet across.
Step 9: Making Smaller Sticks and Trapezoids.
One really nice thing thing about this part of the project is that I was able to get use out of some sticks that were too small for my regular rhombus pieces. I had a pretty good collection of wood that was not usable for my other pieces. I was able to salvage much of it by making smaller pieces.
I made a simple modification to my jig that I used for cutting rhombus pieces and was able to mass produce trapezoid's.
One very important thing to keep in mind. Your pieces need to be pretty close to exact in order to get them to come together correctly. I cut a lot of test pieces to make sure the jig was just right. And then in the cutting process I had to be careful to always have the stick in the correct spot. If a piece was cut to short it was scrap.
Step 10: Some Assembly Required.
After you get all these little trapezoid's cut you have to turn around and glue them back together, just not in the same way they were. I tried a number of patterns but finally settled on both the types of wood and their arrangement.
If you want to get lost in some examples just go to this Google image search and look around.
If that doesn't work then you can copy it here,
https://www.google.com/search?q=Rhombille+tiling&tbm=isch&tbo=u&source=univ&sa=X&ei=48cjUpbiO6uisASF7YGgBg&ved=0CD0QsAQ&biw=1440&bih=662#facrc=_&imgdii=_&imgrc=VXqoMyWqO2fihM%253A%3BYo_PYaJO0o_cLM%3Bhttp%253A%252F%252Fen.wikipedia.org.advanc.io%252Fwikipedia%252Fcommons%252Fthumb%252Ff%252Ff2%252FDelos_cubic_floor_mosaic.jpg%252F220px-Delos_cubic_floor_mosaic.jpg%3Bhttp%253A%252F%252Fen.wikipedia.org.advanc.io%252Fwiki%252FRhombille_tiling%3B220%3B165
The particular 3D looking pattern I used has been used in quilting. There are a number of them in this book of quilting patterns.
http://quiltwithmarcibaker.com/projects/abc-3-d-tumbling-blocks-and-more/#prettyPhoto
The problem with wood is once you glue and clamp stuff together its pretty much for good. I did make a number of mistakes that I had to scrap. Make extra certain of your layout before you spread any glue.
It is possible to make this particular pattern from the triangles, however there are 2 different patterns required if you do it that way. I found it easier to make the diamonds instead since they are all the same. Far less mistakes that way. And since my gluing jigs could make a rhombus from the individual trapezoids in one shot it was the most practical way to do it. Even after the diamonds were made I found I could make them into 2 different configurations.
Step 11: Glue and More Glue.
I recently posted another instructable on custom gluing jigs. Those are the jigs that are used for this project.
https://www.instructables.com/id/Making-and-Using-Custom-clamping-jigs/
That instructable explained it pretty good.
Basically now you get into a rhythm of gluing, clamping, waiting and starting over. The larger the finished plaque the more rhombus you need to make.
Step 12: Gluing Lines
After you get a bunch of diamonds glued you can start on assembling them into lines. I made another gluing rig for doing this. Trying to glue rhombus together is a puzzle. As soon as you try and clamp them they slide. So this jig is made to hold them in a line while applying pressure so they will line up correctly.
No matter how accurate your cutting was you are going to end up with edges that are not flat. I suppose if you wanted to get this pattern correct with no mistakes the thing to do would be to glue it all up at the same time. Have a hexagon clamp to apply pressure to all sides at the same time in all directions. But then you would need multiple hands putting glue on all the pieces at the same time so you could get it ready to clamp before any part dried. Well, that is beyond my current capability, so I glue one line at a time.
I used a belt sander in a stand to smooth down the edges and get them flat so they will line up correctly to the next line of blocks. This was a process of sand a little, match it up, sand a little more. I held the parts together and up to a light to see what areas needed a little more taken off, marked it with a pencil and sanded down the high spots. Doing it this way I got the lines to match with almost no gaps in them. Then it was a matter of gluing the lines together. This took regular clamps to do with additional clamps holding it to the table top so it would stay flat. I didn't need any curl in my plaque.
When it was all glued up I had the inner part of the plaque done. I sanded it down with a belt sander and filled any gaps with wood putty and sanded it again. Then I used a 12 inch Sliding miter saw to trim the edges to make them flat. They were close but there were a few irregularities.
Step 13: Borders
I wanted this to be fairly large so I added a border around it of rhombus pieces. I laid it out on the floor and tried a bunch of different combinations. Have darker wood at the points made the entire thing appear darker. I tried a number of different wood but finally settled on a combination of ash, russian olive and buckthorn.
Gluing the border together proved to be a lot more difficult than I thought. To get everything to line up I used a slot cutter bit in a router table and cut a notch all the way around the inner piece. Then I cut a notch into each rhombus piece so they would all match up. I used my gluing jigs and put the border together a few pieces at a time until I had just 3 main parts. Amazingly they actually fit together to form the border and fit around the center, almost. I had to use a file to make some fine adjustment and in a few places I had to cut some slivers to fill small gaps. It was a lot of work but I was happy with the end result. The final gluing was held together with pipe clamps and the outer edges were also clamped to the pipes to keep it all flat with no bowing.
Step 14: The Frame
I needed a frame to go around the entire thing. This would make it easy to hang on a wall. I chose to make it out of ash wood, a really hard and very nice looking wood. I had several sticks left so I didn't have to make anything special for the frame. In addition to making it easier to hang on the wall if it fit flush to the wall then it would not be possible to get a grip on it and pull it off the wall. The plan is to locate the wall stud, drill a hole through the top point and bottom point of the plaque and screw it directly to the wall. Once flush to the wall it will not be possible to get behind it and pull it off. I will put a couple of plugs over the screw holes to discourage anyone trying to unscrew it.
Once I picked out my frame pieces I routed a channel in them just the size of the edge of the plaque. I was going to use glue only to attach the frame so in addition to alignment the channel provided more gluing surface. I then fit and marked each frame piece and trimmed them to 30 degrees. Using pipe clamps I did top and bottom at the same time. Then another 2 sides and finally the last two. I cut the last pieces longer than they should be and then trimmed them a little at a time until they fit into place. If you cut them to much you have to start over if they don't fit.
Rather than leave a sharp flat edge I wanted to rout it to something more attractive. I experimented with several different bits and finally decided on a simple rounding over cut. It looked nice and had a nice feel to it. Not complicated but also not looking unfinished.
Once it was completed I applied the finish. There are many coats on this, I lost track of how many. I just kept sanding and finishing until it developed a totally smooth surface. I used wet/dry sandpaper of 400 and 600 grit. When the 600 gets worn down its actually a finer grit and acts like a polishing rather than a sanding.
I was pleased with the overall results, it looks really cool, but it really took a lot of work.
Step 15: The Puzzles ---- Starting With Sticks
I used the same technique here as I did for my floor project except I an using 3/4 in thick boards. In addition because the pieces that I will use are going to be finished on all sides I need to have wood that is good on both sides. I went through the whole process of cutting down logs and branches into smaller sizes until I got the dimensions I was looking for. I made stacks of the wood layered by wood type. I made sure that everything I used was dry. In fact I laid many of the rough cut pieces out in the sun for a month or so to make certain it was not green wood anymore.
After making the final cuts I sanded everything with a belt sander and then put a coat of finish on everything to keep the wood from getting any stains as I work with it. In the end I had quite a pile of sticks from 10 different woods.
Step 16: Cutting - Making Rhombus and Triangles
Using my table saw with my jig I cut a lot of diamonds.
Note ----- If you do this save the end pieces because I used most of them either for making gluing jigs or for the storage trays.
Another note --- I did so much cutting and planning that I doubled my normal electric bill.
Step 17: Making Hexagon's and Stars
Rather than just having a bunch of small pieces I decided to assemble some of them into pre made hexagon's and stars. This would help if my dad was not sure about how to put things together. Also having premade pieces there are more possible combinations.
To make these involved cutting slots in them with a slot cutter and then using a spline to join them. Being done this way makes them a lot stronger since the glue joint is reinforced. I used the clamping jigs, a lot of glue and ended up sanding them down and refinishing them so the first coat I put on was a bit pointless. But I didn't know I was going to assemble any of them when I was cutting sticks. This project evolved a lot in the year that it took to do.
The stars were probably the hardest pieces to make since they involved 3 different gluing sessions.
The little trapezoids were another after thought that turned out really well.
I made some large hexagon's with the small trapezoid from the wall plaque part of the project. I really liked the way they looked. They give ideas as to some of the possibilities.
Step 18: The Trays for the Puzzle Parts
In trying to figure out a way to store the rhombus pieces I hit on the idea of using trays. These don't hold as many pieces as storing them another way but they do make them more portable since you can carry the entire tray or even several trays. In addition because of using the end cut off pieces it is not possible to put the rhombus or triangle pieces in wrong. They only fit one way and so it will eliminate any frustration that could be caused by them not fitting.
It could be said that the trays are over built because the bottom is solid oak. Perhaps, but they won't break if dropped on the floor. Besides I had the wood leftover from making the box for the sample wood sticks. The sides are made with laun plywood that I doubled so it should hold up to abuse. I sanded all the edges down and rounded all the corners. And by the way since the trays are coated with multiple coats of floor finish they should be able to be washed with no effect.
Step 19: Organizing a Tub to Hold It All.
I bought a nice size plastic tub to hold all the pieces. With a locking lid it can be carried with out everything falling out. However it is pretty heavy so I look at the tub as mostly storage convenience.
I put a piece of paneling on the bottom to keep the bottom rigid. Then I glued some nice wide wale corduroy to the board so there is a nice cushion effect. Everything is removable from the tub including the bottom piece. I tried out the fit of all the parts and decided on a way of dividing it up. Setting this tub up actually took me a lot longer than I thought it would but I was really happy with the results. I am going to tape a picture of the box contents to the lid along with the number of pieces of each. This way it will make it easy to put it all back together if it is dumped out. With many of the pieces they will only fit one way. For example the stars will only fit in the space made for them. The trays with the other parts fit on top of the dividers.
The dividers were made with plywood that was sanded and then notched to fit the cross piece. it is a simple yet elegant way to make dividers. You cut a notch in each about half way and then slide them over each other. I ran beads of glue along each joint to eliminate and splinters and to make the dividers rigid. They had to be rounded on the bottom to fit in the tub.
Step 20: The Possibilities Are Endless
After making the frame for the wall plaque I had some left over scraps. It dawned on me that I could finish them and use them as stands for some of the hexagon's. Cool, yet more pieces to play with and you can make your own display.
Sitting down with this big variety of pieces it seams like there is no limit as to what you can do with it. One of the really nice things is there is no wrong way to put any of it together. Whatever you do is great, its just up to your imagination.
And then after I thought I had finished I had yet another idea and made some large trapezoids with the triangles I had made. I didn't want to include the small trapezoids because they were to small but one of the really cool things about this is that its all made to the same ratio. So half a rhombus makes a triangle, 3 triangles make a trapezoid and 3 trapezoids make a triangle, only on a bigger scale and your back once again to your starting shape.
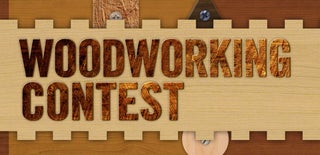
Grand Prize in the
Woodworking Contest
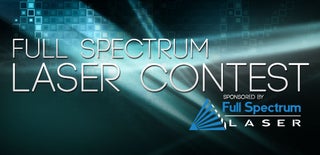
Participated in the
Full Spectrum Laser Contest