Introduction: Making a Medieval Sword
Hello everyone,
we had a Medieval party planned and i had no weapons that fit my outfit. I thought I could make a sword myself. As you can see that ended up better than expected. But after some thinking in the end i left it at home, I didin´t belief that it was a good idea to take a sharp sword to a party full of drunk people ( me included) when i don´t even have a sheath to put the sword in. It just shouted ill-considered ideas.
but now i have one
I have tried to make it with as few professional machines as possible so that everyone can do it. The only thing that may be a problem is the fuller. I did it with a milling machine, but there is a flap disk that is made to grind out round shapes, same as the milling machine. But this process takes a lot longer to finsh. Alsow you will need to place conduction bars with clamps to make sure that the fuller is one straight line.
Step 1: Making the Blade
Required materials:
-iron bar 9x60x990mm
-large angle grinder
-small angle grinder
-flap disc grit 120 ( for small angle grinder)
-disc pad holder ( for small angle grinder)
-disc pad grit 80-120-320 ( for small angle grinder)
-cutting wheel 0,8 (for small angle grinder)
-metal grinding wheel (for large angle grinder)
-measuring tool
-marker
-2 clamps
-milling machine
Step1: Drawing the shape of the blade on iron bar
The knife itself is 40mm wide, if you have an iron bar with the correct dimensions you will have to grind less. I did not have the right size, so I had to cut the shape out off the bar i had.
The dimentions of the blade are 800mm long, 40mm wide. The handle is 190mm long and 18mm thick.
Draw this shape on the iron bar.
Step 2: Milling the fuller
Now you know where the blade begins and ends. Put the bar in the vise on the milling machine and mill the fuller in the bar. It should start 40mm above the handle, finish 50mm for the top and is 4mm deep.
On the side of the handle the mill should gradually decrease from 0 to 4mm in depth over a length of 15mm. On the topside it decreases over a length of 30mm. ( picture 1)
Step 3: Cutting out the shape of the blade
Take your small angle grinder with the 0,8 cutting wheel and cut out the shape of the blade. ( picture 2 and 3 )
Make sure that the line of the cut is straight or this will present problems in the future when you grind the cutting edge.
Now cut out the handle part. (picture 14)
Step 4: Grinding the cutting edge
Now take the 2 clamps and the sword and clip it on the work table, make sure that half of the blade is outside the work table. This will make it easier to grind it in one smooth movment. Take the large angle grinder with the metal grinding wheel and begin to grind the slanted side of the cutting edge. Try to do this as even as possible. (picture 4-5-6) Don´t form the point yet because you will have no space to clamp the blade down.
Take the small angle grinder and the disk pad holder with a 80 grit disk to level the cutting edge.(picture 10) If you move the grinder from left to right like picture 11 all the smaller bumps and dents will come flattend. Do the same with the disk pad grit 120 and 320.
The advantage of using this machine is that you don´t have to worry that the disk changes shape after long time use. You can just change the disk pad and the shape stays the same. (picture 7-8-9)
Now it's time to shape the point, begin at the end of the fuller and grind it towards a point. (picture 12) Now grind the slanted side on the topside and make sure that the fuller and the 2 slanted sides are all in one line to the point. (picture 13)
Round off the eges of the handle (picture 14) excepted the 20mm where the guard is going to slide over.
Step 2: Sanding the Blade
Required materials:
-sandpaper grit 320-500-800-1000
-block of wood
Step 1: Sanding
Wrap the sandpaper around the block of wood so you have a flat surface and begin sanding the blade. Begin with grit 320 and move your way up to grit 1000. If you want to go higher until it looks like a mirror it's possible but for my intentions this was good enough. This will take a while if you want to do the job right but the result will speak for itself.
Step 3: Making the Guard and the Pommel
Required materials:
-iron bar 20x20mm
-small angle grinder
-flap disc grit 80-120-220 ( for small angle grinder)
-cutting wheel 0,8 (for small angle grinder)
-measuring tool
-marker
-2 clamps
-bold M6 20mm
-screw tap M6
-drill 5mm
-drill 9mm
-drilling machine
-square file
-hacksaw
-vise
-centre punch
Step 1: Make the square hole in the guard
Take the hacksaw and cut of a piece from the iron bar, with a length of 190 mm. Now draw the square hole in the middle on the iron bar. ( the dimensions are on picture 1) Put the piece in the vise and drill 2 holes in the iron bar. ( picture 2 )
Put the iron bar straight in the vise ( picture 3 ) and take the square file and file from the one hole to the other. (picture 4) This will probably take a while ... if you are almost at the shape that you want. Begin to check if it fits over the handle of the blade. (picture 5) It must be a tight fit or it will rattle. Now it fits perfect over the handle (picture 6)
Step2: Shape the guard
Take the iron bar and draw the shape with the marker. (picture 1) Clip the iron bar on the worktable with the 2 clamps and take the small angle grinder with the flap disc grit 80 and begin to grind out the shape. The reason why we use this type of flap disc is because we can work with it in a bend. If you are approximately 0.5 mm from the shape begin to change the flap disc grit to 120 and on the end grit 220.
Step 3: Drill the hole in the pommel and handle
Take the hacksaw and cut of another piece from the iron bar, with a length of 65 mm. Measure the middle at the top of the iron bar and hit it with a centre punch. Do the same with the handle. (picture 7) Now drill a 5mm hole in the middle and tap thread in the holes with the M6 screw tap. (picture 7) Take the piece, draw the shape of the pommel with the marker.(picture 8) Grind out the shape with the small angle grinder and the flap disk grit 80. Repeat the same process from the guard and change the flap disk to 120 and 220 at the end. Now the 2 pieces are ready. (picture 9) Take the M6 x 20mm bold and grind of the head and glue it with sealant in the pommel. (picture 10) It was not necessary for me but if you want, you can polish the pieces until they shine like a mirror.
Step 4: Making the Handle
Required materials:
- piece of wood 150 x 200 x 15 mm ( i used paduk)
-T-square
-marker
-chisel
-wood saw
-hammer
-Electric Wood Planer
-wood glue
-clamp
-sanding paper grit 80, 120 and 220
-sander
-vise
Step1: Making the basic shape
Saw off a length of 195 mm from the piece of wood. (picture 1) And then saw out 2 40 mm pieces. (picture 2) Now draw a line 12 mm form the 2 sides now take the wood saw and make a cut of 9 mm deep. (picture 3) Put the pieces of wood in the vise and use the chisel to chop the strip out. (picture 4) Make sure that you test the 2 combined pieces on the handle part of the blade. The best is that they are a little bit tense to slide over. So if you want show off your sword and start swinging around, it doesn`t rattle like a chinese fake. Now glue the 2 parts together and put 2 clamps on them. Make sure that the excess glue is removed from the inside or you will have issues fitting the parts together. (picture 5) Let it rest for a day.
Step 2: Finish the final shape
The guard is 20 mm thick so the handle must be the same thickness or a little smaller if you want to wrap the handle with leather. The piece is now 30 mm thick so we need to reduce 5 mm on both sides. Draw 2 lines on the 2 sides and put the piece in the vise. (picture 6) Take the electric wood planer and shave off small stripes untill you reach the thickness you need. (picture 7) Now take the sander and sandpaper grit 80 and begin to make the handle smaller to the end. ( picture 8) We need to get to 20 mm because of the dimensions of the pommel. Round off the edges so that the handle is pleasant to hold. (picture 9) Now sand off the handle to 191 mm, I like to have some extra material in case something goes wrong. Take the sanding paper grit 120 and sand the whole piece and do this again with grit 220. You can varnich the handle or wrap it with leather.
Step 5: Assemble the Parts
Take all the finished parts and put them together. I made the handle 1 mm longer than needed so when you screw on the pommel it press everything together so nothing rattles.
Remember everthing is made of iron so it will rust, put some oil on it and don´t touch it with your fingers.
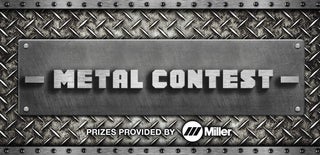
Participated in the
Metal Contest 2017