Introduction: Making a Wall Hanging Brass Mechanical Alarm Clock in the Home Machine Shop
This build is for a weight driven verge and foliot alarm clock based on plans by John Wilding. The plans and materials can all be purchased from Ian T Cobb's website www.clockmaking-brass.co.uk
Like many people I was captivated by Clickspring’s videos of his clock project, so I decided that I would try my hand at making a clock myself. This is the end result. What you see before you took about year of evenings and weekends tinkering in the garage.
The plans for making this clock describe it as ideal for a beginner, which is perfect because that’s exactly what I am.
With the exception of the bell and the chapter ring (i.e. the dial with the numbers on it) I made all the parts of this clock from raw metal stock.
This clock has a verge and foliot escapement using double escape wheels (more on this later). This is one of the earliest known type of mechanical escapements and is rarely used in modern clocks due to its startling inaccuracy.
Most of the parts for this clock were made using my Axminster SC4 lathe (a rebranded SEIG SC4) which I got second hand on ebay. Prior to buying this lathe I had zero machining experience, so there was a very steep learning curve.
The build log for this clock, along with more photos can be found on instagram under my username "thonemeister"
Step 1: The Workshop
This is where the magic happens. My workshop pretty small; just a single car garage, half of which is taken up by a motorbike. I moved into this house about 5 years ago with zero tools and ever since have slowly been building up my tool collection. Having ogled over lathes for years I finally pulled the trigger on a second hand Axminster SC4 in September 2016 for about GBP900, making it by far the most expensive tool in my workshop. The lathe came with some tooling, but I also had to purchase a vertical slide (second hand on ebay, approx GBP70) to complete the clock.
The only other power tool I would say is essential for this build is a drill press. My little drill press was GBP70 from LIDL. Whilst it won’t win any awards for power or accuracy it does the job well enough. Other than these, a few simple hand tools are all that’s required. I warn you though, clock making definitely isn’t a cheap hobby. While basic tools are all you need there are plenty of less basic (and more expensive) tools you’ll definitely want.
Other tools include:
- Small drill press
- Scroll saw (because I got lazy. The project could have been finished with a hand held piercing saw)
- Dremel (useful but not essential)
- Hand held power drill
- A selection of drill bits (I bought a set of drill bits from 1mm - 13mm in 0.1mm increments)
- Various BA grade taps and dies
- Abrasives
- Swearing
Step 2: The Plans and Materials
The plans I was working from came as a spiral bound book. One of the best decisions I made during this build was to scan the book and print another copy to have in the workshop. The workshop copy is now filthy with oily fingerprints and scribbles in it, whereas the original is pristine. Having a digital copy also meant I could look through the plans while I was at work (when I was meant to be doing something more productive) and plan my evening's activities. Scanning the book page by page is a royal pain in the arse (especially when the scanner times out half way through and you have to start over) but a good time investment in the long run.
Also shown here is how it all began; a selection of unpromising looking raw materials. These materials and the plans were purchased from Ian T Cobb (http://www.clockmaking-brass.co.uk/), with a various other bits and pieces coming from ebay.
I've attached a list of the materials required for the clock. This list allows extra for making mistakes along the way. It is taken directly from the plans so there were a few changes I made along the way. Brass is expensive so I would estimate that all the materials for the clock came to approximately GBP300.
Firstly, the list calls for the arbors to be made of mild steel, but I decided to use silver steel instead. Silver steel is slightly more expensive, but it's much more dimentionally accurate and withstands corrosion better.
I couldn't find a weight tube with the exact dimensions called for so I did some maths, and bought the closest size I could find which would give the same weight when filled with lead. Just remember that the weight end caps need to fit on the ends, so don't buy too large an outer diameter.
The plans call for various dimensions of brass blanks (i.e. brass discs). You have two choices here; either buy a sheet of brass and cut out the blanks yourself, or buy the blanks pre-cut. I did the latter, and bought the blanks from Ian T Cobb.
Attachments
Step 3: The Plates
The first step of the construction was to make the plates. These are made of 1” x 1/8” CZ120 brass flats. One of these is covered with layout fluid, and the hole positions and shape marked out with a ruler, scriber, and compass. The two plates are clamped together for the pillar holes to be drilled. They are then bolted together ready for cutting.
The shape of the plates is purely decorative. Bolting together the plates means they are both exactly the same shape and, more importantly, means any future holes we drill will be parallel. These were cut out using a piercing saw, (a saw with a very fine blade used by jewellers. The blades on these saws are very prone to snapping, especially when cutting thicker material, so this process can be quite frustrating.
I later realised that the reason they kept snapping all the time was because I’m an idiot. I had bought the finest grade of blades available which are designed for cutting very thin sheet metal, not 1/4” thick plate. When I later purchased some appropriate sized blades it made the process a lot easier. Don’t be an idiot; buy the right blades for the job.
The fresh cuts are jagged, so need tidying up with files and abrasive paper.
Step 4: The Cross Strut
Next to cut out was the cross strut, again made from 1/8” brass. The hole positions and shape were laid out using engineers' blue. It was cut out with the piercing saw and finished with files and abrasive paper. The picture also shows the piercing saw; this saw became my arch nemesis during the build.
By the end of the build the cross strut has lot of holes drilled in it. I marked these all out at the start, but only drilled the holes as and when I needed them to ensure they were in the right position.
Step 5: The Cross Strut
There are quite a few parts in this photo which I don’t have photos of making so let me paint you a picture with words.
Firstly, the pillars. These are made of 1/2” square section brass and are 2” long. First a section of brass was cut to approximate length by hand then mounted in the 4 jaw chuck on the lathe. As we are just facing the ends I made little effort to ensure they were properly centred. Both ends were faced to make sure they were perpendicular to the sides, marked out with layout fluid, the centres found (by simply drawing a cross), centre punched, and drilled in a drill press.
They were mounted between centres on the lathe and a shoulder turned on each end to fit into the holes on the plates. Finally the holes were tapped. The plans called for BA4 threads but at this point I didn’t have BA4 taps or dies, so settled for M3.
This is something of a theme throughout the build; whenever I didn’t have the right sized tap, die, drill, reamer, etc I improvised and made do with what I had. This worked out well but requires some careful planning to make sure changing the size of a hole now won’t have repercussions later on.
The two pillars are identical, except that the top pillar has holes to mount the bell standard and for the foliot to pass through. In the photo you can see that a) I haven’t drilled these holes yet (but they are marked out and center punched) and b) I’ve put the pillars on the wrong way round.
The screws shown in this picture were quickly turned out of aluminium (aluminum to the Americans reading this). I knew that these screws were going to be taken off many times over the course of the build so I wanted something easy to undo by hand.
The cross strut has been mounted to the back plate. This is held on by a single screw in the centre and two steady pins to stop it spinning. This is also your first glimpse of my tidy, neat, and organised work space.
The steady pins shown in the photo are used in mounting the cross strut to the frames (and at various other stages throughout the build). They are slightly tapered pins made of either steel or brass. They are fitted by drilling a hole through the cross strut and frame. The hole is opened out into a taper using a broach, which is a hexagonal tool that is put through the hole and spun by hand, removing a small amount of material. The pins are then driven into the holes.
In the photo of frame on the wall we can see a few more new parts I don’t have photos of; namely the U shaped bracket and support spikes.
The support spikes are made of steel which was faced, drilled and tapped 6BA in one end, and the other end tapered to a point. Care is taken to make sure these are exactly equal length. These mount to the cross strut with screws.
The U shaped bracket is made from 1/4” brass. The U shape is cut out with our old enemy the piercing saw. Each leg is then drilled and tapped 4BA. The top of the curve is drilled and tapped as well. The plans call for 5BA but I only have even numbered taps, so settled for 4BA. A hook is then screwed into this hole. The hook was made from 1/8” steel rod; more on this process later. The U bracket and hook assembly is attached to the back plate.
The whole thing then mounts to the wall using the hook. The length of the hook can be adjusted so the plates are hanging vertically.
Step 6: Wheel Cutting
Next up is onto the wheel cutting. The photo shows the finished wheels, which are by no means perfect (one of teeth on each wheel is notched where I didn’t index correctly) but do the job.
When cutting wheels there are two main challenges; getting the right tooth profile (i.e. the shape of the tooth) and indexing (i.e. spacing the teeth accurately). Clocks traditionally use a cycloidal tooth profile as opposed to the involute tooth profile found in a lot of machinery. This is partly because cycloidal gears have less sliding friction, suffer less wear and are easier to achieve higher gear ratios with, but also largely because of tradition. This clock is no different; I’m using a cycloidal tooth profiles and lantern pinions.
The correct tooth profile is achieved by using the appropriate cutter, in this case module 1. This was one of most expensive tools I had to buy for this build. This little cutter alone cost about GBP80. One of the reasons I chose this clock to build is that it only requires one cutter; other clocks required multiple cutters, which gets very expensive very quickly. It is possible to make your own gear cutters, however for my first clock I wanted the accuracy of a shop bought cutter.
In order to use the cutter I made a mandrel. The hole in the centre of the cutter is 7mm, so a 7mm spigot was turned on the end of the aluminium rod. The spigot was then drilled and tapped and a retaining washer and bolt put in place.
The wheels themselves are made from 1/16” x 2 1/4” diameter brass blanks. These are centre drilled in the lathe, and mounted in another homemade mandrel. Both wheels are made at the same time, so are mounted together on the mandrel. After this point they aren’t removed from the mandrel until they are finished. The mandrel is mounted in the lathe and the blanks turned down to the outer diameter specified in the plans.
While still being held in the lathe a line is scribed outwards from centre of the wheel. This will be used to align the cutter in the next step. Once this is done the mandrel is removed from the lathe and transferred into the vertical slide. The slide is fitted with clamps at the top and bottom (again, homemade) which the mandrel fits in to. The position of the clamps and mandrel are then adjusted using a dial indicator to ensure it’s vertical.
The line we scribed earlier is used to ensure the cutter is centred on the wheel. If the cutter isn’t centred the teeth will be wonky. I centred this by eye and by zooming in using my phone. Once I was happy the cutter was centred I locked the carriage into position.
In an ideal world the wheel would be indexed using a rotary table. Unfortunately I don’t own one, so I had to improvise. The photos show my ghetto wheel cutting and dividing rig. These wheels have 48 teeth, so using an online tool I printed a circle divided into 48 sections.
I printed this as big as the printer would allow and glued it to some card. I made an extension which screws into the top of the wheel mandrel and the indexing circle sits on top. A scriber is then mounted to point to a line on a circle to indicate the position.
I made a mistake here because as shown in the photo I initially put the pointer on the top of the headstock. This meant that as I adjusted the depth of cut (see below) the dividing circle moved relative to the pointer, resulting in the “chipped” tooth. For subsequent wheels I mounted the pointer on the cross slide, meaning it was stationary relative to the dividing circle.
Not shown here is the method for establishing the depth of cut. Layout fluid is put onto the edge of the blanks, and an initial cut is made at approximately the right depth. The wheel is turned to the next tooth and another cut made. Now examine the tip. If there is layout blue showing on the tip of the tooth (and there should be on the first cut; if there isn’t you’ve gone too deep) increase the depth of cut slightly using the cross feed and make another pass.
Repeat this, gradually increasing the depth each time until the layout blue just disappears. Now lock the cross slide in position.
The rest of the teeth are cut in one pass. The procedure is to cut the tooth, stop the lathe, loosen the clamps holding the wheel mandrel, turn the wheel until the next line on the dividing circle lines up with the pointer, re-clamp the wheel mandrel, start the lathe, and repeat.
Once the teeth were cut the wheels were crossed out. This involved marking out the material to be removed, cutting it away using piercing saw, then filing and papering the cut edges to make it neat.
These wheels have curved spokes rather than the more traditional straight spokes. The author of the plans suggests doing it this way as it’s more forgiving than straight spokes. With straight spokes it’s obvious if the sides aren’t parallel, however with curves when you inevitably bugger it up it’s harder to notice. I’m glad I did it this way, because cutting and filing neatly is a lot harder than Clickspring makes it look.
Step 7: Ratchet Wheel and Pulley Assembly
Next to make is the ratchet wheel. This is what lets you wind the clock (by lifting the weight back up) without the clock running backwards. Because the spacing on these teeth aren’t mission critical I used an even more ghetto method of dividing.
Once the teeth are marked out they are cut using the piercing saw and filed and papered to a good finish.
The pulley assembly is made up of the hub (shown here), the ratchet wheel, and two flanges. When the clock is in operation the rope goes over the top of the hub between two flanges (imagine a yoyo).
To give the rope something to grip onto, the hub is fitted with 6 spikes. These were fitted by dividing the hub (again, doesn’t need to be accurate), drilling holes towards the centre, then hammering in short spikes. I used panel pins for the spikes here, but anything short and pointy would do the job. The gif (if it works) shows my first attempt at making the hub which, for reasons I’m not sure of, wobbled more than Santa Clause’s belly. I had to remake it.
Step 8: The Click and Clickspring
The small piece is the click; this is what catches the ratchet teeth to ensure it only turns in one direction. This was made from a 1/8” silver steel strip.
Cutting this out was a nightmare, and made me hate the piercing saw even more. Silver steel is supplied in a soft annealed state, and can later be hardened. Unfortunately being soft doesn’t mean it’s easy to cut, and I very quickly gave up with the piercing saw; it just wasn’t up to the job. I ended up using a regular hacksaw, brute force, and a lot of swearing. It was then tidied up with files and abrasive paper.
It is around now that I started getting lazy with photos, so let's talk about a few components I haven’t mentioned yet, namely the great wheel, and click spring.
The great wheel was made in the same way as the previous wheels; the teeth (72 this time) were cut and it was crossed out.
The click spring was cut from 1/16” brass strip. It is initially cut straight then carefully bent to match the profile of the wheel.
It’s attached to the great wheel using a screw and a steady pin. Once the click spring is fitted to the wheel, the position for the click is determined. It needs to be positioned so the click spring pushes down with enough force to make it engage with the ratchet. Once the position is determined the hole is drilled and tapped, and a straight shank screw is made to attach it.
The great wheel it permanently bonded to the arbor using Loctite. The pulley assembly is mounted on the same arbor but is free to move to allow the clock to be wound. It is stopped from sliding along the arbor using a steady pin.
Step 9: Escape Wheels
My lazy photography streak continued, so there are no photos of making the escape wheels. These are made in a similar way to the other wheels, except instead of using the tooth cutter shown above I used a slitting saw in the lathe. A slitting saw is just about the scariest cutter you can attach to a lathe! This was used to make 15 radial cuts (divided using the same ghetto dividing system as the teeth).
Only the flat faces of these teeth are critical, so the other curves were then cut by hand using the piercing saw. The wheels are crossed out, fitted to a hub, then all held together with three screws. The centre hole of the hub is drilled and reamed to 1/8”.
Step 10: Pinions
Next up was making the pinions. This clock uses lantern pinions which are made using blued pivot steel. These have a couple of advantages over leafed pinions; they’re easier to make, are easier to repair if worn and, most importantly, don’t require you to buy another expensive cutter.
This is the way I made the pinions. First I turned the pinion blank from 7/16” bar stock using a parting off tool then drilled and reamed to 1/8”.
To drill the holes for the wire I used a Dremel flex shaft held in a quick change tool post holder. This was set to the right pitch circle diameter (i.e. distance from centre ) by first positioning it centrally, then using the hand wheel on the cross slide to feed it out the correct distance (being wary of backlash).
I attached an indexing circle to the face of the rod using double sided tape and positioned a pointer. To make the holes I drilled straight through the indexing circle and the blank, turning the chuck by hand for each hole.
This method wasn’t actually very good because there was too much play in the flex shaft and, because the drill bit was so small (1.1mm), it wandered and didn’t drill straight. Despite many (many) failed attempts at making pinions I finally got some which were good enough. Some of the failed attempts have now been converted into cufflinks for a buddy of mine.
One of the pinions is flat on both ends and the other has a small spigot on one end used to mount it to a wheel.
Step 11: The Escapement
Again, a few pieces that I didn't take photos of when making.
Firstly the verge support arm. This was cut to shape from a piece of 1/16" brass strip and holes were drilled to mount it on the plates and to accept the verge end bearing. I then bent it round a 1/2" diameter former (I used a piece of brass rod) and a twist added so it is flat underneath the verge.
The verge end bearing was turned from tool steel and a 10BA thread added. It was hardened by heating to a cherry red and quenching, then polished and attached to the verge support arm.
The pallet is the heart of the clock. It is the piece that drives the oscilliation from the escapement wheels. This was marked out onto 1/16" tool steel, the centre hole drilled and tapped 10BA and finally cut out and filed to shape.
Marking this out was actually quite challenging, as it is a very small piece and the instructions were not clear. Tapping the 10BA hole was nerve wracking, because the tap is very small, and the metal quite hard. I took it slow and steady with lots of oil, and fortunately didn't break any taps.
The verge arbor was simple to make; the end of a piece of 1/8" drill rod was turned down to take a 10BA thread, and the tip of the thread polished.
Now these parts are made we finally get to see how the escapement works. The escape wheels turn (powered by the weight) which makes the pallet oscillate back and forth. The rate of oscillation is dictated by the amount of weight powering the clock, as well as the amount of weight on the foliot.
The foliot was cut from 1/16” brass, and the notches added with a triangular file.
The weights are made up two parts. The first part is just a piece of brass round stock cut to length. The other is the hook which joins it to the foliot. The plans call for this to be cut from 1/16” brass, which then has a threaded section cut with a die. I tried this and the bit I tried to thread just snapped off each time. I settled for simply gluing it on to the weight with Loctite which worked a lot better. The distance these weights are set from the centre determines how fast the clock runs. The closer to the centre the fast it goes.
Step 12: The Weight and Weight Pulley
The weight pulley is made up of 4 parts: the stirrup, the screw, the bearing, and the pulley wheel.
The pulley wheel was made from a 3/16” x 1 5/8” die brass blank. This was mounted in the lathe and centre drilled. It was then held in the wheel cutting mandrel in the lathe and the outer diameter turned. The groove for the cord was cut using a homemade round end cutter in the lathe. The decorative holes are drilled in the drill press and recesses on either side of the pulley cut on the lathe.
The stirrup was cut from a flat piece of 1/16” brass using our old friend the piercing saw, tidied with a file, then bent round a 1/4” former.
The bearing is simply a piece of 3/16” steel rod drilled through the centre. The pieces are then all assembled into the delight you see before you.
The main driving weight for the clock is fairly simple to make.
It’s based around a 1 1/2” OD brass tube. Two end caps are machines from 3/16” blanks to fit snugly into each end of the tube. A steel centre shaft is faced on the lathe, then one end is drilled and tapped 4BA, and a 2BA thread is cut on the other end. One end of this is screwed to the bottom end cap, and a weight hook is made to screw to the other end of the shaft.
The mass of the weight is provided by casted lead. First the inside of the tube and the shaft were lined with a couple of sheets of printer paper. The bottom end cap was fitted and the tube was held upright in a bucket of sand. Some scrap roofing lead was melted using a camping stove and a blow torch then poured carefully into the tube and left to cool.
Once cooled the paper lining the tube allows the freshly cast lead to be easily removed. This means the weight can be changed if necessary. I used about 3.2kg of lead (I don’t know what that is in freedom units, sorry) which is too heavy for the clock, but easy enough to cut down.
Obviously working with lead is not without its risks (especially when heating it) so I wore welding gloves, a face shield, and respirator. PPE is important! If you're not comfortable casting lead then it would also be possible to fill the weight with lead shot.
Step 13: Get Impatient, Buys Tools.
Over Christmas my piercing saw broke (possibly as a result of being thrown out a window in a fit of rage when yet another blade snapped) so I decided to upgrade and get a scroll saw. My life is now complete.
Step 14: Alarm Work
Now we have completed the main driving mechanism of the clock we can move onto the alarm work. The alarm is activated by a pin on the alarm setting disc (which hasn’t been made yet) lifting a lever at the front of the frame. This in turn lifts a lever at the back of the frame which releases the alarm escapement. The alarm escapement is exactly the same as the main escapement; dual escape wheels are driven by a weight and make the pallet oscillate. In this case, however, the oscillation is used to move a hammer which hits the bell.
These alarm escape wheels are made in exactly the same way as the main escape wheels described previously. The only difference is that one of these escape wheels has notches cut out for the ratchet to fit into. Thanks to my shiny new scroll saw cutting these notches was a doddle.
Next up I made the alarm level brackets. Like the main plates the two pieces were clamped together, drilled, then both pieces cut to shape at the same time. To drill the holes in the main plates the clock was disassembled, the plates bolted back together, and both holes drilled through both in one go.
This stud is where the alarm escape wheels and ratchet mechanism are mounted. It’s made from 3/16” steel rod. This was actually a surprisingly difficult part to make because it requires a long, thin length to be turned accurately. The raw stock was held in the check, then the end centre drilled. The narrow diameter was then turned with tail stock support and taking light cuts. Even taking light cuts it was flexing, so it was neither accurate nor had a good surface finish. Fortunately the alarm work is not too critical, so it was adequate for the job. A thread is then put on the other side to mount it to the frame.
The stud is mounted to the back frame. I drilled and tapped the hole for the stud, then countersunk it using a bigger drill bit. An unfortunate characteristic of machining brass is that it likes to ‘grab’ the cutter, and that is exactly what happened when drilling the countersink. The drill bit grabbed and in the process drilled about 90% of the way through the frame, leaving me with a hole that was far too big and which the thread on the stud would barely grip. Thankfully the position of the stud isn’t too critical, so a small nut on the other side of the frame held the stud in place.
Also shown here are the bearings for the hammer arm.
The alarm is driven by a weight, so another pulley is needed. This is similar the one described above; a central hub is machined and short spikes added. Flanges are added on both sides of the hub. The difference here is that the ratchet mechanism is built into one of the flanges. The click spring here is made of a sheet of 1mm brass (yes I’m mixing metric and imperial). The curved shape is cut using my new BFF, the scroll saw. The springiness is then added by hammering the brass on one side, making it curve upwards. This click spring is riveted to the flange.
The flange in the photo shows two stupid mistakes. Firstly, after I riveted it on, I realized I’d forgotten to remove the blue plastic film from the brass, meaning it was now stuck under the spring. Secondly, I riveted it pointing in the wrong direction. I had to drill out the rivets, hammer the spring again so it curved the other way, then re-rivet it. Idiot.
The completed drive pulley and escape wheels are mounted on the stud. They are both held in place with a taper pin going through the stud. The pin is positioned so that there is some tension on the click spring, but not so much the pulley can’t turn to drive the alarm.
Step 15: Assembled With Bell
Another day, another part I didn’t take photos of; the bell, bell standard, and finial.
Making the bell was easy; I bought it from ebay. I didn’t fancy my chances of turning it from a solid piece of brass (plus it would have been super expensive).
The standard (the tall supporting bit) was a simple piece of turning; both ends were threaded and the middle section slimmed down a little. The finial (the triangular bit on top) was made from 1” brass rod which was drilled and tapped, then mounted on a spigot and super glued in place. The curved triangle shape was turned in two steps. Firstly, it was brought roughly to shape by offsetting the compound. The curved shape was formed using hand gravers.
Step 16: The Motion Work
Shown here is the motion work for the clock. This consists of three parts which, when from left to right are the hour wheel and pipe, the minute wheel and pipe, and finally the reverse minute wheel and pinion.
The hour wheel was cut back when we cut the wheels for the going train. The pipe is made from a length of 3/8 in brass rod. This is drilled and reamed to 3/16”. A spigot is turned into the end to be a tight friction fit in the hole in the centre of the hour wheel. The outer diameter is turned down to 1/4”.
The minute and reverse minute wheel are identical in diameter, however the reverse minute wheel is slightly thicker to accommodate the movement from the small spring mounted behind it. The spring itself should be made from hammer hardened 28 gauge brass shim stock, however I didn't have any, so I cut it out of an empty beer can.
Both the blanks were centre drilled to 3/16 then the 26 teeth cut in the same way as for the other wheels. The minute pipe was made in a similar way to the hour pipe, except it was drilled and reamed to 1/8. The outer diameter is turned to 3/16, and the hour pipe tested to ensure it runs freely, but with minimal play. At first try it was a little tight, but some light sanding took care of it.
The minute pipe will eventually have a thread cut into the tip to accept the minute hand, however for the time being it’s left over length.
The reverse minute wheel mounts on the end of the main wheel arbor which is 7/64” in diameter. The more observant among you will notice that we already drilled this wheel to 3/16” (which is bigger than 7/64”) so first we have to plug this hole, then drill a 7/64 hole in the plug.
The wheel needs to have a pinion built into the centre which meshes with the hour wheel. Making this pinion was very challenging for two reasons. Firstly, the pins need to be on a pitch circle diameter of 0.157”, and the pins themselves are 0.047” in diameter. This leaves very little distance between the center hole and the edges of the pins. I’ve illustrated this problem in a beautifully drawn diagram.
The second issue was one of accuracy. Accurately drilling very small holes on a small pitch circle diameter is very difficult with my setup, as everything has too much flex. I used the Dremel-in-the-tool-post method again, but no matter what I did the drill bit would always wander.
In the end this pinion is far from ideal, in fact the pins do encroach into the centre hole of the wheel, and have a tendency to fall out whenever I put the wheel onto the arbor. That said, it seems to work, so I’ve left it as is.
The motion work is mounted on the frames using the hour wheel stud. The plans call for this to be turned out of a length of 5/16” steel, but because this is a very long and thin part (1.25” long by 1/8”) I knew I would struggle to get an accurate finish. Instead I made a short stud (see diagram) with a 1/8” blind hole drilled and reamed at the centre. Using Loctite I glued a length of 1/8” drill rod into this hole and voila! An accurate long and thin part. Despite a long piece of drill rod being put into a (relatively) shallow hole, this worked remarkably well. I just wish I’d thought of it before I made the stud for the alarm work. The photos show how these pieces fit together to form the motion work.
Step 17: The Hands
Next up the hands. The only critical dimensions on these are the holes where they mount to their respective pipes. Both hands were made the same way. First the shape was laid out using engineers blue onto 1/16” by 1” O1 tool steel. The holes were then centre-punched, drilled and, for the minute hand, tapped.
The shape were cut out using the scroll saw. Even in its annealed state O1 tool steel is much harder than brass so cutting it on the scroll saw was slow going. If you’ve never heard a scroll saw trying to cut hard steel imagine the noise you would get trying to use a scroll saw on a live piglet. Similar sort of noise.
Once the rough shapes were cut out they were finessed using files, then given an initial polish. The tool steel I bought had small ridges on it so these had to be removed with abrasive paper.
Once an initial rough polish was done the hands were hardened. Clickspring has a good video on this process, but briefly it entails heating the hand with a blowtorch to a red heat and quenching in oil. This (in theory) makes the steel very hard, but also very brittle. In order to get rid of some of the brittleness the hands were tempered. Prior to tempering the black oxide layer had to be removed with abrasive paper. They were then heated to a light straw colour.
Traditionally the hands for this clock should be blued (again, see the Clickspring video) but I didn’t like my odds of getting a good result so, after a final polish, I left them in their natural colour.
Finally in order to mount the hour hand onto the hour pipe a collet is turned out of brass. This is drilled and reamed to 1/4” (to match the hour pipe), and a spigot turned on one side to be a friction fit on the hand. I accidentally make this slightly too loose so had to use Loctite to keep it in place. A groove is cut in the thin walled section of the collet to allow it to be tightened by gently squeezing it onto the pipe. It’s important the hand can move on the pipe as this is how the time is set.
Step 18: The Hooks
Time to channel your inner blacksmith and heat some metal.
This clock requires a few different hooks; two to attach the cord to the cross strut, two to join the cord to the weights for the motion work, two to attach the weights for the alarm work to the cord, one to guide the cord for the alarm work, and one for the ‘U’ on the back to attach to the wall. All these hooks were made in the same way.
Firstly, if necessary, a thread was cut on the end of 1/8 steel rod. This was then held firmly using a tap wrench in a vice. A gas blowtorch is used to heat the steel, a section at a time, until it is cherry red. At this temperature it’s very soft and pliable, and is easily bent into shape. Some of the hooks I bent the metal round a brass rod, some I didn’t.
Once the steel has cooled it’s covered in black oxide. This was removed and a shine added using a strip of abrasive cloth.
Goes without saying, but hot things are hot, so glove and eye protection are advised, and it’s always a good idea to have a fire extinguisher handy.
Step 19: Alarm and Jockey Weights
The alarm work is driven by a weight which is simply made from some brass rod which is faced, drilled and tapped, and a decorative chamfer added on the end. To keep the cord tight there is a small jockey weight which is made in the same way.
The cord used for both the alarm work and motion work is blind cord from a local haberdashery. I got a confused look when the man asked me what it was for and I told him it was for a clock. The amount of cord you need will be dictated by how high you hang the clock. The longer the cord, the longer the clock will run. The cord costs pennies so I just bought far more than I needed and cut it to length. The cord is nylon so to stop the ends fraying they need to be melted over a flame or similar.
Step 20: Polish All the Pieces
We’ve now finished making all the parts for the clock, yet they are still grubby and covered in engineers’ blue, so they need to be cleaned and polished.
I don’t have infinite patience for polishing, so I went for a matt finish rather than a mirror polish. The process was the same for all the parts. I used progressively finer grits of abrasive paper, cleaning the parts carefully between each grit to remove any contamination. I used the paper wet to avoid clogging and to help improve the finish.
Round parts (e.g. arbors, weights, etc) were held gently in the lathe and, with the ways of the lathe covered with an old towel, spun gently against the abrasive paper.
Flat parts were polished in a tray of water then dried using an old towel.
Brass tarnishes quite easily from fingerprints and contaminants in the air, so to help protect the finish I applied a thin layer of renaissance wax to all the flat surfaces. Any parts where there is friction (e.g. in the pivot holes, the wheel teeth) were not waxed.
Step 21: Assemble
Before talking about the assembly there are a couple of bits I haven’t talked about.
Firstly the chapter ring. The plans called for this to be made out of a large disc of brass with smaller “shields” attached with numbers engraved. I didn’t fancy my chances of getting a good finish doing this, especially as I don’t have a milling machine. As such I cheated and bought a pre-made chapter ring. This was surprisingly cheap (only about GBP3) and made from very thin brass plated metal.
Two supports were machined (see the diagram) along with two feet. Holes for the supports were drilled and tapped into the front plate, with the positions taken from hole for the hour stud. The clock was laid flat, the ‘feet’ fitted into the supports, and the chapter ring positioned onto the feet. It was then super-glued to the feet.
The gluing was nerve wracking; if I did it wrong I would have to go and buy a whole new chapter ring. The screws in the supports secure it into position, but allow it to be easily removed if needed.
Secondly, screws. These are a mundane part of the clock, but one which actually took a lot of time. It may not seem it but there are a lot of screws in this clock, almost all of which were hand made. They are mostly in BA sizes.
They were all made in the same way, just different sizes.
Firstly steel rod stock was turned down to the outer diameter of the thread. While still held in the lathe it was threaded using a die. I don’t have a tailstock die holder so I free-handed it, sometimes using the tail stock to make sure it was square. The screw was then parted off, usually using a small hacksaw, reversed in the lathe, and faced flat. Finally the slot was cut using a hacksaw again, taking care to properly line it up across the centre.
A quick note on dies; it's worth paying extra for new dies, or replacing old ones when they stop cutting properly. When I first tried cutting threads I was using an old tap and die set I had been given. I couldn't figure out why the dies weren't cutting, but eventually realised it was because they were as blunt as balloon. When I bought my first brand new die the difference was night and day.
So, finally, the clock is assembled. In the process of this build the clock has been assembled and taken apart literally hundreds of times, but this time I had to be more careful to make sure I didn’t scratch my shiny polishing. I wore gloves for the assembly to try to minimise fingerprints.
Step 22: Hang
Finally, it’s time to hang it on the wall. This is a fairly heavy clock so a suitable sturdy mounting is needed. Using the thread on the hook in the ‘U’ bracket it’s adjusted to make sure it’s hanging vertically.
The final step in the build process is to convince your fiancé that having a loudly ticking clock in a small house isn’t incredibly annoying. I’ll report back once I’ve figured this step out.
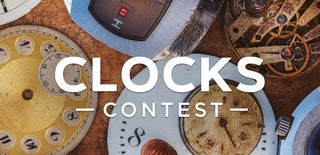
Grand Prize in the
Clocks Contest