Introduction: Marble Pump - 3D Print
This marble pump takes in marbles from one side of the mechanism and pops them out the other. It is intended to be used as the heart of more elaborate marble contraptions, pumping marbles up through a channel so they can then loop through the machine before returning to the pump's intake.
The model was designed using Autodesk's FREE 123D software and printed from ABS plastic on an up3D printer. The pieces snap together using pressure fit nubs, and paperclip bits act as pivots for the moving parts. A small geared motor mounted to the back of the device does the turning.
The files for this project are available at 123Dapp.com
EDIT: 123Dapp is now defunct and the only files I have are a print ready stl and an Inventor part file (just a mesh.) Such is the nature of software I guess.
A few years ago I stumbled on the sweetest website ever to exist, woodgears.ca. This site hosts an eclectic mix of woodworking and engineering projects including complex marble machines. At the core of some of these machines is a device called a marble pump that uses a piston to take marbles in through one hole and then push them up through another.
I was struck by the simple novelty of the gadget and have had the concept rolling around my head ever since. Since I first saw it I've been working on my own version sporadically and finally have some results worth presenting. I hope to eventually build a more elaborate, wooden machine using this very pump at its core. I also have an idea for some modular, model train track style channels that could be snapped together and then added to the pump.
It took me several wood and 3D printed prototypes to get to this point, each one eliminated a problem from the last design before it and eventually I ran out things to go wrong. To begin I went over to woodgears.ca and stared and stared at the examples on this page until the concept finally seeped into my head enough for me to get started on designing. Since there were no dimensions I needed to start from scratch; I ordering a small bucket of marbles and used their size as a base for the rest of the design.
(PS if you have never had the pleasure of playing with a bucket of marbles, you my friend are missing out!)
Since my marbles were 14.25mm in diameter I knew the piston would need to travel that far to be able to pull the marble down and have clearance. That led to the cam (the circular part attached to the motor and the piston) needing a 7.125 radius in order to move the piston that distance. Having the cam size figured out I was able to rotate it to find the furthest distance that the piston would travel to the left and right. That measurement gave me the angles I needed to add the input/output shafts in the right places. With those measurements figured out the rest of the design just fell into place and I completed the model by tweaking the sizes of the moving parts to give them .2mm clearance between one another. After a half dozen test prints and refinements I finally got this version working and presentable.
During that prototyping process I also tested the limitations of the 3D printer by designing very thin parts. Some of the first versions were too thin and would crack, or had details too small to be printed. These little errors really helped me determine how to make the model as thin and lightweight as possible (and use less material), but still be strong enough to work. I found that a minimum 1mm wall thickness was ideal, and that it was best to use .2mm as a base design increment (.2mm is the printers minimum detail size.) Instead of making a part 1.5mm wide, I would instead make it 1.6mm, a multiple of .2mm.
There was a time not so long ago that I would have needed a decently stocked machine shop to make something this small and precise, as opposed to the afternoon of printing and watching reruns that it actually took in today's modern world. Soon to be forgotten are the days of needing a $10k CNC to make precision pieces when instead you can simple hit "print".
Thanks for checking out my project, feel free to use the design and files as you like.
Please share your results!
Works with 14.25mm diameter marbles.
Model Info
Marble Pump v61
W 2.91cm x L 5.92cm x H 5.63cm
Volume = 96.989 mm3
Materials and Tools Used:
Autodesk's 123D design software (www.123Dapp.com)
up3D personal 3D printer (www.up3Dusa.com)
Small geared motor, as found at Solarbotics, Sparkfun, and inside certain "specialty screwdrivers".
Paper Clips, standard bare metal, .8mm diameter
Utility blade, wire cutters, and a handful of other small tools not worth mentioning.
Wee little screws
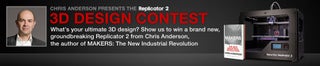
Runner Up in the
3D Design Contest