Introduction: Marshland Pocket-JCM900 Guitar Amplifier
Hello, people, guitarists, amp fanatics and whoever is interested in some facettes of guitar amplification knowledge!
So... What is this?
Despite all the hate it gets, personally I love the tone of my Marshall JCM900 Dual Reverb 4100 "all tube" (I'll get to that later) guitar amplifier, but I cant take it to the small apartment where I am mostly living, so I searched for a way to get the most similar sound possible into the smallest possible housing. Now, my modified version of the original hi-gain channel of the pre-amp, using TL072 op-amps, powered by a PC-PSU on its +12V, GND & -12V cables.
The brand rename might seem a little... yeah... forced, but to me it has at least a double-meaning, as I got most of my musical inspiration from wading through the marshlands close to where I was born. Also it has of course some shameless recognition value and even more shamelessly contains the ending of my own first name. Not that my designing part on this was huge, but it still required a lot of experimentation work. In addition, I love it, when palm muted power-chords give thick, creamy and bubbly "FLATCH-FLATCH-FLATCH"-sounds on the high end and "WRAMM-WROMM-WRUMM"-ones on the low end, I dont know why, but it reminds me of wading some sludgy marshland with totally soaked skater shoes, or walking some asphalt thereafter
What it can do
This pocket - or actually desktop - version of the JCM900 DR 4500 has no tubes and slightly reduced op-amp powering voltages, hence a lot of components are changed in order to sound as good and as original as possible. Obviously, it can't sound the same, as mimicking "done right"-tube-sounds with analog electronics is almost impossible. Still, personally I am very pleased with the outcome. To say: It somewhat can mimic the sound of an original JCM900 with additional pre-gain, as in my opinion, the original needs some signal boosting before hitting the input jack in order for it to really roar and scream the way i want it to (see Step 13: Testing!).
An all-tube amp without tubes - you kidding me?
Well... you see, when an amp is sold as "all-tube", that just means: there are tubes in the pre-amp AND tubes in the power-amp. It doesn't mean there are no transistors, diodes or op-amps in the signal path and the 4100 & 4500 versions of the JCM900 do have them. In fact these amps use a series of op-amps and diodes to create its unique wave shape, that is then smoothly rounded off and "warmed" by the tubes. Now... if you are a 100% tube puritan and still kept reading this far, then feel free to hate me in the comments section.
What it cannot do
I said I copied the pre-amp... and I left it being a pre amp, so don't expect this thing to be loud with high impedance headphones, and even more importantly, don't try to drive low-impedance speakers as you most likely will burn some chips! I originally planned to replace the pre-amp tubes with mosfets, but that was in no way listenable, now all the power output relies on what the TL072 can deliver.
Also included in the pre-amp-only-fact: it does not include speaker+mik'ing simulation, thus don't compare it to a VST that does include such features, but see it more as a distortion effect. Anyways, along with raw output listening samples, I also included 2 samples that were processed with a speaker & mik'ing simulation! Just scroll down all the way to access it.
And... they say Marshall amps are there to be played with the volume knob full up, and they say it for a reason: the the soft clipping of the power-amp is one major component of what makes sound so sweet and creamy. I tried that with my 100W head once, but then I couldn't hear the drummer and I was so focused on my head not to be blown off that I couldn't really enjoy the "sweet cream". Yes I know, there are special devices that attenuate the signal after the raging stormblast that roars through the output jack, but... In the end, this tiny remake can't of course create super smooth tube sounds. But please listen to the samples at the end of this I'ble and hear for yourself!
Step 1: What You Will Need
I hope I found a way to make this section as flexible yet least complicated as possible, as there is a "solid core" of things you need in any case (not further indicated), no matter what, and several optional features, indicated by *(optional modifications in the pre-amp-core), **(EQ), ***(LED-Clipper) and ****(my funny little housing)
MATERIALS
- An expandable repurposed PC-PSU (much thanks to russ_hensel, newtonn2, Sitnalta, punisher_1211 and others for showing how to do that! just make sure you KEEP the +12V (yellow wire) AND -12V (blue wire) terminals, as BOTH are vital for the TL072 to work!)
- Stick board for prototyping
- Perf boards for the soldering
- 2x TL072 op-amps (better get some more, they burn somewhat quickly!)
- 2x 8-pin or 1x 16pin IC sockets* (recommend these for ease of chip exchange)
- Fragments of further IC sockets* ***
- 5x 1N4007 Diodes
- 4x LEDs*** (mine are 3mm bright white)
- Resistors (Numbers mean ohm ratings, power rating: 1/4W is sufficient, for the most, even 1/8W will do):
- 2x 540**
- 2x 1k**
- 3x 4.7k
- 4x 10k
- 4x 100k
- 1x 220k
- 1x 1M
- 1x 5M
- Capacitors: (At least 25V-rating is imperative!)
- 3x 100pF
- 1x 220pF
- 1x 4.7nF
- 1x 10nF**
- 1x 22nF** + 1x***
- 1x 68nF** + 1x***
- 1x 100nF + 1x***
- 1x 220nF**
- 4x 330nF
- 1x 470nF + 1x**
- 1x 470µF + 1x**
- potentiometers (potis, variable resistors):
- 3x 0..22k**
- 1x 0..100k
- 1x 0..1M* (=pre-gain, can be omitted (=shorted) if only aiming for rock to milder metal sounds)
- 1x 0..2.2M (or 0..5M, then, also the switch and 5M fixed resistor are unnecessary)
- 1x Switch* (or more if you plan on making more optional components switchable from the interface)
- 1x Mono 6.3mm (1/4") input jack
- 1x Stereo 3.5mm (1/8") or 6.3mm (1/4") output jack, depending on preference/your mainly used headphone plug
- Wires, twin wires (highly recommended) and even 3-in-a-row cables are helpful
- Small plastic "zipper" bags* ** ***
- Housing (I used a transparent sweets box)****
- A few cm of Ø14mm round wood for the knobs****
- Black and gold spray paint****
- Faux leather****
- White chord (such as you see on the front of the housing, framing the brand logo)****
TOOLS
- Alligator clip cables are convenient for testing the stickboard and early perf board prototypes, especially for clipping them to audio cables
- Soldering iron, tin and flux
- Pliers and cutting pliers
- Marker pen or pencil****
- Handsaw****
- 320 or less grit sandpaper, a fine rasp or a rough file****
- Wood drills sized so that you get your potis through that hole in the housing and the knobs onto the shafts****
- Drill-chuck, separated from an electric screwdriver, or probably also the e-driver will work
- Scissors****
- Stanley knife****
- Cyanacrylate adhesive (super glue) or other well-locking adhesives****
- All-purpose or paper glue****
SKILLS
Well for the soldering, you should know how to use that hot tip, tin and flux (what's told in Electronics class plus some experience should do, otherwise you can try and gather a lot of experience here ;)
I find myself unable to teach you the board-layouting or to give step-by-step soldering instructions. I will show you the schematics and my end product, but please have the patience to find your own layout on your boards. However, help on that has been given before by firesign, ppowell14 and in places like the Official Arduino Forum.
**** With that number of switch, jack and poti cables in such a small space, wire arrangement can be tricky - and I believe that I myself am anything but a master when it comes to that.
**** If you - like me - want to craft your poti knobs yourself, then after the Woodworking Class you will lough at what I have done here.
**** drilling holes in easy-to-crack plastic boxes requires some patience and the ability to tell apart axial pressure force from torsion force (first of which is dangerous even in small amounts, the last of which you will need some)
Anything else you need will be described in the following steps. If you still miss something, please post Comments, I will do the best I can to help!
Step 2: Prepare Your PSU for Use As a Project Power Supply
Unless you have other means of +12/-12V/GND-supply, you can follow my quick PSU-conversion, but if you are new to this, please refer to the Instructables given in the links in Step 1: What You Will Need - MATERIALS: PSU!
Whatever you do, please stick to some safety measures:
(!) Never have the PSU-casing open when it is connected to the mains - high voltage!
(!) Make sure you wait a while after disconnecting the PSU from the mains cable and before opening the case, as high voltage may still be carried by the big capacitors!
Knowing that, the green cable needs to be connected to a black one for the PSU to spin up the fan and start to supply the voltages we need, as shown in the picture and explained in the mentioned Instructables.
(!) If your PSU is not running smoothly, stops after some minutes or does other things it's not supposed to, then please refer to the mentioned Instructables for help!
When your PSU is running and does supply the voltages we need, you can cut all the non-needed wires (the ones not ending in the fat ATX-connector) inside the casing.
(!) Make sure that cut cable ends will not accidently connect to each other or the casing! Heatshrinks, hot glue or other means of insulation should be applied!
Now it is purposeful to rearrange the +12V (yellow) calble on the ATX-connector as shown in the picture, as this step brings all the needed supply voltages together so you can make a small plug for easy connection.
(!) Pay tremendous attention to never reverse-supply your circuit! Best would be if you made a plug that prevents "wrong-way-in's" by its shape, as 24V can easily fry the chips and might also be no good for LEDs and electrolytic capacitors.
Step 3: A Word or Two on the JCM900 DR 4500 Schematics and (Guitar) Amplifiers in General
OK, let me try to keep this short, as another of my Instructables had been critizised for being too little instructive...
The original schematics for the Marshall JCM 900 Dual Reverb 4100 and 4500 models is publicly available on Dr.Tube, and even more specifically on thetubestore. I recommend looking at those, but if you are new to, yet interested in guitar amplifier technology and schematics, then please take it easy, go slow and first read about op-amps and tube amplification principles. In any case I recommend reading some of Rob Robinette's super educative amp sites (but be warned, he is totally what I like to call a "tube puritan", just watch the solid state memes)!
Now... The JCM900 4100/4500 pre-amp schematics appear rather frightening at the first glance, as they are super packed with stuff. The original features switchable "clean-to-slightly-overdriven" and "rock-to-metal-distorted" channels. The switching is done by the switchable M5201 op-amps, and they are fed with +15V/-15V. In my remake, there is only the more distorted channel, thus it uses the non-switchable but equivalent, easier to get and cheaper TL072 op-amps, powered with +12V/-12V, as mentioned before. Also, my version does neither feature tubes nor a spring hall effect, further narrowing down the important region of the schematic.
The actually relevant parts and signal path of the original schematics are highlighted in green in the picture above, plus it states replacement and adjustment components.
Further added parts and the full schematic of the Pocket version will be presented in the subsequent steps.
Other than the JCM800, the early "Master Volume" versions of the JCM900 featured diodes in the signal path, which makes these amps very unpopular among tube puritans, at least today.
Then, with extensive use of op-amp amplification and diode-clipping in the 4100 & 4500 models, although very popular in the 90's, these are now even less favored ones. People complain about their "scratchy" and "cold" sound, still I do like it and I know many others do as well.
Tube amplification - or shall I say "the tube cult" - is actually a very polarizing topic among guitarists; while it is definitely true that tubes are capable of producing soft, warm overdrive and clean sounds that cannot be properly mimicked by semiconductor technology, there is also excessive hate for any semiconductors appearing in circuits at least among the puritans. Especially "solid state" amps (these have tube pre-amps but transistor power stages) are hated by many who never turn their amp up such as to experience the actual advantages of tube power stages. My personal "favorites" are those who feed their full-tube amps only after a "tube screamer" pedal just for the cult of the name, which in fact actually has op amps and diodes to mimic tube distortion! Further, blind tests have shown even audiophile guitarists usually can't tell solid state amps from their 100% tube counterparts. My advice: Be open minded, try everything for yourself and trust your ears, not people who want to tell you who's best.
And... if you are used to DIY-approaches like "op-amp-overstressing"-kind of distortions, then you will be amazed by how well balanced and "sweet and creamy" this preamp can sound even without tubes!
But once more: please listen to the samples for yourself, just before the last step all the way down.
Step 4: The Pre-Amp of the "Pocket"-Version
Now, let's finally get down to the hands-on-part!
If you feel like you don't have the time for stick board-try-outs and instantly want to rush the building of the whole thing, then skip the schematic above, as it lacks EQ and post-clipper! The full schematic will be shown in Step 7: Wholesale Schematic.
Still, if you are - like me - a little clumsy and easily losing track when prototyping bigger schematics, I recommend trying everything out on a stick board and only then solder everything onto a perf board. Things become more familiar and intuitive after experimenting with the sticking pattern!
Unluckily, I did not photograph the stick board prototype and now I miss some components to make a second one, so I can only show you the soldered version of the pre-amp.
Take your time, compare the original schematics with my own drawn ones if you are unsure how and where to stick the components, and be cautious about the power supply terminals! Shorting them will stop the PSU, which is short-circuit protected and it will start up again after removing and re-applying the "power-on-connector" (green-to-black-bridge), but reverse voltage to the chips and over-voltage to the LEDs can do some damage!
I can recommend to begin the building of the circuit at the input and test it for the first time as soon as you have sticked the first amplification stage, keeping in mind the following steps of hazard-minimization. Repeat the testing after each amplification step:
(!) Make sure you always have a series of a coupling capacitor and a resistor of few kOhm between the op-amp output and the speaker/headphones. The cap prevents DC-offset, which would drain power from the op-amp and can lead to quick production of heat and burning of the chip, while the resistor keeps the impedance up and prevents over-loading of the chip that could occur even without DC offset, plus protecting your ears in case of low-impedance headphones!
(!) Also, always disconnect the PSU completely and measure the resistance between the power supply rails on the stickboard before applying the voltage. (Should be at least a few kOhm)
(!) Next, make sure the output of the op-amp is not connected to GND by resistors smaller than a few kOhm, as again, over-loading the output can lead to heat and destruction.
Then you can connect and turn on the PSU while carefully monitoring the chips' temperature with a finger.
(!) remove your finger instantly if you feel heat to prevent burning your skin! Only then try to quickly turn off or remove the PSU-power.
If you hear something like 50/60 Hz mains humming, or strange noises if you touch the input pin, thats great, that part of the schematic seems to work then!
If your phones are silent, just have another temperature check of the chips, just in case! If negative, the resistor before the phones might be too large, carefully proceed to smaller-Ohm-rated ones, but stay in the kOhm region unless you really know what you are doing!
Watch the 1N4007-diode clipper well! It is basically a rectifier bridge with a 5th diode connected such that the rectified current can flow through it. However, some smart guy in a forum wrote this circuit was actually less of a rectifier than a frequency-doubler!
For the interest of how it would sound, I made the 5th diode exchangeable (you can see this in one of the pictures above) to try the sound of different diode types like shottky, zener, LEDs, small signal, fast recovery and unknown ones, but I can tell you to spare the parts and effort, as nothing sounded anything close, basically all of the non-1N4007 types sounded crappy. Maybe someone wants to change all 5 diodes and report the experience, but I have the feeling that it won't get better.
Step 5: The LED-Post-Clipper and Its Actual Purpose
If you watch the original schematics well, you see the signal after the last M5201 Op-amp is subjected to high-Ohm resistors and tube amplification steps. I have tried replacements to mimic the tube sound:
- MOSFETs directly replacing the tubes, but powered by +12V/-12V instead of high voltage DC.
Result: extremely fizzy and saw-tooth like. nowhere tube-like at all, no matter what the resistor values were. - MOSFET clipping - using the MOSFET transistor as a clipping diode
Result: just as fizzy and saw-toothy as before - The op-amp clipping circuit used by the world famous Tube Screamer pedal.
Result: so smooth that any of the much-appreciated distortion from before seems to disappear. - LEDs are said to have smoother clipping characteristics than power rectifier or even small signal diodes, also they have higher forward voltages, resulting in smoother tone and higher output volume.
Result: Indeed, there is a rounding-off-effect to the spiky peaks of the waveform, but it is nowhere close to being tube-like. Probably you would still rather call it a cutting-off-effect.
Single LEDs would cut off too much of the wave, making it basically a square wave - and you could hear that. Also, I feared the LEDs would burn at so much peak voltage without pre-resistors. Thus, I put 2 LEDs in series for each direction, leaving just the portion of the wave that i felt was purposeful. Excessive "fizz" produced from the LED clipping can be controlled by a capacitor in parallel that eats away the high frequency noise.
Despite failing the initial target, I still kept the LED-clipper, as it added just that little bit of distortion that I had missed when playing palm muted power chords of more extreme styles such as Death Metal or Grind, where you expect a thick and heavy wall of sound roaring and vibrating from under your muting palm and only then, the pinch harmonics cut through at full power.
However the LED-clipper is totally detrimental when playing softer styles such as blues or rock, as with less saturated gain levels, the LEDs cut off the peaks when exceeding a certain amplitude level, thus only affecting louder notes and shattering them in very unpleasant noise.
So decide for yourself from my description or better from your own experience whether you would like to have such a post clipper or not! Just please be nice, some like more extreme levels of distortion others don't. No one needs to like the one or the other, but everyone is best off accepting that different people have different needs even if some of them might appear odd to others.
To stay flexible, it would be best to make the clipper switchable (like depicted in the schematic) or stick-able with exchangable "Fizz-Limitation" caps. This is what I did, using a broken IC-socket to stick or unstick the clipper and/or various sized caps (as depicted in the photos).
(!) Please note that this LED clipper has nothing to do with the one
shown in the original schematic, where the diodes are used to create a slight and smooth overdrive in the "crunch"-region of the "clean" channel, which is totally omitted in my design!
Step 6: The Equalizer
Note: the schematic does not show the 470µF-capacitor that is soldered
on the perf board. Probably this is even an overkill, but i think its safer to have one coupling capacitor too much than one missing. The wholesale schematics in the next step are drawn featuring all the components that I actually used.
Apart from that, please watch the schematic well and bring it on your stick board and/or perf board. Be careful with the capacitor values, they can have a big impact on both, frequency roll-off and overall loudness. If you don't have cap's with the correct values, you can try the closest ones you have, or put smaller capacitors in parallel so they sum up in capacitance (Cresult = C1+C2) or put larger ones in series, then the reciprocal of the total capacitance is the sum of the reciprocals of the individual caps (1/Cresult = 1/C1 + 1/C2)
You can, of course, put the EQ on the same board as the pre-amp (and LED-clipper); in this case, you find the complete schematic in the next step!
The equalizer you see in the original schematic seems to be solely applicable for high voltage signals as encountered after the pre-amp tubes. To be honest, I dont have too much of an idea how the original EQ should work (please leave a comment if you do!), but I experienced it did not work with the signal that came from the no-tube design. Hence, I designed my own passive EQ, one that I understand and where I can explain the basic workings to you:
Every capacitor that is placed parallel to the load (eg. headphones) - or in other words: that leads from the signal directly to the ground - eats away the treble content above its threshhold frequency. As you dont want your treble to disapear when you turn up the bass, all such parallel capacitors must have un-coupling-resistors before and after its position, so neither the input nor the output signal is deprived of its treble content. This is why the "BASS" lane hase those resistors at both sides and the the "MID" lane only after the paralell cap.
Every capacitor that is placed in series with the load allows only the treble content above its threshhold frequency to pass, but this does not affect the other lanes, hence un-coupling is not necessary. As there is plenty of high frequency noise in the signal, the "TREBLE" lane needs a resistor in series to be controllable in a similar range of loudness as the other lanes.
The "MID" lane has both, series and parallel capacitors, thus the treble is cut above its range, and the bass is cut below.
The dimensioning of all the parts is a tricky thing to do in a passive EQ, as too much un-coupling leads to substantial loss of signal strength, but too little un-coupling makes the bass knob eat away the higher frequencies. I think the one I built is a bit on the "too-little"-side. But I think the bass is enough even if not 11'ed and the loudness is already pretty low.
Step 7: Wholesale Schematic
Now finally, the whole thing!
Try to solder that to a perf board, refer to the previous steps whenever needed and check the function before preparing the housing!
Pay attention to the pin usage of the headphone jack: use a stereo jack (or you will hear only with one ear, highly unpleasant!) and connect the tip and ring pins both to the output signal. The shaft is connected to GND. now you hear with both ears, but BEWARE:
(!) never connect a mono-cable, as the ring and shaft pins are then shorted, hence the signal output has direct contact with GND, which the TL072 will not tolerate for long!
Step 8: The Housing: Drill Some Holes
Usually I do not care much about the looks of things as long as they work. This time however, I chose to try and mimic not only the sound but also the looks of the original amp.
I decided a transparent box with rounded edges, like this one would be fine.
The most important and equally most hazardous step in processing the housing is drilling the holes for potis, switch(es) and the jacks, thus: always start with the hole drilling, as no resources other than the box will be wasted if you crack that plastic.
Please forgive me I only have photo documentation of drilling the holes of the EQ-poti, which I added only after I had the first concept of the rest ready.
The procedure is prepared as follows:
- Plan a good arrangement/layout of the knobs, jacks, switch(es) and supply cable (refer to the declarative pic in the intro section or create your own)
- Know the size of your potis and knobs as to be able to decide for proper spacing in between them!
- Also pay attention to the internal spacing when placing through-wall-components around a corner! some components can spatially prevent the mounting of others
- Mark the lateral positions of the holes where it will be invisible in the final product
- Decide for a suitable vertical height and cross the lateral positions with that height line don't bother for visible markings as long as they are small - you will cut the hole around them anyways
- Know the sizes of all the holes you need and decide which drill to use for each hole
The actual hole drilling is done as follows:
- At first it is important to only use the naked drill with only your hand!
- Place the tip of the wood drill in the center of your marking and spin it between your fingers.
- Spin it fast but do not press down the tip (avoid axial pressure)!
- When the cutting edges at the perimeter of the drill start to cut into the plastic, finger-spinning the drill will get tough and dangerous, don't slice your skin!.
- Mount the drill to a chuck tool for increased torsion force. I would discourage the use of heavy (in terms of weight) electric equipment, as you crack the plastic easily even if super cautious.
- Continue the drilling with increased torsion force, but stay on a minimum axial force!
- When you are almost through you will hear the awful cracking noises you need to be so scared of, but this time they are intentional, as at some point the hole needs to be cracked open. still, do concentrate on the spinning, do not push it open!
Step 9: Housing: Paintjob & the Faux Leather Cover
Note: by "glue" or "adesive" i refer to cyanacrylate / super glue. If you dislike this kind of adhesive for any of its disadvantages, you will most probably also succeed with textile, leather or stronger general purpose adhesives, but personally I prefer the speedy and tight lock of the cyanacrylate.
For the main box, it is important to glue the leather on before mounting the lateral jacks and other components that need to come through the leather!
Also, of course the housing needs to be spray painted before mounting leather cover!
But it can be beneficial to mark the cut-out shape to the backside of the leather as long as the box is transparent, hence the best procedure will be as follows:
- Mark the cut-out shape as shown in the pictures
- Cut them out
- "Try them on" i.e. clamp it to the housing or hold it there with your fingers and decide upon whether the piece fits best.
- When done, remove the leather from the base box and do the paintjob (gold at the front, black in the back), pay attention to the safety instructions and requirements of your painting methods!
- Re-fit and glue the leather cover
- Find the holes that need to pass through the leather and cut an X-shape into the leather. if needed, pry open the X-shape and remove the 4 triangular parts that now cover the hole
The lid will be covered completely with leather, so no painting needs to be applied, hence you can follow the procedure shown in the pictures and described in the following:
- Roll the lid over the leather and mark the edges as shown in the pictures
- Repeat for all 4 sides
- Extend the markings until you have a full rectangle (if a missing corner happens to you as in the pictures, make sure it will be one of the further back corners ;)
- Cut out the rectangular sheet
- Place the lid on its center
- Fit and glue the sheet on 2 opposite edges, leaving gaps at the corners
- Glue the remaining edges, again leaving the corners
- Fold the edges of the sheet to form a triangular latch, apply glue to fix their shape
- Glue the latches down onto the lid such that the round corner can be seen
- Keep an eye on the direction of the latching, probably it is the best practice to let them all face back
Step 10: Mounting the Through-Wall Parts
Now, hopefully your housing has proper sized holes for all the components that need to cross the housing wall.
The best would be if all your interface components would be screw-able at the interface. Not only does this look neat, but it also has the advantage of being un-mountable for whatever reason there may be.
(!) Take a close look at your screw-through potis and switches: sometimes they have small noses poking into the wall, then you really need those spacer rings they hopefully came with, as the plastic wall is still easily cracked!
Print-mounted parts such as the left poti in the picture can be glued to the interface with a strong adhesive, if you dont fear the non-reversible or possible white film that cyanacrylate occasionally creates close to its site of application. However, do not glue the jacks, they must be screw-on parts, as they are subject to stronger axial forces than the potis and are likely to come off regularly!
(!) If gluing a poti, pay close attention to not accidentally fixing the movable parts!
Step 11: Make Your Own Knobs!
Now, lucky you if you can get suitable and precious looking knobs for a good price! probably this would have been the most costly thing of the whole product so I decided to DIY them. They don't look pretty, but you can see the intention...
How to make them:
- Cut equal lengths from the round-wood
- Grind them plain on at least one side with grits up to 320 or with a fine rasp or rough file
- Taper the front edge all around by laterally moving and slowly turning the knob on your abrasive tool
- Find the center and drill a hole (better use a drill press!). Pay attention not to drill through thre front plane!
- Give them a golden paint job
- Mount them using super glue or some fancy lateral screwing technique (I initially planned to do the latter but ending up applying the first)
- Watch well, where the start and end points of the potis are and mark an indication line
Step 12: Finish That Housing!
Now its time to print out an image imitating the front cloth of the original amplifier with that legendary brand sign on it!
- Measure the aspect ratio (height and width) of the space where you want to have the "front banner" cloth and brand sign
- Make your own personal design with the close-to-original Brand Font!
- Make a few draft print-outs with high brightness to find the right scaling without wasting too much ink
- Make a high-quality print out and glue the paper to the plastic, using a kind of adhesive that stays invisible from the front!
- And the finish of the finish is the white chord, it seems silly, but it really does some magic that never would happen without it!
Step 13: Test the Guts Out of It!
Oscilloscope measurements have been conducted with increasing gain and a number of peripheral settings, starting from a 440 Hz sine wave fed to the input. Results are summarized in the osci-graph.
In the pencil & paper image I tried to show what the output wave shape of the original Marshall JCM900 Dual Reverb 4100 model was when I measured that some years ago. The input was also a sine wave of 440 Hz, but the screenshots of the output got lost somehow, now I can only show you what I remember of it.
Of course, listening samples are a must!
I apologize for the less than poor playing and sub-optimal, mid-pronounced EQ-settings, still, here the pre-amp settings, EQ held constant. These are 100% raw recordings directly from the device's output:
- clean.mp3: pre-gain: 0, gain: almost 0, LEDs: OFF, FizzCap:68n, guit: full up
- slide.mp3: pre-gain: 0, gain: 9 o'clock, LEDs: OFF, FizzCap:68n, guit: 2nd pot down at 3/4
- rocknroll.mp3: pre-gain: 0, gain: 11'oclock, LEDs: OFF, FizzCap:68n, guit: 2nd pot down at 3/4
- hardrock.mp3: pre-gain: 0 gain: pot max, LEDs: OFF, FizzCap:68n, guit: 2nd pot down at 3/4
- heavymetal1.mp3: pre-gain: 0 gain: switch max, LEDs: OFF, FizzCap:68n, guit: full up
- heavymetal2.mp3: pre-gain: max, gain: switch max, LEDs: OFF, FizzCap: 68n, guit: full up
- deathmetal.mp3: pre-gain: max, gain: switch max, LEDs: ON, fizzCap: 68n, guit full up
Further:
- EQ_singlechannels.mp3: each time one channel was max'ed, the others min'ed: treble - mids - bass
- hardrock_AmpSim.mp3, deathmetal_AmpSim.mp3: I applied the free Boogex Voxengo Plugin with Speaker and microphone simulation, omitting any features related to its amplifier or distortion, plus adding a slight nuance of a reverb (or rather: room simulation) effect. To me, this sounds potentially like one could even do recording with that thing and its not even multi-taken or further dug into yet, its really just a quick and dirty "c'mon le's go" effecting!
Step 14: Thanks, Have Fun and Good Luck With Your Own!
I really want to thank every single one of you who made the effort and worked their way through this Instructable!
It was tough to write, I guess its even tougher to read and follow, but I'm confident it is one of the better DIY guitar amps that people will like to build if they had made the easier ones and are hungry for more!
Also looking forward to answering questions and discussing various topics in the comments!
Let me Thank you for once more and wish you good luck and happy making!
- rievezahl
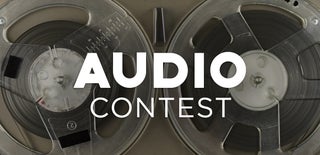
Participated in the
Audio Contest 2018