Introduction: Medieval Hand Cannon
This is a replica of a hand cannon, also known as a handgonne, that would have been used in 14th century Europe.
It is a very easy and quick project if you have access to a lathe. Total time for the project was about 6 hours not including design and the cost was about $30.
Materials:
1.5” dia. x 12” long steel
1.25” to 1.5” dia. wood pole (recommend ash or white oak)
#10 x 0.75” long wood screws
Boiled Linseed oil
Tools:
Lathe
Drill press or milling machine
Hand plane
Carving knife
Rasp
Step 1: Design
I have a fascination with artillery of any kind. My preference is American Civil War but I also like the very early artillery. When I learned about the first hand held artillery I knew that I wanted to build one. After doing some searching I came across a design that I liked and that looked easy to make. I found a hand cannon dating from the 14th century. There were pictures detailed enough to base my design on.
To go from a picture to an actual design I fist printed the picture full size. I knew that I wanted the final diameter to be approximately 1.5" and the bore to be 1/2". Once I had a print scaled to this size rough dimensions were measured directly off the print. These dimensions were then used to create the cad drawing. I tweaked the design until everything looked close to the original. Since the originals are likely to have been made one at a time I’m sure there was a good deal of dimensional variation so I didn’t worry too much over the actual dimensions. I just picked sizes that I felt were easy to work with.
Step 2: Design Evaluation
I decided to be a good engineer and do a quick check of the stresses to make sure the thing was not going to blow up. I remember reading somewhere that a good rule of thumb for cannon design was to have the wall thickness at the breach equal to the bore diameter but I wanted to check what the math told me.
I assumed the barrel to be a thick walled pressure vessels. I also assumed 10,000 psi for the maximum pressure from the black powder. I'm not sure where I originally found this pressure but I believe it was from something I've read about black powder rifles. Whatever the origin it seemed to be a reasonable number.
The maximum tangential stress was found to be 12,500 psi.
The maximum radial stress was 10,000 psi. The fact that this is equal to the pressure is not a coincidence.
Since both stresses are quite high I thought it prudent to use a combined stress. I chose von Mises because that is my preference. The resulting combined stress is 19,526 psi.
Assuming 1018 steel, with a yield of approximately 31,000 psi, the resulting safety factor is 1.6. This is acceptable.
As a double check I also ran a case with a maximum pressure of 15,000 psi. The resulting safety factor is 1.1. This is still acceptable.
Step 3: Building
Machining the barrel was fairly straight forward. Unfortunately I don’t have any pictures of the actual machining.
I started by drilling out the bore with an extra long 1/2" drill. I would recommend reaming the bore. The drilled bore was very rough. This pretty much voids any hope of accuracy when fired. It also just happens that a standard 0.500” reamer is 8” long which is just long enough.
The socket end of the barrel was drilled and then bored to size to accept the pole.
With the two functional features finished the profile was turned between centers. The socket end was done first up to the bead detail. The barrel was flipped and the rest of the profile completed. The curves were done by setting the compound rest to the various angles that closely matched the drawing. Everything was filed and sanded to an even finish. This was a lot of fun because there were no real accuracy requirements. It just needed to look good. In some ways it was a lot more like wood turning. A CNC machine could have made very quick work of this but where is the fun in that.
The last thing to do was drill a hole for the fuse and two mounting holes. The fuse hole was drilled with a #7 drill. This is a little large compared to the bore diameter but 1/8” fuse is readily available and cheep. A second hole was drilled to intersect with the socket for attaching the barrel to the stock.
I made a pole from a scrap of oak. It was rounded using a hand plane then fitted to the barrel. I left it faceted because I thought It looked good and took much less time. The barrel was held to the pole with two wood screws. I found some from a hinge set that looked like cut nails. Alternately the barrel could be glued on with epoxy or even riveted to the pole using a small pin peened over on each side.
The wood was given a few coats of linseed oil for protection. The barrel was left untreated.
Step 4: Firing
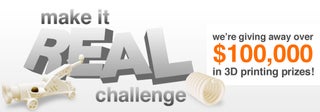
Participated in the
Make It Real Challenge