Introduction: Memory Game of Memories- Transferring Pictures to Wood
The Christmas gift I made for my family this year was a memory card game. We have always played memory together when we were younger and occasionally still do. However our memory game before I made this was for ages 3-6! I decided to make one custom for our family that was full of pictures of when my siblings and I we were little kids. In addition to the cards I wanted to make a box that would also reflect the concept of memory and ended up making a box with copper wire inlay and an etched copper lid with something special. If you want to see a few tears shed, this is a great present to make.
You will need:
- 1/8" ply wood to be laser cut
- old pictures
- gel medium
- #000 and/or #0000 steel wool
- 1/2" plywood for the box
- 1/4" plywood for the interior of box
- polyurethane
-optional: boiled linseed oil
- hydrochloric acid (muriatic acid)
- hydrogen peroxide
- copper (plate, wire, and nails)
- baking soda
-optional: liver of sulfur
- Johnson's Pasting Wax
Step 1: Designing the Shape and Back of the Memory Card
The memory cards are 2" squares with a 1/4" fillet on each corner. I had the shape cut out of 1/8" plywood with the laser cutter. I made 64 cards so there would be an even 8 by 8 square when the game was set up.
1.) It seemed fitting to do a drawing in Autocad that could be etched onto the back of the cards with the laser. I chose to draw the family house that we currently live in. Just place your image into Autocad that you want to draw and then draw on top of it for reference. For this drawing you do not need an incredible amount of detail because it will be only 2 inches tall. Also, for me, the laser cutter charges per minute so if you don't own a laser cutter and send out it, it can add up quickly. Overkill in Autocad to make sure you don't have any double lines that the laser will cut twice.
2.) Draw the shape of the card that you want and then shrink down your drawing to fit inside of it. Adjust your colors for the lines so you can alter the power and speed differently for the cut and the etch. I made my cut lines blue and my etched lines red. Now just copy your Autocad drawing as many times as you want cards. I was going to have 64 cards so I just made around 70 so I would have a couple extra to do tests on.
Step 2: Choosing Pictures for Your Memory Cards
This was for sure the hardest part to decide on for this project. I could only pick 32 pictures so there would be 2 of every picture. I had went through all of our digital photos and picked all 32 pictures 3 or 4 times before I decided that they weren't old enough to make the emotional impact I was hoping for. So I went through all the old photo's that were pre-digital and found pictures that captured myself and siblings when we were children.
1.) Decide the pictures that you want. Make sure the image you want can be cropped to 2 inches by 2 inches without any information being left out or leaving blank space on the card. Scan any physical photographs onto your computer.
2.) I used a very round about way to get a frame made for Adobe Indesign. I took the Autocad shape of the card and exported it as a .PDF then opened that .PDF in Adobe Illustrator, joined the vectors, then copied to clipboard the vectors from Illustrator and pasted them into Indesign. Then I could use the shape as a frame. Copy this frame 32 times and use it to crop your scanned photographs.When you finish make sure that you mirror/reflect all the frames before you print so that when you transfer they are the correct orientation.
3.) Print out 2 of the document that is going to be transferred so you have 64 pictures. This method of transfer will only work if the prints are from a laser printer.
What toner is, is just plastic that is heated up and transferred to paper. An inkjet uses actual ink and actually absorbs into the paper. There are other ways to transfer with inkjet printers but not practically for this project.
Step 3: Transfer Images
I chose the method of image transfer that uses gel medium. I bought my gel medium at a craft store. It is a little tedious to do so many times but the results are worth it. Make sure there are no burns on the face of your plywood pieces. It doesn't matter if there are burns on the edges because they will get sanded later.
1.) Cut out all of your pictures with a knife and ruler. You can just avoid cutting the rounded corners and just make them square because the image will line up with the edges of the card anyway.
2.) Liberally spread gel medium onto your wood piece. You can't skimp on it and make it evenly spread. Once you do a couple of tests you'll have the hang of it. I did my first test with a black and white misprint.
3.) Set up two square edges that you can put the card against. Now use those edges to make sure that the image and the wooden card match up perfectly.
4.) Once you have the image set perfectly on the card, hold down one side with your finger so the paper doesn't slide and use a squeegee of some kind (credit card, extra piece of Plexiglas, etc.) and squeeze out the excess gel medium. Do this for all sides until the image is flat with no wrinkles.
5.) Wait about 8 hours before proceeding onto the next step.
If your etch or image on the back of the card has a specific orientation, make sure it is consistent with the orientation of your transferred image.
Step 4: Cleaning Your Cards
When the cards are fully dry it is time to remove the paper from the back and reveal what you have made.
1.) Just get a bucket of water and dip your card in until the paper is soaked. Then use your fingers like sand paper and gently rub off the paper backing. Underneath you will find your image transferred to wood and in the correct orientation. You will have to let the cards dry and see where there is still paper remnants on the card. Then go back and get it off in the water again.
2.) As a final pass to make sure that all of the paper is gone I just used #000 steel wool a gently ran it across the cards in the water. It didn't hurt the cards so long as they were in the bucket of water.
Step 5: Sealing the Cards
Now that all the paper is off of your cards, it's time to seal them so they are protected during game play.
1.) The negative consequence of water on your cards is slight but needs to be corrected before you seal. The back of the card will be a little rough so it is good to get some 200 grit sand paper and smooth it out. Make sure you go with the grain and don't go deep enough to affect your etch.
2.) Now the edges are all burned up from the laser and clumpy with excess gel medium. Take the time to hand sand the edge of each card with a high grit. sand paper so as not to deform the shape of the card. This makes a huge difference.
3.) At first I though spray polyurethane would be the best choice of a sealer but I was disappointed in the results. It didn't build a very good film and left the back of a card still a little rough after several coats with hours between each coat. If you want a spray finish I would recommend spray lacquer. It is clear finish, can be quickly applied with several coats just a few minutes apart and easily builds a nice protective film. However, to ensure that no spray would run onto the back of the cards when I was spraying the front and leave an uneven finish, I used brush on semi-gloss polyurethane. It took a little more time doing each card individually and waiting a number of hours between each coat, front and back, but the end result was definitely worth the time. There is much more control with the brush than the spray can and it left both sides perfectly smooth and with a rich shine.
Step 6: Etching the Copper Lid
With the cards finished it was time to work on the box. I wanted the whole design to be based around plywood with copper inlay. So the fist thing to do was make a copper etched plate that would be set into the lid of the box.
1.) This computer drawing is the one that you are going to want to spend the a large amount of time on. You will be able to see a large amount of detail and the more you include, the more impressive it will be. Having more detail doesn't make the next steps for etching any more or less difficult so have at it. I took a photograph of the house my family had lived in before the house that was etched onto the back of the memory cards. I spent between 5 and 10 hours using the photograph as a guide in drawing this house. Don't rely entirely on the photograph, draw some perspective points to work with so everything looks the way it should. I used Autocad for my straight lines and definite curves and then exported as a .PDF to open in Adobe Illustrator and sketched the bushes in with the pencil tool and adjusted the line weight. Know the size of your copper plate and how the cards will fit in a box that size before you make your final size image.
2.) Once you have finished the drawing, mirror it in Adobe Illustrator so that when the ink is transferred to the copper it will be in the correct orientation. Send the file to a print shop that prints on transfer paper. Transfer paper is similar to overhead transparency but is used specifically for transferring toner with heat.
3.) When dealing with your copper plate use gloves at all times so your oils do not interfere with any of the process. Tape the transfer paper to the copper plate. Let the transfer paper over hang the copper plate and tape it from the back with blue painters tape. This is just to keep the film in place in the beginning. Ounce you start heating it, the toner will adhere to the copper. The image should look like the correct orientation when you tape it to the plate. This means the ink side is against the plate.
4.) I used an iron I had bought for about 10 dollars to heat up the transfer paper. The transfer should take about 15 minutes. Use the edge and tip of the iron to scrape against the plate to better transfer the toner. When you are done transferring you can let it cool completely and then pull the film back slowly and see what spots you missed, then put it back and fix those spots with the iron. Or if your really certain you did it right and are too excited to wait for it to cool down, just plop it into a bucket of water to quickly cool and then peel the film off. What you should have is a nearly perfect transferred image.
5.) I found a plastic container big enough to hold my acid and copper plate. I then mixed two parts hydrogen peroxide to one part hydrochloric acid. When it is mixed the acid is clear but once copper is introduced to the reaction, the acid turns green. You can also use ferric chloride as your etchant, as I have in the past, but after doing some research on the subject mixing muriatic acid and hydrogen peroxide was a better etchant. Then I just set my copper in the acid. The longer you let it sit, the deeper the etch will be be. The acid will only bite the areas that have no toner. I had done a test on bronze first and let that sit in the acid for about 5 minutes. I let my copper plate sit in the acid for between 15 and 20 minutes and it turned out great. Use goggles, gloves, and common sense, when dealing with acid.
6.) Pull the copper out of the acid bath and put in a container of water mixed with baking soda. Use a tooth brush to scrub the plate and make sure the reaction is completely neutralized. Use acetone or lacquer thinner to remove the toner from the plate and see what you have yielded. Still being careful not to get finger prints on the plate.
More information on the acid mixing can be found here: https://www.instructables.com/id/Stop-using-Ferric-...
Step 7: Finishing the Plate
When the plate is done being etched it's time to seal it so it will be protected from finger prints and time.
1.) There are a couple of ways to seal this plate. One is with lacquer and the other way is with Johnson's Paste Wax. I would recommend the pasting wax because it is easier to remove and fix the plate. Also a friend told me that the copper "breaths" better through pasting wax.
Optional Steps:
When I did my plate, I had not known that baking soda was needed at all so I didn't end up stopping the reaction. I then sealed the copper in lacquer immediately. The copper continued to react and turned green underneath the lacquer. With a recommendation from a friend, I removed the lacquer with lacquer thinner to scrub it with baking soda. In the process I removed some of the reddish patina that had developed from the acid and consequently the color of the raised lines and background blended. I then cleaned the whole plate until it was all the same color with a dull shine using Brasso. I removed the protective polish with lacquer thinner. I ended up buying a new product to create a darker patina to correct the mistake and it came out beautifully. So if a dark patina is what you are looking for, this is the way to do it.
1.) It was recommended to me that I purchase liver of sulfur to make this dark patina. I purchased an extended life gel form of the chemical. Follow the directions for how much to mix with warm water in a plastic container and place your copper inside. It should almost instantly become nearly black. When it is done in a couple of minutes, take the copper out and rinse it in clean water.
2.) Take some #0000 steel wool and rub it with the grain of the metal. Go in the same direction so that any marks will be in the same direction. Now the steel wool will take back the patina. It will give the the lines of the image a dull satin shine because they are the highest parts of the copper plate and it will make the background a nice chocolate brown color.
3.) After this I sealed the copper with pasting wax. Johnson's Pasting Wax is for wood, metal, plastic and leather and has great feel to it. Just put it on the copper with a clean cloth, wait for it to dry to a haze and then buff the wax off with a clean rag. I did two coats on each side of the plate.
Step 8: Designing the Box
After the card and copper plate were all done, it was time to design and make a carrying box. I used 1/2" and 1/4" birch faced plywood to match the cards. I used a simple joint for the box. I used half laps that I could easily cut with the table saw and dado blades.
1.) I made the lid first so it would fit the copper plate. I cut thin strips of 1/4" plywood and mitered the corners together to make a sort of picture frame for the plate and glued the wood pieces together. Then I cut a rectangle out of 1/4" plywood to glue to the bottom of this frame. The rectangle was a half inch shorter than the frame on all sides so the half inch plywood walls could easily rabbet into it. I glued those two pieces together
2.) Next I cut the sides of the box to the the height I wanted off a big piece of 1/2" plywood with the circular saw and cut them to the right length on the sliding miter saw.
3.) I cut a 1/2" rabbet 1/4" deep on either side of the front and back pieces of the box. These rabbets would accept the side pieces.
4.) I made the bottom by cutting a rectangle the size of the box out of 1/2" plywood. Then I cut a 1/2" rabbet 1/4" deep on every side. These rabbets would accept all the side walls of the box.
5.) There was going to be a removable inside component to the box so the cards could easily be removed and put away. I just cut a a rectangle out of 1/4" plywood the size of the bottom of inside of the box. I put a 1/4" dado 1/8" deep through the middle of this rectangle so another 1/4" plywood piece that over hung each side slightly could be glue perpendicular to it and act as a handle to lift the inside out.
6.) To have the inside accept this sliding inside piece, I cut slots in the sides of the box. What I had done was use the table saw to first divide the sides of the box into sides of the lid and sides of the bottom before cutting the slots in the side walls for the inside component. This was to avoid having slots in the lid.
7.) Just glue the lid together squarely and glue the inside component but do not glue the bottom of the box yet so wire inlay can be done to the front of the box easily.
Usually it is best to make a box as one piece and then cut in into two pieces on the table saw to make sure that the lid and bottom of the box line up perfectly. However to make wire inlay easier, I glued them together separately. So it is important to make sure that the lid and the rest of the box are glued squarely so the two pieces line up.
Step 9: Copper Inlay
To give the box more copper to the design, I made some copper wire inlay. I used the router, table saw, drill, and vice to make these inlays.
1.) The lid has a slots cut in it on all sides with the table saw to hold copper and aluminum wire. Just pick some strands of wire to braid together. I took 3 strands of thin copper wire and placed all three in a vice and put the other ends in the drill. Then I just spun the copper wire together into a braid. I repeated this one more time for copper wire and one time for even thinner aluminum wire. Then I took all three of the braids and braided them together to make a braid of braids with two different kind of metal. The whole braid was about 1/8" thick and I glued it into the slot around the lid with liquid super glue.
2.) By twisting a few copper wires together I made a handle for the inside component of the box. Just drill a couple holes in the plywood and glue the wire in with gel super glue.
3.) You can either free hand router your wire inlay for the front of the box or what I did was make an Adobe Illustrator template. I wrote the family name inside a rectangle I drew that was the size of the front of the box. I made sure the letters were roughly 1/8" thick, printed it out, and secured the paper to the front piece of the box with a little spray adhesive. Set up some wood pieces with clamps to hold the front piece of the box down while you trace out the letters with a router. The extra wood pieces that are clamped down against the front piece keep the clamps out of the way of the router and the sander. I twisted some thicker gauge copper wire together to get a 1/8" braid. I glued the copper in with liquid super glue.
4.) Now sand the front piece with an orbital sander or wait until the box is put together and use a belt sander to make the copper flush with the plywood and get any excess glue off. Use a belt sander to make the wire inlay in the lid flush and remove excess glue.
5.) I bought some copper nails at the hardware store just for good measure. Drill some small holes into either side of the front and back. Drill just far enough to get through the first piece so the nail fits through it and then hammer the nail in the rest of the way. I put the nails in after the finishing because because they had their own coating of tarnish resistance.
Step 10: Sealing the Box
Now that everything is completed, the last step is to seal the box. Since there is copper inlay, I would suggest either lacquer or Johnson's Pasting Wax because they bond to metal better than polyurethane. Spray/brush lacquer would better match the way that the cards are sealed as a clear film building finish but pasting wax would make the box match the copper plate's finish. I used pasting wax because the feel of the finish is soft and more natural than any hard plastic type coating of a film building finish. Also as said before the wax will let the copper breath better.
1.) Use boiled linseed oil if you so choose before putting the wax coat on. The oil brings out the color and grain of the birch. Just pour the oil onto a rag and rub it into the wood and wipe off the excess with a clean cloth.
2.) Rub the wax onto the box with a cloth, wait for it to dry to a haze, and then buff it off with a clean cloth. Don't over apply the wax in one coat. Instead of putting a lot of wax on in your first coat, do several coats of a small amount of wax. I did 3 coats of wax.
3.) Pick out a hinge for your box. I had the choice between aluminum hinges to match the wire in the lid or I had the choice of antique bronze to match the copper plate's patina. I chose the bronze hinges. Just screw the hinges on the inside of the lid and on the outside of the box. These hinges were thin enough that I didn't have to cut any slots out of the lid. I also put gel super glue behind the hinges and on the screws to help keep them from pulling out of the wood over time.
4.) Use some gel super glue or epoxy to glue the copper plate into the lid. That's the finishing touch to the memory game box of memories. There is really no need for a clasp but if you desire one I would recommend some rare earth magnets inside the box. Just drill two small holes; one in the lid and one in the lower part of the box and glue the magnets in.
And of course enjoy!
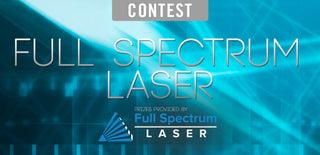
Participated in the
Full Spectrum Laser Contest 2016
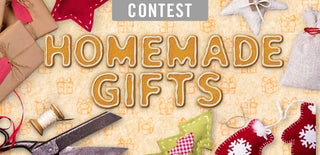
Participated in the
Homemade Gifts Contest 2015
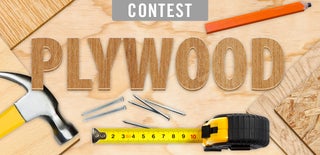
Participated in the
Plywood Contest