Introduction: Metal Sandbox Excavator With Realistic Scooping Motion
A few month ago I started welding and was looking for a first project to practice it. I thought about building a sandbox excavator and looked up some designs online. I didn't like the designs of the sandbox excavators you can buy, because they are only moving the lower arm, but not the scoop (and most off them look very wobbly)
I wanted to have a design where the scoop is turning inwards to get a more realistic movement of the excavator. Since you can only have two handle bars to manually control the movement of the excavator, the scoop movement had to be connected to the lower arm. To design this I used Fusion 360.
I have actually planed to finish this project before christmas. Due to another lockdown in Austria, this will not be possible. I still have to finish some final steps, but most of the work is done. So I thought I could already publish this instructable.
Supplies
Step 1: Design of Scoop Movement
I first started to design the bodies of the upper and lower arm of the excavator as well as the scoop. For those parts I have tried to copy the design of a real excavator as close as possible.
For the scoop movement I have chosen a 4-bar linkage to connect the movement to the control of the lower arm. The lenghts and joint positions of the 4 bars are very critical to get a good movement. Worst case could be, that the movement works in only a very small area and locks itself very fast. The linkage can be calculated, but I just used Fusion 360 to make a design study. I set up a parametric model and tried to move the values around until i found a linkage design that did not lock and had a nice trajectory. I added a few pictures to show different positions during the trajectory.
I then created an aditional control rod to connect the movement of the lower arm and the scoop mechanism to the handle bar.
During the design phase I tried to avoid any possibilities to squeeze fingers between the moving parts. The parts are either very close together so you can't put fingers between them, or they have a bigger gap in between so the fingers won't be squeezed.
I didn't design the base frame with the seat in advance. There I just thought about improvising it when the arm assembly is build up to get the proportions right.
Step 2: Parts and Build Up of Scoop and Excavator Arm
After designing the parts of the arm it was time to start building. The side surfaces of the bodies are rather complex and the positon of the holes in the parts for the linkage are cirtical. That's why I have created cardboard templates of those parts with a laser cutter. This also had the advantage, that I had the possiblility to test the linkage design in advance. This reduced the risk of spending a lot of time in welding up all the components just to figure out there is a mistake in the design.
When I was sure that the linkage is working, I transfered the templates to the sheet metal. For this I used 2 mm steel sheets. To cut out the components from the sheet metal I used an angle grinder. This was a lot of work and a big mess in the workshop. I think if I would do it again, I will consider ordering those parts laser cut somewhere online.
Additionaly I needed the bottom/top surface sheets to create a rigid body from the sides. I didn't create a template for those, because they where just straight strips of sheet metal.
One thing I have totally underestimated was the distortion during welding, especially for the thinner lower arm. When I was done, I recognized, that the part is bend to the side a little bit. Fortunatly I was able to straighten it back with a hydraulic press. But from that moment on I payed more respect to clamping the parts down properly while welding and spread the heat input equaly over the whole part.
The upper arm has a opening on one end where the joint to the lower arm sits. I first welded the whole outer shell and then used a 20mm drill bit and an angle grinder to open up this area again. Then I welded the inside surface.
Step 3: Build of Rotary Base Frame
After finishing the arm and scoop of the excavator, I thought about how to build the base frame. The requirements it had to fulfill were:
- Mounting interface for the arm assembly
- Seating area
- Integration of the wheel bearing to allow the rotation of the upper part
- Strong base for the whole excavator
- Mounting interface for the gas pressure spring
- Height adjustment of the seating area
On the pictures you can see that I have choosen to go with two parallel 30x30mm square tubes. There I have conneceted the ball bearings for the arm and also included a mounting plate for the wheel bearing. On top I will mount the wooden seating area.
The metal arm assembly is quite heavy. I thought that this weight will be too much for a kid. That's why I have added an adjustable gas pressure spring. This worked out much better then expected. The whole weight of the arm is compensated by the spring force. Only little force is necessary to move the arm.
The bottom of the wheel bearing is connected to a plate and a piece of 40x40mm square tube. This matches the inner diameter of a 44x44mm square tube and allows it to slide inside of this piece. Thats how I realised the height adjustement.
To finish all of I used to more rails of 30x30mm square tube and connected it with some U-shaped connstruction to the height adjustment.
Step 4: Final Steps
As I have mentioned in the beginning, I was not able to finish this project before christmas. There are a few final touches that I still have to do, but most of the work is done.
Since this excavator is supposed to stand outside in the sandbox it is necessary to add some rust protection. I have the possibility to use a powder coating machine, that's why I have chosen this to cover the whole assembly and protect it. The base assebly will be black, the arm and scoop will become yellow.
To make it more comfortable to use, I will add a wooden plate as a seat and some rubber bicycle grips on the control arms.
All in all this was much more work then I have expected, but also great fun. The goal of the project was to improve my welding skills, which I think worked out well. I hope the kids will enjoy playing with it once it is finished.
This was my first instructable. I hope you liked it and I was able to describle the process so it understandable.
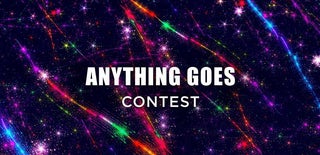
Participated in the
Anything Goes Contest