Introduction: Modding Inexpensive Car Door Hinges Into Expensive Greasable Hinges
One problem that is common in older 3rd Gen F-Body GM cars is the door hinges wear after the thousands of open-close cycles that they have seen. The newest of these cars are now 23 years old. The doors sag slightly and become difficult to close. Many hinge repair kits are available, the expensive ones cost as much as 100 bucks per hinge for ones that could be greased, on the other side of the price spectrum good basic hinges can be obtained for $8.50 from Amazon.
The only difference between the expensive ones and the basic is the grease fitting. One can mod an inexpensive door hinge into the expensive style using a lathe.
The parts that you need for both doors on a 3rd Gen F-Body GM cars are:
1. 2x Dorman 38401 $8.50/ea on Amazon
2. Lathe with 4-jaw chuck
3. 1/32 drill bit
4. 0.230" to 0.235" drill bit (15/64 = 0.234375")
5. 4x Alemite 3054-B $0.50/ea on Amazon
6. 1/32 lathe cutting tool.
The Alemite 3054-B fittings are thread-forming and need an untapped hole from 0.230 to 0.235" in diameter. The grease nozzle is angled at 90 degrees for access in tight spaces such as is needed for the doors on the car. Any 90° grease fitting will work but you may have to add a step to tap the hole. These worked slick.
The only difference between the expensive ones and the basic is the grease fitting. One can mod an inexpensive door hinge into the expensive style using a lathe.
The parts that you need for both doors on a 3rd Gen F-Body GM cars are:
1. 2x Dorman 38401 $8.50/ea on Amazon
2. Lathe with 4-jaw chuck
3. 1/32 drill bit
4. 0.230" to 0.235" drill bit (15/64 = 0.234375")
5. 4x Alemite 3054-B $0.50/ea on Amazon
6. 1/32 lathe cutting tool.
The Alemite 3054-B fittings are thread-forming and need an untapped hole from 0.230 to 0.235" in diameter. The grease nozzle is angled at 90 degrees for access in tight spaces such as is needed for the doors on the car. Any 90° grease fitting will work but you may have to add a step to tap the hole. These worked slick.
Step 1: Drilling the Side of the Bolt
For this step use the 4-jaw chuck and a 1/32th or smaller drill bit. A 4-jaw lathe chucks allow each of 4 jaws to move independently, permitting elliptical or in this case off-center placement of a work piece.
Using a 4-jaw chuck capture the bolt with the center of rotation is in the middle of the portion where the bushing will ride.
Measure how far your grease fitting will extend into the bolt once you are done and be sure the hole is not into the threads.
Take the time on each bolt to double check the alignment is on axis (center of the side of the bolt) with the drill bit, if the axis is even slightly off the drill bit will be pushed by the bolt rather than be able to drill into the side. Drill approximately half way through the bolt.
For these bolts the bearing surface was .595" dia so the depth chosen was .30".
Using a 4-jaw chuck capture the bolt with the center of rotation is in the middle of the portion where the bushing will ride.
Measure how far your grease fitting will extend into the bolt once you are done and be sure the hole is not into the threads.
Take the time on each bolt to double check the alignment is on axis (center of the side of the bolt) with the drill bit, if the axis is even slightly off the drill bit will be pushed by the bolt rather than be able to drill into the side. Drill approximately half way through the bolt.
For these bolts the bearing surface was .595" dia so the depth chosen was .30".
Step 2: Grease Grove
A three jaw chuck may be used for the remaining operations and the bolt is m
Using the small lathe cutting tool make a grove for the grease to flow into once it is installed. The grove insures that grease can flow into the bushing, if there is no grove the bushing can seal off the hole and prevent grease from getting in. Much like how one can plug a garden hose with their finger even though most cities water pressure is more than 40psi.
The grove only needs to be .010-.020 deep. Be sure the grove intersects the hole.
Using the small lathe cutting tool make a grove for the grease to flow into once it is installed. The grove insures that grease can flow into the bushing, if there is no grove the bushing can seal off the hole and prevent grease from getting in. Much like how one can plug a garden hose with their finger even though most cities water pressure is more than 40psi.
The grove only needs to be .010-.020 deep. Be sure the grove intersects the hole.
Step 3: Drill Pilot Hole
Using a 15/64 drill bit for this step.
Drill down till the cross drilled hole is intersected.
If an air hose is handy the flow through these holes can be verified by blowing into the pilot hole and feeling the cross drilled hole for the air.
Drill down till the cross drilled hole is intersected.
If an air hose is handy the flow through these holes can be verified by blowing into the pilot hole and feeling the cross drilled hole for the air.
Step 4: Thread in Grease Fitting
The last thing to do is thread in the grease fitting, these fittings required a 3/8 wrench and just turn the chuck by hand gives enough force to thread.
The drill chuck can be used as a guide to help start the fittings.
Any 90° grease fitting may be used but if yours are not self tapping you need to add a step to tap the holes for them.
That finishes these hinge bolts.
They are ready to install saving over $150 by making these simple modifications to turn the inexpensive bolts into expensive ones.
Good luck on your project!
The drill chuck can be used as a guide to help start the fittings.
Any 90° grease fitting may be used but if yours are not self tapping you need to add a step to tap the holes for them.
That finishes these hinge bolts.
They are ready to install saving over $150 by making these simple modifications to turn the inexpensive bolts into expensive ones.
Good luck on your project!
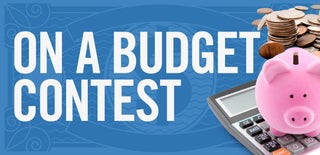
Participated in the
On a Budget Contest