Introduction: Mosaic Eye Knife Handle Blank
In this Instructables, I am going to show you how to make a mosaic slab. So there is an idea came in my mind why not to make a mosaic slab because I have already made some mosaic pins which are usually used in knife handles. I decided to make a whole handle slab out of these pins so that I can use that as my knife handle. The beautiful thing about this build is that you can make an infinite pattern with these pins. There are literally no limitations to the design. The more pins you add the better the design looks. Mosaic pins are always the main key features of any knife handles. It completely changes the overall aesthetics of your blade. I heard from many peoples that are making mosaic pins is very difficult, but it's just a rumour. If you are also in one of those then believe me just give it a try. You can watch the full tutorial on my Instructables post. I have to say that making mosaic pins is really the easiest job in knife making. Just give it a try. But one thing I have to admit that making mosaic slab is definitely a little difficult task than the pins. Just kept the vision clear in the mind because there are infinite ways to make the pattern. The chances are high that you may divert from your original plan. There are many things you can make with these pins more I am going to bring if I got access to a lathe. If you have suggestions feel free to post them.
Supplies
Material and Tools Needed
Following are the material I use for this build
1. Brass rod 1.6mm and 3 mm.
2. Brass tube 2 mm, 4 mm, 6 mm and 10mm
3. Aluminium rod 1.6 mm 3 mm and 4mm 30mm pipe (25mm id)
4. Copper tube 4mm 8mm 10mm and 12mm.
5. Glow in dark pigment
6. Black Powder for colour
7. Two part epoxy.
8. Acetone to degrease
Following are the tools I uses for this build
1. Pipe cutter
2. Wire stripper
3. File
4. Sand paper
Step 1: Material Cutting
To cut down the material you can probably use any tool you want but for thin tube try to avoid power tools and try to use hand tool as they are quite delicate and if end gets crimped then it would be difficult for the resin to flow. I didn't cut the thin brass tube and decided to fill them with resin first and then cut them with a cutter. Before cutting I first clean down all the rods because once they cut down to smaller pieces it became difficult to do. I remove all the oxidation layer from the pipes with 220 grit sandpaper. Once the pieces have been cut down I start the marking process and there is much easy way I found, I cut down the 10mm tube in which I am easily able to insert remaining thin tubes. This 10mm tube acts as a template and I insert them over the tube and made a mark then move downward and again made a mark and kept continue onto all the pieces. The tubes have diameter 4mm and larger cut with the help of pipe cutter and thin rods are cut down with the help of wire cutter. The 1" aluminium pipe is also cut down with pipe cutter. The cut wasn't straight that's why I need to file down this piece. Once the material cut down I put them individually in a separate container to keep them organised. The thin tubes are filled with resin and filling process is very simple if you are using a syringe. Just suck the resin-filled with pigment and then fill it in the tubes. Because of this method, the resin gets into the tube with syringe pressure and remove air from the tube. Once the resin is cured you can cut them in required sections. If you wanted to kept them empty then try to cut them with jeweller saw. Although if you are willing to keep a see-through idea you can probably fill it with clear resin. By doing that it has both strength and the purposefully achieved.
Step 2: Cleaning Process.
Once the material has been cut down I start the degreasing process. I pour them in acetone and kept them stirring for about 1-2 minutes and black residue come out of the material. You can use any degreaser but acetone works way faster I think. But this process is important because if you didn't perform this task then it may have a lack of strength.
Step 3: Constructing the Iris
So for my handle design, I decided to go with an eye look and first thing I decided to make iris of the eye and this is important for me to do because the entire thing is going to wrap around this iris so it would be good if it's dimensions are known. I kept the 1" (id) pipe in the middle and then wrap 6mm copper tubes around it. The space around the pipe is not plenty enough that I am able to wrap it with all the copper tube so that's why I have to use two-piece of brass of smaller diameter which is 4mm. So its completely depend upon your creativity that what you are going to make and if there is an area where you can't able to put the desired size of the tube then probably change the dimensions of the tube, that's the reason why I go with so much different sizes of tubes. All of this pieces are temporarily attached with a tiny drop of ca glue which helps to bond the all tubes until the final resin process has been carried out. I also flush down the one end so that it remains perfectly straight when I place is onto the table.
Step 4: Creating the Eye Shape.
So after the iris has been constructed I start the outer shape of the eye. For that, I made a layout onto the scrap ply by place the iris and also kept in mind that I have to make it for a knife handle not too big not to small. I go with a 4.5" long handle which seems feasible to me according to my hand. Then I have a scrap piece of laminate laying in my workshop and then made an eye-like shape in which I going to shape down my pins in the shape of an eye. I use tape to hold the laminate to the required shape and then apply tape over it so that it would be easy to separate the pins from the template. Then I lay the pieces in such an order that It looks beautiful and I am also able to get that contour shape with those pins at my required length. Then I straighten them out and then glue them one by one with a tiny drop of ca glue. After a few seconds, I get that eye shapes. I repeat this process two times until I get both the upper and lower shape to complete the eye design.
Step 5: Preparation Before the Resin Pouring
Once the eye work is completed I place them over a scrap piece of ply. Onto that, I apply some tape so that it would be easy for me to remove the mould from the ply. Then I place the iris first and then place the upper and lower section of the eye. At the two ends, I am going to use copper tubes in which orange pigmented resin is filled as I did with those thin tubes. From hereafter the main creativity begins. So you can either use mosaic pins filled with a different colour of resin and then use them so that you are able to get that different colour look. I also did the same thing here. Few pins are constructed separately. The procedure is simple just put the pins in one another either first filling them with different colour resin and then insert them in a bigger tube which is capable of holding those smaller tubes. So as I said this completely depends upon your creativity and you can use different ways to construct the pattern. I also wrote an instructable over mosaic pins you can check that also. The iris is also filled with different pins patter. The middle is filled with 12mm of copper tube and then around it, some brass and aluminium rods are filled.
Step 6: Resin Filling
Once the preparation is done its time to fill the resin. For that, I first mix the glow in dark pigment into the resin and then also it to set for 2 hours. The reason for this is because the glow in dark powder particles is slightly heavy so if the resin is quite viscous then pigment particle didn't settle down. For thin tubes, I filled the the the resin with the help of syringe so that I am able to avoid bubble formation in the thin tubes because with the help of syringe the resin enters into the tube with pressure as compared when I poured it directly over the top. By direct pouring, it mostly depends upon gravity. Once the resin has been cured I remove the case and check the work and it looks beautiful. I never did this task so definitely gets excited to see the overall result. For a few pins which didn't have any other pins in them I decided to change the colour a little bit, so I drill those holes and filled it with black colour resin. Make sure not to drill too fast and avoid overheating. If you have resin which capable of holding little bit higher temperature then it's not a big problem for you.
Step 7: Sanding and Finishing
Once the block has been cured after the second pour I start the sanding process and for that I use a couple of different power tools and hand tool combination but I after one grind with the angle grinder I avoid it and use belt sander and files to make the block bring to the final usable dimensions. I constantly cleaning the belt to avoid the belt clogging so that it removes the material at a much faster rate. I did the sanding work up to 120 grit because in the knife the finish is going to be done after reshaping it.
Step 8: Conclusion and Final Thaughts
Overall said I really like the overall outcome of this slab and this is what I planned during the starting of this build. There are slight minor issues here and there but I think with practice and more care you can avoid them. Just tried to keep your pieces nice and straight ends so that they can stand straight while you pouring the resin. Initially, before starting this project this is just a thought but it's felt good to see the end result. The only motive is that try to share an idea which can be used in many different ways like drawer knobs, handles, rings etc. Probably the possibilities are endless with resing and pipes.
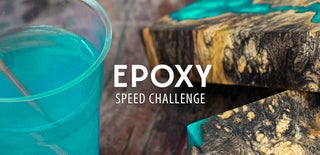
Participated in the
Epoxy Speed Challenge