Introduction: Most Simple DIY Electric Skateboard With Optional 3D Printed Parts
This is probably the most simple open source DIY electric longboard project, this project is basically plug N play, easy to build and fun to ride!
- Budget for mechanical parts and electric components: $220 (USD)
- Budget for a longboard with adapted wheels, trucks and deck: $80 (USD)
- Overall budget: $300 (USD)
- Build time: 4 hours to one weekend
- Theoric speed of my current setup: 30km/h – Average effective top speed with my settings: 28km/h (I reached 38km/h on a flat road with perfect condition but it's way too scary!)
- Theoric range of my current setup: 25km / Effective range: I can ride it for 20km
This page is detailed and aims to popularize the concepts and use of each component for beginners. For advanced makers, please use the part list with the components and the basic wiring diagram.
Please check the full and enhanced tutorial on my website: http://eboardmaker.com/build- e lectric-longboard-tut...
Check my Electric Mountainboard build here
Pay me a beer on Paypal to say Hello and/or Thank you!
Here are a few videos:
[Play Video]
[Play Video]
Before to start, please check the following requirements:
- Learn how to ride a longboard first, it’s very important to learn skateboard basics before to start this project. This will prevent you from injuring yourself by taming the engine’s propulsion in addition to attempting to manage your balance and steering.
- This project requires tools and specific equipment. I personally add to use a soldering station because my batteries’ connectors were not standard and I had to use a hot glue gun, a hex key set, an electric screwdriver, my rotary tool to adapt my truck to my motor mount and to create a handle in my deck. These tools could be totally optional and I will detail one setup below that require just some tapes, screws, hex keys and sockets. I would like to recommend to buy a skateboard tool as it brings together all the socket sizes needed to set your trucks and wheels and a screwdriver.
- Always wear a helmet and appropriate protections before attempting any and for the use of your e-skateboard, you can seriously injure yourself if you are not careful and properly equipped.
Step 1: Basics and Considerations
An electric vehicle needs basically a source of energy, a motor and an electric speed controller, a transmission that will drive the wheels with the help of the motor, and a controller to send the signals to the electronic speed controller.
Motors
Brushless for RC models are commonly used for electric longboard project, mine is a RC Car motor.
These motors are usually categorized by their KV rating. The KV rating refers to the rpm constant of a motor – the number of revolutions per minute that the motor will turn when 1V (one Volt) is applied with no load attached to the motor. It is related to the power out from a motor, or more usefully the torque level of a motor. In summary, a low KV motor will produce higher torque, a higher KV motor will produce higher speed but less torque. Suitable motors for electric skateboards obviously need to have high torque (between 150kv and 300kv).
ESC = Electric Speed Controller
An electronic speed control or ESC is an electronic circuit with the purpose to vary an electric motor’s speed, its direction and possibly also to act as a brake. ESCs are often used on electrically powered radio controlled models, providing an electronically generated source of energy for the motor.
The first important aspect of the electronic speed controller is the voltage and current rating, which must not be exceeded. An ESC should always indicate how many volts you can pump through it and this is often expressed in how many cells you can use (the number of cells your battery has). For this project, you will use an ESC that is able to handle 6S batteries (22.2V). You need also to look at the current rating (maximum AMPS) and make sure your motor draw will not exceed that. Most motors will say how many amps they draw (MAX AMPS) and this rating should never exceed the amp rating of the ESC. Actually, you need an ESC that can support very high amps as they usually are more resistant and will tend to behave better with lower amp draw. Most modern ESC contains microcontroller interpreting the input signal and appropriately controlling the motor using a built-in program, or firmware. this firmware can be configured by using a programmer. I will explain how to configure the ESC I use.
Batteries = Source of energy
Just like the motor and the ESC, the LiPo batteries used in this project are widely used for Radio Controlled Models. These are rechargeable batteries of lithium-ion technology using a polymer electrolyte instead of the more common liquid electrolyte. A LiPo battery is defined by:
- its cell number (also referred as “S”: a 3S battery having 3 cells) which define the voltage (see bellow)
- its voltage, determined by the number of cells. Tere are a few common voltage measurements worth noting:
- Charged: the voltage of a fully-charged LiPo cell is 4.20V. A fully charged 3S pack is 12.60V. Please note that charging above this will damage the cell.Nominal: this can be considered a sort of “half-charged” voltage, as it is 3.70V, in between charged and discharged.
- Nominal voltage is what manufacturers use when describing the voltage of their batteries. For example, a 3S battery is marked with its nominal voltage of 11.1V (3.70V*3 cells).
- Discharged: the voltage of a discharged LiPo cell is 3.00V. But we consider that discharging below 3.3V will definitely damage the cell.
- Storage: When you want to store you battery for a few weeks or months, I strongly recommend to charge or discharge each cell to approximatively 3.80V which is the most stable state of a cell.
- its discharge capacity, exprimed in with an integer followed by “C”. The C rating of a battery tells you how many amps can be safely drawn from the battery constantly. By multiplying the C rating’s coefficient by the capacity of the battery in Ah, you can determine the sort of amperage you can draw. In the case of a 3S battery with a capacity of 5000mAh (5Ah) and a C rating of 20C, I can multiply 20*5 and get the max constant output of my battery, which is 100A. You will want that this max constant output is equal or above the max amps rating of your motor.
- its capacity, measured in mAh (milliamp hours). This basically tells you how long you can expect the battery to last on a charge. A 5000 mAh is equal to 5Ah (amp hours), which means that the battery can discharge at 5 amps for one hour, 2.5 amps for 2 hours, etc.I will recommend a list of batteries for this project and the adapted chargers BUT using LiPo batteries requires special attention and misuse of these batteries (such as complete discharge, shock, hazardous storage, etc.) can lead to a start of fires and serious injuries.
I strongly recommend to read this safety guide and to check this guide to learn more about Lipo batteries. Note that you can use for this project one 6S LiPo Battery or two 3S batteries in Series. Plugging two batteries in series means that you will double the cells and so the voltage for the same Amps capacity, in contrary to the parallel wiring that double the amps capacity for the initial number of cells (or initial voltage).
Transmission
The transmission is composed of a timing belt that connects a small pulley attached to the motor and a large pulley attached to one wheel.
- Timing belt: A timing belt is a flexible and non-slipping mechanical drive belt with teeth molded onto its inner surface. Multiple types of timing belts are available but for this project, I use a 5mm Pitch HTD Timing Belt of 9mm wide. HTD belts have been designed to withstand loads.
- Motor pulley: The motors pulley is way smaller, with a small number of teeth (usually between 12 and 18 teeth). You have to be careful of the pulley bore diameter. For this project, I use a 12 teeth pulley 8mm bore.
- Wheel pulley: This pulley is larger (with a higher number of teeth, usually between 35 and 40) and is attached to the wheel. I used a 36 teeth pulley that threaded through the cogs of the Abec 11 wheels with a large washer on the outside.
Step 2: Parts
This setup is composed by 2x 3s 5000mAh Batteries, a 280KV motor, a 120A ESC. You just have to plug everything together. This build will cost approximatively 300 USD. You are free to source similar parts on your own, but note that I have tested this part list and it works well. Using any other parts is your own responsibility: check the specifications of the suggested parts to be sure that it matches your locally sourced part. Finally, you will find all the 3D model I used for my prototypes, including the wheel pulley that I found on Thingiverse (credits: Brent Yi).
- 1 x Longboard deck (You can check the deck guide here)
- 4 x 83mm Flywheels. (please check the wheel guide here)
- Any 180mm Truck. If you order the previous deck, just add these 180mm truck to your cart. (please check the truck guide here)
- 1 x Brushless Motor - 5060 280KV 4-12S (diameter 50mm, Lenght 60mm)
- 1 x FVT 120A Waterproof ESC (Favourite 120A Car ESC)
- 2 x 3s 5000mAh batteries
- 1 x Programming USB interface for the ESC
- 1 x Motor mounts and pulley set for 83/90/97 flywheels . If you already have different wheels, check the alternative parts to find the appropriate pulleys and motor mount set.
- 1 x T-Plug series cable
- 2 x Lipo checkers
- 1 x Charger . You need any charger with at least 5Amps charging capacity
- 1 x Power supply + 1 Power chord adapted to your country.
- 1 x Remote control +1 x 2.4ghz radio receiver - NOTE that you have to buy the remote and the receiver separately from the same product page. (A more expensive but smaller alternative is available here)
- 1 x Plastic box for the enclosure (Note the dimension of the batteries you use and find the appropriate box)
Tools and Misc.
- Hot glue gun
- Epoxy glue (if you can find the one suggested, it's the strongest Epoxy I have ever seen, it's strong as hell)
- Any Duct tape (choose your favorite color)
- 4 Wood 6-8mm screws (or equivalent) to fix the battery enclosure to the deck
Optional parts
- Print the ESC enclosure + 4 Wood 6-8mm screws (or equivalent) to fix the ESC enclosure to the deck
- Print the motor mount and use one M4-25mmm screw with locknut
- Print the fasteners for the battery enclosure and use 2 x M3 10mm + 2 x M3 lock nuts (or equivalent) to fix the fastener to the battery enclosure
- 2 x Straps if your plastic box does not have clasps
All 3D printed parts are available on Thingiverse on https://www.thingiverse.com/thing:2474716
Please note that these files are under Attribution-NonCommercial-ShareAlike 2.5 Canada (CC BY-NC-SA 2.5 CA) license.
Step 3: Build
- Assemble the trucks to the board
- Add the wheels to the trucks but leave the drive wheel apart
- Add the motor mount to the truck and make any required adaptation to adjust it (sanding, filing...) and put some thread-locker to the motor mount screws.
- Add the motor to the motor mount
- Add the small pulley to the motor's shaft
- Add the large pulley to the drive wheel
- Add the drive wheel to the trucks with the belt and then adjust the belt to both pulleys
- Tension the belt by adjusting the distance between the motor and the truck
- Follow the wiring diagram for the electronic components and fix everything to the deck with hot glue, duct tape, a 3D printed enclosure...
- Enjoy!!
Please note that I used different connectors, as explained on my website because I used 8000mAh LiPo batteries on my board. This tutorial covers exactly the same setup but with 5000 mAh and everything is just plug N play.
Step 4: ESC Configuration
In this section, I will explain how to install the programming application on your computer, update the FVT 120A ESC (Favourite Car ESC 120A) firmware and program the ESC settings.
- Go to your computer
- Download and install the programming application
- Download the ESC firmware for electric longboard (please check the last version of the Linear brake "BrakeLine" firmware)
- On your computer, open the programming application
- Go back to you ESC: verify that your ESC power button is in the OFF position
- Connect the ESC to your batteries (Use the Wiring scheme)
- Plug the JST connector to the USB programming interface
- Connect the USB interface with a Micro USB cable
- Push the power button of the ESC to ON position
- You should see that the link status for ESB Device and ESC device are both green
- Click on Update Software and follow the procedure until you hear a beep and you can see the ESC settings
- Change the settings as follows:
- Motor timing: High (Increasing timing increases rpm and motor temps but decreases torque, efficiency and run time.)
- Initial acceleration: Soft (allow to accelerate gradually instead of being ejected right away)
- Running mode: Forward w/o Reverse (it means that the motor will only for forward and never backward)
- Percentage braking: 30% ( I AM still experimenting braking by playing with both drag brake and brake percentage, I will update this section each time I improve my results)
- Percentage Drag brake: 7%Cut-off voltage: 3.2V
- Throttle limit: 100% (if you are a beginner I recommend to set the limit to 60% or 80% to limit top speed)
- Throttle percent reverse: irrelevant for me as I will not use the reverse so I am using the original value
- Motor rotation: Reverse in my case but you might have to use the other value if your motor is not rotating in the correct direction)
- Neutral range: 9%Batt type: Lipo
- Start power: 30
- Click on Send settings, you should hear a beep
- Shut down your ESC and disconnect the programming interface, you are good to go!
For more details, please check the FVT 120A ESC manual
Step 5: Issues
Vibrations
I had a lot of issues in my first test with the bad conditions of the street in Ottawa and Montreal (Canada). I have to use Aluminium Motor mount instead of my 3D printed files because the roads are so bad that I had some cracks on the motor mount (violent vibrations). Also I lost one screw from the motor mount during my first ride and the screws on the wheels were all loose after a few minutes. I resolved this with some Thread locker and I also have reinforced my motor mount on the truck with JB Steel reinforced Epoxy glue.
Carrying the board
A DIY electric longboard is not very light and I move every week to another city where I work so I wanted to carry my board more easily. I designed a Handle Bar in the deck to carry the board with a Dremel tool and then I wrapped the handle with a Tennis racket overgrip to make it comfortable.
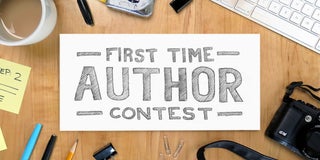
Runner Up in the
First Time Author Contest
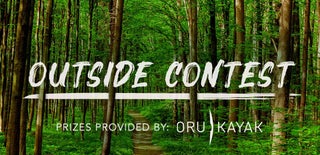
Participated in the
Outside Contest 2017