Introduction: Movable Dock, Lego Style Brick Legs, Under $300 Part I
The rules were simple in the HOA: you can build a dock, but it has to be removable. In other words, no permanent fixtures can be done. No pilings, no cement. Challenge accepted.
Step 1: The BOM
I decided this portion of the dock would be 5' x 10'. In order to keep the cost (and weight) down, The top of the dock was built with the dog ear pressure treated fence post ( https://www.lowes.com/pd/Severe-Weather-Common-5-8... ) also available at home depot. This is a really cheap 5/8 x 6 board, it has the added advantage of being rough cut and not sanded. This is perfect for a dock as the rough surface is not as slippery. The drawback is it is very thin. To compensate for this all I had to do was decrease the spacing of the beams from the normal 16" to 10" I actually built this one even tighter spacing of 8", but I'm quite sure you can go with 10".
BOM
11 2x6x10's pressure treated
2 2x4x10's pressure treated
1 2x4x8 pressure treated
26 5/8 x 6 x 6' pressure treated dog eared fence picket
1 box of 1 5/8" deck screws
1 box of 3" deck screws
12 16x8x8 cinder blocks
7 16x16x2 cement pads
5 12x12x2 cement pads (for leveling purposes)
1 16x8x4 cinder block (for leveling purposes)
to be added later:
section of chain for the anchor
cinder block for an anchor
maybe pipe sections for ground anchors
not used:
55 gallon drums.
as my deck is very shallow water (under 2' deep) I didn't have to float the deep end of the dock. but that was an option at one time.
Step 2: Wood Shop Work to Start.
With the wood at the house, I might as well take advantage of the woodshop to prep some of the wood with all the tools rather than have to drag them to the shoreline. to start, the dog ears come at 72" tall. we cut them down to 60" on the radial arm saw. While we are at it, ever sit on the edge of a dock with your legs in the water? you need to round the edge of the wood so the angle doesn't cut into your leg. lets take care of that now as well. You'll want to sand one side of the pickets rounded and you'll want to do it so the warp is against the beams, so pick which side to sand based on curve of the grain on the edge (look at the picture.)
We'll need joists and end caps for the dock out of 2x6, so we cut 2 of the 2x6x10's in half to make 4 pieces of 60" length. Since we are in the shop lets take advantage of the clamps and combine the endcaps and beams in L brackets. here and now.
Step 3: Build the Beam Structure
Now its time to lug all this stuff to the worksite. Also note I always pre-drill all wood before putting deck screws into them. It just works better that way. I use the 3" deck screws when connecting 2xbys to 2xbys, and I use 1 5/8" deck screws when I connect the dog ears to the 2xbys.
we are working upside down for now, as in the bottom side up. we stand up 2 2x6x10's, and put the L brackets that we made over the ends and complete the rectangle by screwing the bottom part of the L bracket to end beams. just one screw for now as we will have to skew the rectangle (actually parallelogram, ) into a perfect rectangle. Screw down all 4 corners. You'll notice in the pictures I put everything up on cement pads to give me good access under the assembly.
At this point we have a parallelogram, as in opposite sides are parallel to each other. In order to make sure all the angles are at 90°, we have measure the diagonals and make sure they are the same length. when you measure them you'll notice that they are not the same, you'll want to push the corner of one of the longer diagonal more towards the center of the assembly. when both diagonals are the same, then the dock is truly rectangular.
Once all the beams are nailed down, lets turn the dock over so the top is face up. (last picture.
Step 4: The Double Secret Trick to Making Rectangle Stay: Adding the Triangle.
So you've made the dock nice and rectangular, but how do you really keep it that way? When you put the planking down if you do it at 45° you'll make it really strong as you'll have a triangular structure. We'll do that next time. For this time however we are going to add a single triangular brace out of a 2x4x8. the triangle keeps the rectangle from skewing (look it up on the internet.) Now I could just off attached the triangle to the bottom before I flipped it over, but then the bottom won't be flat, and I'll need a flat bottom later on for either the floating barrels or cinder block footings, so what we'll do is a neat trick of putting the diagonal inside the beams by notching out the inner beams.
As my lovely assistant vanna is showing, we place the 2x4 across the beams with the ends just on the inside of the outer beams. we draw on the 2x4 a diagonal line sorta where we want to cut off the ends so they fit a little better. it doesn't have to be exact, but when we cut off these ends the 2x4 will fit a little better and closer to 45°.
Lay the 2x4 down in position on the beams so the the ends come pretty close to the outside beams. Take a pencil and draw on all the inside beams where the 2x4 passes the beam on both sides. This will give you the cut line to notch out the 2x6 beams.
Set your circular saw to a height such that is it about 1/8-1/4 inch wider than the 2x4 and cut on the pencil lines. The cut won't go through the entire 2x6, you'll have over 4 inches of thickness under the spot where we notch out the 2x6.
Now comes the fun part, take a big flat head screwdriver and a hammer, and bang it into the wood on a line between where the cuts go through the 2x6. to both ends, and then the middle. then do the other side the same way. My guess is before you get to the sixth bang in, the piece of wood between the cuts will crack out. All of mine did, some of them cracked out by the third bang. Clean up the notches with a hand saw if you have too.
If you did it right, and at the right depth, the 2x4 will fit nicely into the notches and be flush with the top of the beams. put 3" deck screw into all the beams through the diagonal.
Step 5: Doing the Planking.
This is pretty straightforward with just 2 tricks. The first one and most important is you need the spacing between the planks even. Somebody is actually selling a toll to do this, All I did was use a 3/8" bolt, put it through a paint stick and use that, In the pictures I show a 8d nail. I tried that first but I felt the spacing was too thin so I use the 3/8" bolt instead.
Work from both side evenly towards the middle. I highly doubt that this will work out evenly so when you get to the last 3 or 4 planks, its time for the next trick.
Step 6: The Last 3 Planks.
So I'm down to the last 3 boards and as you can see, they won't fit. The space isn't big enough. Rather than cut down one board by the total amount I need to reduce things by, I'm gonna cut 3 boards 1/3 of what I need. With the 3 middle boards cut down, nobody will notice that they are not as wide. I took a ruler and measured what space I did for 3 regular boards, and then I measured the space I needed the 3 last boards to take up. Be careful! the space includes an extra gap (see the pencil drawing.) I think the math is shown pretty clear there as well.
Also note the jig was set up to rip the boards. Ripping a board (cutting with the grain,) can be tricky and potentially dangerous, so take you time and mind the safety conditions.
Step 7: The Lego Footings.
If you remember, this dock has to be removable so nothing permanent can be created. Cinder blocks and cement pads are very cheap, heavy, but not too heavy to be lifted. As the deepest footing I have to make is 17" deep, I am simply going to stack these items and interlock them in a way I can easily undo it.
First we make a 10 foot ruler so we can see where the footing should basically go. The layer that is touching the bottom of the lake is a 16"x16"x2" cement pad. These of course where not level when I put them in the water and using a regular brick or two, a 16"x8"x4" cinder block, I wedged the smaller bricks/cement stuff under the corners to level the 16x16x2 cement pad.
Due to the underwater terrain, one footing was 2" lower than the other footing, to fix that I simply added another 16x16x2 pad on top of the shorter side pad. In fact, I then wanted the footers to be taller so I added another layer on top of both, so I had a 3 high on one footer, and a 2 high on the other,
On top of the stack of pads, I placed 2 layers of 16x16x8 cinder blocks alternating the split of the stack. this was actually quite stable as is, but I really wanted them locked together, like lego pieces, so I cut a 4" pvc pipe into 8 pieces 12" long, and dropped them into the holes of the cinder blocks (see pic) Now there is no way a cinder block can slide out. Just to really secure it, I traced the hole pattern onto a piece of marine plywood and cut 16x16 square, gorilla glued 2x4 squares to it to make a top for the footer that locked the 2 cinderblocks together.
The shore side was just a single 16x16x2 cement pad and 2 cinder blocks set up in a square. I also made a line of 12x12x2 cement pads under the edge of the deck so no ground contact would happen in case the footings settled.
Step 8: Final Assembly
now at this point, the footings it turned out didn't align with the end beams of the L brackets I originally hoped would be the support for the deck. I had to add 2 (well I added 3,) 2x4's to act as beams so all the joists would be supported. they were places so they would be on the footings. Alas to attach them I had to flip the whole dock over again. Surprisingly I could do it myself, one person.
Once done, I flipped it back, and then my son and I dragged the dock out to the water. The deck was reasonably buoyant, (well it is wood, and wood is supposed to float,) so we were able to move it into position and then drag it up onto the footings.
Once in place I was amazed how solid, sturdy, and steady this dock was with only gravity holding it down onto the footings. I will put an anchor chain and cinder block anchor onto the dock incase it gets knocked off so it doesn't float away, but other than that, this part of the dock is done. It is so solid the two of us were jumping up and down on the dock, trying to rock it forward and back while on it, and we couldn't even get the footings to make a ripple in the lake.
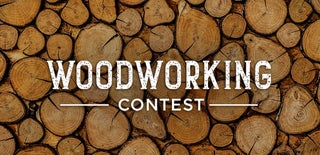
Participated in the
Woodworking Contest