Introduction: My Rebuilt Boat Galley
I never thought anyone but me would care about my struggles with scrap wood, so I didn't document my project as well as I could have. As I worked on it I began dreaming of all the power tools that I wish I owned to re-work my scraps. The dream of winning a planer to compensate for future wood shortages is a strong incentive for publishing my first instructable.
What you see here is the finished product of a classic effort to put a square peg into a round hole. I have a commercial fishing boat on Kodiak Island. I had a diesel oil stove serving as both heater and cooking appliance. Diesel stoves burn continuously, so they aren't the most economical or thrifty devices. Worse, the diesel stove would occasionally backdraft and turn the entire cabin interior black and hideously filthy. I dreamed of that nice propane stove for years before finally taking the plunge. I had no idea that something so simple could turn so complicated. One of the biggest complications was the discovery, after ripping the galley apart, that the local lumber store had stopped carrying the high grade okoume plywood that I had expected to use. Thus this project was eventually pieced together from some old marine plywood scraps, and old pieces of tropical woods from a burn pile I had not yet torched in my yard. In the end I was extremely grateful for my laziness in not cleaning up the yard sooner.
Step 1: The Demolition
Here we see a before and after view of the old stove with barely functional drawer beneath, and the hole after tearing back wood to a reasonable stopping point. I really mean "tearing" the wood too. In the after shot you can see that the outermost layer of plywood has been ripped off the walls where old wood strips were glued to them. Every piece of wood originally installed in this boat was glued and screwed. One thing anyone will learn in this sort of project is that some extra destruction is inevitable. Don't worry. Anything can be filled back somehow. It may not look the same, but almost anything in this world can somehow be glued back together.
One thing that can't be seen is the alarming amount of diesel fuel that had soaked into all of the wood over the decades. The shelf where the old stove sat burned like a candle for 20 minutes when I finally torched the scraps. You can't re-use diesel soaked wood, no matter how tempting!
Step 2: Cleaning Up the Area.
My remaining wood was pretty filthy and there were signs of old salt water leaks. I was really worried about that dark floor, since it is a double layer of old mahogany plywood and the sheets extended under the entire cabin area. I was afraid that diesel oil had soaked them too. I got really lucky here. Despite all of the filth, etc, I managed to sand and clean everything back to find good wood everywhere. This demonstrates exactly why certain woods are used in marine applications. This boat has been frozen in winter, soaked in various mishaps (Yes, in the interior!) and generally abused and neglected for years on end. If searching for overlooked sources of high grade salvage, never underestimate an old boat.
The funny little triangular points in the third photo are examples of sanded wood vs the filthy wood. I was using an orbital hand sander that couldn't get into the corners. This mess was really much filthier than the pictures indicate.
Step 3: Pondering the Hole—nothing Is Square!
I can't stress this enough! Nothing on a boat is square! That floor is on arched joists. The back wall in this photo is curved, and neither of the corners at upper left and right are anywhere close to being right angles. The board bolted to the wall across the top of the picture is not level with the floor. The boat itself is not level! Since it is a fishing boat, the trim changes as it is loaded with fish. As the boat sits in this photo, the whole boat is tilted aft and listing slightly to one side.
How do I make a level shelf for my stove? What about a level countertop beside the stove? How will I make level—or square— drawers? I'm not a carpenter, and I'm certainly not a skilled boatwright! I do have some basic carpentry tools, and a table saw and radial arm saw gained in a garage sale deal some years back.
Around the time of the sanding shown in the last step, I discovered that the local lumber store no longer sells the beautiful okoume plywood that I wanted to use for a nice interior finish. They do carry "marine plywood" though, starting at about $40 for a 3/8" sheet. True marine plywood uses a special glue and all of the voids are plugged, so it is strong but not pretty. The special glue resists warping and delamination in wet conditions, but, like the rest of the boat, even marine plywood tends to get curved from bad storage, though it does actually begin with square edges. Adding to my lumber woes was the fact that I did not want to spend a fortune on marine plywood. I was already racing past zero on the bank account.
At this point I was so screwed. What I did have is a collection of scraps and a pile of trash wood from an earlier demolition of another part of my boat.
Step 4: Keys to Reconstruction
The photo above represents plenty of painful obstacles overcome.
Something must be square. The propane stove is square. This problem was ignored with the old stove. It sat on a much larger shelf and had big gaps all around it. Spills and hideous stuff fell into those gaps and I could never clean properly, so I wanted the new stove to be flush. If you are paying attention you will notice that I have stainless ball bearing drawer slides installed, and those do not tolerate anything more than the slightest deviations from being perfectly parallel. I set myself a problem that is difficult to appreciate until faced with it yourself.
There is a solution to this problem, coming from the world of mapping and surveying. A base line is established, and all further measurements are made from that initial line. ALL measurements... and it is easy to fall back into a perception of level or square that doesn't exist!
At the top left of this picture is a wood strip that remained after demolition. I had a big carpenter's square that rocked slightly when placed against the wall on top of that strip. Pushing/rocking in one direction defined my starting line. The top side of the wood strip slopes slightly toward the empty space. THE LINE, NOT THE WOOD STRIP is what defines all measurements!
From my starting line I could shoot across to the upright panel at the right, forming the upper line of a face panel. I could also go straight down. Therefore the lower wood strip at the left could be marked and placed. A line can also be shot from the lower wood strip across to the right side. That gives a roughly matching vertical line on the right side of the gap. I took the wall at left to be an "approximately flat" surface so that I could hold the big square against it to shoot across the open space. It's not flat. Don't take this simplistic explanation as a simple task. Measure, measure, measure!
Step 5: Multiple Flat Planes
Yeah, I repeated the same picture plus another view of my starting point, but this time concentrate on the wood strips around the top of my project. For my countertop to sit flat and match the stove top, all three sides of the space—that is, the two upper wood strips and the top of that right side panel—left after demolition need to be in plane with each other. The top of that vertical panel at the right had a big trim piece that I ripped off. The upper left and back strips were close enough to consider them to be in the same plane, and I could sand down the top of that panel on the right side of the hole. All of this was aligned by setting a big carpenter's square and a 4 foot straight edge in endless configurations and eyeballing until I was convinced that I was screwed no matter what I did, so I might as well call it good.
Remember, the top sides of these wood strips are not level or straight. Only a reference line where each strip meets the wall is in plane. The top of that panel on the right (looking at the empty hole) is actually bowed with a dip in the middle. It's way too late to sweat the small stuff.
First hurdle: Fit a new vertical panel to parallel the existing panel in order to support the drawers.
Before working out the vertical support, I measured, measured, measured and did plenty of sketching to figure out the drawer sizes. Then I cut out the face panel, including the holes for the drawer stack. This gave me a way of establishing the front of my new drawer support panel. That face panel doesn't really support any weight but it sure ties the room together.
With a reference plane established around the top, I could measure down at various points and across the face plane. This gave initial roughing marks for the new vertical plywood panel that supports the left side of the drawers. You can see where the plywood face panel meets the top of the new vertical plywood support section. That point is mostly square in all three dimensions. The bottom and back edge of the support piece is anything but square. It took hours to carefully trim bits away until it was flush against both the wall and floor. At the same time the top of the support needed to remain in the same plane as the strips around the top edge of my space. Big tip: you can freehand cuts on a table saw! I had one set up with guards and fence removed and the blade cranked up high. I sort of wiggled the board against the blade to carve wood away. It works better than using a jig saw or handheld radial saw.
The drawer holes in the face panel are square with each other, but the face panel itself isn't quite square either. It required some gentle trim. The face is flat in the "vertical" front plane though. That is important for the drawer faces and stove front to align with each other.
Step 6: Straightening the New Plywood Support
Let's keep in mind that ball bearing slides are supposed to have something like .003" of tolerance. I don't see how anybody gets that close in residential construction, but this was an even trickier situation.
This whole project is a mix of plywood scraps of different thickness, and few if any were close to flat. The ball bearing drawer slides are very demanding. I needed a stiff square box for the drawers. Once shaped to the back wall and floor, the new support panel was gently tapped into place with wooden blocks on the back wall until it was perfectly straight. Some of the small blocks needed to be moved multiple times, since screwing them down some times made them drift back and forth. Referring to the picture above, the raised support strips where the drawer slides are attached are there as much for their stiffening action as for alignment with the face panel of the drawer box. What eventually became the counter top was also cut and drilled at this time to hold the upper edge of the support in place. I'm showing the photo with counter top in this step because I accounted for it at this point though the actual photo was from a later point.
Maybe I'm not expressing it well, but what I did was bend and peg a bunch of twisted scrap wood into a stiff box that was almost perfectly square on the front, left and right sides.
In order to do something like this with scraps, it is advisable to do some serious sketching of the plan, with dimensions of the various scraps and their placement. Note that the drawer slide is screwed to a strip that is flush with the face panel. I spent some serious time with a tape measure and all of my wood pieces to come up with a cutting plan. Since I had limited wood scraps and really didn't know what I was doing, I spent lots of time marking my scraps with a pencil before I finally cut them up. I had 3/8", 7/16", 1/2", 3/4", and 1" thicknesses and there were a few small surprises in trying to match things up.
Step 7: Fitting the Boxes
It was not so difficult to cut the material for the drawers perfectly square by using a radial arm saw. Again, I spent some serious time measuring and planning beforehand. I think there are three different thicknesses of scrap material there. Look carefully at the bottom drawer and you can see that the front of the box doesn't match the height of the sides. You can find the same thing at the backs of the drawer boxes. I was a tiny bit short on material. The bottoms and the ends were routed to make rabbet joints and the boxes were epoxied together. They came pretty close to being square.
The width of the drawer slides (that is, the distance between the two vertical support walls) was beyond adjustment at this point, but they do have some slotted screw holes. I took a shot at something close to square to install the bases inside the cabinet, and then I used the slots on the drawer parts for initial attachment. This gave a tiny bit of wiggle room to orient the drawers correctly. After testing, the drawers were removed and permanent screws were put through the round screw holes to hold the slides permanently in place.
There is a good reason why the drawers are shown being installed from the bottom up. It was so much easier to reach into the cabinet that way.
Despite all of my incessant measurement and fretting, it was a moment of amazement when I got the third drawer installed and saw that I had hit all of the planes and lines in space correctly!
Step 8: The Stove Shelf
Here I'm showing a picture from later in the project, but it illustrates the next step. The stove shelf was pretty straightforward and beneath it a larger drawer for pots and pans was added. Just when you think it is all smooth sailing though, disaster is just around the corner. For one thing, if you were to review the "pondering the hole" step, that piece of lumber bolted at an angle to the wall happened to cross the stove shelf diagonally. I wish I had a picture of that, but I'm not going to pull the stove out just to get one.
There is a bigger yet more subtle problem lurking. This is a boat, and space is always tight. The stove door needs to open, and the big bottom drawer needs to be able to extend out on its slides. Rather than explain it, take a close look at two pictures above that perfectly show my space issues. The back door of the cabin protrudes slightly into the space. Sure, I took my starting line from the same wall where the door is installed, and like I said earlier I also took the starting wall to be approximately flat... but it's not. In the end the stove door and the bottom drawer each had less than 1/8" of clearance. Given the odd twists and curves I didn't have a very good way of proving the clearance beforehand. I was hoping for a bit more, but it works.
Also, at this point in my project I was running out of scraps. To trim the hole around the big bottom drawer, I cut some scraps to fit and began sticking small blocks of wood behind them. The trim pieces are a mishmash of mahogany steps and several exotic hardwoods. I don't know what sort of wood it is, but several pieces already had holes drilled through them. I carefully mapped out how to re-use existing holes wherever possible, and then used the last scraps as backing blocks all around the back side of the trim pieces.
Step 9: Fitting the Stove
I wanted that stove to be tight so it would be able to survive somebody being tossed into it during a big storm, and believe it or not the whole thing is designed to be held in place by two little screws at center bottom. As shown previously the stove door also needed to pass the back door as it opened. Here the stove was fitted and then removed so I could finish trimming its hole.
At this point I added one more hidden feature. Among my pile of saved crap are scraps of fiberglass cloth and epoxy. I covered that stove shelf and the walls in a layer of epoxy and cloth to make it waterproof for the inevitable gusher of soup, gravy, or who knows what that will get spilled everywhere one day. I don't want that nasty mess that I found in demolition to be repeated. This is cleanable.
Also note here that I had already added front face pieces to my drawer stack. Those were made from my last good chunk of mahogany plywood. That explains the odd striped pattern around the edges of the drawer fronts. I wanted to use solid mahogany but my only piece was hopelessly trashed.
At the right of the stove the new counter top is already visible. That was also made from scrap. I had a piece of white formica from another project and by carefully arranging my cuts I got just enough out of my scrap to cover that piece of counter, and also a little strip of matching counter that is about to be installed to the left of the stove. As I noted several other times, the wood strips that support the counter pieces along the wall are not themselves level (the common plane is defined at a line where the wood strips meet the wall, rather than the surfaces of the strips), so there is a sizable collection of shims to place the two counter top pieces into the same plane.
Step 10: Finishing the Stove
Here you can see the stove in final position with steel trim pieces in front and on top, plus the white counter pieces on each side. I wanted it tight, but I didn't expect it to be that tight! I ignored the installation instructions and measured the stove directly when sketching everything beforehand. I would not recommend that, but in this case it worked. There is not enough room to slide a piece of paper between the stove and its trim. Measure, measure, measure!
There was a slight hitch in finishing that bottom drawer, still missing in this photo. I was out of scraps. I had to trade a 12 pack to a local guy who does cabinetry for a suitable scrap, and I also had to veneer a 1/16" mahogany layer myself to make it match the other drawers. It all looks the same if you don't stare too closely.
Step 11: Those Damned Drawer Handles!
The ride at sea can be quite violent at times in bad weather, and I had just made smooth sliding drawers on ball bearings.Such an installation is virtually unknown on fishing boats, partly because that sort of construction creates one hellacious slide hammer effect if a full drawer doesn't get properly latched closed. Most boat drawers are sticky and tough to open, which isn't always bad. Of course I had to be different.
I examined literally hundreds of different latches. I went through catalog after catalog after website, etc, and none of them seemed suitable. This was turning into my greatest obstacle, which seemed pretty ironic after going through that hassle to get working drawer slides in the first place. One evening I ended up at Walmart. Yes, we have a Walmart here, supposedly the most remote Walmart in the entire system. Our Walmart is a small and especially crappy one, but I treat it as a source of raw material rather than a source of finished goods. I think of Walmart as a really big scrap pile. After a disappointing review of the Walmart shelves I was sort of staring cross eyed into space when the above solution hit me: Storm door handles!
I've never seen a storm door handle used this way, but it sure makes sense. My drawer fronts are about the same thickness as a storm door. They are fairly cheap and I can buy more of them easily. They are very positive grips to control drawers in bad weather. When a drawer slams shut the storm door latch will positively click shut. I even had scrap storm door latches at home! I did break down and buy all new latches for the boat though.
Step 12: Some Final Trim
There are a few other odd trim pieces that were added to the project. The new stove comes with a wooden cover/cutting board that fits over the burners. When the stove top is in use the cutting board is an awkward thing to have laying around, so I made a couple of blocks out of my remaining mahogany plywood bits to hold it against the back wall. The striped effect of using plywood is especially visible in this photo.
Boat tables and counters almost always have some sort of raised lip. Looking above the topmost drawer handle, one type of teak table trim strip is visible. If one looks very closely at the last picture, a second type of teak trim was used for the far right edge of the counter. Where they meet outside these pictures, and in a place that I carefully sculpted to hide in plain sight, the taller trim profile was rounded down to meet the shorter one. Both pieces were free. Finally, a pair of white trim pieces finish out the back edge of the counter. The white pieces are made from something called Azek, which is some kind of rigid PVC foam that is sold as a sort of plastic lumber. I cut some strips from an Azek board and routed them down into my own custom trim pieces for another project a few years ago. These pieces were scrap bits from the earlier project, which explains the funny angle on the end of that piece to the left of the picture. Also visible is a fairly large gap between the back of the stove and the wall. The stove company, Dickinson, recommends a 2" gap at the back of the stove. Now that I have some experience using the stove I intend to cut a salvage piece of stainless steel from my backyard to form a cover plate over that gap, finishing off the stove trim. I put the angled piece of white trim back there intentionally so that it would slope down to meet the future stainless steel plate.
Step 13: Trash to Treasure!
My boat is not a yacht, but unless you stared closely for several minutes, you'd never guess that I did this all by myself, with no cabinetry experience, using the scrap pile that I had been preparing to torch to clean up my yard. Work boats usually don't have a very high finish level on the inside. This one is on the upswing. Next I want to upgrade my focsle/bunk area up forward into a tiny little miniature pleasure palace. That is sort of a weird thing to do to a commercial fishing boat. These things are made for work, not play, but what's the point of roughing it? I'm not so sure where I'll get my materials in the future though. After turning over my shrinking scrap pile until there was not a usable piece left, I torched all of the rotten or diesel soaked trash wood.
Oh, one more thing. After finishing the stove installation the battered old floor looked so bad that I sanded it down. Then I made a very thick paste out of some laminating epoxy, fine milled fibers, silica powder and some white pigment and troweled it onto the floor. Now the floor is as shiny white as my new counter top, literally almost bulletproof, and I can clean it with acetone if necessary.
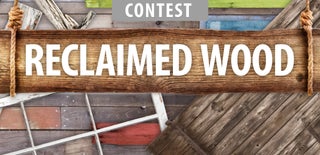
Participated in the
Reclaimed Wood Contest 2016