Introduction: NES Controller Coffee Table
I saw a few NES tables around the internet and fell in love with the idea. However, they all fell in either the "not quite what I'm after", or "there's no flippin' way I'm paying that!" category.
I decided straight away that it didn't need to work as a controller...as I thought the novelty would become a bit old before too long. Instead I wanted something that was a bit subtle, looked good, and showed off some nice wood.
Here's how I made mine.....
I decided straight away that it didn't need to work as a controller...as I thought the novelty would become a bit old before too long. Instead I wanted something that was a bit subtle, looked good, and showed off some nice wood.
Here's how I made mine.....
Step 1: Measure Up
First I got my trusty controller out and hit it with some digital calipers to get all the dimensions.
Step 2: Design
Armed with the dimensions I draw up the face on AutoCAD, scaled it up to the size I wanted (about 1m long), and worked out some details for some basic designs.
I didn't stick too rigidly to the plan...I'm a bit of a geek though so it was important to me to get the top spot on.
I didn't stick too rigidly to the plan...I'm a bit of a geek though so it was important to me to get the top spot on.
Step 3: Let the Build Commence!
There's 3 colours on a NES controller...
Black - Oak
Grey - Maple
Red - Mahogany
I was thinking of using walnut for the black bits...but I really like oak!
First up I went to my local timber yard and selected some nice bits of oak, and got a few maple & mahogany offcuts too.
I cut the oak roughly to size, and fed it to my planer/thicknesser until I had some nice square bits of wood.
Then I glued it together using "Resintite" wood glue (kinda like Urea-formaldehyde adhesive), and plenty of clamps.
When dry the glue got scraped off and I had a good go at it with a belt sander.
Not pictured here...but I got some glass cut at this stage for the top (as I didn't trust them to cut it accurately enough later). Then I cut the oak panel to match the glass.
Black - Oak
Grey - Maple
Red - Mahogany
I was thinking of using walnut for the black bits...but I really like oak!
First up I went to my local timber yard and selected some nice bits of oak, and got a few maple & mahogany offcuts too.
I cut the oak roughly to size, and fed it to my planer/thicknesser until I had some nice square bits of wood.
Then I glued it together using "Resintite" wood glue (kinda like Urea-formaldehyde adhesive), and plenty of clamps.
When dry the glue got scraped off and I had a good go at it with a belt sander.
Not pictured here...but I got some glass cut at this stage for the top (as I didn't trust them to cut it accurately enough later). Then I cut the oak panel to match the glass.
Step 4: Rebates for Inlays
I marked out where all the details on the top were to go, and found the center points of the radius' of the corners.
I drilled little pilot holes and drilled all the corners with a forstner bit. Then scored in lines between the edges of each corner with a sharp knife.
I then took out the bulk using my router at a depth of 4mm. All the rest was taken out with chisel & mallet.
A long day of chiseling later, and all the rebates were done!
I drilled little pilot holes and drilled all the corners with a forstner bit. Then scored in lines between the edges of each corner with a sharp knife.
I then took out the bulk using my router at a depth of 4mm. All the rest was taken out with chisel & mallet.
A long day of chiseling later, and all the rebates were done!
Step 5: Maple Inlay
I took my maple and mahogany and ripped it as thin as I dared, then thicknessed it as thin as I could (just over 5mm).
With a lot of patience I shaped all the maple so it slotted perfectly into the rebates.
Then they got glued & clamped in place, and sanded flush with a belt sander.
With a lot of patience I shaped all the maple so it slotted perfectly into the rebates.
Then they got glued & clamped in place, and sanded flush with a belt sander.
Step 6: D-Pad
For the D-pad, I first thicknessed a bit of oak and made it into a little panel. It then got shaped to fit into the rebate.
It needed a 6mm maple edging though. So I made a template off it using a flush bit in my router, then I rebated off the template with a 6mm rebating bit.
I thicknessed some maple to 6mm and worked it to surround the cross.
Then glued...clamped....sanded flush
Annoyingly, the oak I used for the cross looked completely different from the rest of the tabletop. I recommend just making a 6mm channel and filling it with maple instead.
It needed a 6mm maple edging though. So I made a template off it using a flush bit in my router, then I rebated off the template with a 6mm rebating bit.
I thicknessed some maple to 6mm and worked it to surround the cross.
Then glued...clamped....sanded flush
Annoyingly, the oak I used for the cross looked completely different from the rest of the tabletop. I recommend just making a 6mm channel and filling it with maple instead.
Step 7: Marking Out Letters
Right....now for the dreaded letter detailing!
I found a NES font & nintendo logo and added them to my CAD drawing.
I put masking tape over everywhere there were words on the tabletop, and projected my drawing onto it.
Then traced around the projected words with a pen, and cut through the tape to score the letters into the oak.
This also provided me with a perfect template for the mahogany inlay.
I found a NES font & nintendo logo and added them to my CAD drawing.
I put masking tape over everywhere there were words on the tabletop, and projected my drawing onto it.
Then traced around the projected words with a pen, and cut through the tape to score the letters into the oak.
This also provided me with a perfect template for the mahogany inlay.
Step 8: The Road to Madness
I chiseled the letters out by hand so they had about a 3mm rebate.
I then shaped the mahogany by hand to fit perfectly into the rebates....this took flippin ages...seriously, it was fiddly and delicate and almost drove me insane!
Everything got glued/clamped/sanded flush.
I'm really glad I took my time over this...came out really nice!
I then shaped the mahogany by hand to fit perfectly into the rebates....this took flippin ages...seriously, it was fiddly and delicate and almost drove me insane!
Everything got glued/clamped/sanded flush.
I'm really glad I took my time over this...came out really nice!
Step 9: A/B Buttons
For the red buttons I drilled the center points and defined the edges with an 87mm hole cutter in my drill.
The rebate was made using a router and a little chiseling.
Then I made some circles from mahogany by hand and they got glued/clamped/sanded flush.
The oak start/select button got done in a similar manner (sorry, not pictured)
The rebate was made using a router and a little chiseling.
Then I made some circles from mahogany by hand and they got glued/clamped/sanded flush.
The oak start/select button got done in a similar manner (sorry, not pictured)
Step 10: Maple Edging
It all got a thorough sanding down to 240 grit, then a coat of sanding sealant, then down to 400 grit. Then finished with a clear wax.
Then I planed down the last of my maple, cut it to size, and mitred the corners. They were made to stick above the surface by 4mm so the glass should slip nicely into place.
They got biscuited and glued in place, with a bit of oak veneer in the corners cos I cut them too short....looks good though, lets just say I did on purpose eh?
Then I planed down the last of my maple, cut it to size, and mitred the corners. They were made to stick above the surface by 4mm so the glass should slip nicely into place.
They got biscuited and glued in place, with a bit of oak veneer in the corners cos I cut them too short....looks good though, lets just say I did on purpose eh?
Step 11: Table Top Done!
Some more sanding sealant and wax, and that's the table top done!
Step 12: Legs
I cut the oak roughly to size and planed/thicknessed it nice & square.
Then marked out the ends, and cut the mortices for rails...using a morticer. I then cut them to length.
I decided to put tapers on the legs, so made a jig for my table saw.
The tapers looked great...but left me with some scorch marks that took ages to sand out.
Then marked out the ends, and cut the mortices for rails...using a morticer. I then cut them to length.
I decided to put tapers on the legs, so made a jig for my table saw.
The tapers looked great...but left me with some scorch marks that took ages to sand out.
Step 13: Rails
I planed/thicknessed the oak for the rails, then cut to length, then cut tenons.
For the rail on the front I marked out where I wanted the draws and drilled all the way through with a forstner bit.
I then cut between the holes with a jigsaw to take out the bulk.
The edges were formed by tracing along a straight edge with a flush bit in the ol' router...then I spent too damn long sanding off the burn marks that left me!
For the rail on the front I marked out where I wanted the draws and drilled all the way through with a forstner bit.
I then cut between the holes with a jigsaw to take out the bulk.
The edges were formed by tracing along a straight edge with a flush bit in the ol' router...then I spent too damn long sanding off the burn marks that left me!
Step 14: Drawers
I had some pine for the drawers kicking about so I cut the back and sides, then cut channels for the drawer runner and base (6mm ply). I put a strip of ply across the front of the drawer to make things a bit easier later. It all got glued together & clamped.
I then made the runners for the drawer from some more softwood I had in the shed...I've always struggled with drawers in the past so totally over engineered em to give as little play as possible, but without being too tight.
Then I made the drawer fronts so there would be about 1mm gap around them and the face rail.
I then made the runners for the drawer from some more softwood I had in the shed...I've always struggled with drawers in the past so totally over engineered em to give as little play as possible, but without being too tight.
Then I made the drawer fronts so there would be about 1mm gap around them and the face rail.
Step 15: Glue It Together
The base got glued together, then the drawer rails glued in place.
I then sanded it down to 240grit, gave it a good coat of sanding sealant, sanded it down to 400grit, and waxed.
I glued the drawer fronts in place with the drawer closed so I knew they'd fit just right.
Last of all I attached a "push to open" fixing to the rear of the draw - you push it in a mm or so and it pops open by itself, meaning there's no need for for handles on the front.
I then sanded it down to 240grit, gave it a good coat of sanding sealant, sanded it down to 400grit, and waxed.
I glued the drawer fronts in place with the drawer closed so I knew they'd fit just right.
Last of all I attached a "push to open" fixing to the rear of the draw - you push it in a mm or so and it pops open by itself, meaning there's no need for for handles on the front.
Step 16: FINISHED!!!
And there we go!
Right then...anyone want to commission me to make one for you?!
hickscustomfurniture@hotmail.co.uk
Right then...anyone want to commission me to make one for you?!
hickscustomfurniture@hotmail.co.uk
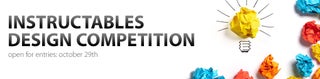
Participated in the
Instructables Design Competition