Introduction: New Ripping Fence for an Old Triton
A couple of years ago I bought an old Triton Mk 3 saw bench from Gumtree for about $125. Frugality is both a necessity and a principle of my lifestyle and I rarely buy new shiny things. I'm also possessed by a 'fixing things' gene I must have inherited from my father who got it from a long line of male tinkerers and craftsmen in the truer sense of the word. It means I have the knack of solving all sorts of problems and that's what I set out to achieve with the old Triton.
Well, I suppose I got what I bargained for - a rusty, ancient, very orange 'Thingy' for slicing up wood (and bread bricks if need be). It looked rather like a giraffe with its spindly legs and patchy finish. It still looks like a giraffe with its new bits, but unlike a giraffe it cuts wood. It came with an old drawer brimming with interesting ' treasures', none of which I really had a clue about or thought I needed. I had barely whisked it out of a friend's boot, than I had hitched up to its underside, another old relic gathering dust in the shed, a 9 1/2 inch Hitachi circular saw. Toot, sweet! Feeling a great deal of trepidation, I switched it on and swoosh! someone else's sawdust jetted into the air. I passed my first plank through it. It was a revolution and revelation far too great for one so attuned to simplicity, so I switched it off and went for a walk.
This past two weeks has been spent in myopic concentration building a great many gadgets for it. That all started because I gave my shed a Swedish death clean, and well, that gets one thinking about how good a shed can be when everything is working well and systems have been put in place so that creativity and chaos do not have to occupy the same limited space. Not for the first time in my jill of all trades life, improved productivity seemed to be a thing.
I soon realised the limitations of a Triton giraffe a few months into its introduction to my workshop. It didnt have a blade height winder, through slots, a fence that could glide as if on ice, dust ports, visible cutting width gauges and a proper riving knife. I could have gone back to Gumtree and bought something more suitable, but that's not the way i operate in my resource challenged lifestyle. So I set about adding the improvements that could be added. I've learned a lot from Instructables masters and Youtube gurus who have such spotless work environments, that I've considered moving mine into the house and sleeping in the shed. Nah, not really, but ambition is a driving force in my life even if it's not about wealth building and more about having it all by having less. Less chaos and a working sawbench was a good start.
It now has a modest crosscutting jig, a new ripping fence based initially on a design found in this link
https://www.instructables.com/id/DIY-rip-fence-for...
and the transformative blade height winder in this link
https://enredandonogaraxe.club/en/homemade-table-s...
Thanks in spades to all the true geniuses of this planet and thank goodness because without them my own backyard engineering would be far less impressive, if not a reason for falling about laughing at my own folly.
Supplies
I bought nothing. Lousy consumer, me. I recycle everything. Have to. Bunnings is over 80km away and I only ride a bicycle. The plywood is old scrap from the skip at the local tip or my kindling shed. The timber was salvaged from scraps from past building projects and from other people's reno skips. Every bolt, nut, washer and nail is from something else. A few screws and the copper pipe for the height winder are new-ish remaindered from building projects. The unirail is a length salvaged from a dismantled solar array. Below is the cutting list in millimetres and parts list for the ripping fence. It was all predetermined by the materials immediately available to me and a degree of deep, logical thought and lots of cups of tea. Anyone else could do it differently but hopefully this list shows that it can be made from just about anything.
- Front: Hoop pine VJ 1100x70x20 (1)
- Rear: Ironbark 1100x70x20 (1)
- Base: Plantation pine 1100x60x20 (1)
- Rail Supports: Ironbark 1000x70x20 (1) Dressed pine molding 1000x68x19
- Infill blocks: Form ply 60x50x16 (6 - two at the outfeed end for extra reinforcement)
- Sled guide block: form ply laminated to face ply - 4 layers - top 250x90x12 (1), mid carriage section 250x90x18 (1), lower outer guide layers 250x30x18 (2)
- Rail supports: Backing piece bolted to Triton bench - Ironbark 1000x50x20, Base piece Plantation pine 1000x65x12
- Guide rail: Unirail aluminium track for solar modules 1000x60x20
- Auxiliary guide (feed end): plywood 150x7x25
- Polycarbonate glide: 90x25x2
- Chipboard screws various sizes
- M8 hex bolt 30 (2)
- Locking bolt M8 T-bolt, washers and nut
- Homemade hoop pine handle
Step 1: Main Fence Body
The main body of the new ripping fence is made from two, very straight 1000mm lengths of timber - ironbark for the back and hoop pine for the front and a piece of pine for the base. That's all I had that wasn't bent, twisted, half rotten or too big to break down.
These planks form a channel in which I can stow my pencils, square, push sticks and tape measure, although in practice they are anywhere but the intended receptacle. The plywood dividing blocks give the fence enhanced rigidity. Each plank was cut to measure, hand planed and arrissed and I glued and screwed them together.
I glued a small piece of 2 mm polycarbonate on the base at the feed end of the fence. This has the effect of reducing friction by lifting most of the fence a tiny fraction off the table surface. The polycarbonate is itself super smooth and slightly 'greasy'.
Construction of the fence was fairly standard using glue and screw technology, much careful squaring to the original Triton fence and meticulous measuring.
Additionally, I used a couple of squared blocks and some clamps to ensure plumb and squareness while the fence body was being constructed. Once I had the body made, I could clamp it to the original metal fence, adjusted previously to make the Triton perfectly functional, to be parallel to the blade and true the sled accordingly to it and the new rail.
Step 2: Going Off the Rails a Bit
The guide rail is supported on a length of ironbark bolted to the bench by means of two countersunk M6 hex bolts and a piece of pine molding, again the only suitable lengths of wood available to me on the day.
Initially I had made something similar to the Instructables link above, but wasn't happy with the amount of racking movement and stickiness I was experiencing, especially on moist, cold winter mornings when the tolerances I'd allowed were gobbled up by moisture expansion in the rail slot.
My shed is a tin shed. In other words it doesn't keep much more than the sun and rain out. It's freezing when it's cold and an oven when it's balmy. Climate control amounts to standing in the sunny part at the front or the shady section at the back. The guide stuck so fast some days, I wondered if it was an epoxied T-square addition to the Triton and not a ripping jig. My timber selection( and old silky oak window frame) was proving to be the nuisance, so I tossed the outside rail back on the rack and pondered as I worked on other projects.
The epiphany happened at about 11 pm one evening when it occurred to me that the old solar array I'd pulled off the cottage roof a year ago had been mounted on aluminium unirail. Unirail has the requisite slots to accept T-bolts, it's aluminium and it's very very very straight, in fact it would make an excellent fence by itself, but maybe another time.... I thought it might do the job. The goddesses of full bikkie tins must have been bestowing their beneficence upon me that morning. I always celebrate a win with a homemade bikkie. A single one metre length of unirail with two slots on adjacent faces was leaning against the wall. And the bikkie tin was full.
This piece of unirail was the one thing that stood between me and junking the Triton in favour of the shiny something that already sported the long list of haves and superfluous extras I truly desired. It was in fact the only thing that saved the Triton from a Gumtree expulsion from the dusty, sacred, inner sanctum of my workspace.
I could immediately see how this one fortuitous find was going to function. The top slot would house two guiding T-bolts ( or whatever fit in there) and the side slot would accept a secondary guiding T-bolt that could double as a locking device. All I had to do was make it happen.
Predictably this involved several searches of the kindling shed which is actually a rather grand title for what amounts to half a tank turned on its side into which I tip all my offcuts to keep dry. That yielded most of the plywood for the sled end of the fence. The rest came off the racks, salvaged from skips and from the useless things pile neatly catalogued in a couple of drawers. I keep a bit of that sort of just-in-case junk, though nothing that could be construed as hoarding. It has to fit in two small drawers made from ... yes, scrap plywood and an old apple bin. My workshop is mostly quite ordered, even in its chaotic/creative mode, part of the 'simple as is simple done' code of ethics I follow with and dangerously didactic zeal.
Step 3: the Sled
The main sled at the outfeed end of the fence is made from laminated form ply and face ply scraps. Form ply has an oily, smooth coating that slides beautifully on the aluminium unirail.The face ply was simply the right thickness to make up the difference between the 18mm form ply and the guide rail.
It's the only original design solution I can claim as my own (apart from the polycarbonate glides at the other end), and has two adjustable hex bolts that run along the slot. These can be torqued up and down in the slot to achieve the perfect tolerances so that the whole fence glides smoothly across the table, the bolt heads neither too high so as to bind in the top of the slot, nor too low so as to score the aluminium base. I filed the little numbers and letters off the hex heads and polished them to make them as smooth as possible.
The fence sled glides along the rail almost as if on ice, the main body barely skimming the table's surface. It has virtually no rack and only due to a slight error of tolerance, but not enough for me to bother changing it. I can push it with a feather touch and it will move a millimetre, give it a two finger tap and it will move pretty much exactly where I wish it to go, none of the jerking and careful placement along the measuring guides of the old fence. I used a vernier gauge and a combination square to measure things accurately. The sled construction forms a neat almost press fit channel around the unirail (which is itself a channel), thus ensuring nothing can move more than a skerrick out of alignment.
Step 4: Fence Lock and Handle
I've made a lock by drilling a hole horizontally through the sled block accessing the side slot. An M8 T-bolt that had formerly tied a solar panel to the rail, now slides back and forth in the T-slot when adjusting the cutting width.This wedges the T-bolt firmly into the slot.
It can easily be wound into the lock position by spinning the handmade wooden handle on the thread. The handle was simply jigsawed from some hoop pine scrap and sanded into shape on a linisher. Crude but effective. I could have used a spoke shave for a more traditional finish, but for this I was content to speed up the process with some wood butchery.
The handle spins freely on the machined thread by means of a nut epoxied into a drilled and chiselled recess and the action can be performed quite quickly, both in and out of the locked position. It's centered in the middle of the sled and doesn't interfere with anything being ripped. I've use a couple of standard washers and a thin, convex washer to act as a sort of spring between the handle and the rail to soften the clamping action.
In retrospect, I could have reversed the process by using a hex bolt epoxied into the handle so that its threaded end pressed the other way into the back of the channel, but either way works equally well against the outer blocking of the sled, so I haven't altered it. I've considered melting a thin layer of plastic on each of the guiding bolt heads to protect the aluminium from abrasion, but perhaps that's overkill. Sparing application of a spray lubricant and some beeswax is doing a good job.
Step 5: New Triton Fence Summed Up
The fence is a vast improvement on the short Triton fence that came with the bench. It solves most of the problems I had with the original fence with its short, closed slot travel and having to squint at the measures inside it. I will be replacing the somewhat dulled and damaged tape measures with bright, new ones before too long and the measurements can be gauged accurately from the front edge of the fence body.
It's longer length gives more support for long rips onto a dual use workbench bench at the outfeed end. It glides smoothly and isn't limited by the table slots, by now sliding along the outer edges of the table. It doesn't alter or damage the original table and is fully removable leaving only two small 6mm holes in the outer casing where the rail support is bolted. The longer guide rail enables me to expand the usefulness and versatility of the bench with an extension to house the router attachments that came with it and for cutting wide sheet materials. Additionally, I can use the same fence as a router fence on the new extension, since the rear is as straight and true as the front.
A work in progress is the dust extraction system which will be made from two buckets, a barrel and an old vacuum cleaner. I've added a hardwood zero tolerance insert into the blade slot to stop thin shards of wood from entering and blocking the circular saw safety guard beneath the bench. I'll also make a new riving knife to replace the Triton splitter. I may upgrade to a 10 inch saw but that isnt a priority. After that who knows what I will do with it, but adding a new top with through slots and a router extension are on the cards. You know the sort of thing, doing something for the love of it, but practicality and satisfactory performance as is, may well win out.
There it is, a still rusty, orange'ish Triton workbench that does the same job it's done for nigh on 30 years, only better... well without the awkward moments and rumbles of discontent anyway.
In this article I've focused on the ripping fence. I'll also write another one about the blade height winder, which was a thoroughly satisfying exercise in its own right and one I might have thought impossible looking around the web at other people's solutions, except that, I'm one to tilt at dragons at the best of times...
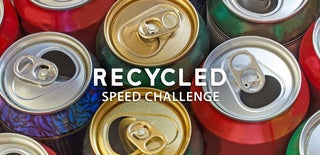
Participated in the
Recycled Speed Challenge