Introduction: No Hole Circle Cutting Jig
In the woodworking world being able to cut out a circle without having a hole in your finished piece is often a necessity. This jig does just that. There is no need to drill a small hole in you finish piece to use as a pivot point. Instead it utilizes double sided tape on a separate piece that has a hole that can be removed after cutting. Be sure to check out my video to see it in action!
There are many jigs out there but I got the general idea from Chris on his YouTube channel Christofix -
https://www.youtube.com/channel/UC0PQBl1PyIR6sqa4S...
I made a small tweak in that I put a coupling nut in the pivot section that allows for small adjustments by spinning the threaded rod. I had a project at the time where I needed to sneak up on a cut to allow one 1/2 round shape to fit into another 1/2 round cutout shape. Being able to sneak up on the cut allowed these two pieces to fit just right. Check out my Instagram page and look for the Brazilian cutting board to see how it came out.
https://www.instagram.com/ltdwoodworks1/
I realize that not every one will have the same trim router but I believe the same principles can be followed to make this work on your own router.
Supplies
3/4" Plywood
1/2" Plywood
Sandpaper
(1) Bearing with a 3/8" inner diameter to match the 3/8" all thread. Outer diameter doesn't really matter.
2 1/4" hole saw
1/4" drill bit
Wrenches
(2) 3/8" Regular Nuts
(1) Slim 3/8" nut
(1) 1/4" Hex head bolt
Small clamps
The above links are affiliate links for some of the items I use. This
means if you purchase anything through these links I will receive a small commission at no extra charge to you. Just a small way to support my channel.
Step 1: Prepare the Pivot Pieces
Using a scrap piece of 3/4" plywood I used a 2 1/4" hole saw on my drill press to cut out 4 circles. The drill press is not needed but does insure a straight cut. I then used some 150 grit sandpaper just to remove any sharp edges.
Step 2: Pivot Point Prep Continued.
I needed to create a hole or channel through what would be two circles put together. This is where the coupling nut would be secured. I achieved this by first laying out some guide lines and then clamping the two pieces together. Once clamped securely, I used a 5/8" forstner bit and drilled a hole all the way through.
Then taking what would be the bottom I counter sunk a 1/2" diameter hole into the wood. Just deep enough to allow the future head of a 1/4" hex head bolt to sit flush.
Step 3: Assemble the Pivot Point
I first mixed up a small amount of 5 minute epoxy and applied it to the counter sunk hole. Then I put the 1/4" x 3/4" bolt into the epoxy ensuring that it was sitting flat, straight and centered.
While that was drying for a few minutes I took what is the top of the pivot and applied more epoxy. Then I set the coupling nut into the epoxy. I then applied even more epoxy on top of the coupling nut and the flat sections of wood and "glued" the two halves together. A few clamps ensured that they would have a nice tight bond while drying.
Step 4: Preparing the Attachment Point
I had first already cut a scrap piece of 1/2" plywood to 1 3/4" wide by around 7". The 7" dimension will be cut down later. Measuring down 1 1/4" I drilled a countersunk hole to the diameter and depth of my bearing. In my case it was a 1" hole about a 1/4" deep.
After test fitting the bearing I then removed it and flipped the wood over and drilled a 3/4" hole the rest of the way through.
Really though, in my case the 1" hole could have been drilled all the way through as my bearing has a flange to keep it from going any deeper.
Now that the hole is drilled, I cut the piece of wood to it's final length of 2 7/8".
Step 5: Preparing the Attachment Point Continued
In order for the wood to sit flush onto the router I had to create a channel or dado into the wood to fit over the little "nubs" of metal on the router. These normally align the edge guide that comes with most trim routers. Marking their location on the wood, I went over to my table saw to cut the channels to the same depth of the "nubs" of metal. I also took care not to continue the cut all the way down the length of wood. Having the hole in the wood made it nice to know when to stop.
Now that the wood fits over the nubs of metal, the clear base was now in the way a bit. So I marked its location on the wood and cut out the wood on the table saw again so that it fit over the plastic base and now flush to the router.
Marking up from the base of the router to the mounting hole of what would be the edge guide, in my case 3/4", I drilled a 1/4" hole through the wood. This will allow the use of the same mounting bolt that comes with the router to be used to mount this wood to the router.
Step 6: Almost There!
With more five minute epoxy I secured the bearing to the wood. Once dried I started to assemble the jig. Taking two regular 3/8" nuts I threaded them onto the all thread a couple of inches. Next, slide the wood with the bearing onto the all thread. Now I put a couple of drops of red LockTite onto the all thread and threaded on the slim 3/8" nut. I had to use a slim nut because of the small spacing between the wood and the router. Lastly, I could tighten the regular 3/8" nuts up against the bearing and lock those two nuts together with two wrenches.
At this point I went ahead and secured the all thread and mounting point to the router using the bolt that came with the router.
Now it's time to thread on the pivot point with the coupling nut onto the all thread. And with the fourth circle piece I had cut earlier I enlarged the center hole to 3/8" and epoxied it onto the end of the all thread. This is to be used as a handle to spin the all thread.
Step 7: Time to Put It to Use!
The way this works is you take the one lone circle piece of wood and adhere two pieces of double sided tape to the bottom. Make sure the wood is sanded smooth for a tight bond. Using a 1/4" drill bit which is the same diameter as the hole that is already in the wood, insert the bit all the way through. This can now be lined up on a marked location of where you want the center of the circle to be. Press firmly and remove the drill bit. Now the rest of the jig with the 1/4" bolt can be inserted into the hole in the first piece that is taped down.
Ideally you can spin the pivot point on the all thread to the distance needed before you put it down on the wood. But you can also just spin the all thread in or out while on the pivot point. This feature makes it nice to fine tune your measurement to "sneak up" on a cut if need be.
All that's left is to cut out a circle. I used a straight cut 1/4" bit in my router to do this. Take your time and be careful. In general you will want to take many shallow passes till you cut all the way through you wood.
Be sure to check out the video to see this in action!
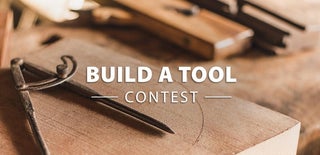
Participated in the
Build a Tool Contest