Introduction: Normalizing Carbon Steels
This is the third Instructable in my series about heat treating of carbon steels.
If you read the preceding Instructables: An Introduction To Heat Treating Carbon Steels and Annealing Carbon Steels then you learned that heat treating is the manipulation of a metal's molecular structure via exposure to specific temperatures. Carbon steel's molecular structure is crystalline and has a grainy appearance. Exposure to heat changes the shape of these crystals. Each crystalline shape exhibits a different set of properties, which can be beneficial in different ways depending on the material's application.
In order to understand the normalizing process, we must also understand the annealing process. The two have a lot in common and are easily, and often, mistaken for one another. There are two primary differences between them however; one is in practice, while the other is in application.
Step 1: The 1st Difference
Above: Microscopic view of Ferrite (top), Austinite (bottom left), Pearlite (bottom right)
When annealing a carbon steel, it is heated above its critical temperature into its transformation range and held for a prescribed time. This causes a phase change in the crystalline structure from what was predominantly ferrite to austenite.
Once the steel has been heated for a time and to a temp appropriate to its alloy, it is then cooled as slowly as possible until it reaches a temperature of about 100°F below its critical temp. This is usually done in some kind of insulating environment such as vermiculite.
Normailzing follows the very same procedure as annealing right up until the time comes to cool the piece. When this happens, instead of placing the piece in an insulating environment, the steel is left to cool in open air. The faster cooling rate does not allow the formation of cementite in quantities that annealing does, but it is slow enough for the formation of some pearlite, which is a combination of ferrite and cementite.
It is the rate of cooling that dictates subsequent phase changes from the the transformation range, and this is the first of the two major differences between normalizing and annealing.
Step 2: The Second Difference
Above: Microscopic view of Austinite (top) and Cementite (bottom)
Cooling very slowly from the transformation range (annealing) gives the carbon a chance to dissolve out of the austenite and form cementite. This maximizes the softness and ductility of a steel. There are instances however when stress relief is desired, but softness is not.
The normalizing process (a faster cooling rate from the transformation range) does not necessarily have to result in a softer steel. It depends greatly on the preexisting state of the steel and the desired outcome. Normalizing a piece of hardened carbon steel will soften it, but the same process applied to another piece of carbon steel that happened to be annealed might result in a harder finished state.
This makes knowledge of the state of your material very important when beginning a project. Is it new or is it used? Has it been work hardened? Has it been heated to excess and lost its temper? If the answers to these questions are known, then we can decide what method of heat treating is necessary to move forward with the project. If this information is not known, then the material must be brought to a known state, and the decision defaults to whether to anneal or normalize. Both will produce a given state, but each has different applications.
This leads us to the second major difference between the two processes, which is intent.
Step 3: Intent
Heat treating is all about changing the molecular structure of a steel in order to improve its working properties. While annealing is associated mostly with the softening of metals, normalizing is used by and large to refine and homogenize the grain structure of steel and create uniformity. Both are in service to stress relief.
So, what is the project? A knife made from an old file? Reforging an old chisel into a new shape? Making a hammer from an old truck axl? Repairing a bent prybar? New steel or used? The variety of material options for projects like these is vast and each of these might require a different form of heat treating and at different temperatures.
With so many design variables, it should be obvious that being equipped with as much knowledge as possible about your materials, and what is required to make them usable, is very important before starting any project.
This kind of information will inform the intent of the project and what heat treating process will be the most successful for it.
Step 4: The Process
Above: (Top) Steel Temperature Color Chart (Bottom) Iron / Carbon Phase Diagram
Like all facets of heat treating carbon steels, maximizing the success of normalizing depends on a prior knowledge of the material data. What is the steel's specific critical temperature? If this information is not known, then an educated guess can be made based on the iron / carbon phase diagram above. There, it states that the low end of the transformation range of carbon steels is 1333°F. The color chart also states that steel glows somewhere between dull red and cherry red at 1300°F. So, getting the steel up to a temperature that makes it glow bright red or into the orange range, tells us that we are in the austenetic range.
Normalizing:
- Heat the steel slowly and uniformly,
- Hold the steel at its transformation range for a suitable time. (Roughly 1 hour / 1" of thickness),
- Cool in open air to room temperature.
If there is one term that stands out more than any other in relation to normalizing, it is "uniformity". This is the key to normalizing in all facets of the process.
Heating evenly ensures that the forming austenite will be homogeneous throughout the piece. This may mean moving the part around in the forge or flipping / rotating it throughout the heating process. Soaking at the proper temperature allows the grain structure to grow evenly throughout in its form.
Uniform cooling requires total flow of air on all sides of the steel. An obstruction can restrict or accelerate cooling on that side which will alter the desired uniformity of the grain structure.
Some helpful tricks for cooling uniformly include: building a quick wire frame that suspends the piece in air, propping the metal on something heat resistant like a fire brick, or, if the piece has any holes , hanging the piece on a wire.
Step 5: What Does All of This Mean for the Home Metalsmith?
Above: Differences in crystal structure of a forged part
If you are like me, then budget is always a factor when beginning any project. Found and used materials have been an important resource for me and countless other smiths and fabricators. As mentioned before, using these materials brings an added risk that can potentially destroy a project or cause injury.
For this reason, knowing as much as possible about the material is recommended, particularly when salvaging parts that have received cyclical loads in their past lives. These types of parts tend to have stress built up in particular locations within their grain structure. Also, parts that have been formed using heat and force in the manufacturing process, or have dramatically different cross sections can have wildly varied internal crystalline structures, which can be problematic.
For example, some truck axles receive a forging operation to make the flange on one end of the part. The heat and force needed to achieve this creates a fine grain pattern in that part of the steel (Seen in the drawing above). The other end of the axle, while heated to similar temperatures, receives no forging and hence has a course grain structure.
Why does this matter? Because dissimilar grain patterns can introduce the opportunity for stress to exist along the grain boundaries. This can cause trouble for subsequent steps in the manufacturing process such as difficulties for machining and welding. It can also be a dangerous situation for parts that get put under load, such as axles, as this is the point where the part is likely to fail.
So, in conclusion, normalizing refines grain structure. It evens out and homogenizes the grain pattern throughout the part. It relieves stress build up in work hardened parts, and improves the mechanical properties of the material. It can do all of this without maximizing the softness of the steel, making it a very useful process for preparing used materials for new projects.
Stay Tuned for the next heat treating Instructable which will be focused on Hardening.
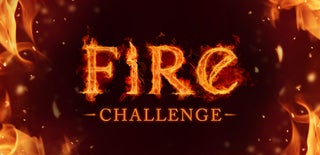
Participated in the
Fire Challenge 2017