Introduction: O2 Sensor Replacement- Goodbye Check Engine Light
I bought a 98 Ford ranger XLT several months ago and have been working through it fixing issues whenever time permits. Today I decided to the tackle pesky check engine light that has been on since I purchased the vehicle. This instructables will contain information on how to read error codes via OBD port and remove and replace an upstream O2 sensor. This process is fairly straight forward and is easily achieved in an afternoon. Let's begin.
Step 1: Reading the Code
First things first, you need to find out why the check engine light is on. Lucky for you your car is trying to tell you what is wrong with it, all you need to do is listen to it. Whenever the check engine light comes on that means there is an error code waiting to be read, think of it as an inbox notification. If you have an Advanced Auto Parts nearby they will read the code for you for free. I purchased a bluetooth reader for android by BAFX Products(link) for $24 since I fully expect there will be more problems down the road (there are 198,000 miles on my truck).
Connect the OBDII reader to your OBDII port and turn the ignition on (you don't have to fully start the car). Since I purchased a bluetooth reader I had to connect via bluetooth and download the free version of Torque. This app works well and can even provide real time feedback while your engine is running. Your reader should return an error code, typically this is just a number.This is where google can become your best friend, search your vehicle model followed by your error code ("98 ranger P0133"). I found pages and pages of information on my particular error code (P0133). You should be able to easily find what the error code means as well as a list of potential sources of the problem.
The code I was getting meant: Oxygen Sensor Circuit Slow Response (Bank 1, Sensor 1). After a quick google search I found that this could be any number of things including bad sensors, exhaust system leak, intake system leak, and the list goes on. Upon further research I concluded that the most probably issue was a bad O2 sensor. This was also the easiest of the possible causes and thus a good starting point.
I hopped on over to Advance Auto and picked up an upstream O2 sensor. You don't have to know exactly what you need, they will be able to look everything up for you. In my experience they have been much more knowledgeable and friendly than some of the other auto parts stores in the area. Just bring in the info you know: 1998 Ford Ranger (be prepared to tell them the engine size), and which O2 sensor (the error code told us this "bank 1, sensor 1"). In my truck there are three different O2 sensors: two upstream (bank 1 and bank 2), and one down stream. Upstream simply means before the catalytic converter and down stream means after.
Step 2: Remove the Old Sensor
Locating your O2 sensors is fairly straight forward. All sensors will be on your exhaust either before or after the catalytic converter. My sensor was bank 1 (so upstream of the catalytic) and sensor 1 ( on the exhaust side of cylinder 1). On my vehicle this was the passenger side, it may vary on your vehicle so be sure to do a little research to make sure you are replacing the correct one.
I drove my truck up on ramps so that I could get under it a little easier. Before starting any work disconnect your battery. Once I located my O2 sensor I quickly discovered that I needed a bigger wrench. Until this point I haven't had a need for any larger wrenches or sockets so my collection only goes up to 18mm. I ended up using an adjustable wrench , but the bulky end made maneuvering difficult. I recommend purchasing or borrowing a wrench to fit your O2 sensor just to make removal go a little easier.
Make sure you disconnect to O2 sensor from the wiring harness before you start removing it. This will ensure that no unnecessary strain is put on the wires while you are turning the sensor as well as make your job easier. The connector on my truck was buried between the engine and the fire wall. I had to access this from the top of the engine, sticking my arm in blindly and feeling around. There may be an easier way on your vehicle, but regardless there will be a connector somewhere close to the sensor.
Your exhaust is constantly heating up and cooling down and more than likely there has been some corrosion between your exhaust and O2 sensor. Hopefully the factory (or the last mechanic) put anti-seize compound on the threads so that you will be able to loosen the sensor. It will be tight, but I promise with enough torque it will come off, you may need to use a cheater bar (a pipe fit around the handle of your wrench for more leverage). Once you have your old sensor out head inside to your soldering station.
Step 3: Removing the Old Connector
My O2 sensor came with a generic water proof splice. This thing is not the most helpful considering where the other half of my connector is hidden behind the engine. I opted to save the old connector and put it onto the new sensor. This may have been a little more work upfront, but I didn't have to cut the stock connector off of my truck and it makes changing the sensor in the future easier.
Take note of where each color wire is in the connector so that you can reassemble in the correct orientation later. I drew a little diagram to help me remember (the white wires are interchangeable). Start by breaking the white piece off the back of your connector. This piece has been glued on, but should snap off with a few good whacks. I used the edge of a piece of wood and hit the white piece against the corner. Then gently pry the rubber grommet out of the housing, this will just be pressed into place. Using a small screw driver push the red pin lock out from the back of the connector (see note in picture). Now using a small screw driver gently pull back the tabs holding in the pins while pulling on the wires. The pins should pull right out.
Using small pliers or a small screw driver pry open the crimped prongs holding in the wire. Since the end of the wire was crimped tightly in place by machine it is very difficult to get the wire completely out. I ended up working the wire loose by bending the wire back and forth until the end broke off. This leaves the end of the pin free to crimp and solder in the new wires.
Step 4: Reassembling the Connector
Now that you have the connector completely dissembled compare the wire and sleeve length to that of the old sensor. Cut the sleeve and the wires on the new sensor to match that of the old. It is important to mention that you should leave the protective cover on the end of the sensor until just before you install it.
Now we need to reassemble the connector in reverse order. Be sure to follow these steps closely as order is important here. If you leave a piece out you will have to backtrack before continuing. Slide the new sleeve onto the wires. Line up the wires according to the diagram you drew making sure they will be going back into the connector in the same orientation as the old ones. Slide one the white cap piece followed by the rubber grommet. Strip the ends of the wires and add a little flux to each lead. Crimp the connector back onto the wire and solder in place. It is important to get a good solder joint so that the wire does not work itself free over time. Be careful not to apply too much solder as this will pool up and make reassembly of the connector impossible.
Once all four pins are securely soldered into place push them into the connector housing. Be sure that all pins ended up in the correct orientation. Now put the red pin lock back into the center of the connector and push into place. Finally apply some super glue around the white cap and glue back into place. You should now have an O2 sensor that looks just like the OEM one you removed.
Step 5: Finishing Up
Reinstall the sensor the same way you removed it. My sensor already had anti-seize compound on the threads, if your doesn't be sure to apply some. It is very inexpensive (<$2) and will make your life easier in the future. The recommended torque for the Ranger is 35 lbs. I don't own a torque wrench and just snugged everything up by hand. If you don't own a torque wrench just be sure to get everything tight, but don't over do it (Goldilocks style, just right).
Once your sensor is reinstalled and plugged back in reconnect your battery. With any luck your check engine light will be off. Take it for 15-30 minute test drive to see how it runs. Try to go on both highway and city type roads and see if any error codes pop back up. Luckily this seems to have fixed my problem. If your check engine light comes back on then work your way down the list of potential causes.
If this simple fix doesn't completely solve the issue and you don't feel comfortable doing the rest of the work yourself, take it to a mechanic. Don't be entirely discouraged tho, the mechanic would have replaced the O2 sensor first as well and charged you $75-$150 to do it. So either way you just saved yourself some money. Happy tinkering!
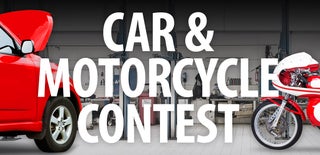
Participated in the
Car and Motorcycle Contest
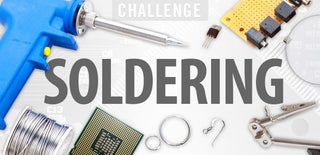
Participated in the
Soldering Challenge