Introduction: OPA Based Alice Microphones: a Cardioid and a Figure 8
For those who follow my instructables, I love microphones, and building them. It is kind of an addiction. I am a big fan of the TSB2555B capsule. It is the one used in my original “modify a cheap microphone” instructable. I have used many of these in builds for my musician friends and a few of them are in use in several studios. The DIY community buys several hundred a year and there are thousands of these capsules sold annually for commercial microphones. They are electret capsules meaning they are self biased. To turn one into a usable microphone requires a very high impedance circuit to extract the audio signal. That is the focus of this instructable - a simple but top notch impedance converter using a dual OPA or Operational Amplifier. Along the way we will build two studio grade microphones. A standard Cardioid response mic, great for vocals and many other uses, and a Figure Eight microphone that solves a few recording problems with sound isolation. With the help of the online microphone building community, it is even easier to do now than when I wrote my original Instructable. A huge shout out to two of the members: Homero Leal and Tom Benedict. Homero took the schematic I came up with and turned it into a PCB that is orderable online. Tom crafted multiple microphone saddles that are 3D printable and also orderable online. We will see their work in other upcoming mic building instructables as well. If you are into microphone building, please join us and the group.
On to the electronics! There are two functions it needs to accomplish. First, as mentioned, it is an impedance converter. Second, the electronics need to provide a balanced signal to the mic preamp. Condenser microphones have been around a long time. As in over a hundred years. They were Invented in 1916. Originally the high impedance converter was a vacuum tube. There are still microphones that use these and many people revere them. This may be blasphemy to some, but I am not a fan of tube circuits for multiple reasons. Complexity being the biggest reason. They need high voltages, output transformers, supporting components etc. And their noise floor while good, can be improved upon. Not to mention reliably sourcing tubes. Then in the 1940’s the Field Effect Transistor or FET was invented. But no one could build one until the late 1950’s and not commercially until the 1960’s. In 1965 Schoeps launched the first FET input condenser microphone and to quote from their website: “Now that field-effect transistors of the necessary quality were available for use in microphones at the highest quality level, this series represented a transition in solid-state microphones from RF circuit technology to the superior linearity of audio frequency technology.”
The Schoeps design and variants of it are used by almost every microphone manufacturer today. Which brings me to the current situation. When I published my first Microphone Instructable I used a J305 FET. (40+ years old) Then I had to replace it with a PF5102. These are also going obsolete. There are others that are suitable with low noise and low gate capacitance. Don't get me wrong, you can still find good FET’s, and there are companies that specialize in making small batches of components when the original vendor stops manufacturing. But it is becoming harder and harder to find them reliably.
I wanted a simpler solution that would be available longer term. I wanted an operational amplifier, OPA or “op amp” solution. I am a huge fan of operational amplifiers. Over the years I have designed many useful analog audio circuits using op amps as the building block. They really are great. With that said, I am a fan of Digital Audio Workstations and all they can do. Today you can easily replicate a wall of analog processing with zero added noise. My philosophy is this:
- Keep it clean, quiet, low distortion
- Get it into an A/D converter as fast as possible
- Keep it simple
So, back to the op amp… Doing a little research showed that at least one commercial microphone company uses them (CAD) and several online articles showed them in use as well. My challenge was to implement a simple circuit while powering it from phantom power. My CAD E-350, which is a great microphone, has two rechargeable 9V batteries internally. The academic paper I found used an external power supply. We are not doing that. That violates the “Simple” part. I want this to be powered from phantom power, available from the preamp or recorder.
Like everything in life, there are compromises. The really good audio op amps that I’ve used previously, draw a decent amount of quiescent current. Typically on the order of 10ma or so, which is a no go for phantom powering. We also need a real high input impedance. The NE5532, the go to audio workhorse, has a pretty low input resistance of about 300KΩ. which is fine for most uses, but not as an impedance converter. My go to for a really high input impedance was the OPA134 and OPA2134. They are FET input and they will supply +-35ma of current. Their downside is that they draw 4-5ma per channel just idling. These were used in the main paper I found online.
I built a few using a 9 volt battery and those worked well. But I wanted to use phantom power. Phantom power supplies 48VDC to pin 2 and 3 of the XLR via two 6.81K resistors. In theory that gives us a maximum current of 14ma if we completely short the pin to ground. Most preamps “allow” 10ma total. Drawing 5ma from each leg would mean about 35V would be dropped across the internal resistors and we are left with about 14V available. A single OPA134 has a quiescent current of 4ma. Hmmm, this might work. I took the circuitry that generates the 12VDC from the Alice/Schoeps circuit and added a resistor divider and a capacitor to create a virtual ground. Op Amps run on split power supplies, so this lets us bias the op amp correctly by “faking it”. I built a prototype using a single OPA134 and it worked. This let me drive one pin of the XLR connection and impedance balance the other pin. This works but isn't optimal. It also gives less total signal to the microphone preamp, actually, cutting it in half. My goal was to send a fully differential signal down the mic cable. Then I found the OPA1642. It has great noise specs and best of all, only uses 1.8ma quiescent current per channel. Meaning a dual one would use what my single OPA134 was using. Now my only problem was that it is surface mount. Yes, I’m really old school here. I know. The challenge isn't soldering one 8 pin surface mount device. For me, it is prototyping with it. So I shared the circuit with a colleague from the Mic Builders forum. He laid out a board and I sent the files to PCBway. Other than the OPA, all the rest of the components are “through hole”. I have used this circuit now in several TSB2555B builds, like the original Instructable, which is the first mic we are building today. I have also used it with a full external bias condenser, and a figure 8 build, which we are also building today. I am super happy with it and feel I have found a path forward without using harder and harder to find FETs and through hole transistors. Additionally, by substituting a 1MegΩ resistor in place of the 1GigΩ resistor, this will make an excellent high Z piezo pickup interface. One that is phantom powered. We will be following up on that one!
And thanks again to our mic building compatriots, everything you need to build this with can be ordered online. All you need are soldering skills and a screwdriver.
Attachments
Supplies
PCB
OPA-Alice PCB https://www.pcbway.com/project/shareproject/Dual_...
Electronic Components are in the BOM and all available from Mouser and other suppliers.
UPDATE: A complete PCB assembled using surface mount components is available from JLI ELectronics here:https://www.jlielectronics.com/diy-accessories/opa-alice-single-channel/
Non Electronics:
Fig 8 Saddle https://www.shapeways.com/product/UZS4SESZ6/tsb-1...
TSB2555B Saddle https://www.shapeways.com/product/7Q5MC658X/tsb-2...
Grommets for the saddle https://www.amazon.com/gp/product/B0015GZ864/
M2.5 Screw assortment https://www.amazon.com/cSeao-Phillips-Machine-Ass...
TSB-2555B https://www.jlielectronics.com/microphone-capsule...
TSB-165 https://www.jlielectronics.com/microphone-capsule...
Step 1: Lets Build It!
Here is a video of the complete build, time stamped for each section. We start with the circuit description and then the board assembly. Followed by disassembling of our donor bodies, a BM-800 and BM-700 so you can see the similarities and the differences, which is literally just the headbasket. Then we assemble the first microphone followed by a discussion of why you might want a figure eight mic and conclude with building that one.
Step 2: Circuit Details
Let's start at the XLR connector. The two 22nF capacitors are for RF/EMI suppression and are mounted on the XLR. They need to be mounted at the XLR for a couple reasons. At RF frequencies our entire microphone cable acts as an antenna, over the past 20 years cell phones and Wifi have become ubiquitous. They both transmit in the gigahertz range meaning the wavelengths involved are very short. All of this needs to be caught and filtered right as it enters the microphone. Pin-1 of the XLR connects to the chassis ground at this point. This is also critical for quietness. See the tech resource list at the end of the instructable for a great article on this by Bill Whitlock of Jensen Transformers on grounding. Next are the two 47ohm resistors. They isolate the rest of the circuitry and provide needed stability for the op amps. Going to the “Power Supply'' section, the two 2.2KΩ resistors and the 47uF capacitor take the incoming phantom power and supply a stable voltage to the Zener diode section. The small .1uF capacitor adds high frequency filtering for any residual noise or other high frequency artifacts that might not be filtered by the 47uF. This may sound counterintuitive as the .1uF is a lot smaller than the 47uF. The 47uF capacitor is electrolytic, meaning it is made of a long piece of aluminum foil that has a coating on it to form a dielectric insulating layer. Then it is all rolled up to fit in the little round can. That actually adds internal inductance that won't show up at low frequencies but at high frequencies it can. In essence the .1uF capacitor, which isn't a “coil of foil”, bypasses the bigger one. The zener diode does what a zener diode does. When it is reverse biased, at a certain voltage (in our case 12VDC) it will break down and conduct. This gives us a constant 12V DC. However zener diodes produce noise when they do this. Not a lot but enough that we need to fix it. That is where the 200Ω resistor and the second 47uF capacitor come in. They form an RC filter and reduce the zener noise to insignificance. There is some debate on this. Zener diode noise varies for zener diodes that work above and below about 5 volts. If you want to know more, read this. As an experiment, my friend laid the board out so you can use either one 12V zener, which I am or, two 5.2V zeners in series. In either case the RC filter of the 200Ω and 47uF capacitor gets rid of it. I could not get a measurable difference once the RC filter is used. The next part of the circuit is the two 47KΩ resistors and 47uF capacitor that form a voltage divider. It provides us a “virtual ground”. Op Amps normally run from split rail supplies. One supplying a positive voltage and one negative. To get around this we create a reference voltage that is in the middle of our 12 volts. This gets tied to the 1GigΩ resistor providing a DC bias on the “+” input on our first Op Amp stage. The first one is a classic non inverting buffer. The signal from the condenser capsule is developed across the 1GigΩ resistor and connected to the “+” pin of our first opamp. The output follows this exactly and is coupled to both the “-” pin giving us 100% feedback and zero gain. The cool part is that op amp can drive a decent amount of current, so we get current gain, not voltage gain. The second op amp stage is a unity gain inverting buffer. The two 2.2KΩ resistors set the gain a of -1. Now we have the same signal as the first op Amp but 180° out of phase. Exactly what we need to send out of our microphone to the preamp. Both of those signals are riding on our DC bias from the virtual ground so we couple them with two more 47uF capacitors. Note the polarity here. The XLR connector is still a higher voltage so we have the “+” terminal facing that way. You may have noticed here that I am using a lot of 47uF capacitors here. Not all of them need to be this value. A couple could be lower value and still work, However, it makes it a lot easier to order parts if they are all the same. I am very happy with the results from this circuit and plan on using it for my microphone builds moving forward.
Step 3: The Printed Circuit Board
My colleague who designed the board agreed to share it by putting it on PCBWay as a shared design. It can be ordered directly from them pretty inexpensively. When I bought my first batch, I ordered 20 as the shipping cost from China was almost as much as the boards. The size and layout of the boards with their mounting holes is such that they will fit perfectly into most donor microphone bodies including the BM-800 and BM-700.
Here is the Circuit diagram from the CAD program so you can match up the components to their locations on the board. With the exception of the IC chip everything is through hole and labeled. I found soldering the IC not too bad. I use water soluble flux based solder, Kester 24-6337-6417. This makes clean up much easier. Pay attention to where Pin 1 is and then hold it in place while “tacking” one of the pins with solder. Then switch to the other side and carefully solder all the pins. Solder bridges can happen. If they do, use the soldering iron tip to pull them away. You can see me do this in the video. The polarized components are the 47uF capacitors and the Zener Diode. There is a line on the Zener designating the cathode lead. On the capacitors, the longer lead is positive while the body is marked for the negative lead. We are bending one lead of the resistor over and mounting them upright on the PCB. You can either solder the 1GigΩ resistor now if you know you are using the board in a microphone or wait, If you substitute a 1MegΩ resistor for this, the circuit makes an extremely quiet high Z piezo pickup interface. And, one that is phantom powered, totally simplifying things.
After assembly, inspect the board for soldering and component placement. We are now going to thoroughly clean the board with focus on the op amp area and the input section. This is critical for proper operation in a high impedance circuit. Use a small acid brush or toothbrush and dish soap. Scrub it until there are no bubbles and residue. Then rinse off with a final rinse of distilled water, which you can get at your grocery store. Turn your oven on to 200F. Once it warms up, put the board(s) in and turn the oven off. Let it sit for 20-30 min to thoroughly dry. It turns out many PCB manufacturers do this exact thing to clean their boards post soldering. This is covered in the video as well.
Attachments
Step 4: Disassembly of the Donor Body
First thing you will need is a BM-800 or BM-700 body. The best thing to do is search using those terms in Amazon or Ebay. You should find them in the $20 dollar range. Once you get it, let's take it apart! The bottom unscrews letting you separate the parts. Cut the wires on the circuit board and then remove it, Save all the screws as we will reuse them. or, which I highly recommend, order an assortment of M2.5 screws. Once the PCB is removed take out the XLR connector. We will reuse this. You need to screw the retaining screw inward to move it into the XLR body. This will slide out once loose. Now take off the headbasket. This again, uses two more m2.5 screws. Note the capsule that came with the mic. I have seen everything from a 16mm capsule similar to the TSB165 to a tiny one held into a larger housing. These mics are a case study in poor quality control and sourcing. With that said, I have never had an issue with the metal components, it's always variants of the PCB, the capsule, screws not tight etc.
Step 5: Assembly of the Cardioid Mic.
This is the one that will match the previous Instructable as we are using a TSB2555B capsule. We do have a couple upgrades. First there is a Saddle available on shapeways that Tom designed. And we are going to use little rubber grommets to do some handling noise and resonance damping. The saddle is designed to have little servo grommets inserted in the slots on the side that will clamp in place when the mounting screws are inserted. We need to glue the capsule to the saddle. E6000 works great and is my goto for this.
There is some final prep we need to do. For the XLR connector, we need to remove the old wires. Then we need to solder two 22nF capacitors across pins 2 to ground, and pin 3 to ground. See the video for details. Last step is to solder new connection wires to the connector. I color code mine so as to not lose track of them. Make these about 2 inches long and strip and tin the ends. If you have not soldered in the 1GigΩ resistor (R-11) yet, do that now. Using some 24 or 26 gauge wire, attach 4-5 inch leads to the signal and ground pin at the op amp end of the PCB. Do a final and careful cleaning of the board in that area.
Now solder the XLR leads to the PCB at the input connections for XLR Pin 1, 2, and 3. Make sure they are good, then mount the PCB to the frame using two of the M2.5 screws you saved from the disassembly. Or, preferably new ones that are panhead.
Now it is time to mount the capsule and saddle. Note that the capsule faces the tab on the top of the frame. find it is easier to slide the wires through the hole in the saddle as you are mounting it. So do that now. Using either 2 or 4 screws (depending if the frame is tapped for four holes or two…) snuggly hold the saddle down to the frame.
Inspect everything and if it looks good, put the basket over the capsule and secure it with yet two more m2.5 screws. This provides a faraday cage for the capsule and if you don’t have that, there will be an amazing amount of 50/60 hz hum, buzz and noise. Once the saddle is on, screw the body parts back together and viola! One really great microphone is now in your hands.
Step 6: The Figure 8 Alice Microphone
What is a figure 8 microphone?
A figure eight microphone is a specialized microphone that “Hears” what is in front of it and behind it but not on the sides. Most microphones are omnidirectional, which pick up sound in all directions or cardioid, which favor sounds in front of them. A figure eight mic equally picks up sounds in front and back but not on the sides. Obviously there is a range extending out like a bubble. And conversely sound from the side isn't absolutely silent. But they are pretty good at minimizing side sounds.
Why would you need one?
Interestingly, the reason you need one is more for the isolation of side sounds vs the pickup in front and rear. They are used in studios in recording situations where multiple musicians are playing simultaneously or a solo artist is playing guitar and singing. I’ve used them and in particular this one, to help isolate a very quiet guitar from a female vocalist while we were recording. There is a video of that recording at the end of the instructable. They have been used with great results while recording orchestras and ensembles where you can’t get as close to the performers as you would like. They reject the side sounds i.e room reflections and audience (not the people behind and in front of the mics).
What can you do with a pair of them?
Two is always better than one. And a pair of figure 8 mics is better than just one. Having two allows you to do some interesting stereo recordings. Because they minimize the side sounds they can allow for clearer stereo imaging on things like acoustic guitar and other instruments. These are mics where mic placement really matters. The best thing to do is to wear closed headphones while adjusting mic position so you can hear how changing it is affecting the output. You can also mount them at 90 degrees to each other and create a Blumlien array.
Background:
There are a few “naturally occurring” figure eight microphones. Ribbon mics are inherently figure 8 by virtue of how they work. There is one “ribbon” that moves to changes in sound. Sound from the front or back moves the ribbon where sound coming from the side of it doesn’t. Really good ribbon mics are both expensive and delicate. Then there are some high end condensers with dual capsules. These allow you to switch the response patterns between omni, cardioid and figure 8. Those tend to be expensive as well. We are going to use two separate capsules, face one front, one back, and then wire them in series, out of phase. I did this exact thing in my “Build an MS microphone” instructable. This uses the same concept but with a few changes, making it easier to build and simplifying the electronics. We are going to use the same capsule, the TSB165. This one is quite revered in the DIY community as a small diaphragm condenser.
The wiring:
I mentioned that we were wiring these in series, phase reversed. We need to do this because the capsules are facing opposite directions, thus already 180 out of phase. If we just wired them in series, we would in essence have an omnidirectional microphone. This is what dual diaphragm condensers do when switched to Omni. I know this because this is how I first wired them when building my MS Alice microphone! Interestingly, there is another effect occurring, the capsules have somewhere between 12pF and 18pF capacitance. This is cut in half as two capacitors wired in series have ½ the capacitance. Also the signal output increases by a few dB. That is less noticeable as the capsules are in opposite directions. I have seen some nature recordists who close mount four capsules facing one direction and wire them in series to improve S/N ratio. Hmmm, might have to try that in another project…
Step 7: Use, Summary and Taking It to the Next Level
I am very happy with the results using an op amp. Theoretically the circuit is a few db noisier than the best FET/Transistor equivalent. With that said the Op amp we are using contributes about the same amount of noise as a 2.2KΩ resistor. Real world usage is not an issue here. As I was working on my write up here, the Mic Builders forum had several posts for people trying to find replacements for FET’s that were called out in previous builds. And we had a decent dialogue about this project as I was developing it. I have put these through real world usage in multiple builds. And the fact that substituting one resistor lets the circuit become a Piezo pickup interface is very cool. I put four of the boards into a small enclosure and I am thrilled with the results. That will be the focus of another Instructable as will a full external bias condenser project. In closing I want to thank Homero Leal for the board layout and Tom Benedict for the Capsule mounting solutions. I am truly grateful. And with that I leave you with Kady Speaks, who I recorded outdoors with two figure eights on guitar and this circuit in my full condenser build. Interestingly, I have had this build idea for a while. I recorded Kady last summer and with her vocal range and dynamics, voice really bled through the guitar part when she got loud. That spurred me on to build these and get back outside with her to record again. I’m pretty happy with my results.
Step 8: Troubleshooting
I added this guide March 2022. As of now there are over 150 builds using this circuit. Thid guide is based on helping people and, some of the things I did wrong multiple times :-)
Enjoy! Oh, these mics are really good!
Attachments
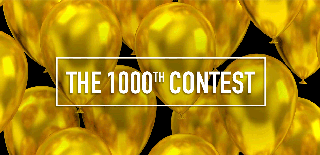
Runner Up in the
1000th Contest