Introduction: Reclaimed School Bleachers to Wood Floors
Back in 2012, I was able to get my hands on 40-some wood planks that made up the seats of some really old school bleachers. It was a great find, and I was luckily at the right place at the right time, because they were literally an hour or two away from just tossing everything. So with help from a few friends, we all got to work and removed the planks from the metal framing, loaded the wood up into a long passenger van, and stored them in my garage.
Fast forward to the New Year of 2016, and my wife and I got the great news that she was pregnant with our first kiddoe!
After a short discussion, we picked out which room would be our nursery, and then I got the great idea that not only should we install wood flooring, but I could use the reclaimed wood and custom make our own wood floors! I had most of the tools needed, and if I didn't, I simply borrowed them from friends, or sweet talked my lovely wife into letting me invest in what tools I needed.
I hope that by sharing this journey from scratch to finished product, I can maybe help you if you decide to do something like this.
Step 1: Please VOTE and Comment!
This was a HUGE project that I undertook, and I love that I get to show you what I learned through the project!
With that, if you like this Instructable, please vote for me! I plan on entering my Instructable to woodworking and home improvement related contests here on Instructables.com, and would really appreciate it if you vote for me!
On this page, and every step of this Instructable, to the right of the "title" that's in bold text, you may find a "Vote" option that you can use to help me out. Also, if you find this Instructable in the contest page of this website, please do me the honor and VOTE for it!
Step 2: About the Wood
Like I said in the intro, this wood flooring is completely made from reclaimed wood!
One of the best finds I have ever had, and I was super lucky to grab it. My wife may have not been too happy about me bringing 40 some planks home that one day back in 2012, but she definitely loves it now!
The one thing I would say about getting reclaimed wood is this...don't be shy to ask around, and don't let any opportunities pass you by! You can find usable wood from anywhere, whether it be online like Craigslist or special Facebook Groups, to just knowing people. I happened to be in the right place at the right time, and with a few minutes of introducing myself and having a friendly conversation, I was able to convince some people to let me have the wood if I did the hard work of removing it.
It was a win/win situation for both parties. They needed these old wooden bleachers gone, and we agreed that I could take the wood if I dismantled the bleachers and hauled it out. And as a small bonus, the metal framing that the wood was attached to was worth a decent penny at the metal recycling center. Pretty good stuff!
I knew I had a great find because the kind of wood used on bleachers would definitely be hardwood of some kind, and that's exactly what you would want in wood flooring. So after a few friends of mine dismantled the bleachers, I took the wood home, and my friend took the metal and made a pretty dime. NICE!
Storing the wood is pretty important!
In my situation, the only place I could store the long planks was in my external garage. They were, for the most part, kept out of the weather. They were exposed to the outside temperatures...so what the temperature was outside, the garage temperature was following. That's why it's also important to be mindful of the timing of the preparation of your project! It was incredibly important to move the planks indoors to a temperature and humidity closer to the nursery. When me and my father moved the boards indoors, I refrained from any cutting for two weeks. That let the boards even out in both temperature and moisture levels!
Step 3: Tools Needed
If you're going to make custom wood flooring from reclaimed wood, you're going to have an arsenal of tools at your disposal, either by borrowing them, renting them, or flat out owning them! There's a lot of cutting, planing, sanding, nailing, finishing...the list goes on and on and on!
Safety is of course #1. You'll need tools to cut, sure...but you're going to want to stay uninjured and ALIVE to get this project done.
- Save Your Ears! I'm a sound engineer by trade, so saving my ears is obviously important. Ear plugs, inserts, or over-the-ear muffs are vital. You're going to want something that is comfortable for you while keeping your ears 100% safe because you'll most likely be working for long periods of time.
- Keep your eyes protected! Face shields, goggles, and safety glasses are vital. You should never be working with equipment and risk getting a stray particle, or even worse, a whole chip planting itself in your eyes.
- Keep It Dust Free. One piece of safety machinery that I initially overlooked was a dust collection system. After the first hour of cutting wood, I quickly decided to remedy that! Fine particles will not only choke you up and make breathing uncomfortable, but being exposed to that dust for prolonged amounts of time will cause you to suffer later in life with injuries to your lungs. Either keep some clean air flowing in, with the dust flowing out, OR do what I did and get yourself a dust collection system with a filter good enough to filter out the fine particles. It's also handy during cleanup, especially because the time you would use during cleanup can now be used to work a bit longer!
- Sharp Blades. Keeping a sharp edge to your blades will actually be something you want to have. It's almost a no brainer. The sharper your saw blades, the cleaner the cuts, but also the less frustrated you will be. Your pace of cutting the wood will also be quicker too.
- Cleanliness. A clean work area is vital too. It may not look like my work area is optimal, but what I'm talking about is keeping the dust off the floor to reduce slipping. My interior garage floors are smooth as can be, and with a little bit of wood dust, it was slick at times. I kept my broom close by to quickly sweep away any buildup, and at the end of the day, sucked it up with my dust collector.
And honestly, something that most people don't think about when it comes to safety is this...your mood! Having a bad day at the job, getting grouchy because you skipped lunch, or maybe just frustrated and think working on something will help out? Well don't...period. Your bad mood and working closely with equipment that can cut off any part of your body just doesn't mix. You need to make sure you're in good spirits before you dedicate a few hours to this project! Keeping focus, being calm, and in a good mood is a very good idea when woodworking. Kum ba yah anyone?
In the way of tools, here's what I used:
- Table saw. Get something that is beefy and more powerful, ESPECIALLY if you are re-sawing the wood! More safety features, the better!!!
- Routing Table. You don't really need one, but cutting the joints into the planks of wood will be easier if you have a routing table.
- Miter Saw. Depending on the width of the boards you are planning to make, you might need a miter saw with a telescoping arm. My boards were only 4 & 1/4" wide, so my smaller one was just fine.
- Blade Sharpener. You gotta keep those blades sharp! I got a saw blade sharpener cheap from my local Harbor Freight store and never regretted it. I used it a lot, especially because of the re-saw cuts!
- Air Nail Gun & Air Compressor. Hands down, you shouldn't even touch this project if you don't have an air nail gun in hand...period. The nail gun doesn't come into play until after you're done with all the woodworking and the nursery sub-floors are prepped. Of course, it goes without saying, an air nail gun needs a compressor to work!
- Sanding Tools. Really the ONLY time I sanded my boards is when they were laid down in the nursery. I had to use a giant floor sander, which I rented from a local rental store.
- Miscellaneous Tools. Pry bars, hammers, flat-head screwdrivers, staple guns, and all kinds of miscellaneous tools!
Step 4: Measuring for Square Footage
You're going to have to know the square footage of your floors to get an understanding of how much wood flooring you're going to need! This much is obvious...
Getting the square footage of any room is simple. Measure the width and length of your flooring, and multiply your measurements to get your square footage. Our nursery is 10ft. wide, and 12ft. in length, for a total of 120 square feet! However, we also had a small amount of floor space in the closet, 2x2ft, so adding it to our original measurement, I found out I needed 124 square feet of coverage...and I like to play is safe with my measurements, so I planned for 130 square feet.
Step 5: Chopping for Manageable Lengths
When I brought these old bleacher wood planks home, I had to take several trips using my church's 12-passenger van. These things were LONG!
Using a friends extending miter saw, I was able to chop these 20ft. long boards down to two 6ft. and one 8ft. boards. This was a no-brainer. I HAD to cut these things down to manageable lengths. This took a LONG time...40-some boards cut down to length.
So now, with a total of 120 boards, next step is to rip them all down to the width of the floorboards I wanted!
Step 6: Squaring the Edge and Ripping Correctly
So to maximize the number of wood boards from each plank, I would take my 10" wide plank, run one edge through the table saw to square the edge. Then, after I squared the edge of ALL 120-some planks, I ripped 4 & 1/4" wide boards.
Why the extra 1/4" to the 4" widths?
Whatever width you want your floorboards to be, you still have to consider the tongue and groove joint at the edges of the finished floorboards. That's super important, and it takes some forward thinking from you!
After my boards were ripped to the right widths, I then approached a new problem that was showing up...
Step 7: Problem With Dust...
So I mentioned in the safety steps of this Instructable that dust is a serious issue when it comes to woodworking. It was at this point in my project that I realized I needed some SERIOUS dust management.
At this point, I was able to sweet talk my wife into getting me a planer for this project...but a dust collector too?
Actually, it was really easy to get her on board with buying a dust collector. She saw the huge amount of sawdust, not only what was collecting on the floor, but the amount just floating around in the interior garage and eventually landing on everything. It was a complete mess, but more seriously, dust is extremely flammable. In certain situations, when it's ignited it could easily be described as "explosive". Too much dust floating in the air can be combustible with a single spark!
Plus, as you can see in the video, it's helpful when you want to get the dust out of your long hair quickly!
So a run to Harbor Freight and for around $250, I was able to get a fairly decent dust collector that did the job very well! After a cleanup job in the shop and assembling the dust collector, our momentary pause in our project was over and we started the next step...
Step 8: Re-Sawing?
After ripping the wood, I got the bright idea, "Hey, I want to eventually put wood flooring in the other 2 bedrooms. It would be best if I would use wood from the same 'batch' for all three rooms!", and quickly figured out the square footage for everything. Doing some math and double checking, I decided that re-sawing was needed to have enough wood planks to do all three bedrooms, with plenty of wood left over for other woodworking projects.
I didn't take any photos of me making the re-saw cut, but our friends from Woodworkers Guild of America shows a great example. Workaround: Table Saw Resawing
With that, I decided to add the extra step of re-sawing my planks in half, so would be taking 1 &1/2" thick boards, and re-sawing them to two boards that are nearly 3/4" thick boards. This is plenty thick for wood flooring, real or synthetic.
WOW...did I bite off more than I could chew!...almost...
First off, the table saw is reportedly the #1 power tool that causes the most injuries. Using any power tool that spins, oscillates, or circulates a piece of metal with incredibly sharp teeth is dangerous enough, but most table saws, even the large ones, don't have room to do a re-saw with safety guards in place. So nervously, I had to remove all safety guards from my contractor table saw, and use just the fence to make the cut. THAT was nerve-wracking.
This is the point too that I made myself stick to the rule of refraining from using the saw if I was tired, hungry, frustrated, or too un-nerved. Being in anything less than in a good mood and in good condition would just add to the dangers of woodworking, but especially the re-saw cut on the table saw. If you can find even one reason why you shouldn't, DON'T!
And also, the re-saw cut produces a HUGE amount of dust and will require you to sharpen your blades constantly. During any other cut of wood, the blade is only in contact with the wood for a little at a time, but with that wood board on it's edge, the blade is touching and cutting several inches the whole time! You are removing a vast amount of material the whole time, so sharp blades and dust collection is very encouraged for this cut!
Step 9: Time to Use the Planer!
Planing wood was always my favorite step in woodworking class in high school. Taking the raw cut lumber that my teacher always came across, and feeding it through the shop's GIANT industrial planer was FUN!
One of the huge perks of making wood flooring from scratch yourself is that if you have to buy tools to do the job, it's still going to be cheaper than buying wood flooring from a box store and getting them installed...AND YOU STILL GET TO KEEP YOUR TOOLS! I was able to sweet talk my lovely wife into getting me a tabletop planer that was good enough to tackle my project easily. What a deal huh? Also, this was the moment where I realized that getting the dust collector was a GREAT choice, because wow...those planers sure do spit out wood shavings like crazy!
Fortunately, during the re-sawing phase of this project, I was incredibly careful to make the cut exactly in the middle, so for a large number of boards, there was zero planing needed. Only about 20-some boards came out thicker and needed some planing done.
And once again, I didn't get any photos of me and my friend doing some planing! Honestly though, with only a few boards needing planed, and the planer actually makes quick work, there was barely any time to take a picture. However, there is a photo of some boards sitting next to each other showing the before and after!
Just secure the planer to a workbench or a portable stand, attach your dust collector, and off you go!
Step 10: Using the Router Table
It's an extremely necessary step, in my opinion, to add a tongue and groove joint to every board to ensure that the whole floor locks together.
This was probably the most mind wracking part of this project in my opinion for a few reasons.
- You have to make a tongue joint on one long edge and one end of the board, then make a groove joint on the other two edges.
- For the remaining boards, you HAVE to make those identical joints for ALL of them. First, you will choose which face of the board you want to be the top of the floors, and then make sure you make the identical joints for all the boards. Don't get confused! I only wasted only 3 or 4 boards, but if I didn't pay enough attention as often as I did, I could have wasted a lot more.
- You have to make sure the fence doesn't shift over time, or let your router that's mounted under the table to drift lower throughout cutting all the boards. Routinely check with a metal ruler that your measurements haven't changed!
Also, remember in Step 6, "Squaring The Edge And Ripping Correctly", that I mentioned the extra 1/4" to the width of the boards? This is why - My tongue joints was exactly 1/4", where the grooves joints were also 1/4" deep. After a board was fitted into it's adjacent board, there was exactly 4" of board exposed. This is where planning is crucial! If I hadn't thought of this, I probably would have ripped only 4" wide boards, and overall had 3 & 3/4" wide floor boards. Not an extremely terrible thing, but in the end, a 4" board to a realtor or home inspector would appear more professionally done then something that looks accidentally wrong.
Step 11: Prepping the Nursery
The next step was to move the new floor boards into the nursery and let them rest for some time.
Why? Well just like I mentioned in Step 2: "About the Wood", you need to make sure that the new boards have adjusted to both the temp and humidity levels of their final resting place, the nursery (or whatever room you may be working on). Moving the boards into the room and letting them rest for at least a week (in my opinion) made absolutely sure that the majority of the expanding or contracting was done beforehand, and not AFTER I had nailed them down. This isn't too necessary for smaller rooms, but the larger the room, the more imperative it is that you let the boards relax to the room's average temp and humidity.
Before laying down the new wood floor boards, the next step was to strip the nursery room floor of EVERYTHING. That means carpet, floor padding, staples, etc.
Do yourself a huge favor and buy those massive contractor garbage bags that can fit large cans, and wear masks and safety goggles. We had some incredibly nasty, old carpet in the room that came with the house when we bought it, and let me tell you now, old carpet that's bad looking on the top is WAY nastier underneath! The padding under the carpet was super brittle and obviously old as heck with mystery stains and unexplainable blotches. All that carpeting and padding kicked up an absurd amount of dust, so don't breathe that in and make sure your room is well ventilated!
After the carpeting, I had to inspect the sub-floor. I was incredibly thankful that our sub-floor was in excellent condition! Using a long level edge, I checked to see if there was any drooping or rising in the floor. There was only one spot where I used a wood screw to push down one small rising part of the floor, but that was it.
I hope for your sake, that if you're doing a project like this, your sub-floors are as good as mine were. I have done some bathroom remodeling, where the sub-floor was wrecked, and this is the most loathing time of the whole remodeling. You MUST tear out the old stuff and put in new. If there are only SOME spots that are bad in the sub-flooring, you're going to have to weigh the pros and cons of either just repairing the one spot, or redoing the whole floor. In my opinion. if the sub-flooring is old in the first place, does it make sense to finish a project with old sub-flooring? Nope! If the sub-floor is bare already and you have easy access right now, just bite the bullet on this one and replace the whole sub-floor for an entirely NEW floor system that you can be both confident and proud in!
I chose to replace the base boards too in this project, so with a pry bar I got rid of it all. Then with an assembly of flathead screwdrivers, needle-nose pliers, channel locks, and ANYTHING I got my hands on, I then took out the various carpet staples and nails. The sub-floor needs to be bare of anything. Obviously, you have to remove any nail-strips that will hug the edges of the room too...those can be nasty, so handle with care!
Step 12: Vapor Barrier and New Floor Boards!
You just HAVE to protect these new wood floors, both from above and below! We have a semi-finished basement, so the plastic vapor barrier wasn't very necessary, but I opted to put it in anyway.
A vapor barrier can either be the official product, or in my opinion, just buy 6 MIL thick plastic sheeting from the box store. It's exactly the same thing, but $20-some less. With the cleaned sub-floors, the vapor barrier, and a staple gun, I laid down the vapor barrier, adding an inch or two excess around the edges. I also decided to use packaging tape to seal over the staples, to hopefully make the whole barrier completely vapor proof. If I didn't use the tape, I still think it would have been okay without it.
Now the fun part! Even my preggo wifey got in on the action!
Using a scrap 1/4" thick piece of wood, I perfectly allowed some space between the wall and the first row of boards to allow for expansion. A special note about this first row...it HAS to be perfect. Anything that isn't fitting square or straight will show and magnify in the next row, then the next, and so on and so on. Find your straightest, flattest boards, and use them as the first row.
With that said, you should try your best to make sure EVERY row of wood boards is nailed down as straight as possible, and you may have to be creative to wedge, pull, push, and clamp those boards tight against the previous row before you nail them down. I had to use a variety of techniques to do this from using long wood clamps, to even using screws in the sub-floor to push a board tight up against the other boards. I made a moderate effort to keep things straight, but in the end, I wanted character in the flooring too, so a minor gap here and there in it wasn't too concerning. In a later step, you'll see how I fixed those small gaps!
Using an air nail gun is practically imperative at this point. I would HATE to use a regular hammer here; it would prolong one of the more fun steps of this whole project and you would undoubtedly become frustrated quickly. I borrowed my father's air compressor and bought my own nail/brad gun. Don't go crazy with the thickness and length of the nails by the way; They only need to get through the thickness of your wood boards and the sub-floors. Just use some common sense with the length of the nails, but keep them as thin as you can to properly do the job.
Also, the power miter saw is needed for this step. You'll likely have to chop down a board to make the exact fit for the last board of every row, and having the saw in the same room makes things easier. Just remember, keep that dust out of the air as much as possible with plenty of ventilation! One more thing: keep in mind for expansion, and don't cut the board so that it's all the way to the wall. Keep at least 1/4" of a gap between all outside edges of the room and your floors will be a happy camper! This is especially important for larger rooms!
Step 13: Sanding, Sanding, & MORE Sanding!
This next step is where the large wood sander came into play. I opted out from using a belt sander here, as it can easily ruin your work with large gashes! Instead, I went to my local tool rental shop and got myself a floor sander with the grit paper they recommended. These guys will likely know what you need, so take their advice when they give it!
Before you begin sanding, there's a few things you need to do first:
- Dust. You know exactly what I'm going to say if you read this Instructable so far. You HAVE to plan on getting rid of airborne dust and bringing in fresh air, and you MUST ALWAYS wear dust masks. The better the mask, the better you'll be. Also, you'll need to seal off the room from the rest of the house so that the dust doesn't get anywhere else or in the ventilation. This means closing and sealing the door AND closing off any air duct vents and return air vents. I don't care how you do it, just seal off the rest of the house!
- Nail Heads. Make sure you don't have any nail heads protruding from the surface. My air nail gun would sometimes misfire and not shoot the nail head below the surface, so my first pass over the floor with the sander was partially unsuccessful due to a few nail heads tearing up the sand paper.
- Work quick! When I rented the sander, I had an unusually long weekend with Memorial Day on Monday, so I made a deal with the rental shop to have the sander on Friday, Saturday, Sunday, AND MONDAY for the same weekend price...sweet! But I needed ALL of that time with the sander to do the next few phases of my project. Plan ahead, or you'll pay the price!
Your sanding technique will need to be pretty good with the floor sander, but if you get an oscillating version of a floor sander, it's very forgivable if your technique isn't too good. Basically you'll want to move the sander only when it's actively turned on and vibrating, AND you'll want to work in loops and figure 8's with some overlapping on the next few rows of the wood floors. The sander will vibrate the heck out of you, so only use as firm as a grip as needed, so your fingers will take the beating, and not your shoulders and back. You'll feel this sander's punishment the next day! If you have gloves, use them, especially the ones that have extra padding on the palms and inside finger areas.
Sand the whole floor, then sweep and remove the dust from the whole area. Once the dust is collected, do another pass again, then collect the dust. Do both the sanding/dust collection as many times as you feel you need!
Once you have the entire floor nice and smooth to where you like it, next step is liquid wood putty, and MORE SANDING!
Step 14: Liquid Wood Puddy and MORE SANDING!
I REALLY wish I had more photos of this next step. Sorry, everyone!
Most likely, if you are making wood floors from scratch and reclaimed wood, you won't have perfectly fitting boards with zero tearout from your power tools. Also, in my case, the reclaimed planks I took from the bleachers had bolt holes drilled throughout them everywhere, but I truly didn't mind these flaws, nicks, and imperfectly assembled boards! To me, this added some lovely character to my final floors, and once I stained the whole floor, they were BEAUTIFUL with all those imperfect spots; However... You'll still want to fill in every hole, gash, and seam at least some!
If you use your regular kind of wood putty from the box stores, you'd be dedicating DAYS to just filling those gaps, but I don't have that kind of patience nor the time. I only had ONE DAY to apply the liquid wood putty, so I had to use something fast! Enter the liquid wood putty!
I ordered my stuff from online and it came a week before I needed to apply (planning is key!), and it came pre-mixed to what I needed in color and consistency. With a wide, plastic drywall trowel, I was able to cover the ENTIRE floor in about an hour.
In this video, they show the exact kind of technique I used to apply the liquid putty. (*Note: this isn't the putty that I used*) With the back and forth motion, I was able to cover the whole room in less than an hour, with minimal amounts of putty...I'm pretty sure I have enough for the other two rooms!
After applying the putty and letting it dry for a few hours, I was able to get the floor sander out and clean it all up! This left a completely level floor without any gashes, but left the visuals of an imperfect floor, full of character! Be extra careful here with the putty being sanded. This part kicked up a large volume of dust, more than ever before!
Step 15: Stain
After I was completely satisfied with the putty, I needed to move on to the stain. Again, I had to do this quick, and with several hours needed in between coats, I needed to be prepared, fast, and good at applying the stain.
My wife and I pre-picked the kind of stain we wanted, and we really liked the darker brown look to wood floors, so that's the shade we went with. We also went with a stain/polyurethane mix in hopes to save on time and effort, but more on that later and why I kinda regret that!
Everything you need to apply the stain and the final coats of polyurethane will most likely be in one aisle in the box store. You'll need the following:
- Get Enough! With stain and polyurethane, plan to do several coats! For us, a gallon was enough to do one complete coat every time. I planned on doing two coats of stain and one coat of polyurethane, so that was three gallons all together.
- Tools. Wool applicator with long handle. This was in a kit, so it helped with choosing what to go with. Don't use a regular brush! That wool/sheep fur brush is important to apply stain to a floor apparently.
- Paint Pans. We went with a metal pan with plastic liners that were designed to be thrown away. Just be careful with that kind of plastic liners. Especially with stain, if it's left for some time pooled in the liners, the liners could actually melt. Just be careful.
- Work Clothes. Do yourself a favor, and wear clothing that you don't mind ruining. I wore crappy shorts and shirts, and wore junk slippers to work in, and thank goodness I did! It's very easy to get stain on you, even if you are extremely careful. It just happens.
- Junk Rags And Paper Towels. Spare cloth rags or durable paper towels. The same reason that you need work clothes--stain gets everywhere, and having something to wipe up accidental stain quickly will do you well.
You BETTER HAVE SOME SERIOUS VENTILATION at this point!
Staining is no joke with the fumes that it expels, and plan on ventilating that room for SEVERAL WEEKS after you're finally done with the whole project. Fumes from staining and polyurethane will linger for a very long time, and even when you don't smell it, it's still there. For a newborn's room, it's highly recommended having the room ventilated for at least a month after you stop smelling it, so that's like 2 months completely aired out.
Finally, a note about stain: you should only stain a number of coats that visibly is good for your choice of darkness. I'm the kind of guy that goes by what the book says, so when I saw on the stain's instruction label that you should do 2 coats, I did exactly that and had an obviously darker shade. I was actually very happy with the shade with one coat, but I did what I was told and it made the floors DARK! However, I was still very happy with the stain with two coats, so no big deal. Just be aware and coat to the darkness that you like!
Step 16: Polyurethane
After the final coat of stain was dried enough to walk on without leaving marks, it was time for the polyurethane. With an abrasive pad on the floor sander (similar to the coarseness of steel wool), I lightly scuffed up the last coat of stain, just enough for the polyurethane to have something to grab on to. After using the vacuum to get all the dust up, I started to apply the polyurethane with the same tools used for the stain.
Now, here's where I messed up, and hopefully, you will avoid this mistake. Do yourself a favor and do AT LEAST two coats of polyurethane!
My mistake was this: The stain was a stain/polyurethane combo mix, and after doing two coats of the stain, I thought that by doing just one coat of polyurethane, it would have been enough. I mean sheesh, it's "practically three coats of polyurethane!" I reasoned with myself.
But dang, do I really wish I had done at least TWO coats of polyurethane - three preferably to be honest.
However, I'm not totally dismayed. Even though I lost that window of time to apply a second/third coat before the baby comes, I'm predicting that I'll be able to get around to laying wood floors in the 2nd bedroom in about two years. With the large area rug we have in the nursery now, the flooring in the nursery will take just a little beating, and when I'm ready in two years to stain and polyurethane the 2nd room floors, I can move the then 2-year old and my wife downstairs temporarily while I reapply more polyurethane to the nursery floor AND the 2nd room.
Not all is lost I guess!
Step 17: Extra: Showing Off the Finished Nursery
This isn't necessarily a step to the floors, but me showing off the rest of the finished nursery!
I'm so proud and excited with the final look of the nursery. My wife and I seemed to have tied the whole room together with the white trimming, ceiling, and furniture; with the medium gray walls, we can use things like the curtains, rugs, blankets, picture frames, etc to add color and make it gender neutral. That way, if we decide to have another kid, we may use this room for baby #2 for the nursery again, and move out our little girl to bedroom #2!
Step 18: Final Thoughts
This was a VERY long, tedious, and exhausting woodworking project for us to tackle, but I am completely happy with the end result! I'm curious and willing to bring in someone to professionally assess the changes to see if the value of our house went up and by how much.
A lot of people were shocked when I mentioned a long time ago that I was planning on doing this, and seemed that they were trying to discourage me from doing it. They were right--it was hard and a lot of work, but for me, it wasn't so bad as I've been woodworking for quite some time now. It really didn't bother me, and I tried to keep a good mood and level head throughout the whole project. I stood back often when I completed a "phase" and admired what I was doing and "patted myself on the back", and that helped keep my spirits up.
And it DEFINITELY helps to have extra hands to help out, not only because they are physically helping, but I noticed that I didn't "burn out" as fast because I had someone to have a break and converse with. When I was alone during some of the work, I noticed I would mentally get bored quicker, lose my concentration and drive to keep going, but with a buddy around, it helped A LOT!
If you have intermediate knowledge and experience with woodworking, I would definitely encourage you to think about making your own wood flooring! With hard work, patience, this Instructable, and using Google a lot, you too could tackle this size of a project yourself!
*************************
This was a HUGE project that I undertook and I love that I get to show you what I learned through the project!
With that, if you like this Instructable, please vote for me! I plan on entering my Instructable to woodworking and home improvement related contests here on Instructables.com, and would really appreciate it if you vote for me!
On this page, and every step of this Instructable, to the right of the "title" that's in bold text, you may find a "Vote" option that you can use to help me out. Also, if you find this Instructable in the contest page of this website, please do me the honor and VOTE for it! Thanks!
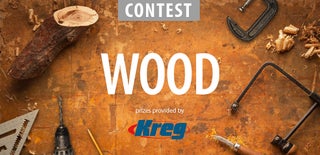
Participated in the
Wood Contest 2016