Introduction: Open Lights MADE FOR MY WHEELCHAIR
In the project MADE FOR MY WHEELCHAIR we develop open source wheelchair add-ons with wheelchair users (www.madeformywheelchair.de).
With this guide you can create two lights for wheelchairs. We call them I and O.
The components of I and O can be assembled without screws and adhesives. They can be attached to a wheelchair in different ways. But more about this later ...
Share us your feedback if you've made it in our public Facebook group MADE FOR MY WHEELCHAIR or here. We want to see your version of OPEN LIGHTS.
The project is run by Fab Lab Berlin, Makea Industries and be able. It's funded by the Federal Ministry of Education and Research, funding program Photonics Research Germany, contract number - 13N14244.
Step 1: Preparation - Materials, Tools & Technologies
1. Electronic soldering iron, Eg 30 watt, with soldering tip and soldering sponge
2. A small side cutter
3. Pointed pliers
4. Third hand with magnifying glass
5. Cable with three different colors for soldering
6. Solder
7. 3D printed housing (Filament PLA or ABS)
8. Acrylic cover (acrylic plate 3mm)
9. For I: Adafruit NeoPixel Stick RGB LED 8 x WS2812
10. For O: NeoPixel Ring RGB LED
11. For each lighting an Adafruit Trinket, 5V Logic
12. One push button T602 per lighting
13. A power bank (we recommend at least 2200 mAh per lighting, for several lighting systems a stronger power bank with multi-USB port makes sense)
14. One USB A to USB mini cable (Should have the distance from the location where you locate the power bank )
15. For attachment to the wheelchair you can choose cable ties, velcro fasteners, power strips or Sugru dough
16. FDM Desktop 3D printer with a heated platform.
17. Laser Cutter
Step 2: 3D Printing of the Housing
1. download: stl files for I and O
3D model of housing for manufacture with a 3D printer
2. Print the housing with a resolution of 0.1 mm without support structures or base plate for best results.
In any case, a heated platform is suitable for the component to not deform during the printing process.
We recommend using black to highlight the color of the acrylic cover.
Step 3: Lasercutting the Cover
1. download: svg file for I and O respectively
Vector to cut the cover with a laser cutter
2. Use the appropriate settings for cutting 3mm acrylic plates of your local laser cutter.
It’s useful to leave the cover film on the plate to keep the edges clean.
Step 4: Electronics - Prepare Cables
First you cut the cables.
In the picture the components are cut roughly the lengths needed for mounting. You can use this for orientation when cutting. For a better overview it would be great if you can use cables with distinctive colors.
With the side cutter the cables can be easily cut and you can also remove the insulation at both ends of the cable over a length of 3 mm.
Step 5: Electronics - Assembly the Push Button
First you have to straighten up the four little legs with a flat-nose plier.
Then the component can be pushed into the opening on the front side with a little pressure.
You have to bend the four legs outwards. Fits!
Step 6: Electronics: Solder the Cables
1. download: soldering plan for I and O
2. If soldering is a whole new territory for you, then take a look at this video and practice a bit.
3. When soldering, you have to stick exactly to the soldering plan. Note that this is only about the soldering positions for the individual cables. The cable lengths and the Position of the components are not shown correctly.
Step 7: Electronics - Assemble Other Components
1. When all connections are soldered, you can press the LED module and the Trinket into the designated pockets. Make sure the cables lie under the LED module.
If the housing is printed properly, the components should engage in their positions when light pressure is applied. If it does not fit 100% you can adjust the situation with a file or some sanding paper.
2. Also the cover fits with light pressure.
There are also colored transparent acrylic panels. ;)
Step 8: Trinket and Arduino IDE
1. download: ino file
Program for light control to play onto the Trinket Microcontroller
2. The module looks great now. For turning it into a lighting device you now load the ino file, a program that controls the LEDs, on the microcontroller.
A detailed introduction to the development platform Trinket, and everything you need to know about the program can be found here.
3. When the battery is connected, you can turn on the module by pressing the button once. Each time you press, you change the light effects. There are nine different effects pre-programmed between which you can switch.
4. You can of course also write your own code and develop your own light effects. A good introduction to the programming of Neopixel LEDs is available here.
Step 9: Attaching to the Wheelchair
1. The housing offers different connection points on the bottom side for attachment to the wheelchair.
Cable ties can be pushed through the long holes.
Self-adhesive velcro tape or double-sided adhesive stripes can be applied onto the surface.
The notches in the surface are suitable for Applying Sugru, an air-drying plasticine.
2. Do not forget the cable and the battery. The battery should be reachable and accessible to the wheelchair user in any case. You can attach the cable to the wheelchair with cable ties.
3. Each wheelchair is adjusted to its user and there are countless models and possible mounting locations. From our experience, three positions are most practical and popular: front lighting, floor lighting and back light
Step 10: Done!
Enjoy the first night out with your own lighting!
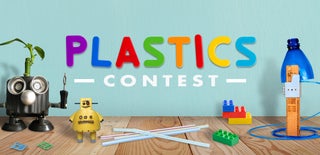
Second Prize in the
Plastics Contest