Introduction: Oscillating Spindle Sander From a Massage Pillow?!! (and a Drill Press)
So, we had a massaging neck pillow that never got used and being the curious fellow that I am, I took it apart to see what made it work. Lo and behold, I found a motor and two different sets of gears to turn the little magic fingers that worked the knots out of your neck. After knocking the stuffing out of that pillow, there was no going back to the original use and the mechanism sat in my shop (read that as one-car garage...) while I pondered how I would reuse said mechanism. Fast forward several years and several other videos about making spindle sanders and I had a veritable light bulb moment - I can make an oscillating spindle sander using my drill press and the guts from the massage pillow!
Materials: This build was accomplished almost completely by using miscellaneous materials from my shop
Guts from an old massaging neck pillow
Misc. wood scraps - plywood, 2x8, etc
Aluminum angle
1/2" square tube
Misc. bolts, nuts, and washers
CA (cyanoacrylate i.e. super glue) and accelerator
Misc. plastic tubing
Tools:
Compass
Tap and die set
Hack saw
Band saw or jig saw
Circular saw or table saw
Drill and drill bits
Chisel
Hammer
Warning! This is a fine example of redneck engineering. If you proceed with this build, you assume any risk of personal injury or damage to your drill press and/or other equipment.
Step 1: The Base
First, I measured the base of the column on my drill press. To get an accurate measurement, I used two combination squares. I held one up against one side of the base and then set the second on the other side of the base and against the first square. This will give you a very accurate diameter measurement, in this case 4-3/8". I cut a piece of plywood to the width of the pedestal base of my drill press and roughly 18" long. I then drew a 4-3/8" diameter circle centered on the plywood and centered about 8" from one end. I also marked parallel lines from the circle to the end so I could slide it around the column. Cut out the shape marked and check the fit. I marked the center of the slots in the base of the drill press and notched the end of the plywood so I could secure the plywood to the base and did so with two 1/4" bolts with washers and wing nuts. Lastly, I made a couple of small wood blocks that fit into the same slots in the base and glued them to the plywood with CA glue to help with alignment when setting this up in the future. I added a block of wood under the opposite end of the plywood to support it on my work bench.
Step 2: Attaching the Pillow Mechanism
I found a couple of long screws that held the cover on the gears and drilled slightly oversized holes all the way through the case. I used screws long enough to go all the way through the case and into a piece of 2x8 that was laying around and attached the mechanism to it. My 2x8 was about 15" long. I added another block of wood on the back of the 2x8 so I could clamp this assembly to the plywood base from the last step.
Step 3: Connecting to the Gear Mechanism
I needed to extend the shaft from the gear mechanism. The diameter of this shaft is 13/32". I cut a piece of square tube approximately 1-1/2" long and clamped it in my vise. The inside of the tube was 3/8" across so i drilled it out slightly using progressively larger drill bits until I had a snug (but not tight) fit on the shaft. You should be able to spin the square tube on the shaft without a lot of wiggle. The shaft already had a hole in it from the "magic fingers" so I drilled a matching hole for a pin to hold this in place.
I used a scrap of maple 9" long, 3/8" thick, and 1-1/2" wide and drilled a 1/2" hole in the center. (For your build, this length should be about the same length as the diameter of the circle traced by the handles that operate your drill press.) I then used a chisel to create a square hole that was a tight fit for the square tube and drove the tube in with a hammer. You'll want the tube to be as square (as in 90 degrees) to the maple as possible.
I used a trim head screw to make a pin to secure the square tube to the shaft.
Step 4: Connecting to the Drill Press
I removed one of the handles from my drill press and will use a 3/8x6" bolt as its replacement. I drilled a 3/8" hole through a small block of scrap wood, slid it onto the bolt, and secured it in place with a nut. I threaded the bolt into place on the drill press and used a short level to mark a plumb line on the block of wood. Cut the block of wood to create a face on this line. The reason for this is so the maple "arm" and the face of this block are in the same plane.
Step 5: Making the Linkage
Using the appropriate drill bit for your tap and screws that you will be using, drill a hole in the new face on this block of wood and one hole near one end of the maple arm. I used an 8-32 tap because that's what size bolts I had on hand. Tap the holes in the two pieces of wood.
Note: A trick I learned from a fellow woodworker is that after tapping holes in wood, squeeze some super glue into the hole and let it penetrate into the wood and dry. Then re-tap the holes. Do this once more and you'll have a really strong thread in the wood to hold screws.
With the maple arm assembly on the gear shaft (do not secure it with the pin yet) and roughly parallel to the arm on the drill press, measure the distance between the two threaded screw holes. This will be the approximate length of the connecting linkage. You'll want the two arms (gear mechanism and drill press) to be roughly parallel when measuring. Cut the aluminum angle to this length.
I used some plastic tube that I had to make a bushing for the connecting screws for the linkage. Drill the appropriate size hole through each end of the aluminum angle for the diameter of the plastic tube and slip a short piece into each hole. Use a little CA glue to hold them in place. Connect the aluminum angle to each arm.
Step 6: Testing It Out
The gear mechanism mount should still be clamped to the base at this point. Rotate the maple arm on the shaft by hand to test the range of motion for both it and the drill press. You may need to reposition the gear mechanism for best performance. I had a fair amount of adjusting to get this contraption aligned and the length of the maple arm correct for the proper range of movement to work with my drill press.
Once you are content with the operation of this, put the pin in the shaft of the gear mechanism and put some hot glue on it to hold it in place. This will allow easy removal if needed. Screw the mounting block for the gear mechanism to the base. I also removed all the other arms from my drill press to prevent any interference when using the sander.
As you can see in the video, I also built a work table with guides for my homemade spindles. If you've made it this far in this build, I have every confidence that you can come up with something that will work for you. The work table and spindles may be the subject of a future Instructable
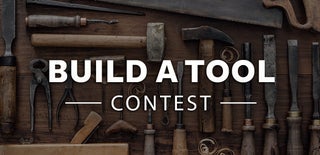
Participated in the
Build a Tool Contest