Introduction: PSoC 6 Wi-Fi BT Prototyping Kit Container
Have you ever wondered how to store your microcontrollers, especially this size?
Last semester, I was requested to use the CY8CPROTO-062-4343W PSoC 6 Wi-Fi BT PROTOTYPING KIT (PSoC 6 in short) for one of my classes at UC Berkeley. It does a lot of stuff but it's hard to carry around, unlike the other microcontrollers which are smaller and thinner. Also, since I have soldered the pins on it (sorry for the poor soldering skills XD), it made it even harder to store or bring it around. So I decided to make a case for it to help with storage and carrying it around so as to prevent from cracking and bending the pins.
After I finished version 1.0.0 of the case, I realized there is a better way to enhance it. So I made version 1.2.0. I will title them version 1.0.0 and version 1.2.0 to categorize them as old designs and modified versions.
Supplies
This is a case that can be 3D printed.
3D printed: need filament and a 3D printer, PLA will do the job
Sandpaper: some sanding might be required
Drill: a bit of drilling is required if using the version 1.0.0 design
Step 1: Tray Version 1.0.0
To start off, Let's make the tray that holds the board nicely. After measuring the PSoC 6, we will know what dimensions are required for the tray.
- Make a rectangle that is 127mm x 89mm as the size for the entire tray.
- Extrude the sketch by 15mm and you will have a rectangular block that is 127mm x 89mm x 15mm.
- Make a 123mm x 83mm rectangle on top of the rectangular block created above
- Extrude cut the block by 13mm and you will have a rectangular block that is 127mm x 89mm x 15mm.
- You will end up with a tray-like object, the PSoC 6 will fit perfectly in the tray with some moving space.
- Now, we make the handle for the tray.
- Create a 15mm x 5mm rectangle at the center of the rectangle on one of the longer sides (127).
- Extrude the sketch by 3mm and you will have a rectangular block that is 15mm x 5mm x 3mm.
- On one of the sides of the new rectangular block, create a triangle sketch that has an angle of 30 degrees.
- Extrude cut the triangle sketch by 15mm and you will end with a trapezoid-shaped handle.
- Fillet the outer edges with 0.20mm.
- Fillet the inner edges with 0.10mm.
- Fillet the handle with 0.20mm as well.
There you go, you now have a drawer-like container to hold the PSoC 6.
For 3D printing, here are a few notes to consider...
Nozzle size: doesn't matter, I used 0.8mm, larger nozzle size prints faster
Layer height: 0.1 mm
Infill Density: 10% (speed up the printing time)
Print Speed: 70 mm/s (no details need to be printed)
Infill Speed: 55 mm/s (speed up the printing time)
Initial Layer Speed: 15 mm/s (to make sure it sticks to the build plate)
Support: no support is needed since there's no overhang
Build Plate Adhesion: Skirt
Since some thermal expansion and warp might occur, the size might not be right. If you have time and enough material, reprinting it will get the best tight fit. If you don't want to, lightly sand away the defects until the tray can be slid into the case with little resistance.
Step 2: Case Version 1.0.0
Now for the Case itself...
- Make a rectangle that is 131mm x 91mm as the size for the entire case.
- Extrude the sketch by 19mm and you will have a rectangular block that is 131mm x 91mm x 19mm.
- Make a 127mm x 15mm rectangle on one of the longer sides (127mm).
- Extrude cut the block by 89mm and you will have a rectangular block that is 127mm x 15mm x 89mm.
- You will end up with a case-like object, the tray will fit perfectly in the tray with minimum space for a tight fit.
- Fillet the outer edges with 3mm.
- For the mouth of the case, Fillet the outer edges with 1mm.
- Fillet the inner edges with 0.20mm.
- On the top of the case, create text on top of the case to label which microcontroller is it. This will help the organization.
- Extrude cut the text by 0.17mm.
There you go, now you are ready to 3D print the case.
For 3D printing, here are a few notes to consider...
print the case where the mouth is facing upward to avoid support
Nozzle size: doesn't matter, I used 0.8mm, larger nozzle size prints faster
Layer height: 0.1 mm
Infill Density: 10% (speed up the printing time)
Print Speed: 70 mm/s (no details need to be printed)
Infill Speed: 55 mm/s (speed up the printing time)
Initial Layer Speed: 15 mm/s (to make sure it sticks to the build plate)
Support: no support is needed since there's no overhang
Build Plate Adhesion: Skirt is fine but the brim will make sure the case sticks
After 3D printing it, I realized that I need to release some pressure when the case and the tray were combined. And I was running low on materials to reprint so I drilled a hole on the opposite side of the mouth to release pressure. Feel free to create a hole in the CAD to avoid drilling.
Since some thermal expansion and warp might occur, the size might not be right. If you have time and enough material, reprinting it will get the best tight fit. If you don't want to, lightly sand away the defects until the tray can be slid into the case with little resistance.
Also, if you are into aesthetics, feel free to paint the text to make it stand out.
Step 3: Tray and Case Version 1.0.0
If the tray doesn't go into the case, its mainly because of thermal expansion and warp while printing. Please sand the inner of the case and the outside of the tray. If sanding is required, be careful to not over sanding both parts or else the tight fit would not work.
After using it for a few days, overall, the case does the job and I was able to store the board and carry it around without worrying that it may break. However, the handle is not big enough for me to pull out the tray from the case which causes slight trouble.
Because of that, I modified the design and created version 1.2.0
Step 4: Tray Version 1.2.0
Refer back to Step 1: Tray Version 1.0.0 to make the container for detailed CADDing. I have placed the instructions here as well for convenience.
- Make a rectangle that is 127mm x 89mm as the size for the entire tray.
- Extrude the sketch by 15mm and you will have a rectangular block that is 127mm x 89mm x 15mm.
- Make a 123mm x 83mm rectangle on top of the rectangular block created above
- Extrude cut the block by 13mm and you will have a rectangular block that is 127mm x 89mm x 15mm.
- You will end up with a tray-like object, the PSoC 6 will fit perfectly in the tray with some moving space.
- Now, we make the handle for the tray. This time, I decided to make a slider mechanism on the slides.
- Create a rectangle and a semi-circle-shaped sketch on both shorter sides of the tray. The rectangle should be 18.647mm x 12.50mm and the semi-circle should have a diameter of 12.50mm.
- Extrude the sketch by 2mm.
- Create 3 rectangles with semi-circles at the ends on the new handle. The rectangle should be 9mm x 2.71mm.
- Extrude cut the sketch by 1.5mm.
- Fillet the outer edges with 0.20mm.
- Fillet the inner edges with 0.10mm.
- Fillet the slider with 0.3mm.
Step 5: Case Version 1.2.0
Refer back to Step 1: Case Version 2.0.0 to make the case for detailed CADDing. I have placed the instructions here as well for convenience.
- Make a rectangle that is 131mm x 91mm as the size for the entire case.
- Extrude the sketch by 19mm and you will have a rectangular block that is 131mm x 91mm x 19mm.
- Make a 127mm x 15mm rectangle on one of the longer sides (127mm).
- Extrude cut the block by 89mm and you will have a rectangular block that is 127mm x 15mm x 89mm.
- You will end up with a case-like object, the tray will fit perfectly in the tray with minimum space for a tight fit.
- To avoid drilling the hole, create a hole with a diameter of 9mm at the back.
- On the top of the case, create text on top of the case to label which microcontroller is it. This will help the organization.
- Extrude cut the text by 0.17mm.
- Create a rectangle and a semi-circle-shaped sketch on both shorter sides of the case. The rectangle should be 18.647mm x 13mm and the semi-circle should have a diameter of 13mm.
- Extrude cut the sketch by 132.5mm to create a slot for the slider.
- Fillet the slot with 0.3mm
Step 6: Tray and Case Version 1.2.0
The new design allows the user to pull out the tray more conveniently and is looks better since nothing is sticking out from the case unlike version 1.0.0 where the handle is sticking out.
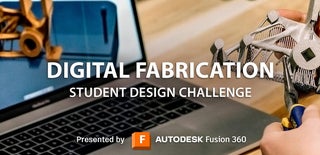
Participated in the
Digital Fabrication Student Design Challenge