Introduction: PVC Beach Sand Shovel
My friends will tell you I have an affection for making things out of PVC pipes. I tell them "they're like Lego for grown-ups!". Don't get me wrong, I think Lego are for humans of all ages, but PVC is something I can buy from Lowe's or Home Depot. That, and it's much cheaper to make big things when compared to Lego.
Anywho, my family and I were getting ready to head to the beach when I knew that "shovels" were on the list of things we needed to buy. We've had some fairly flimsy, cheap shovels in the past that don't hold up to the rigors of beach sand digging and castle making. Therefore, I took it upon myself to make something that would last using one of my favorite building materials (if you couldn't tell from the first paragraph, I'm using PVC pipe). I chose to use 4", schedule 40 PVC pipe since I had a section of that already. The process is quite simple!
Step 1: Parts and Tools
I used 4", schedule 40, foam core PVC pipe, but this should work for other sizes as well. I think the foam core may actually help somewhat for the softness of the grip. I also tried to make a shovel from a 2" pipe so it might be easier for the little kids to operate, but I had a problem using it. I'll explain later. I interspersed some of the 2" pipe process in the pictures. Otherwise, you'll need:
PVC pipe cap (4" in this case)
Tape (I used electrical tape, but any tape will work as it is only used for marking edges of cuts)
Tools: Saws
I used a powered miter saw to cut the PVC to length Sawzall, oscillating multitool saw, hacksaw, or coping saw would work
Drill and drill bit
Rasp/file/sandpaper
Step 2: Cut the PVC to Length
You may do this for whatever length you want. I chose 24" and, after real-world use, it worked quite well. My miter saw blade radius isn't deep enough to cut through the whole pipe in one go before bottoming out on the arbor, so I cut as far as it goes, rotated it, and repeated until it was all done. This can be done with any number of saws as long as you're safe about it. I wouldn't necessarily recommend using a chainsaw, however.
CAUTION: PVC has a tendency to grab a blade if it's too dull or if the PVC isn't firmly held in place.
Step 3: Mark Layout of Scoop
Since a sand shovel is more of a transfer shovel than a pointed digging spade, I made it with a flat blade. There's nothing really scientific about the design, just an intuitive shape.
First, mark a chord on one end in which if you were to make a pie wedge out of it, it may be about 1/4 to 1/3 of the whole. Make a third mark that is equidistant to the first two so that the 3 would transcribe an isosceles triangle with two equal sides. You can do this using a compass or a center head (the picture shows a center head used on a piece of 2" pipe). This center mark will also be extended down the length of the pipe to define a reference spline.
Mark the length of pipe from the center mark using a straight edge, like a level. I set the pipe on a flat surface next to the level so I could scribe the line along the center of the pipe. I found this to be the easiest way to make sure the line stays parallel. In the pictures, I hadn't found my permanent marker yet, so the pencil line doesn't show up the best. Plus, I inconveniently made the mark exactly over the factory type. I suggest using a marker and not trying to draw over the factory text. It's hard to see otherwise. By the time I started work on the 2" pipe shovel, I found my marker.
The wedge cut out of the pipe is defined by the first 2 marks on the end as well as one more 6 inches up the center spline. I don't know of a good way to draw a diagonal line along a curved surface, so I used strips of tape to define the edges.
I wasn't sure how big to make the handle holes, so I somewhat based it off of the slots on my 2' level (it feels good in the hand). My hands are somewhat big (of course, bigger than my children's hands), so I used my hand as the metric to determine the maximum size the slots would be. I picked a width of 5" by about 1". I centered the hand slots about the midway point of the shovel (1 foot). I used the tape again to mark the edges.
Step 4: Cut It Out
I originally used a 1/2" twist drill bit to define the corners of each of the cutouts. Then, I followed up with a plunge cut with my oscillating multitool to remove the perimeter of each. This proved to work quite well. Do be careful when working with power tools and PVC. If the PVC gets too hot, it can outgas and be pretty bad for you. Also, it wouldn't be good to inhale fine dust. I used a hand saw for this purpose as well to prevent too much heating. However, this felt too much like exercise, so I opted for the power tool. Using a dust mask is highly recommended!
For the smaller shovel, I ended up not spending the time to drill out the corners and just did 90 degree corners. However, this proved to be a bad idea. The sharper corners ended up creating concentrations for stress when shoveling. On the first trip to the beach, the shovel cracked at the corners of the handles due to the increased stress at the corners. The larger shovel, with the rounded corners, worked like a champ. I think the drilled out corners helped spread the stress and keep the integrity of the PVC. I recommend rounding off the corners with relatively large diameter drill bits to keep it strong.
When all the cutouts are done, smooth the edges with rasps, files, and sandpaper. Again, be careful with the dust. "Sharpen" the scoop so it can cut unto the sand instead of being too blunt.
Step 5: Beach Time!
The larger shovel worked great in the sand! It had the advantage of being able to keep water in it as well, so it somewhat doubled as a bucket. If tunnels are your thing, it works well in boring a tunnel.
As I mentioned before, you can see that the smaller shovel broke at the front of the handle. Otherwise, the design works pretty well! Have fun!
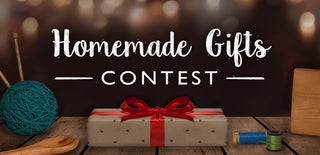
Participated in the
Homemade Gifts Contest 2017
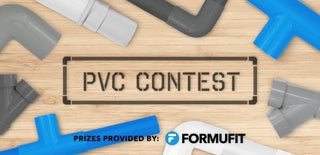
Participated in the
PVC Contest 2017
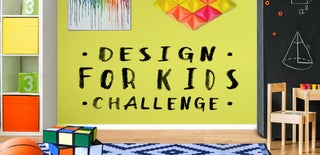
Participated in the
Design For Kids Challenge