Introduction: Paduak Inlay Epoxy Serving Board
In this instructable I will walk you through step by step on how to create an Inlay serving board out of epoxy.
Step 1: Supplies
I am using a wood species called paduak. (Pick your own color choices of hard wood that suits you)
Epoxy resin Total Boat http://www.totalboat.com/product/high-performance-...
My form is made of Left over Birch Plywood
Tyvek Tape https://www.lowes.com/pd/Tyvek-Tape-1-88-in-x-164-...
Arrow hot glue gun https://www.amazon.com/Arrow-Fastener-TR550-Lever-...
Rustoleum Headlight Restorer https://www.walmart.com/ip/Rust-Oleum-Headlight-Re...
Sander.
Drill
Screws
CNC, Planner or Belt Sander
Step 2: Measuring and Set Up
Using a combination of miter saw / table saw I cut my squares to 3.25 (3 1/4). This gave me a 4.5 (4 1/2) diagonal measurement.
Laying out the approach I cut my form base 1/4" over to allow a tight but breathable fit of 1/8" on each side
Step 3: Building the Form
I went with the overlap design as it does not need to look pretty but serve a purpose. Quick and dirty way to ensure you have a solid box.
In the short video you can see I use a counter sink bit pre-drill and then screw everything together to my base.
Step 4: Taping the Form
I am using the tyvek tape listed above. The epoxy will not stick to the tape allowing a clean and easy separation when cured.
This part ended up being a little tricky getting into the corners. Wish I had some better advice here I used a paint can opener that had the rounded back.
Step 5: Adding Squares and Gluing Up the Form
Using hot glue I add a dab to the back of each piece and secure them in place you can see in the video.
As I had the glue gun out I went back over the form and applied glue to all inside corners also shown in the video above.
Step 6: Color Choice and Pouring
This was a tough choice as there was no turning back.
Any pigment coloring will work in epoxy I like the depth pigment adds over paint additives.
But gray it is!
Step 7: Cured and Ready for Flattening
Once the pour is completely cured its time to break the little guy loose. Now grab a rubber hammer and get out some of that anger haha.
Once its out I gave it an over all inspection and moved over to the Shapeoko 3 CNC.
!!!!!NOTE!!!!!!
Here is where some projects may differ Instead of a CNC you can use a planer but you will need to take very small passes extremely slow. Drum Sander would work great. Or a belt sander also would be a nice alternative.
For cnc users Im using a 1.5 inch flattening bit. I first took a little off the bottom to give me a flat surface to work off of. I then flipped it and completely cleaned off the face as you can see.
Step 8: Sanding
Here I have sanded the board at 120 then 220 then 320.
Next we will move on to the wet sanding
Step 9: Wet Sanding and Buffing
In the video you can see I am using the Headlight Restore kit.
The kit included everything i was needing for this project.
- Drill attachment
- 800 grit sand paper
- 1500 grit sand paper
- 2000 grit sand paper
- buffing pad
- buffing compound
Step 10: And Enjoy!
This may be the most important step!
Sit back relax and enjoy your creation!
This was a fun little project that I encourage anyone to try if looking to get into epoxy work!
As always if you have any questions ask away, I will be happy to help!
If interested in seeing more projects like this check out my Instagram @handcrafted_by_trey
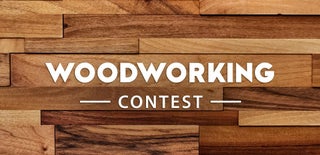
Participated in the
Woodworking Contest