Introduction: Pair O' Stools With a Pair O' Tools
In this Instructable I will show you how I was able to build a pair of flatpack stools out of a single piece of plywood, using just a couple of basic power tools. This project is affordable (around $30), attainable by even the most novice woodworker, and is a fun exercise in geometry and flatpack design.
Many flatpack projects I have come across involve CNC machines and advanced digital design/ 3D modeling. My ultimate goal in attempting this project was to demonstrate that possession/mastery of these tools does not necessarily represent a barrier of entry into flatpack design. This project does not even require a computer, so I feel that it opens the doors to a much wider audience of makers.
So grab a seat and let’s get to it!
Step 1: Design Goals
Before I even went to the drawing board I set a few rules for this project. While rules may seem restrictive, the intent of these was to provide a greater challenge and force me to think outside the box.
- Cut from a single 2’ x 4’ sheet of plywood
- Produce as many stools as reasonably possible
- No CNC allowed – only hand tools, and as few of them as possible
- Collapsible
- Packs Flat
- Assembles using no special tools
- No fixed fasteners, i.e. screws, nails
- 20” tall --- Std. height is around 18” but I wanted them a bit taller
- Stable --- I mean, c’mon. Duh.
- Easy to mark using basic drawing tools
I spent a lot of time sketching concepts, testing ideas, and staring blankly at my sheet of plywood before I arrived at this design. It is far from perfect, but I think it is a good first attempt.
Step 2: Materials
You need very few things to build this project.
- 2’ x 4’ x ¾” Plywood sheet – I used birch
- 3/8” Carriage bolt, 10” long, round head --- Qty 2
- 3/8” Wingnut --- Qty 2
- 3/8” Fender Washer --- Qty 2
- 3/8” Lock Washer --- Qty 2
- Sandpaper – recommend >180-grit, but choose based on your desired finish
I was able to get all of the above (sans sandpaper, which I had already) at my local Home Depot for around $30. Prices may vary depending on where you live and shop.
NOTE: You may want a few other items to finish out your stools, such as paint or stain. That’s an open-ended topic, so I am going to leave that part up to you. Painting will not be included in this Instructable.
Step 3: Tools
As advertised, this project can be completed in rough form using only two power tools. There are certainly better tools out there, but these are probably among the most common, the cheapest to own, and the easiest to use that you will find.
- Jigsaw --- I recommend using a blade with a higher tooth count (10-12 TPI) and straight teeth as opposed to the stock blade. The stock blade is intended for general purpose rough cuts and does not produce the highest quality edges. I knew this, ignored it, and the edges of my pieces suffered. Don’t be like me. Buy the correct blade and do it right!
- Drill --- 3/8” bit + another to be determined based on your jigsaw blade. We will be drilling holes to create the “dogbones” you typically see in flatpack pieces. Choose a bit that is slightly wider than your jigsaw blade. This will allow you to make those tough inside cuts. More on this later.
Marking Tools
You will need some basic stuff to mark out the templates for all of the components.
- Pencil
- Ruler
- Yardstick
- Protractor
- Compass --- capable of extending to > 8” diameter
- Paper (optional) --- for notes and templates
- Any round object ~4” diameter (object) --- time saver for marking radii --- I used a large pitcher
Optional Tools
There are some other useful tools that you may need depending on your end goals for the project, or that may save you some time along the way. If you have access to any of these then go for it.
- Power Sander --- I used an orbital sander, but any other variety (drum, belt, planer, etc.) would do the job as well
Step 4: Marking Overview
As you can probably imagine, marking the templates comprises the bulk of the workload for this project. Before we dive in I would like to address some general items and design components that you will encounter.
There are four components that make up this design (legs, seat, frame, and compression plate) and dimensioned drawings are included for each. If you feel comfortable reading and translating these into marks on your sheet, go for it. However, for those of you who need some additional guidance, I have also included some excruciatingly detailed instructions explaining how I went about making each mark.
If you download the attached design files (included in the individual steps) you will notice that they are comprised of many layers. Each layer represents a unique portion of the design (grid marks, detailed marks, cut lines, mandatory holes, optional holes, etc.) and selectively turning them on/off in your viewing program will allow you to focus in on specific information as it is presented. I encourage you to take advantage of it. My drafting instructors would be so proud…
The little holes in the corners of some joints are referred to as dogbones. They are required because it is impossible to make an inside 90-degree cut in certain scenarios. Scenario 1 would be on a CNC machine, whose round bit can’t cut a square inside corner (outside is possible). Scenario 2 would be a saw trying to cut an interior, rectangular slot. You can make the cut by going in at an angle and slowly clearing away the back edge but this is messy and time consuming. In either scenario, the dogbone effectively takes the corner away, providing clearance for the blade/bit and ensuring that we get square edges.
In the case of this project, it is possible to cut some inside 90-degree corners without using a dogbone. Being able to do so depends on the sequence in which you cut components out and your tolerance for simultaneously handling/sawing small pieces. These holes are marked as “optional” and you can include/exclude them as you desire.
Finally, precise marks and general organization will make or break you in this project. The old adage, “mark twice, cut once,” definitely applies here. Labeling parts, double-checking alignments, taking advantage of symmetry between parts, and shading cutout areas to distinguish them against a busy background of marks all go a long way to help out. As colorful as your sheet may get, remember you can sand it all off later.
Attachments
Step 5: Marking: Base Grid
In designing this project I spent a lot of time thinking about how I could layout and mark all of the components with as little effort as possible. The product of this was parts sharing several common dimensions, making use of existing edges, sharing edges, and laying neatly on a base grid.
To take full advantage of this, you need to go ahead and draw a grid of your own. Each square needs to be 4” x 4”. For all you non-math types, that means that on a 2’x4’ sheet you will have a 6 x 12 grid with 72 total squares.
Required areas (in 4” grid spaces) for pieces are as follows:
Seat –3 x 3 --- Qty 2
Leg –1 x 5 --- Qty 6
Frame – 2 x 1 + some change --- Qty 6 --- the key on the top of the frame piece will extend outside of this area. Fortunately, we have ample space to accommodate this.
Compression Plate = 2 x 2 --- Qty 2 --- this is conservative. We’ll use the extra room to account for the extra areas in the frames above.
In case you weren’t counting, that means we’ll have about 4 squares (64 sq.in.) leftover. Yay! Scraps for another project!
Feel free to play around with different configurations on your own, but I think that the best way arrange them is with the seat on one end, the frames and tension plates on the opposite end, and the legs in the middle. This divides the sheet “hot dog style” with one stool per vertical half of the sheet. This arrangement also eliminates several cuts by taking full advantage of straight edges placed along the edge of the sheet of plywood.
This grid and the general arrangement outlined above will make your life much easier in the upcoming steps as we detail each component. Let’s dive in.
Step 6: Marking: Legs
In order to achieve the required base area, the legs will need to be angled 10-degrees from perpendicular. They will also need to slotted to connect to the frame piece, notched to seat the compression plate, and eared to clear the carriage bolt. Let’s get to it.
- Start in the top corner of the leg and use your protractor to draw a 10-degree angle across the width of the piece. This will form the angle at which the leg contacts the bottom of the seat.
- Measuring from the top corner and along the length of the leg, place marks at 2” and 7-1/2” (relative to the corner). Repeat this process on the opposite side relative to the point at which the 10-degree angle line you drew in Step #1 intersects the edge of the leg. Connect each set of points using your ruler to create parallel lines at a 10-degree angle.
- Measuring from the point where the original 10-degree line you drew intersects the edge of the leg, and along the 10-degree line. Make a mark at 1-1/2” and at 2-1/4” (3/4” between).
- Draw a line through these points, perpendicular to the original 10-degree angle line, and intersecting the 10-degree angle line drawn at the 2” mark. This will form the slot for attaching to the frame.
- Parallel to the slot, in the top corner, draw a perpendicular line passing through the point where the the 10-degree line at 2” intersects the side of the leg. This ear will provide the necessary clearance for the carriage bolt to pass between the legs.
- On the same side, measure 1/2” along the 7-1/2” offset 10-degree line. Draw a perpendicular line running through this point and toward the side of the leg. This line shoud be parallel to the frame slot and the ear you just marked. This notch will provide a flat seat in which the compression plate can seat and pull the assembly together.
- There are two required dogbone holes at the bottom of the slot. A third, optional dogbone hole is at the corner of the notch further down the leg.
- Finally, use your compass or a round object to draw a radius (> 2”) at the bottom of the leg. Alternatively, you can make a flat bottomed leg by drawing another 10-degree line through the bottom corner, and parallel to the other lines you just drew.
PRO-TIP: If you mirror pairs of legs then you can reuse the 0”, 2”, and 7-1/2” offsets, reducing the marking time significantly, and better ensuring things align properly.
Attachments
Step 7: Marking: Frames
The frames are perhaps the easiest component to mark since the make use of the most basic geometries. Precision is key however, as they provide the foundation for much of the assembly.
- Begin by dividing the 2x1 grid area in half, vertically. This will form the top of the slot and the bottoms of the notches that allow the frame to connect to its twin siblings.
- Next, use your ruler to mark 1” from the edges of the piece, forming two 1” x 2” rectangles in opposite corners of the piece. These notches are where the frame pieces will interconnect later.
- Finish marking the 2” deep leg attachment slot by centering a 0.75” x 2” rectangle, oriented vertically, on the bottom edge. You can draw this by marking a 3/8” offset on either side of the main gridline dividing the piece in half, or by measuring 3-5/8” from the left or right edge.
- To mark the top key by which the frame inserts into the seat, draw a horizontal line ¾” above the top of the piece (4-3/4” from the base). Draw the sides of the key by placing a mark offset 1” from the centerline, or 3” from the edge on either side.
Much like the legs, dogbone holes are required in the slot, but are optional everywhere else.
Attachments
Step 8: Marking: Compression Plate
The compression plate is the piece that literally holds everything together. Its base shape is an equilateral triangle, and marking it is simpler than you think.
- Start at the base of a 2 x 2 grid, and adjust your compass to a diameter of 8” (across two grid squares). This will be the bottom side of your triangle and the endpoints of this segment will be two of its three vertices. Place the point of the compass on either of the vertices and draw an arc intersecting the centerline of the 2 x 2 grid. Technically, this intersection point is the third vertex of the triangle, but go ahead and repeat the process on the opposite side to verify.
- Connect the bottom vertices to the top one using your ruler and the equilateral triangle is complete!
- The plate will be slotted where it mates with each leg. Each slot will be ½” deep and ¾” wide to match the width of the leg. To get the placement for each one, start by finding the midpoint of each side of the triangle (hint: one side is already done).
- Draw a line intersecting this midpoint and the vertex opposite it. Your slots need to be centered on these lines.
- Mark the ½” depth along the perpendicular bisector lines you just drew.
- Then draw parallel lines at 3/8” off both sides to finish out the slot. Each of these slots will have two dogbone holes since they are interior corners.
- The point where all of the perpendicular bisectors meet is the center of your triangle. It is also the precise location where you will need to drill a 3/8” diameter hole for the threaded end of the carriage bolt to slide through. Mark it accordingly.
- Finally, for aesthetics and so a pointy triangle doesn’t poke you in the leg while you are using your stool, we’ll round off the corners of the triangle. I used the same 4+ inch round container to mark mine. Any round object, or your compass will do the job though. Just be sure to leave plenty of room for the slots to do their thing!
Attachments
Step 9: Marking: Seat
The seat was possibly the most intimidating piece for me since it is the most visible piece of the entire assembly. That meant that getting it right was critical to ensure I didn’t end up with a loose, sloppy, poorly fitting mess.
- We’ll start with the easy part; rounding out the corners. Pick up your favorite round object or compass again and mark some radii. You could also make a circular seat if that suits you better. I chose a square seat because…well I don’t know. It just looked cool!
- Next, find the center of the seat by drawing the diagonals of the 3 x 3 square. The hole for the top of the carriage bolt will go here.
Now, you may have noticed, the top of your carriage bolt is square! This allows it to be tightened despite its round head. Surely you’ve heard the saying, “you can’t fit a square peg in a round hole.” This is that in real life!!! I’ve got a simple solution to fix this later, so for now just make a mark for a 3/8” hole.
The challenging part is locating the three keys that attach the frame to the seat. When assembled together, the inside edges of the three frame pieces will form a 6” equilateral triangle. We need a 6” equilateral triangle, STAT!!! Geometry to the rescue, yet again!
I experimented with a few methods, but by far the easiest is to separately draw your own equilateral triangle and transfer the necessary dimensions to the seat.
- To start, bust out your ruler and a sheet of paper and draw a 6” line segment.
- Using the same technique that you used to mark the triangle for the compression plate, find the third vertex of the triangle (Recall: 6” radius arc from each vertex, do it for both sides, 3rd point is where they intersect).
- Draw in the sides to complete it.
- Just like you did for the compression plate, find the midpoint of each side and draw the perpendicular bisectors to reveal the circumcenter of the triangle.
- Place one end of your compass on the circumcenter of the triangle and the other end on any of the three vertices. Transfer the compass over to the seat template and draw a complete circle with its center at the center of the seat. Choose any of the four points at which this circle intersects the diagonals. This is vertex #1.
- Go back to your sheet of paper and set the radius of your compass at 6”. Now transfer it back to the seat template and draw a 6” radius arc with its center at the vertex you drew in the last step. The final two vertices are located where the circle you drew in the last step intersects this arc.
- Connect the vertices to form the sides. Your 6” equilateral triangle is complete!
- Find the perpendicular bisector of each side by marking the midpoint and connecting it to the vertex on the opposite side.
- The process for marking the holes is also exactly the same as it was for the compression plate (centered on the bisectors you just marked). However, in this case the holes go outside of the triangle and their dimensions are 3/4” x 2”. Each one gets a set of 4 lovely dogbones as well. Fido is drooling right now…
And with that you are done marking!!!! Thank goodness!!!! That was painful, but it’s all downhill from here.
Attachments
Step 10: Drilling
We are depending on the dogbones to allow us to make some of the required cuts, so drilling first is mandatory (with the exception of the center holes on the compression plate and seat). Bust out your drill and get to work.
As you may recall, the holes for the dogbones need only be as wide as your jigsaw blade. I would recommend using the smallest size you can get away with. Mine were 5/16”.
3/8” is the only option for the center holes that will the carriage bolt will pass through. Go ahead and drill these now as well.
Once you’ve got the hole drilled in the seat, we have one last piece of unfinished business. Run the carriage bolt through the hole until the square end stops it. Use you pencil to carefully mark along the sides of the square head. You will need to cut out this box to allow the carriage bolt to sit flush on the top of the seat. The 3/8” hole you drilled will serve as its dogbone and you can square off the small corners using the jigsaw in the next step.
Step 11: Sawing
Finally, the moment you’ve all been waiting for….cutting it out! There’s really no guidelines here other than take your time, follow the lines, watch what you cut, and watch your fingers!
Sequence is entirely up to you!
PRO-TIP: Shade in the areas that are not part of any component so you don’t accidentally cut through a part.
Step 12: Sanding
Chances are good that, along your cuts, there are some burred edges and your lines aren’t perfectly straight. Luckily most of this can be fixed with a good buffing. Smooth out any rough spots, flatten any bad lumps, and get you pieces cleaned up so they will fit together easily in the next steps.
Step 13: Assembly: Seat
Begin assembling your stool by running the carriage bolt through the square hole in the seat. Flip the seat upside-down and rest the head of the bolt on the floor, ensuring it remains flush with the surface of the seat.
Step 14: Assembly: Frame
Grab the three frame pieces and arrange them to form an equilateral triangle by alternating the orientation and interlocking the notches on the ends. All three of the top ¾” x 2” keys should be facing downward.
Carefully lower the interlocked pieces so the keys slide into the slots on the bottom of the seat. This requires some coordination.
Step 15: Assembly: Legs
Insert the slots on the legs into the slots on the frame pieces. Legs should be angled outward and their inner tips should just clear the carriage bolt.
Step 16: Assembly: Compression Plate
Carefully slide the compression plate onto the threaded end of the carriage bolt until it is seated at the bottom of the notches in the middle of the legs.
Adjust the legs so they are seated firmly within the three slots in the compression plate.
While holding the legs in place with one arm, install a fender washer, lock washer, and wingnut on the end of the carriage bolt. Tighten the wingnut down until the lock washer compresses and until you can no longer turn it by hand.
Your stool is complete! Go try it out!
Step 17: Project Recap
On the whole, I have to say I am beyond excited at how these stools came together. Not only did I achieve every single one of my design goals, but they look great, and are reasonably comfortable too. Designing them truly was a truly enjoyable exercise and I can’t wait to try some more flatpack design on some future projects.
I did the math and the material utilization rate of the plywood sheet for this project was just shy of 80%. I don’t have much basis for comparison, but I would say that’s pretty great!
Despite owning my own CNC machine, I sure seem to make every effort to avoid them in my Instructables. In reality, I love CNC machines more than anything but, having built my own, I am fairly keen as to what their limitations are. The key issue with mine is size. Hopefully one day I will be able to expand it so it can handle a sheet of plywood, but until then I’ll stick with my jigsaw.
Step 18: Thank You!
As always, THANK YOU SO MUCH for taking the time to read this Instructable. I hope that you have learned a thing or two and are already well on your way to building your own pair of stools. It truly makes my day to see those “I Made It” banners, so please post your takes on my design or what you’ve done to improve upon it.
If you like what you see, then please go check out some of my other Instructables, my blog, my YouTube channel, and follow/subscribe so you don't miss out on what's next!
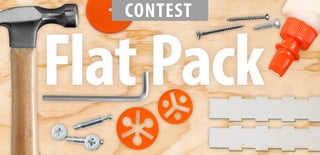
Participated in the
Flat Pack Contest