Introduction: Parallels for Aligning Lasers and CNC Routers
In a previous Instructable I showed how to build the "Laser Buddy". This device get the laser aimed very precisely a a point on the workpiece. But there is no guarantee that the workpiece is square to the axis of the machine. Here's a set of adjustable parallels that will save the day.
CNC routers have the same problem, so this device is helpful to both types of machines.
The parallels are connected as a parallelogram. The long pieces, I call them rules, are linked together with links that can pivot. Since both links are the same, and the pivot points on the two rules are identical, the two rules will remain parallel no matter what distance separates them. So you can use the parallel to offset an object any distance from a machine reference and keep it aligned with the x/y axis of the machine.
You will need:
1/4" (6mm) Acrylic
Posterboard or other material for washers (see text)
Six #10-32 x 1" Flat Head Screws (other size, see text)
Six #10 steel washers
Six #10-32 Wing-Nuts
Tools:
Laser Engraver, Drill Press or equivalent, and an 82 degree countersink bit.
Step 1: Cut Out the Rules and Links
The included DXF file has 12" rules and 4" links. This gives an adjustable distance from 1.5" to 4" (27mm to 100mm).
Cut the Rules and Links from 1/4" (6mm) acrylic. The holes are 0.196" in diameter for #10-32 hardware. If you wish to use other size hardware you should modify the hole diameters accordingly.
Attachments
Step 2: Countersink the Holes in the Rules
Flat head screws require a countersunk hole. On one side of each rule, cut countersinks so that the screw heads will be flush, or slightly below, the surface of the rule.
Step 3: Cut the Washers
Cut the washers from posterboard or similar material. Thin PVA foam may be a good choice. The washers provide some friction between the Rules and Links to hold them in position. You may want to modify the hole size in the washers to fit you hardware if #10 was not used.
Attachments
Step 4: Assemble the Parallels
Put a small amount of glue on the screw heads to keep them from turning. E6000 or similar flexible adhesive would be a good choice. Put the washers on the screws and then the links. Next install some steel washers and wing-nuts. Don't tighten the wing nuts too much, it may cause the rule to crack.
Step 5: Inspect Your Build
This shows the finished set of parallels. Adjust the wing-nuts so that the unit adjusts smoothly. When in use, only one wing-nut generally needs to be tightened to lock the parallels.
Step 6: Using the Parallels
The bottom rail of the honeycomb bed of this laser is set parallel to the X axis of the machine. I use the parallels to space the workpiece away for the rail, but still preserve the alignment with the X-axis. I used the red dot to find the center of the workpiece (Laser Buddy would be more accurate). As you can see, the border was aligned perfectly with the edge of the piece. The center alignment is a tad off. Maybe I should have used a Laser Buddy.
The parallels also work well for aligning workpieces on the bed of a CNC router. Take a few minutes and build one of these. I'm sure you'll find many uses for it.
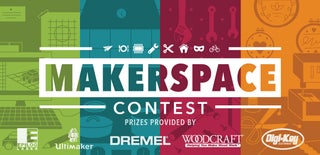
Participated in the
Makerspace Contest 2017