Introduction: Personalised Pendants
In a previous Instructable (Coaster Making), I explained the process of making 3D printed coasters with an exposed infill pattern filed with epoxy resin to add both strength and colour.
In this Instructable using the same techniques I decided that I would make something that was functionally different, portable, and personalised.
The result was the Personalised Pendant.
This can be used as a keyring, necklace, zip-puller or luggage tag that can be personalised.
The personalisation would take the form of a single initial on the pendant indicative of a first name.
Supplies
Step 1: Design
The design was created using BlocksCAD.
The Blocks code illustrates the process described below.
First of all we have to decide on the shape of the pendant, I chose a circular shape.
The circular shape being a short cylinder with dimensions with 15mm radius and height of 5mm.
Having decided on the shape and dimensions we place a small hole towards the top the cylinder, this will serve as a location with which to hang the pendant. The hole has dimensions of 1mm radius with a height of 5mm at a location of X=0, Y=11mm, on the central vertical axis.
The personalisation will take the form of a single letter within the central area of the pendant creating a cut out.
The depth of the cut out letter will be 2mm.
By placing the code in a module and passing three parameters, the letter, x & y co-ordinates multiple letters may be produced on the design grid and thereby printing a collection of different letters.
Attachments
Step 2: Slicing
Once you have finalised the pendant preparation for printing with a suitable slicer is required.
Using Cura I will use this to describe the process.
Open the OBJ file created with BlocksCAD design software.
This is were we will make adjustments to the slicer print setting.
In order to display the infill we will need to set the the Top Layers to 0. The top layer will therefore not be printed revealing the infill pattern.
Leave the Bottom Layers set to the defaults as we want to retain the fill within the confines of the printed pendant and around the letter and not have the epoxy resin escape out of the bottom.
For the infill pattern I have chosen Tri Hexagon in order to make filling the infill pattern post printing an easier task, do not set the percentage too large, I have chosen 60% the reason will become clear during the filling process.
Obviously you can change the infill pattern type and the infill density to suit different requirements.
Step 3: Post Print Preparation
You may use any number of colours for printing, although black will highlight a greater range of infill colours. Once the pendant has been printed there is some preparation to be completed first.
The printing process is not without some imperfections and each cell my not be entirely isolated, small holes may exist within the structure of the walls.
A visual inspection may identify holes, cracks or layer separation which depending on severity can be filled in with Cyanoacrylate adhesive, putty, or tape. As the process will also identify any holes in the perimeter walls of the print.
If you create multi-coloured designs you will need to be aware of unintentional colour mixing from seepage between cells. Not an issue if you will be using one colour.
******* Sealing epoxy resin mix only required for multi coloured designs.**********
Prefilling action is required as a precaution for multi-coloured designs using a sealing epoxy mix.
Using a suitable epoxy resin mix having chosen a 2:1, two part mix with 12hr cure time.
Make sure the product has a useful working time and not to make too much unless you can make use of the excess elsewhere.
Following the manufacturers recommendation and wearing suitable protective equipment make a clear mix without adding any colour.
Pour into the infill cells up to a maximum of 75%, the thicker the object the more epoxy may be required to fill the bottom and side walls.
Although, wicking action will pull the resin up the wall to seal holes nearer the top hence filling up to 75%.
But also having enough of a pocket to accept your chosen colour and that some post cure sanding will be required to level the surface.
However, these guidelines will vary subject to the infill pattern, size, imperfection density and epoxy viscosity
Step 4: Colour Filling
If a multi coloured design is being created allow the previous epoxy to cure before adding colours.
Try not to place differing colours in adjacent cells in the same process, allow one colour to set before adding another to prevent colour seepage. Pre filling the cells as in the previous process will help to reduce the likelihood of this happening.
In the event of a single colour non of the afore mentioned issues should apply.
As mentioned previously setting the infill percentage too high results in small cells and these resist taking up the epoxy due to the formation of air pockets.
Therefore, dripping or piping the epoxy into the cells allows the air to escape, these air pockets may not be obviously immediately but can erupt later in the process slowly rising due to the viscosity of the epoxy, if the cells are filled too quickly.
Fill slowly and tap the object to encourage any air bubbles to show up sooner before the epoxy cures. Although, depending on the cell size and colour complexity post filling can again be applied but it's much easier if its right first time.
Over filling will not normally be a problem as it makes it easier to end up with a uniform flat surface and without recourse to post filling and give a better surface for polishing.
Underfilling, will result in depressions in the cells, these may or may not be widespread across the area that has been filled. However, it can be tempting to try and sand all these out flat but exercise cause as you may end creating more issues by thinning or revealing deeper features that may then require remedial action.
Step 5: Post Fill Processing
With the filling process complete allow the epoxy to fully cure.
If the epoxy is not fully cure it will still be a little soft and will smear and tend to resist sanding resulting in pick of grit on to surface giving it a dull appearance that is hard to polish.
Even after curing, you may yet still identify some imperfections.
These could be:
1: Poor definition of infill separation boundaries.
This may be recovered by sanding the surface use a fine grade paper such as 240 to minimise deep scratches. Recommend washing in a mild detergent to remove grease and debris after sanding. Making sure its dry before applying further epoxy resin.
2: Voids in cells due to air pockets. Refill again and/or checking more frequently during the curing.
3: Boundary seepage marks. Remove by sanding, filing or cutting off excess. If the seepage is in a noticeable colour compared to its surroundings it may be necessary to apply further epoxy or acrylic paint to the area to blend it in to the surrounding material.
Step 6: Polishing
Once the Post Fill processing is complete its time to apply the finishing touches.
This could be in the form of two methods.
1: Surface polishing with an epoxy resin polish to remove all surface imperceptions and add a shine.
This is ideal if the surface is very flat with few imperfections.
2: Apply a layer of clear uncoloured epoxy to the surface I applied the latter as it gives a superior finish as long as you ensure the surface is clean and grease free, IPA or Methylated spirit works well.
This also helps produce a smooth surface if a number of small depressions exist.
Once you have polished it or applied a clear epoxy coat and allowed it to cure the pendant is complete.
All that remains is to determine how to hang it.
Step 7: Hanging the Pendant
As described in step one the finished item can be used as a keyring, necklace, zip-puller or luggage tag requiring personalisation.
This can be accomplished by attaching a split ring through the hole.
If the hole is too small for the chosen ring it can be widened with a small drill bit 2.5-3mm.
Attach a second ring through the first ring if you want it to face forward rather than sideways if your using it as a zip puller on a jacket or coat for example.
Another method of attachment could be a small diameter ball chain or cord subject to personal taste and/or usage.
Step 8: Finally
Display it with pride as per your chosen method.
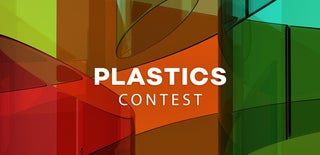
Participated in the
Plastic Contest