Introduction: Phoenix Fire Puppet
Please Take a second to vote for this instructable and rate it if you enjoyed it! :)
Although this is part of a larger structure, the puppet itself can work as a stand alone project. Photo byShaan Reza Ali
View the entire Forest Rising fire art project including the structure we launched the puppet from.
https://flamewriter.art/forest-rising/
Step 1: Design the Steel Structure
I based mine on an Australian Kookaburra and drew this up in Adobe Illustrator. The idea is to use as less material as possible to keep the weight down as much as possible. The heavier the puppet, the harder it is to puppeteer.
This reference by Creative-Addict
Step 2: Design With Dimensions
All measurement in MM. The purple is mm solid steel rod (D: 4.76mm) with the rest round tube steel (D: 12.7mm WT: 1.6mm ID: 9.5mm Kg/mt: 0.441)
Step 3: Main Puppet Frame
Joined using stainless steel hose clamps. The right angle joints were done with two interlocking hose clamps.
Step 4: Puppet Hinges
An extra piece of steel was added to the hinge joints to thicken the steel to re-enforce them. I used high tensile bolts for the hinge.
Step 5: Welding the Other Pieces
The wing feathers, head and tail were welded by Rohan at Norm Warehouse.
Step 6: Welding Complete
We also added the verticle pipe pictured in the next image
Step 7: Attach the Springs
Puppet with the springs attached. On each side is a stainless steel spring as well a standard steel one from the hardware shop. I predicted the springs to be the fail point and a risk that they would fail completely with the heat of the fire. They lasted 12 seconds and enough for the show.
Step 8: Detail Showing the Spring Attachments at the Top
Springs fail when stretched too far so I attached a cable (top + left) to stop the spring overextending. Not shown are the cables that pull the wings down. They are placed further out on the wing to increase the angle of the cable.
If the wings went too high, the angles prevented the downwards pull so we made two stops pictured in the large circle. You can see the curve on the bar, where the springs are too strong for the material so we also re-enforced this bar. We got this slightly wrong, so I used another hose clamp to space it perfectly. I predicted a risk that this bar may fail, however, the structure held perfectly with the springs the only fail point of the bird. Secondary welding by Brian.
Step 9: Dimensions of the Spring Stretch
Step 10: Video Explaining the Lift Mechanism for the Puppet
The anchor point for the downward motion of the wings was re-enforced and better secured than was pictured in this video.
Step 11: Lift Pully at the Bottom of the Pole
(missing From Video)
Step 12: Drawings Explaining the Lift Mechanism for the Puppet
Step 13: Moving the Completed Lift Channel
Step 14: Lift Channel Inside the Main Support Structure Being Lifted Verticle.
Step 15: Adding the The Accelerant Cladding
The accelerant cladding was done in two layers. The first using molten soy wax bound in jute strapping, secured with thin tie wire. Wax requires a high temperature to burn and once it is alight burns hot and bright.
The second layer was raw jute strapping as we planned to add gum turpentine while dousing. We could not add the gum turpentine (see below) so only the soy wax provided the flames.
Step 16: Lifting the Puppet With a Crane
Probably the lightest thing the crane operator has ever lifted. Once in place, the puppet was secured with a pipe sleeve and hose clamps. We attempted to hide the puppet as much as possible while stacking timber into the structure so the burners would not know about this part. We like surprises.
Step 17: Dousing the Bird
The view from the top of the scaffolding while we are loading 80 litres of used vegetable oil sourced from the Grongi pub. We attempted to douse the puppets second layer of webbing with gum turpentine. This was not working and could not be done safely so we abandoned the plan. The first layer of soy wax burnt well anyway.
Step 18: The Puppet in Flight
00:00 – Tiffany and myself pull the rope that is attached to the steel cable mechanism to pull up the puppet.
00:02 – Puppet reaches its peak height. Wings have not pulled down.
00:05 – I assume the downward wing mechanism has failed. After reviewing the video, the puppet has not reached full height. Probably some wood has jammed somewhere. Likely stopping the bolt we used to stop the puppet twisting. During this time i realised the lubrication from 80 litres of chip oil has made the puppet feel a lot lighter for one person to handle. I ask my partner to drop her rope.
00:07 – I get the feeling of the mechanism and puppet weight.
00:09 – I start jerking the puppet as hard as I can to get the springs to recreate the pull effects.
00:10 – This works. I keep jerking.
00:18 – The wing springs fail.
00:26 – I drop the puppet.
Step 19: Orginal Sketch
I originally planned to have a flexible tail but went with a rigid one.
Step 20: Plastic Alternative
Not quite finished version 1. I started with “a little bit of plastic”. As you can see, this is a lot of plastic. I was tripping with this direction and scrapped it.
I predicted this should have worked better than the steel one as it would have flexed and added more life to the puppet. It would have also been destroyed in the fire. Made from fire sprinkler CPVC pipe with fibreglass tent poles. Bound (not completed) by fire-resistant fibreglass tape.
Step 21: View the Entire Project
View the entire Forest Rising fire art project including the structure we launched the puppet from.
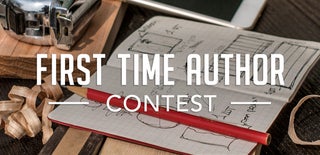
Participated in the
First Time Author