Introduction: CNC Pink Foam Surfboard
After learning how to surf in New Zealand and Australia, coming back to the United States without a surfboard made going out on the water a little disappointing. With a little bit of extra time I decided to make a surfboard from scratch and hopefully get it done in a few months so I could take it out on the water in the summer. Luckily I am a student at Georgia Tech and have access to the awesome Invention Studio. Here I have access to 3D printers, laser cutters, waterjets, a cnc router, a full woodshop and much more, so this isn't exactly a DIY project, unless you happen to have access to all this equipment.
Supplies
Shaping the Surfboard
Insulation Foam Board (2" x 4' x 8')
Thin plywood (1/4" x 6" x 8')
Wooden dowel (1/4" x 4')
Gorilla Glue
Sandpaper (~100 grit)
Ratchet Straps
Access to:
CNC Router
Bandsaw
Fiberglassing the Surfboard
6 oz Fiberglass Cloth (40" x 9 yrds)
2 Part Epoxy Resin (1 Gallon)
Resin Research Additive F (4 oz)
Mixing Buckets (at least 10)
Wooden stir sticks (at least 10)
Cheap brushes (at least 10)
Flexible spreaders (2)
Various Sandpaper (100 to 1000 grit)
Blue painters tape
Scissors
Razor Blade
Builders Paper (to protect your working area and for easy cleanup)
Disposable gloves (tons)
Painting the Surfboard
Water based paint (I used white as a background color)
Alcohol dyes (I used blue to tint the resin)
Paint brushes
Blue Paint
Fins and Leash
Polycarbonate (3/8" x 12" x 12")
Metal rod (1/4" x 4")
Access to:
Laser Cutter
Resin 3D Printer
Handheld Router
Step 1: Designing Your Board
This is the most creative part of the process and is where any surfing experience can influence how you create your board. Surfboards come in a variety of shapes and sizes depending on how experienced of a surfer you are and what waves you are looking to ride. In general, beginners learn on longer, wider, thicker boards that are easier to get up and stay balanced on. As you become more advanced, you can transition into rider shorter, narrower, thinner boards that are lighter and more maneuverable in the water.
You can find CAD models of surfboards that manufacturers use to make their boards but I chose to create my own design, while basing it on the rough dimensions from a manufacturer. I used the catalog (attached below) from a surfboard blank company to give me the rough shape I wanted and then design my own edges, tail, and curvature in the board. The edges are very important for how the board reacts in the water. As seen in the first pic above, symmetric rounded rails (50/50) are great for beginner soft boards as they make the board very stable in the water. Hard rails (80/20) have a much sharper edge and are great for really digging the board into the side of a wave while turning. This is perfect for advanced surfers but make it much tougher to balance on the board for beginners. For my rails I chose a progressive system where the shape of the rail changes from the nose to the tail. This way, the board is still very balanced in the middle but does allow for tighter turns when you shift you weight towards the back when carving through a wave. With Solidworks, this was relatively easy to do with variable-radius, asymmetric fillets.
The tail design and curvature of the bottom of the board also affect how it rides but not nearly as much, especially for a beginner rider. With these aspects, as well as general shape/lines/contours I took a more creative route and just designed a board that I thought looked great.
Attachments
Step 2: Shaping Your Board
This next step is the hardest to do without a large CNC router: shaping your board. I had access to CAMaster Cobra router which made cutting the surfboard out of a piece of 2'x8' pink foam extremely easy. Since the final board was going to be thicker than 2" (thickness of my stock), I did have to split the design into three layers that I cut separately and then glued together at the end. I did this by splitting my model up in Fusion 360 into 3 separate parts that were each 2" thick, and then created my tool paths for each part. How you set up your tool paths will vary greatly depending on what machine and what tools you have available so I won't go into too much detail about what I did. To start off in Fusion 360, I created indexing holes and pegs in all the parts so that I would be able to position each part after I flipped it over to machine the other side. Then I created a roughing pass with a 1" end mill to get rid of most of the excess material. After that, I had one more pass with a 1/2" ball end mill to more accurately define the curved surfaces and edges of the board.
After this, I glued the three layers together with Gorilla Glue and used my indexing holes created with the CNC and wooden dowels to keep all three layers aligned while clamping. Since it was such an organic shape, I used 7 ratchet straps to provide even clamping force while the glue dried.
To strengthen the board lengthwise, its standard to run a thin piece of plywood down the middle of the foam board. I used a bandsaw to cut the board in half lengthwise and then traced the profile of the board onto a peice of plywood. I used a jigsaw to cut out the profile and then used the ratchet straps to clamp everything together while I glued the plywood profile in between the two foam halves.
The final step is to trim all of the wooden pegs so they don't protrude out of the board and to sand off any excess dried glue and to get rid of the lines and ridges left over from the CNC passes. The foam is very soft so sanding by hand with a piece of sand paper wrapped around a block of wood will be the easiest way to get the surface finish you're looking for.
Step 3: Fiberglassing Your Board
This next step is easily the messiest so be prepared with a wide open workspace and lay down builders paper on the floor and tables so you don't drop epoxy everywhere. I set my board on two old paint cans on top of a table so that the board was high enough for me to work on the top and on the edges down towards the bottom of the board and make my way around the entire perimeter.
The first step is to fiberglass the bottom of the board, so we have to mark the outline on the top of the board. The easiest way to do this is to take a sharpie and tape it to some paint mixers as shown in the pic above and then let the shape of the board guide the sharpie to get an outline about 2-3" in from the edge on the top. Then take some blue painters tape and outline the inner edge of the sharpied line (so that the fiberglass wont stick beyond this line). The next step is to put on some gloves so that you don't get fiberglass fibers or epoxy all over your hands, and then lay out your fiberglass cloth on the bottom of the board. Cut the cloth so that there is at least 6 in extra hanging off the sides of the board. A clean, sharp pair of scissors will help with cutting the cloth without fraying. After cutting it to length, go around the board and cut triangles out of the cloth around the tight corners of the board so that the cloth will be able to lay flat when you wrap it around the edges of the board.
Now its time to mix up the first batch of the epoxy. How exactly you do this depends on the brand of epoxy you have so make sure to follow the manufacturer's directions exactly. I started out with mixing 600 ml total of epoxy, but this might change depending on the weight of your cloth and the size of your board. As long as your'e quick about it, you can always mix up another batch of epoxy if you run out midway. Once you mix it thoroughly, pour the epoxy over the cloth and with a plastic spreader, slowly spread the epoxy across the whole board. You shouldn't have to push down very hard as the cloth will soak up a good bit of epoxy. Spread it all out evenly across the whole board and then start working on the edges. I found it easiest to hold up the part of the edge I was working on and then spread epoxy onto that part and let it soak in, and then use the spreader to push the edge down and up against the underside (top) of the board. If the epoxy is saturated enough, the cloth will stick to the underside and you can move onto the next edge. Continue this all the way around the board until all the cloth is saturated and there are as few wrinkles as possible.
Make sure to note the time when you mixed the epoxy and then check back after 2-3 hours and you should be able to take a razor blade and cut the fiberglass that extends over the blue painters tape. The epoxy should be just cured enough that you can easily cut through it and then peel back the excess, leaving a nice clean cut lap right over your sharpie line.
After that cures according to the manufacturer's instructions, its time to flip the board over and do the exact same thing again. This time you will draw your sharpie line on the bottom of the board (on top of the fiberglass you just recently laid). Continue with the painters tape the same as last time, and this means that the edges will end up with two layers of cloth while the middle of the top and bottom will only have one. This is okay as the edges are often the ones under the most stress so its worth it to have some extra protection there. You should need about the same amount of epoxy as the first time, so mix up what you think is the right amount and then repeat the fiberglassing process for the top of the board.
The final step is optional but is often a good idea to make your board last as long as possible. Since the top of the board will most likely take more damage over the years (knees, heels, palms digging into it), lots of surfboards have a double layers of cloth on the top. This is very simple to do and you virtually just repeat the steps for fiberlgassing the top of the board, while being extra careful when cleaning up the edges of the fiberglass to leave a nice clean cut lap edge.
Step 4: Fin Boxes and Leash Plug
Since I had access to some Form 2 Resin 3D printers, I decided to design my own fin boxes and leash plugs, but you can easily buy these from any surfboard manufacturer and install them yourself. Whether you design your own or buy some, you need to take the outline of the parts and trace them on the board. I used a handheld router and a custom jig to cut out the holes.
Step 5: Sanding and Painting
After all of the fiberglassing, you will likely still feel the texture of the fiberglass cloth on the board. I liked the texture that this gave the board and the paint but you could skip to the next step of putting on a gloss coat and then come back to do the sanding and painting. Since I wanted the texture in the paint, my next step was the sand the whole board to get it ready for painting. The purpose of this is just to roughen up the surface and clean up any sharp edges so the paint adheres better. If you sand too much off you will actually end up sanding of parts of the cloth as well as the epoxy and this can lead to soft spots in the board where its more likely to crack. After all the cut lap edges and corners are sanded and the main portions of the board is sanded just slightly its time to paint.
For this part, there is not wrong answer to how you decorate and design your board but just make sure to only use water based paint on the board. If you use spray paint or oil based paint, the next layers of epoxy will not adhere correctly. I opted for just using plain white paint on the top to cover up the pink foam and dark blue paint on the bottom of the board. After the paint has dried, its a good idea to give it another quick sanding, again to make sure the surface is prepared for the next layer of epoxy.
Step 6: Gloss Coats
This is the final step, but is also one of the messiest. In this step, you also have the freedom to do as many gloss coats as you want. The more you do, the stronger and more durable your board will be, but it will also be heavier and more dense. I did one clear gloss coat and then one more gloss coats with different colors. For the clear gloss coat, I mixed the epoxy like before but instead of pouring it on the fiberglass cloth, I just poured it straight on the board and spread it out with cheap disposable paint brushes. Try to get the epoxy as smooth as possible and constantly work the edges to make sure not drips are forming. Depending on how you painted the board, this could be the end of your gloss coats.
If you want to use dyes to add color to your board, buy alcohol dyes and mix them in with the epoxy before your pour it on the board. I got three different shades of blue epoxy dye and then mixed 4 different buckets of epoxy (clear, light blue, blue, and dark blue). I then poured them out all at once darkest at the bottom to clearest at the top and then used multiple paint brushes to spread the different colors into one another at their borders.
Step 7: Final Sanding
Now your board is virtually done! Just a little bit of sanding to get it super smooth and your board will be ready for some real waves. I did some wet sanding with sandpaper with grits from 1000 to 3000. This is helpful to make the top gloss coat as clear as possible.
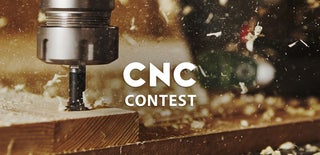
Participated in the
CNC Contest 2020