Introduction: Pixelated End Table
Have you ever thought of the best response to your friend's trash-talking? I'm talking full-on mental judo, the type of response that flips their insult completely on its head? Now imagine you're holding a cup of coffee in your hand that's preventing you from responding in a timely manner. We all know just how important response time is when you're talking trash, right?
Well, that's the situation I found myself in the other day when I decided to make this table. I looked around me and there was no good place to put my coffee down. In that moment I decided I had to spend the next 3 days building an end table to hold my coffee so my response time could be kept as low as possible.
Join me on my journey as I create what is quite possibly the world's most elaborate cupholder.
Step 1: The YouTube Video
I know many people prefer to read Instructable posts, but if you're more into video content then I've got you covered. Here's a link to this exact build in video form!
If you're in the majority of the people who prefer to read, then by all means, keep on scrolling. Let's start this build.
Step 2: Materials
As with any project, the first thing you're going to do is assemble all of your materials and admire their potential. They're about to go on a wild ride of transformation.
This is a pretty simple project in terms of the things you're going to need. You'll need about 30 board feet of a wood, or two, of your choice. I went with walnut and ash for that two-tone look, but feel free to use whatever wood you want! If you plan on mixing woods one thing you'll want to consider is that your wood should be of a similar density so that they expand and contract at similar rates when the seasons change.
Outside of that, you're going to need some wood glue, and a cheapy brush to apply it with, as well as a finish to seal the whole project when it's done. I used Saman Stains Hybrid Satin Floor Varnish, but there are tons of great finishes out there.
Step 3: Prepping the Wood
Job number one is going to be prepping all of that raw wood. Chances are if you're buying wood from a mill or a lumber store it's far from perfect. I used my jointer to completely flatten and square up two sides of my wood. Eliminating any twists, bows, and warping.
Once I had one face that I knew was flat I put the wood through my planer to flatten the opposite face. I also reduced the thickness of each board to exactly 1".
With 3 sides square and flat I headed over to my table saw and began ripping all of that wood into 1" wide strips, being careful to keep my square side against the fence. When I was done I had a number of long 1"x1" rectangular prisms made out of walnut and ash.
I then proceeded to cut those rectangular prisms to random lengths using my miter saw. The longest pieces were 9" and the smallest were 2".
Step 4: Building the Central Column
Ok, that's enough of breaking down the wood into smaller pieces, let's reverse course and start reassembling!
My plan for this project was loose at best. I figured the best thing to do would be to make a central 3"x3" column and then build the rest of the project off of that.
I started by gluing three 1x3 layers together. Each was approximately 24" long. Before the glue could have a chance to set up I immediately sandwiched all three layers together, forming the 3x3 central column. Imagine a big mac, replace the buns with wood, and the meat with wood glue, and you're pretty much there.
For the next 10 minutes, I experimented with different clamping techniques. Eventually, I found what worked best was to cut 3" long blocks and clamp those to the outside of the column, alternating between top and bottom and left and right, to keep everything held together tightly.
Step 5: Cleaning Up the Central Column
Once the glue had dried I spent a bit of time cleaning up the central column. I put it through my thickness sander to remove any excess glue stuck to the outside and make sure it was exactly 3" x 3".
Then using my miter saw, I cut the ends off to square them off. I made the central column 23" high/long, which, not coincidentally, is the final height of the table.
Step 6: Building Out the Bottom and Top (First Attempt)
With the central structure done it was time to start building out the top or was it the bottom? I guess it doesn't really matter since the whole piece is reversible.
My initial plan of action was to build off of the central column by gluing concentric layers to it. I laid out my next two layers, applied glue to them and attempted to glue them in place. That turned out to be a bit of a mistake. By the time I was reading to clamp everything together the glue had started to set up before, it made it impossible to get everything perfectly aligned. Luckily I was close enough that it didn't ruin the project, but I definitely needed to adjust my strategy going forward.
I even added a bit of water to my wood glue to extend the drying time, but it still wasn't enough.
Step 7: Error Correction
Using a little plane and my random orbital sander I corrected some of the mistakes from the last step and brought the piece back into square. I had to be careful not to remove too much material otherwise I'd ruin the project in a completely different way, so I just focused on removing high spots and frequently checked my measurements.
There was a moment where I thought I was going to have to start all over again, and, needless to say, I was pretty bummed out. Luckily the damage wasn't too bad and I was still able to press forward.
Step 8: Building Out the Bottom and Top (Slightly Modified)
Going forward I slowed my roll a bit and only expanded by 1 layer at a time. This kept the working time more manageable and ensured that I was able to get a tighter fit on every layer, making for a much cleaner end product.
Layout the row, apply glue, attach to the central column, clamp in place and let the glue dry. Rinse and repeat until I had an 11x11 grid of ash and walnut on the top and bottom.
Step 9: Error Correction Round 2
Unfortunately, another slight problem reared its ugly head as I removed the clamps from the final layer.
I did my best to make sure each individual block of wood was pushed right down to the surface of the table before I applied the clamps, but, evidently I missed a couple. This meant I had a couple of low spots on both the walnut and the ash sides. Trying to sand the top and bottom until they were flush with these low spots probably would've taken the better part of a year (seriously, end grain is tough, trust me). So that was out of the question.
Time to build a router sled.
I started by leveling the end table using shims and then clamped it in position. Next, I clamped 2 plywood rails approximately 1/2" above the surface of the table. I made sure both rails were perfectly level and flush to one another. Then I built a long sled that held my router and placed it onto the rails.
Using a cutting bit on my router I slowly cut away at the end grain until I had a perfectly flat top with no low spots. I then flipped the whole end table over and repeated the process on the other side (except I didn't have to shim it to keep it level this time).
True, this was a lot of extra work, but I had planned on building a router sled for some time, so this was actually a good excuse to do that.
Step 10: Error Correcting the Error Correcting
The router worked great for flattening the top and bottom, but unfortunately, it came with its own cost. Namely, blow out.
I should've clamped a sacrificial board to all 4 sides of the top instead of just 2, and as a result, I had some blow out on the unsupported edges. Not to worry though, I had was planning on rounding over the top and bottom of the project anyways.
I threw a 1/4" round-over bit on my trim router and got to work. This eliminated about 95% of the blowout. Wood filler took care of the rest.
Step 11: Sanding
Onto the sanding! Oh, the sanding.
I know its basically an established trope at this point that everyone hates sanding, but this project was particularly bad. I spent a long time sanding the end grain on both the top and bottom. Even using 40 grit sanding pads I had to spend 4 or 5 hours sanding away until I got the results I was looking for. I followed up the 40 grit with 180 grit in preparation for the finish.
With so many tight corners and hard to reach crevices on the interior section I had no hope of using any type of power sander, so I plugged away at it using my little sanding sponge.
Step 12: Branding
As a no name internet blogger my number 1 fear is that someone will rip off my designs (just to be explicitly clear: that's sarcasm) As a result I like to include my authenticity brand on all of my projects haha.
Seriously though, I like to brand all of my projects, it's a simple and easy way to add a unique mark to my projects without being too heavy-handed. It's also super satisfying to do. While I was sanding I started heating up my electric branding iron. Once it got hot enough I took a second to burn my logo and signature into the ash side of the table.
Step 13: Applying the Finish
Homestretch!
Applying the finish to this project was possibly the most straight forward part about it. I loaded up my brush with my favorite clear coat and started brushing it on. I used a bigger 3" brush to apply it to the top and open faces on the sides, and then switched to a smaller 1" brush to do all of the smaller details in the middle.
I did 3 coats on the high wear areas and 2 coats on the interior, sanding lightly with the 180 grit sanding block between each coat for maximum smoothness.
Step 14: Testing
Obviously, all of my projects undergo rigorous testing before I put them into service. The most important of these tests is whether or not a project can support the weight of its creator. I'm happy to report that this little table passed the test. Wood glue is a crazy thing.
Step 15: Enjoy It
With all of the testing and building out of the way the only thing left to do is to sit back and enjoy it. I set it up in my living room right next to my favorite armchair and now I have somewhere to rest my coffee in the morning while I talk trash to my friends online.
Hope you enjoyed this build! If you have any questions or comments please drop them below and I'll do my best to get all of them!
Also, if you like this build. Consider checking out some of my other builds on Instagram (@ZacBuilds) and YouTube (YouTube.com/ZacBuilds) Thanks!
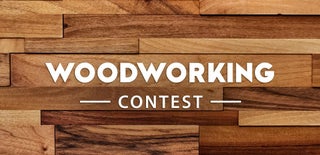
Grand Prize in the
Woodworking Contest