Introduction: Planetary Gear
Intro – planetary gears also refer as epicyclic gearing consisting three elements sun gear, planet gear and ring gear. Sun gear is located at the center that transmits torque to planet gears orbiting around the sun gear. Both systems are located inside the ring gear. In the toothed formation sun and planet gears are externally mesh and ring gear internally meshes. (See Fig. 01)Fig. 01
Planetary gear is found in many variation and arrangements to meet a broad range of speed-ratio in the deign requirements. Planetary gear system is use in varies applications such as, clocks, lunar calendar, car mirror, toys, gearhead motor, turbine engine and many more.
For detail understanding on the planetary gear: http://en.wikipedia.org/wiki/Epicyclic_gearing Planetary Gear Design
Planetary gear system will no assemble unless the number of teeth in each gear is selected properly.
Planetary spur gear drive ratio 5:1 means the sun gear must make 5 revolutions for each revolution of the output carrier.
Desired number of teeth in the sun gear is 24.
Design requirements:
Ratio = 5:1
Sun gear = 24
Module = 1
Since, I am working in the metric unit every dimension will be in mm. Selecting gears in metric unit the gear tooth profile of the spur gear will be in Module.
M = Module
N = Number of teeth
Nr = Number of teeth on the ring gear
Pd= Pitch Diameter
R = Ratio
PDs=N/M=24/1=24mm Eq. 01
Pitch diameter of the sun gear is 24.
Calculate the number if teeth required in the ring gear for the ratio 5:1.
R=1+Nr/Pd Eq. 02
Solve for Nr
Nr=Pd (R-1)=24(5-1)=24(4)=96 teeth
Pitch diameter of the ring gear with 96 teeth and 1 module is.
Pd=Nr/M Eq. 03 Pd=96/1=96mm
Pitch diameter of the planet gears must be found from.
PDp=(Nr-PDs)/2=(96-24)/2=72/2=36mm
Number of teeth in the planet gears may now be found from.
PDp=N/M Eq. 04 36mm=N/1 36mm (1)=N N =36 teeth
Check:
R=1+Nr/P_D =1+96/24=1+4=5
The ratio is 5:1, as design was required.
Planetary gear is found in many variation and arrangements to meet a broad range of speed-ratio in the deign requirements. Planetary gear system is use in varies applications such as, clocks, lunar calendar, car mirror, toys, gearhead motor, turbine engine and many more.
For detail understanding on the planetary gear: http://en.wikipedia.org/wiki/Epicyclic_gearing Planetary Gear Design
Planetary gear system will no assemble unless the number of teeth in each gear is selected properly.
Planetary spur gear drive ratio 5:1 means the sun gear must make 5 revolutions for each revolution of the output carrier.
Desired number of teeth in the sun gear is 24.
Design requirements:
Ratio = 5:1
Sun gear = 24
Module = 1
Since, I am working in the metric unit every dimension will be in mm. Selecting gears in metric unit the gear tooth profile of the spur gear will be in Module.
M = Module
N = Number of teeth
Nr = Number of teeth on the ring gear
Pd= Pitch Diameter
R = Ratio
PDs=N/M=24/1=24mm Eq. 01
Pitch diameter of the sun gear is 24.
Calculate the number if teeth required in the ring gear for the ratio 5:1.
R=1+Nr/Pd Eq. 02
Solve for Nr
Nr=Pd (R-1)=24(5-1)=24(4)=96 teeth
Pitch diameter of the ring gear with 96 teeth and 1 module is.
Pd=Nr/M Eq. 03 Pd=96/1=96mm
Pitch diameter of the planet gears must be found from.
PDp=(Nr-PDs)/2=(96-24)/2=72/2=36mm
Number of teeth in the planet gears may now be found from.
PDp=N/M Eq. 04 36mm=N/1 36mm (1)=N N =36 teeth
Check:
R=1+Nr/P_D =1+96/24=1+4=5
The ratio is 5:1, as design was required.
Attachments
Step 1: Conceptual Phase
Conceptual Phase
Compute simple calculation for the center distance or mounting distance.
Ring gear = 96 teeth
Planet gear = 36 teeth
Sun gear = 24 teeth
Compute simple calculation for the center distance or mounting distance.
Ring gear = 96 teeth
Planet gear = 36 teeth
Sun gear = 24 teeth
Step 2: Components Selection
Sun Gear - A 1Z 2MYZ1002408
Step 3: Planet Gears
Planet Gears 3 x Planet Gear - A 1P 2MYH10036
Step 4: Ring Gear
Ring Gear - 1 x Ring Gear - A 1C10MYK10096
Step 5: Assembly
Assembly
- Gear assembly
- Gear assembly
Step 6: CAD Model
Using CAD software assemble planetary gear system for the prototype.
Step 7: Prototype
Step 8: Return of the Planetary Gear
Sound from the deep space. Please disregard the motor sound.
Attachments
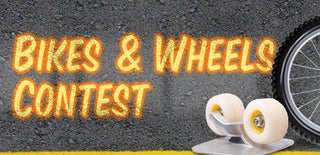
Participated in the
Bikes and Wheels Contest