Introduction: Plywood Bundt Pan Banjo (Bundt-Jo)
This was a strange little project I pulled together: I wanted to make an instrument that used a bundt cake pan as a resonator. The body is made of layered plywood, and the neck is made of maple (mostly to give it extra strength and keep the whole thing from collapsing in on itself!).
The "Bundtjo" has a pretty unique tone, somewhere between a resonator guitar and an actual banjo. The body cavity isn't very large, so it's not the loudest, but its got chutzpah, and that's all that matters.
Supplies
Lumber:
- Birch plywood for body
- Poplar blocks for anchoring tailpiece
- 3/4" Maple for neck, and also a small piece for a bridge
Not Lumber:
- Bundt Cake Pan for resonator
- Turnbuckle and screw hooks for tailpiece
- Tuning machines, fretwire, and strings for ... well, making music
There weren't too many specialty tools or parts needed for this project. Power tools were mainly a router (as well as a jig for cutting circles and a jig to use the router as a "mini-planer"), table saw, and scroll saw. Hand tools consisted of a hammer, files and a spokeshave, along with some wire cutters for the fretwork. Tuning machines and fretwire were from stewmac.com, and the tailpiece was a fairly heavy-duty turnbuckle from home depot.
Step 1: Cut Body Layers
As a starting point, the plywood will need to be cut to fit the bundt pan. Measure the radius of pan just below its lip.
Using a basic circle-cutting jig for a router, set the cutting radius first for the outside body radius (I used ~1", so the outside radius would be the pan's radius plus 1 inch). Cut the outside circle, then reset the jig for the inside radius, which should match the radius you measured from the pan.
The first layer will be a complete circle, but the rest will be shaped like cartoonish magnifying glasses. By leaving this rectangle of wood on the layers, you're forming the neck block, which will be used to glue the neck to later on. The dimensions of the neck block should be roughly 2" x 4."
There should be enough layers so that the bundt pan does not extend past the plywood. Once you've reached this point, cut a circle of plywood to match the outside radius. This will end up being the back of the banjo.
Step 2: Glue Body
Using as many clamps as you can, start gluing up the layers that you've cut out. Titebond 2 seemed like a good glue for the job. Make sure that the neck block pieces all line up, and make sure that the sides are as even as possible. Some wobbliness is ok, but the neater you are, the less cleanup you'll have to do later. The ring without the neck block should be on top, and the back should be ... on the back.
I found that it also helped to glue together only a few layers at a time. The layers didn't slide around nearly as much that way.
Once you get all the layers glued together, start sanding the outside of the rings. Make sure that the body has a smooth, even surface. Cleaning up the neck block isn't as important at this point, but we'll get to that later.
Step 3: Glue Tailpiece
I probably over-complicated this part, but I was afraid that a single pressure point for the tailpiece would create too much stress. By anchoring the tailpiece at two locations, I think I distributed the load a little bit better.
Cut two pieces of poplar to match the depth of the body. The next step is to shape the inside of these blocks so that they'll match up for a solid glue-up.
Put a piece of rough sandpaper on the body of the banjo, and sand the blocks so that the inside of each one matches the curvature of the body. The better the pieces match up, the better the glue will hold.
Glue and clamp the blocks to the body, keeping them symmetric with respect to the neck block.
Once the glue has dried, drill pilot holes for the screw hooks. Screw in the screw hooks, and then attach and tighten the turnbuckle.
Step 4: Start Making the Neck
I cut out the rough shape for the banjo neck using a table saw, making sure to stop before I cut the headstock off. The banjo I made was a 5-string, which has a high drone string and which complicates the neck shape a little bit.
The important part here is that you need to determine the scale length (the distance from the nut to the bridge) of the instrument you'll be making, make a pattern for your fingerboard, and make sure that the bridge is at the exact center of the bundt pan. On a normal banjo, you'd be able to move your neck to adjust the intonation of the instrument, but here, there's only one place that the bridge can go. FretFind2D (https://acspike.github.io/FretFind2D/src/fretfind.html) is a wonderful resource, where you can put in the dimensions of your fretboard and print out a pattern to follow.
I made a jig for my router that basically turned it into a tiny planer, just by setting it on a little platform. (Alternately, you could use a hand plane.) I used this jig to get a fretboard to a consistent thickness. Using the same jig, I reduced the thickness of the headstock to fit the tuners (about 0.5").
Once I got the thickness right, I cut out the pattern for the neck using a scroll saw, but you could do the same with a coping saw or something similar.
At this point, you can see things start coming together. In the last picture in this step, I have a test bridge I was messing around with. It's not what I ended up using just because it's too heavy and tall. Live and learn.
Step 5: Sawing and Gluing Fretboard
I took the pattern from FretFind2D and transferred it to the fretboard. Using a small miter box I made with some scrap wood, I precisely cut the slots for the frets.
Once the frets were glued (again, with TiteBond 2), I used a long (really long!) rubber band to glue the fretboard to the neck. Using the rubber band instead of clamps distributes the pressure and helps to center the fretboard on the neck.
After the fretboard is glued to the neck, I used a block plane to remove the overlap. You can do the same with a file or a sanding block.
Step 6: Shaping the Neck
Turn the neck so that it's facing downward, and clamp it or use a vice to hold it in place by the end. Draw a centerline down the length of the neck.
Using a flat file or rasp, shape the neck at the ends (and at the transition point in the middle, if you have a higher fifth string like I did). When you're shaping the neck here, be sure not to cross the centerline that you've drawn, or else you risk having a neck that's not symmetric.
Once you're happy with the curvature that you've filed, you'll want to shape the neck with a spokeshave. Use the spokeshave to extend the curvature between the filed-in areas. Again, be sure not to cross the centerline that you've drawn.
Once you've finished with the spokeshave, use a strip of sandpaper to smooth out the curvature and remove tool marks. You'll want to use a "shoeshine" type motion here as you move down the length of the neck.
Step 7: Drilling for Hardware and Hammering Frets
I got my hardware from stewmac.com, but there are a lot of places you can use. Once you have your tuning pegs, transfer the pattern for the pegs to the headstock and drill out the holes. Also drill your pilot holes for the screws that hold the tuning pegs in place.
If you have a 5th string, also drill the hole for that tuning peg. There are a lot of varieties of 5th string tuning pegs (some friction fit, some pressed in place, etc), so follow the instructions for the specific hardware that you have.
Gently (but firmly) hammer in your frets with a non-marring hammer (something with a nylon head is good, but in a worst-case scenario, you could use a wooden shim as a sort of caul to protect the frets as you hammer them in. You can also use a small dab of thin superglue to make sure that there's a firm grip for each of the frets. I used painter's tape to protect the fretboard during this step. After you hammer in each fret, use a wire cutter to snip the frets close to the fretboard. Note that I left the higher frets missing for now, so that I had a flat block of wood to work with as I glued the neck to the body (in the next step).
To get rid of the sharp ends on each of the frets, I sawed a 45 degree angle in a block of wood and wedged a metal file in it. I used this to file the fret ends to a consistent angle and get everything flush with the sides of the neck.
Step 8: Gluing the Neck
In the first picture in this set, you can see that in order for the strings to clear the center of the bundt pan, the neck has to be set at an angle. I used a handsaw to cut a wedge that sets that angle for the neck. Once I smoothed the wedge flat, I glued it to the neck.
Positioning of the neck is very important - the neck must stay aligned with the bridge and tailpiece, and should be centered on the neck block. To keep the neck from moving around as I glued it up, I snipped the pointy bits from a thumbtack and stuck them into the wood. They were sharp enough that they sank completely into the wood when everything was clamped up, and didn't interfere with the glue at all.
Using the TiteBond 2 again, I glued the neck to the neck block on the body.
Step 9: Cleanup and Final Touches
Using files and lots of sandpaper, I cleaned up the neck block. The plywood actually looked really nice after the edges were evened out and the glue was all sanded away.
Some final steps here: I glued in the nut (again from stewmac.com, but you can use a piece of hard wood here, or even a bolt if you're going for a "Cigar Box Guitar" sort of feel) and I attached the tuning machines. You might notice that the tuning machines are upside down - my headstock design looked nice, but didn't leave any room for the hardware! Again, live and learn...
This is also when I installed the last of the frets, since the neck was glued in place.
Finally, you'll need a bridge. I used a small triangular piece of maple, set on the center post of the bundt pan.
Step 10: The Final Product!
All in all, it turned out to be a pretty good project! I've been thinking of improvements or next steps:
- There's currently no finish on the instrument. At the very least, I'll probably put some mineral oil and beeswax, just to provide some minor protection.
- I'm interested to find out if additional holes in the bundt pan would increase the volume, or at least change the tone in some way. At some point, I'll probably get a second bundt pan to experiment with.
- I'm not sure if the turnbuckle is the best approach to the tailpiece. The strings put tension on it in a way it wasn't designed for, but it seems to be holding up pretty well for now. It's also probably not best to have the metal strings rubbing directly on the metal turnbuckle, but there haven't been too many broken strings (yet).
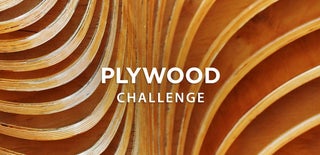
Participated in the
Plywood Challenge