Introduction: Plywood & Fiberglass Drop Through Longboard
A little over two years ago I got the idea to make my wife her own longboard. The story starts with us finding romance and love in longboarding together; the only problem was that I only had one board. I would have bought her one, but #1 - I like making stuff and #2 I knew she would have the most fun on a board that had a custom flex built just for her. The board that I made for my wife turned out very well and eventually I decided to make one for myself.
The inspiration for how I decided to make longboards came from watching many videos and reading up on how they are made. The design and procedures I settled on are the result of eliminating costs and difficult procedures, while still maintaining the quality of the finished product. It has taken me quite a bit of time and effort to figure out the best way to make two longboards as a small hobbyist. I hope that my methods are of help and inspiration to you. There are definitely simpler and easier ways to make a "longboard", but if you want to make a longboard that performs just as well as one you can buy, this Instructable is for you.
Step 1: What I Used
Supplies:
(2) 3/4 x 10" x 45" Boards for top and bottom plates of press
(9) 2" x 8" x 10" Boards for the blocking of the press
(1) 1/8" x 30" x 48" Baltic Birch plywood cut to make three layers for board lay-up - https://www.woodcraft.com/products/baltic-birch-p...
(1-2) 10" x 48" Pieces of BiAxiel Fiberglass cloth - http://www.fiberglasssite.com/biaxial-mat-1700-30...
(54) 1.25" Screws to attach the blocking to the plates
(1) Plastic putty knife to spread epoxy
(1) Epoxy/Paint mixing cup
(1) Mineral Spirits for cleaning up epoxy
(1) Quart of Entropy Super Sap CPM Epoxy resin - https://www.jamestowndistributors.com/userportal/...
(1) 16oz. of Entropy Super Sap CPS slow hardener - https://www.jamestowndistributors.com/userportal/...
(1) Roll of painters tape for taping your design
(1) Black spray paint
(1) Clear spray paint finish
(1) 3' long 1/2" steel square tube for bumpers
(4) Size 4 3/8" screws to attach the bumpers.
(1) Tube of clear silicone adhesive.
(1) Solder for metal
(1) Set of Caliber II longboard Trucks
(1) Set of 8 Bones Red Bearings
(1) Set of 4 Arbor Outlook longboard wheels
(2) 1/8" longboard truck risers
(8) 1.25" black longboard truck hardware
(1) Set of Skateboard wheel speed kit hardware
(1) Sheet of black diamond longboard griptape
Tools:
Jigsaw - https://www.amazon.com/Bosch-120-Volt-Variable-To...
Jigsaw Blades - https://www.amazon.com/Bosch-10-Piece-Assorted-T-...
Random Orbital Sander - https://www.amazon.com/Bosch-Random-Polisher-ROS2...
Sanding discs - https://www.amazon.com/Diablo-DCD050120H04G-120-G...
Dill and Impact set - https://www.amazon.com/Bosch-CLPK22-120-Lithium-I...
Drill bits - https://www.amazon.com/dp/B0000683DM/ref=sxr_rr_x...
Dremel Tool - https://www.amazon.com/Dremel-4000-4-Performance-...
X-acto knife - https://www.amazon.com/X-Acto-XZ3601-X-ACTO-Knife...
Cutting mat - https://www.amazon.com/SE-CMG1219-Self-Healing-Do...
Paint Finish sandpaper - https://www.amazon.com/3M-25320P-G-Advanced-Sandp...
(6) Pipe clamp ends - https://www.amazon.com/Bessey-BPC-H12-2-Inch-Styl...
(6) Pipe for pipe clamps - https://www.amazon.com/Everflow-Supplies-PCBL1248... To be honest its cheaper to get this item at your local hardware store.
Torch head for soldering - https://www.amazon.com/BernzOmatic-Basic-UL2317-P...
Propane fuel cylinder - https://www.amazon.com/Standard-Propane-Fuel-Cyli...
Step 2: Building the Press
For my longboard press I cut two 3/4" plywood sheets to 10" x 45". These two sheets are a little bit wider and longer than the board that I was making.
Next I took a 2x8 and cut it into 10" long sections. These sections of 2x8 will be used to make the blocking of the press, which presses the board into its shape.
To determined how much concave curve I wanted the board to have across the board, I simply measured the concave curve of an Arbor longboard that I have. Match that curve on one of the 2x8 sections, but be sure to add a little bit more curve than you want the board to have. The reason for this is that the board will flatten out a little when you pull it out of the press.
The next step is to build the lengthwise camber into the press. To do this I started by attaching the center block of the press onto the bottom plate of the press. Then each pair of blocking outward from the center block was reduced in height relative to the one inward of it. After you create your desired amount of camber in the press, match the blocking of the top plate to that of the bottom plate. The top and bottom blocking does not have to match up perfectly, but it should be close.
Step 3: Board Layup & Pressing the Board
I took a piece of 1/8" Baltic Birch plywood and cut it into three pieces 10" wide by 48" long. These pieces will make up the three layers of the board. Next I cut one piece of biaxial fiberglass 10" wide by 48" long with the strands of the fiberglass running parallel and perpendicular to the board. I weigh 150 lbs and I really liked the playful flex of the board with a single piece of fiberglass. If you like a stiffer board or weigh more I would add another piece of fiberglass to your layup. If you run a second sheet of fiberglass in the board I would cut it so the strands run at 45° to the length of the board, or in an "X" pattern.
Now for the layup! Do this on cardboard or somewhere that isn't important because epoxy is very hard to remove. First measure out your epoxy to make sure you have enough. You shouldn't need to use more than 1/4 liter mixed. Make sure to mix the epoxy very thoroughly for six minutes. The layup should go from bottom to top as follows, plywood - fiberglass - plywood - plywood. If you use two pieces of fiberglass, I would place the second piece between the two top pieces of plywood of the layup. As you wet the pieces of fiberglass and plywood during layup, make sure you get all of the fiberglass wetted with epoxy. With a slow epoxy hardener you have 50 minutes of work time so there is no need to rush the lay-up.
After completing these steps, I wrapped the board in Saran wrap to keep epoxy from dripping all over the press. Before I put the board into the press, I cut two pieces of corrugated cardboard to the width and length of the press. This cardboard is placed above and below the board to keep the press from gouging the longboard. Finally, I tightly clamped the two sides of the press with pipe clamps and let the board sit for 24 hours.
Step 4: Wrong Fiberglass
When I laid up my board I put two pieces of fiberglass in my board. However, when I went to test it I couldn't tell that it was any stiffer than my wife's board which has one piece of fiberglass in it. The reason my board wasn't any stiffer was that I had used the wrong kind of fiberglass. I used woven fiberglass cloth instead of biaxial fiberglass.
Be sure to use Bi-Axiel Fiberglass! I know it is a little expensive and it is easier to get the cheap automotive woven fiberglass cloth at your local hardware store. However, cheap automotive fiberglass will not make your longboard any stiffer. I made the mistake of using the cheaper fiberglass in my board and ended up having to add a layer of biaxial fiberglass to the top of my board to make it stiff enough.
Step 5: Cutting and Shaping the Board
To cut out the shape of my longboard, I made a stencil based off of another board that I own. Then I cut the board out with a jigsaw. Alternatively, you could use a band saw to cut out your board.
Once the board is roughly cut to shape, I used a sander to even everything out and make it smooth. I originally rounded the edges of my board with my sander (I didn't have a router which would have been much easier) which worked perfectly fine, though tricky to execute. When sanding the board, I started with 80 grit sandpaper and then finished with 220 grit. I shaped the dropouts with a sanding drum on my Dremel tool.
Step 6: Fixing the Wheel Bite
After testing the board, I found that it had wheel bite issues. Wheel bite is when a wheel rubs against the side of the board from a hard turn or sketchy landing. The wheel "bites" the board, which causes the board to instantly stop, throwing the rider off. To correct this, I redesigned the shape of the board, which meant I had to go back and re-cut it. Instead of the board having rounded edges and curved ends, I cut the board into a coffin style (angular) shape to eliminate wheel bite. This effectively eliminated the wheel bite and gave the board a unique look, which I quite like.
Step 7: The Graphic
For the graphic on my board I chose to base it off of the constellation Scorpius. I mapped out the graphic on the board and then used craft google eyes and diamond studs to mark the position of each star. For the lines connecting each star I used a cutting mat, X-acto knife, and ruler to cut thin strips of painters tape. This worked quite well.
After the graphic is all taped, make sure that all the tape is sticking to the board. If the tape doesn't stick correctly, you will experience overspray sneaking under the tape.
I like to paint boards so that half of the edge of the board is the color of the graphic and the other half is plain wood. I think that it makes the graphic look more professional. To do this, tape the whole edge of the board and then run a razor blade down the center of the edge. Peel off the tape on the bottom half of the edge. This will give you a clean paint line around the edge of the entire board.
I painted the board with three or four coats of paint. As always, it is better to do many light coats of paint than a couple thick coats.
It is best to remove the stencil/painter's tape when the paint is still wet, but since it would've been easy to smudge the paint trying to remove the little lines of tape, I waited for the paint to dry. If the paint wants to lift off as you peel off the stencil, use a razor blade to cut the paint attached to the stencil. I did have a few runs under the "stars" and lines, but they were easily cleaned up using a knife.
To add a little bit more protection to the graphic, I sprayed two coats of clear Rustoleum spray paint finish on the board. My thought was that this finish would seal the board from water and possible damage. However, after using the board for a few months, I wish I wouldn't have used the Rustoleum clear finish. The clear finish has chipped wherever a little stone has hit the board and has not proven to be durable. I would recommend using an outdoor water based polyurethane which I used on my wife's board and it still looks amazing.
Step 8: Grip Tape
Once the graphic is finished, make sure the top of the board is smooth and free of dust. You are then ready to put the grip tape on. So to be honest, I was so excited to finish my longboard that I forgot to take any video or pictures of how to put grip tape on. I am still learning how to apply grip tape perfectly so here is the video that I learned from and found very helpful.
Step 9: Making the Metal Bumpers
To add some durability against curb strikes and whatever my board may run into, I made protective, metal bumpers for the ends.
I used 1/2" steel square pipe to make the bumpers. First, I cut off one side of the square with my Dremel tool to make it into a U-channel. Once I had the U-channel, I cut two triangles into the sides to allow the metal to bend to the appropriate angles to fit the ends of the longboard. Once i had everything cut and bent to the right angles, I soldered the corners of the bends together. I finished by sanding everything until it was smooth and shiny.
Step 10: Attaching the Bumpers
I had to carefully cut the griptape and sand down the ends of the board with my Dremel so that it was thin enough for the inside of the 1/2 in steel channel to fit over. Once the bumper fit onto the board correctly, I used a black marker to color the part of the board I had sanded to fit the bumpers. The black marker helped to hide any imperfections with fitting the bumpers perfectly to the griptape.
I used two screws through the top of the bumpers to attach the bumpers to the board. To keep the screws flush with the top of the bumpers, I countersunk the holes for the screws. I also pre-drilled the holes for the screws in the board since the screws were going into the board near the edge and I didn't want it to split.
Before attaching the bumpers to the ends of the board, I ran a bead of clear silicone adhesive inside the bumpers. The silicone is to fill in the gaps where I failed to match the end of the longboard to the inside of the bumpers and keep them from rattling. Screw the bumpers down and your done!
Step 11: That's It!
Just add your trucks, wheels, and go have fun! I love how my board turned out and is by far my favorite longboard to ride! It is quite flexible and has a very smooth and surfy feel. It rides quite similar to a flexible pintail, but in the shape of a drop-through board.
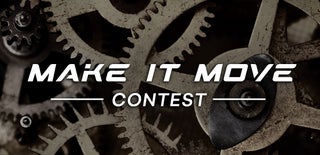
Runner Up in the
Make it Move Contest