Introduction: Plywood Icosahedron
Shown decorated as one typically would. Presented here for your viewing pleasure is a wooden icosahedron in D20 formation.
Made from 1/2 inch plywood. Glued and sealed. This one is made to be used!
UPDATE(Feb 25, 2019): Included here is a 100mm per side blade angle template that you can 3D print to help you with setting up the blade of your cutting tool. This works by placing the face against the solid surface of the saw and angling the blade along the side towards the cut off section of the pyramid shape
Attachments
Step 1: Why?
I had recently rebuilt a discarded cast iron table saw. This thing was an absolute tragedy... I'm certain that the previous owner had actually used it to cut ceramic tiles. There it sat waiting for trash pick up, all rusted and abused. More importantly, It was all there, only the belt guard was missing.
A complete disassembly, 2 new spindle bearings, 2hp motor rebuild and I even had to remove paint, concrete and construction adhesive from every surface.
New switch, complete rewire and lots and lots of hand sanding to remove the rust.
I proceeded to build a rolling station for it and it is going to be a long road to get it back to great condition but that will have to wait. I really wanted to test it out by making something amazing.
If you are wondering, General 50-185M1, weighs over 300 pounds, Has an American made motor and extra long fence and rails.
Step 2: Devise a Plan... and Execute!
I wanted to try making a complex shape requiring lots of repeated angle cuts. That would be quite an adventure...
One critical hit later and the idea was born, a 20 sided die!
A cursory internet search shows the angle cuts needed so using precise angle measurements on an imprecise tool, the cutting began.
20 sides meant 20 equilateral triangles. I wanted about 6 inches per side. that means that I would need wood strips about 5.2 inches wide. I chose 1/2 inch construction plywood since I would be covering it with paint in the end.
I built a T stand from some scrap lumber and clamped my miter fence to it, tail side up.
Using a digital angle finder thingy I zeroed the reading to the base then made the slot guide read 0 as well, this was clamped in place then the Miter fence was set to 30 degrees and locked in place.
Using a backing piece I made the first cut all the way along the side of the strip. Flipped it over and aligned the point to the cut off miter wood then cut out the last side of the triangle.
The cut triangle was close enough so I cut up lots of triangles, I needed 20 but ended up with over 40.
Step 3: Make the Sides Fit.
The side pieces need to have an an angle cut from the mating faces in order to have a seamless fit from one face to another. My saw has the demonstrated the capability of delivering this precision but my measuring device does not. In the end I set my blade angle to 20.9 degrees and hoped for the best.
I test cut 5 pieces the hard way and glued them together with cyano type adhesive.
The finished form looked about right so I built a small jig as shown from off cuts of the triangle cutting to hold the triangles firmly and safely while cutting the edge angles along the saw fence.
Step 4: Dealing With Construction Grade
This type of ply has a bad finish at the best of times. I had to fill and sand every piece to get a semi usable surface. Wood filler used liberally and 150 grit on the belt sander made quick work of the individual pieces.
Step 5: Tape and Glue
I love painter's tape for clamping odd pieces. I placed 5 sections together wide side up and taped the edges together then flipped the sections over. White glue was used in the cavities created by taping and the pieces were folded up one at a time until the last side meets the first. Glue is used there as well and tape is used to hold.
Working quickly I made 3 more, Yes I know they will not fit together like this but I wasn't thinking that far ahead when I was doing this step.
Next I glued 2 of the forms together then has to add a couple of individual sections before the third completed shape was added. I then continued with individual pieces until the last one was glued, placed and taped to complete the shape.
The last piece fit rather well which tells me the angle were all cut relatively equal and within tolerance.
Step 6: Fill and Sand
With the tape removed it is easy to see there is some gaps and imperfections that need to be filled. More wood filler was used.
Once dry the entire structure was sanded with 150 grit paper and the edges were softened by sanding off the seam angles. I think I makes the entire shape more aesthetically pleasing.
Again more filler and more sanding is needed.
At this point I used a spray primer to coat the entire surface before final fill. This makes all the imperfections show up.
The final fill is a light weight wall filler which I used previously to finish the surfaces of my giant Rubiks' Cube.
This was sanded once dry and every surface was primed again before the final coat.
Step 7: Final Coat
Paint and you are done!
Well sort of...
Not all the sides could be painted at once running the risk of rough bubbly looking over-spray from the sputtering spray can.
At this point I chose to make a painting stand to get the remaining sides at the bottom.
I used one of the unused sides to draw an outline of one side on a scrap piece of wood. # holes were drilled with a 1/8 inch bit about a half an inch in from the points. Small nails were pushed through the wood.
The wood with nails is used to support one painted side while the others are being painted. This leaves the least amount of contact with the not dry paint.
Step 8: Numbers
I thought of routing numbers into the sides to make the 20 sided die but in the end I went with stencils and white paint.
I have a Dymo label printer and as it turns out printing a single number bold with "auto fit" on its side to a large shipping label (30323) is the exact size that I needed. Since these labels don't really stick to well they are perfect to make stencils from. Just print and cut out with a razor knife.
The stickers were adhered to the faces using standard arrangement from a google image search. all the remaining green was covered with painter's tape and the letters were sprayed gloss white as a nice contrast to the green that I used for the structure.
Once dry the masking layer was removed to reveal the die.
Now on to make the others for back yard adventuring.
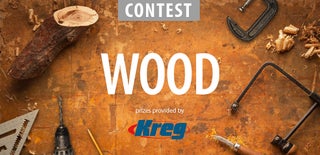
Runner Up in the
Wood Contest 2016