Introduction: Poor Man's 3D Printer
My goal was to build a cheap and inexpensive 3D Printer for less than 100 Dollar/Euro
What are the features of the Poor Man's 3D Printer ?
- Fused deposition modeling ABS/PLA
- Heat bed
- use of open source firmware, modified version of Tonokip
- free host software, Repetier-Host
- bowden-extruder
- max. build size 40mm x 40mm x 40mm
- resolution 0.08mm
Step 1: Parts
Parts i bought:
- Arduino Board Mega 2560 (on ebay from china): 10 Euro
- 2 pcs. Stackable Motor Driver Shield L293D 6 Euro
- Hotend MK7 MK8 noozle 0,4mm+thermistor+cartridge 20 Euro
- PTFE Tube 4 x 2mm & 2 pcs. 1/8" BSP 6 Euro
- Fan 30mm x 30mm 2 Euro
- MOSFETs,resistors,caps,LEDs,thermistor 5 Euro
Recyled PC/printer part:
- 4 pcs. DVD/Blu-ray drives, with stepper motors ! old cd drives can't be used because they work with dc-motors
- old PC power supply, 12V/5A and 5V/2A are required
- stepper motor nema17-like from old printer for extruder
- i use a modified gear (see pictures) from an old hp printer for the bowden-extruder, optional you could get an airtripper extruder for about 25 Euro
Things that every hobbyist has in his garage :-)
- many screws, nuts and washers M3,M4,M5
- lots of wires
- aluminium-sheet for the frame, you can also use wood
- some alu/metal profiles, see pictures
Step 2: Pictures From Building the Chassis
Step 3: Endstops
use endstops from dvd drive !
Step 4: Counterweights
I had to made counterweights for the z-axis because the x- dvd drive + Hotend are too heavy for the small steppers
The counterweight is simply connected through a cord and a pulley with the drive.
The weight of one counterweight = weight of (x drive + hotend) /2
Step 5: Extruder
The Extruder was build of a gear of an old hp printer deskjet 300. I remove the original stepper (too weak) and
replace it with a bigger one, i find two of them in an epson stylus color 600.
The shaft was shorten and milled grooves with a dremel, then a metal gearwheel was placed near the shaft.
The gearwheel has one groove too.
Step 6: Hotend
The Hotend is a MK7/MK8 i found on ebay.
i cut some aluminium plates for a better cooling and place a small fan beside
the bigger alu plate above separates the hotend from the BSP fitting via two small screws
Step 7: Heat Bed
the bed is heated by two parallel resistors 22R/7W/axial and reaches 110°C
Step 8: Schematic
I uploaded a hand drawn schematic, feel free to comment/ask questions.
In the picture you can see how to modify the second shield, cut the connector pins D12 and D7,
bridge D12 with D13 and D2 with D7, now the mega can talk with the shields separatly
Attachments
Step 9: Firmware/Software
I use Tonokip in a modified version and added Adafruit Motor shield library also modified to use 2 shields.
The Software i use is Repetier Host
See Settings.zip for Repetier-Host and slic3r settings
Step 10: Results
here you can see the first results before/after calibration and some final changes in the firmware, the cube was printed with 1.75mm ABS filament, the edge length in the gcode is 10mm the final result 10.06mm !!!
Step 11: First Update
I change the driver board to ramps 1.4 with A4988 Stepper driver because they have become very cheap on ebay.
( board + 4 stepper drivers about 20$ incl. shipping)
I have supplied the x/y/z steppers with 8 Volt, 12 Volt is to much for those tiny things, with only 5 Volt the drivers won't work. i also limit the current to 300mA (with the poti at drivers)
Here are my results with using Marlin as Firmware.
I uploaded my configuration file from Marlin and also the slicr settings.
Attachments
Step 12: Photos From Printing
Step 13: Update 2
Because of the great demand, I have uploaded a drawing from the ground frame.
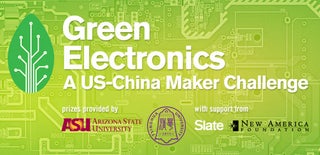
Runner Up in the
Green Electronics Challenge
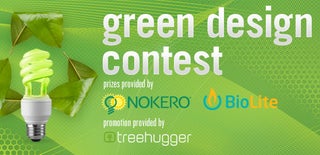
Participated in the
Green Design Contest