Introduction: 3D Printing Portuguese Azulejo Tiles
My wife and saw Azulejo tiles when we did a trip to Portugal. The tiles were great and we are very interested in integrating some into some house projects, but there are two issues when attempting to source materials, finding design(s) that we both liked and/or had to purchase in quantities well beyond what we needed. So to remedy this, I found some test designs online and began tinkering to see what I could build with my Prusa i3 Mk3.
Step 1: Finding a Design You Like
So to start off I found some photos online (non-commercial) and downloaded them. From there I used Gimp to clean them up and created a silhouette of each color, with the exception to the white. For the first two tiles, this was just a single jpg I created and then for the second (tricolor) file I created two jpg images. These files are simple black and white, just to create a vector file from. I used the website https://convertio.co/jpg-svg/ to convert the jpeg files to a vector file (svg).
Step 2: Make Your 2D Image 3D
Now that you a vector file, let's make it 3D. I went simple and used Tinkercad, import the file and then give it some depth. I made the design 1 mm thick and then i made a square base for the entire tile that was also 1mm thick with a wall around the perimeter, to catch the white drywall spackle filler I will use later.
I attached the stl files here so you can see what I built.
Step 3: PRINTING (my Favorite Part!)
This part is pretty simple now that I know how to print relatively well. I would suggest using PLA vs something like ABS because I've found that ABS warps too much especially as you get a larger print area for thing pieces such as this (if anyone has suggestions for fixing this i'm all ears). You can go up to very thick layers for this print, doesn't need to be nice and fine. I ran these at 0.2 mm per layer which was the highest Slic3r allowed me to go. As you can see I do not have a multi-material printer so for the tri-color tile I printed the orange separately.
For the orange I did have to use an xacto blade to shave off some of the edges to get it to fix, but it was overall very minimal.
Step 4: Spackle Up Your Tile
So I used some simple and inexpensive FIXALL brand drywall spackle for this. It is pre-mixed and I bought white vs the tan color that is also available. Using a putty knife I scooped up a good helping and lathered it on a nice thick layer across the entire print. I looked to fill in any holes or gaps then I gently as one would with a normal drywall fill, scraped off the excess trying to have a nice level surface across the entire tile. Don't worry about the printed are being very visible, we'll take care of that later. As you can see with the last few photos the image looks a bit ghost like through the spackle, which is perfect. Let this sit for several hours (I usually let it dry overnight just to to be saved, some of the larger depressions take a while to dry and you want this to be hard and rigid). You can poke one of the bigger white areas and if it is like putty or just soft and not hard, then it's not dry enough yet for more.
Step 5: Sanding Away the Extra Spackle and Filament
So I first tried to do this with a hand sander, which works well except on large open areas such as with the bird tile (mind you the bird tile is about 10"x10"). The orbital overall had more success with not pulling up too much of the spackle and getting everything smooth and level. I still used the hand sander on a few areas. This is needed to not only remove the extra spackle but to give the filament a smoother finish. Because I didn't use the Cura software to make my gcode file for printing I did not have the ironing feature (I plan on trying that in the future) so to compensate for having the "lines" from laying down the filament I did a little extra sanding to make it smoother. It's starting to look like a tile at this point. I then just to clean everything off took some isopropyl alcohol on a paper cloth and gently wiped off the entire surface.
Step 6: Make It Shinny
Now I have only done this to the two smaller tiles, the larger one I plan on using food safe pour on resin to see if I can make it into a cutting board. I used some rustoleum semi-gloss clear spray paint. I know the spray paint in the photo says satin, which is what I tried first, but I did a second semi-gloss coat after I realized how poor the shine was one it. I did one coat, let it dry for about an hour or so then sprayed on a second coat. After several hours outside getting the lovely smell to dissipate it was ready and I must say looks pretty great!
So we plan on finding some designs (or making some custom designs) and using them for some accent shelving backslashes in the kitchen.
I am always open to comments, suggestions and even criticisms of my work. What did you think of this?
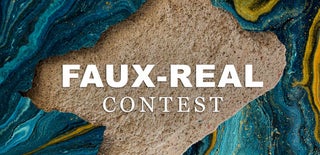
First Prize in the
Faux-Real Contest