Introduction: Propane Foundry Forge Burner
Just to be clear this Instructable is about making the torch, not its use.
The first burner that I made for my Beer Keg Metal Melting Furnace was sadly anemic! It was time to make a new torch.
The original burner was built from a cannibalized commercially available small propane torch. The one described in the following steps is completely from parts, nothing special to buy.
I like to use parts that are readily available but since the local big box is highly picked over I went for what I could buy in a single trip.
I had acquired a propane regulator, hose fittings and 10 foot hose from a local specialty supplier that happened to be open on Saturday. These are not important for the build but necessary for proper torch operation.
Step 1: The Shopping Trip
My only requirements were that the hose has 1/4 MIP fittings and a max diameter of 1.5 inches to fit the metal melting furnace.
I had some parts from another build, Namely a 1/2 X 6 black pipe nipple, a brass waterline fitting, a MIG welding tip and a LP rated Shut off valve and a little pipe sealant compound.
I did purchase:
- 1 X 6 Black pipe nipple
- 3/4 X 2 black pipe nipple
- 1/2 to 3/4 inch reducer
- 3/4 to 1 inch reducer
- 1/4 FIP to 1/2 MIP bushing
- 1/8 FIP to 1/2 MIP Bushing
Only basic hand tools are needed:
- A couple pairs of pliers
- a file
- and a drill
Step 2: The First Crutial Modification
Since I was going to use some of the items in a manner not intended, I needed to modify and check for fit.
The first critical piece is the 1/8 FIP X 1/2 inch MIP bushing. This was chosen to mate with my waterline adapter that has a 1/8 MIP fitting.
The bushing has to fit on the inside of the 1/2 X 3/4 reducer.
In order to accomplish this, I needed to file the shoulders off of the nut portion.
Since I had no way to tighten this to the inside of the reducer. I need to make spanner holes in the end of the bushing.
Drilling brass can be troublesome but a little cutting fluid and pressure will yield a smooth hole. I drilled 2 1/8 diameter holes in the face of the bushing as shown.
These holes are to tighten the bushing in the reducer. If you use needle nose for this purpose be advised that they are typically not rated for this kind of load and the jaws may bend or snap.
I used pipe sealant on this joint and tightened the parts together.
Step 3: The Orifice
As before I used a MIG nozzle in a waterline adapter for the propane orifice. Mine is .035, big but it still works. The threaded part of the nozzle goes in the water line adapter, the ferrule is added, be sure to use brass, not steel or plastic, the the crimp nut is added and the whole thing is tightened down.
The propane nozzle assembly is then threaded into the bushing that is inside of the reducer as shown. I used pipe compound on this joint.
This assembly is now used to measure where the air inlet holes are needed.
Step 4: Air Inlets
The air inlets need to close to the propane nozzle tip for adequate mixing.
I used the 3/4 2 inch nipple for the air inlet.
The nozzle was placed along side the nipple and tape was wrapped around the nipple at an optimum point.
The tape was then removed, measured and marked at 6 equal points.
The tape is wrapped around the nipple again the the marks are used as a drill guide.
Center punch the marks and drill a 1/16 hole. Then a 1/8 then a 3/8.
The 3/8 bit is abused and the drill is tilted downward to "mill" the holes so that the air path is angled towards the tip from the propane inlet side.
I found that this greatly reduces howling at faster burn rates.
These holes can be enlarged further if more air is needed.
All metal burrs both inside and outside were removed using a file.
Step 5: Assemble the Torch End
The air inlet nipple is now threaded into the nozzle reducer as shown. No pipe compound on these parts.
The 3/4 X 1 inch reducer is now threaded onto the air inlet nipple.
The 1 X 6 nipple is now threaded onto the end. these are all tightened by hand as much as possible.
Step 6: Handle and Valve
I chose to use a 1/2 X 6 inch nipple as a handle, this was threaded onto the propane nozzle reducer and then an LP rated ball valve was placed on the end.
The LP hose and regulator were attached to the valve using a brass reducer and hose coupling adapter as shown.
From start to the test fire was about 2 hours and 27 dollars!
I backed the regulator right to 0 then gradually increased the pressure until I could light the flame. then increased the pressure until the point just before the flame jumps off of the torch tip. The heat is tremendous!
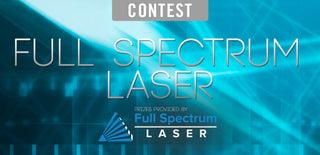
Participated in the
Full Spectrum Laser Contest 2016
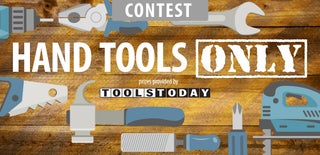
Participated in the
Hand Tools Only Contest 2016