Introduction: Propane Tank Bench
This bench is made from a scrap propane tank.
Step 1: The Raw Material
This idea originated with a junk 575 gallon propane tank on my property, which my wife told me I had to get rid of or "do something with." A lot of energy had been used to form the 5/16" thick steel into this curvaceous shape and it seemed a shame to just cut it up and recycle it as scrap. We needed some outdoor seating so I began to consider possible ways to carefully dissect the tank and reassemble the parts into a bench. My goal was to not have to reshape or reform the metal in any way, just carefully cut out the parts and weld them back together.
Step 2: Design Parameters
These are my initial two sketches. As I considered exactly where I would make my cuts my thinking was as follows:
- There is only one straight edge in the tank's shape, along the cylindrical portion, so that would have to serve as the seat and backrest.
- Standard height for seats is 17-18" and standard seat depth is 19-21", based on my field research of measuring lots of park benches.
- The bench needed to be balanced properly since the backrest would make it back heavy.
With the above functional elements factored in I began to consider the design's aesthetics. I wanted to add additional curvature so there were no straight lines in the whole design except for along the seat and backrest. I also wanted to keep it simple and not dissect the tank any further than necessary.
Step 3: Marking the Tank Ends
The 575 gallon tanks have a 37" diameter, large enough to support the basic seat and backrest dimensions mentioned previously, so I decided to cut them out first and then fit the seat and backrest between them.
Step 4: Preparing the Tank for Cutting
Just to be clear, I am NOT recommending, suggesting or implying in any way that you should cut up a propane tank. It is very dangerous and could kill you if it explodes.
Our scrap tank had been sitting for decades outdoors with some of the fittings missing, so I was relatively confident there was no more gas inside. Just to be sure I filled it 80% full of water.
Step 5: Cutting the Ends
I tried to keep as steady a hand as possible.
Step 6: Measuring the Seat
I placed the two ends on my work table and clamped them in place. I marked the seat height at 17". I rolled 1" bar stock and made a curved steel frame that matched the curve in the tank. This allowed me to make a template of the joint between the curved seat and spherical end. I marked out the shape of the seat on the cylindrical portion of the tank and cut it out.
Step 7: Attaching the Seat
I welded in the seat and feet, which I also made from the cylindrical portion of the tank. I drilled 3/4" holes in the feet before attaching them.
Step 8: Measuring and Cutting Backrest
I used the same jig I had made for capturing the seat joint to make the template for the backrest. I eyed what I thought would be a good position to allow the backrest to provide lumbar support realizing that I still needed to determine the exact position. I marked the remaining tank material and made my cuts.
Step 9: Fitting the Backrest
The backrest was so heavy that I had to use my tractor to help position it onto adjustable stands. Then began several weeks of trial and error to determine the exact position for the backrest. Numerous friends and family sat in the seat and patiently waited as I made adjustments (unfortunately I do not have photos).
After much experimentation an ideal relative position of curved seat to curved backrest was determined which provides good lumbar support for a wide range of body sizes. As it turns out, the combination of curved seat and curved backrest allows smaller bodies to slip slightly further back and down into the funnel like shape at the rear of the seat and receive good lumbar support. I believe this arrangement provides an ergonomic advancement over traditional benches with flat seats.
With the backrest position finally established I welded it in place.
Step 10: Trimming the Backrest
I used a piece of plastic EMT to mark a gentle curve for the top edge of the backrest before trimming it off. I ground down the welds and other sharp edges.
Step 11: Assembled in the Raw
Here's what the bench looked like before I sent it off for powder coat. I decided to leave the original lift hooks in place as a way to reference the source material, in case it wasn't obvious enough.
Step 12: Completed Bench
I had it powder colored in it's original color. I also affixed a new decal and mounted the original manufacturer's ID plate, showing the tank was made in 1972.
This bench is sculptural, comfortable, durable and extremely eco-friendly, containing 99% post-consumer reused content. I was so thrilled with the design that I applied for a patent and 9 months later it was granted! I've taken the next step and applied for a utility patent to protect my concept and process.
Step 13: Epilogue
The first bench wetted my appetite.
As I searched for more junk tanks I learned that locally sourced scrap tanks are an abundant and sustainable "raw" material due to strict regulations limiting their service life.
I have continued to create new seat designs. See attached PDF or visit my website: www.colinselig.com
Attachments
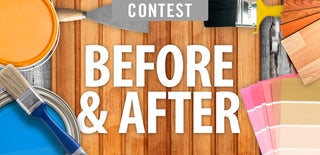
Grand Prize in the
Before and After Contest 2016