Introduction: ProtoSpray: How to Make Your 3D Prints Light Up!
ProtoSpray is a process to create 3D printed objects with light up parts. We are actually going to 3D print our objects, and then spray materials over them. The spraying, being an additive process, almost fits under the banner of 3D printing!
We have used this process to create display-elements for research, but the process can be used to create light-up 3D prints for any purpose. Do you want a glowing amulet for cosplaying? Do you want individualised flashing shapes for a bike helmet? Or do you just want to customise your 3D prints to create beautiful designs? This process can be configured for so many different applications.
These "displays" (or "segments") are created using electroluminescent (EL) material. The process involves two steps:
- Multimaterial 3D printing of insulating and conductive plastic
- Spraying of electroluminescent materials on top, to create lit-up areas in 3D.
Warning: This is not a process for beginners - although if you have experience 3D printing and spraying it is relatively straightforwards to pick up. Handling of materials can be dangerous as some contain strong solvents.
Background: If you want more information on the theory of how electroluminescent layering works, why these can be seen as "displays" rather than just lights, or what kind of applications might be appropriate, - please see our paper "ProtoSpray: Combining 3D Printing and Spraying to Create Interactive Displays with Arbitrary Shapes" (https://olliehanton.github.io/ProtoSpray_Paper.pdf)
Step 1: Assemble Materials
This project has some pretty high fixed costs - especially if you don't have an airbrush or 3D printer. But trust us, it is worth it, if nothing else than for the CAD, spraying and 3D printing skills you teach yourself along the way!
3D printing materials:
- Insulating PLA (Any can be used, we used Filaprint filament - ~£20/kg)
- Conductive PLA (ProtoPasta - ~£50/500g)
3D printing equipment:
- 3D printer (we were lucky enough to be able to borrow an Ultimaker S5 but also had success producing prints on an Ultimaker 3. In the past I have used a Lulzbot with multimedia attachment and heard good things about the Prusa multimedia head - although haven't been able to test either of them for this process).
Spraying materials:
We need 3 materials to spray on as layers:
- Dielectric layer - My preferred material is clear lacquer for cars (we used Halfords clear lacquer - UK based - ~£8). This seemed to produce EL layers that were as bright as those using Lumilor's lacquer but the car lacquer is designed to produce a cohesive coat and so is more robust and runs into corners better, making it more suitable to cover a 3D printed surface.
- Electroluminescent material - We used Lumilor's electroluminescent phosphor-based paint. This stuff is pretty expensive whereever you get it from and Lumilor's formulation was the best we used. I'd actually recommend getting Lumilor's starter pack as you get the emissive paint and PEDOT:PSS to use and copper paint and dielectric to play around with. Most importantly you get some good EL inverters as well. (total for Lumilors starter pack ~£400 https://www.lumilor.com/dealersassuming that you have access to a 3D printer and spraying equipment this is the biggest cost by far.
- Transparent conductive electrode material: this is PEDOT:PSS - a transparent conductive polymer. It is also pretty expensive. We used Lumilor's version although also had success with PEDOT:PSS from Sigma Aldirch. (price as above)
Top tip: The small pots of paint that come in the Lumilor starter kit go a long way and we created 50-60 glowing objects with just one kit. The various bits an pieces that you get are also super helpful with familiarising yourself with how electroluminescent materials go together.
Spraying equipment:
- Airbrush - we used an Iwata eclipse hp-cs which has a 0.35mm nozzle size. Anything with this nozzle size of larger than this should be usable although we would recommend gravity fed and dual action for control of material. Cost ~£130
Top tip: Don't use an airbrush that you use for fine detailing. Over time, the electroluminescent paints and attempts to clean the airbrush seemed to reduce the smoothness of the airflow. At the same time a low-end airbrush will give you difficulties in this process and generally they seem to be harder to dismantle to clear blockages
- Compressor - a compressor with an airtank is necessary to get enough pressure to push the thick EL phosphor through the brush. We used an AS-186 that costs ~£90 on amazon or ebay.
- Filters (120 mesh nylon) for keeping dried phosphor-based paint out of the airbrush and fresh tub of phosphor paint after application is completed. (<£10 on ebay)
- Pipettes - for adding material to an airbrush and conserving left over material (<£10 on ebay)
- PPE - respirator, gloves, airbrush cleaner (both standard and some acetone for any really tricky blockages), ventilated area (we used a "Lab bubble" as shown in the picture).
Control equipment
- EL inverter (from Lumilor starter kit - see above for total price)
- Series of relays (Optocoupler relays - we used an Egloo mega2560 8 channel relay set up - about £8 onAmazon)
- Arduino nano (~£5)
- Wires (male-to-male)
Step 2: Design Object
Design your multimaterial 3D print in a CAD program. There are a massive number of tutorials for designing multimaterial prints online. Personally I used Blender for designing 3D prints and was able to design all the prints that we made either in Blender, or Sketchup for the simpler ones.
Lessons Learnt: the most fool-proof way that we found to design these multimaterial prints is to design both parts joined together and then split it into two files and delete a different part in each file.
When you design your object, you must create sections of the surface of the object that will be printed in conductive plastic. These are the areas that will then light up. For each of these segments, you then want a channel attached to this segment that goes through the object to an area that you designate for electrode connections (ideally on the other side of the object). This channel can be relatively thin (think a couple of mm) but needs to be continuous when it is printed. It will conduct better if it is printed horizontal to the print bed due to the way conductive material gets layered.
There are a number of additional design constraints that you will need to take into account to get this to work - it might take some trial and error to really understand the nuances! Your object should be relatively simple with the shape mostly made of insulating plastic and the active components made of conductive PLA. The conductive PLA will act as the base electrode of your EL display. You will also need a transparent conductive top electrode that will later be sprayed on.It is imperative that these two electrodes do not touch.They will be layered on the same areas (those that eventually light up) but there will be a layer of dielectric and emissive between them. For objects with a single segment this is straightforwards as you can just designate one side of the object to have the top electrode sprayed on and the other to have the bottom electrode connection points.
Where you design your electrode connection points for the base electrode, we found it best to design cylindrical holes (1mm diameter, 10mm depth) in which to attach the pins of wires. These wires can then be fed to the control to power the EL display.
Step 3: 3D Print Base Object in Insulating PLA and Conductive PLA
Printing:
Print the object in conductive and insulating plastic. Tips on how to optimise this depend a lot on your printer.
Lessons learnt: conductive filament is very brittle and so requires special care. 1) store it in a dry place with moisture absorbing beads, 2) lower the tension in the feeder on your 3D printer. multimaterial 3D printing's constant retraction of material has a tendency to chew through materials that are much more sturdy than conductive PLA 3) increase the temperature of your print head to 220-230 degrees for improved adhesion.
Make sure that there isn't stringing of conductive plastic between channels. This will cause segments to be electrically connected to each other and so you won't be able to control them separately. If there is stringing, you likely need to reduce the nozzle temperature on conductive PLA.
Post Process:
Sand the surface of the print to get a smooth a surface as possible. Any bits of conductive plastic that are sticking up might not be completely covered by the dielectric and phosphor layers and would then cause shorts with the top electrode stopping the EL from lighting up.
Step 4: Spray on Layers to Create EL Display
Once you get going the whole spray process takes about 1-2 hours. Most of this is cleaning the airbrush. Largely we followed tips from the Lumilor tutorial, defintiely worth checking out (effectively we just replace the substrate shown in the lumilor video, and the sprayed on copper layer, with a single 3D printed object):
For each layer we found that it was best to spray two thin coats. Due to the fast drying nature of the solvents, the airbrush needed to be cleaned inbetween each coat.
1 dielectric layer (Halfords, clear lacquer)
Our prefered lacquer comes in a rattle can so this was straight forwards to apply. We did two even coats in the ventilated area over the parts of the conductive PLA that we wanted to have Electroluminescence. These were left to dry for as long as possible before the next step. Ideally you want to overspray a little with this, beyond where you will spray the PEDOTPSS to ensure that there is no short circuit.
Lessons Learnt: leave this layer to dry for a long time and take extra care to ensure even coverage. It is rare that the dielectric ends up too thick but short circuits were our most common cause of failure and when each object is costing you £5-10 to make, you really want to minimise these!
2 phosphor layer (Lumilor)
This was the hardest layer to apply. It was coated on with airbrush. It is more of a suspension than a solution and is very thick. We had to put the pressure of the compressor up to ~45psi to enable spraying and it can still cause issues of blocking the nozzle. We found that acetone was the most effective material for cleaning such blockages, along with very fine wire as a pipecleaner. This is best sprayed under UV light, as in the Lumilor video above, so that you can see where it goes because it is pretty transluscent. Again, two thin layers are about right, or until it looks like the glowing "S" shape above.
3 pedot:pss layer (Lumilor)
The PEDOTPSS was sprayed through the airbrush but under far lower pressure. The PEDOTPSS is dissolved in water and is much thinner. Too high a pressure will cause it to globule and run. We sprayed it under 10-20 psi. Be careful to clean the full airbrush, taking it apart, between each step so as to avoid bloackages with these relatively expensive materials. The PEDOTPSS is very runny so you have to be very careful to spray 2 thin coats to get an even surface. It also has a tendency to run along layer lines of a 3D print and create short circuits. We found that some designs required the use of masking tape to help contain the PEDOTPSS, although depending on your design and airbrushing skills, this is not always necessary.
Once you have sprayed it, it can take up to 5-6 hours to dry fully in our experience. You can then test that it is cohesive and sufficiently conductive with a multimeter.
Protective layer: (Halfords, clear lacquer)
The PEDOT:PSS layer is very fragile to scratching, water and other damage. Once you have checked that your display lights up, we suggest sealing it. Fortunately we have the perfect material and can reuse the clear lacquer to provide a cohesive protective layer!!. Just make sure that you don't cover up your electrode connection sites completely or you won't be able to power your display.
Multiple objects:
Most of the time taken in this process is cleaning the airbrush. You can save a lot of time by producing several objects at once, as well as minimising wastage of material through cleaning. I would still recommend doing your first few prototypes individiually until you get the hang of all the constraints and variables. I found that up to 8 designs, each with a few segments that could light up, was about optimal. You have a pay off between the efficiencies in time-savings and paint-wastage from a production line but you also have to keep in mind where connections are sprayed, where overlap needs to happen and keeping the airbrush running and not clogging.
Step 5: Attach Electrodes/setup Control
If your object is designed to have N segments you will need at least N+1 connection sites for wires. Each segment/bottom electrode will need one attachment to one side of the EL inverter. The last connection site is for the top (PEDOTPSS) electrode. We ran the bottom electrode connections through a set of relays so that they could be controlled individually using an Arduino Nano. This is shown in the image.
For connections to bottom electrodes (conductive PLA) we suggested creating holes in our designs in the CAD stage. If you did this you can just push a male-end wire into the hole and provide a pluggable connector. If this feels like a loose connection then add some of the Lumilor copper paint to the hole to make the connection better.
This is also possible for the top electrode. If this is done we would recommend making a 10mm cube of conductive PLA on the surface of your object for a tube to sit in to plug-in connectors. This should be situated far from electrode connections for base electrodes as you will need to have sprayed the top electrode (PEDOTPSS) to cover it. PEDOTPSS does not form a very strong electrical connection with conductive PLA however. To improve this we would recommend painting the top of this part (and only this part) of the conductive PLA with copper paint using an old paintbrush - this can be seen to the right of the "S" in the image shown in step 4.
Top tip: If these connection sites sound too busy or complicated, start with following this guide but use the spade wire attachments that come with the Lumilor starter set to do electrode connections. Creating "sockets" to plugin wires isn't necessary! Although it does reduce construction time.
Good Luck!! And if you make something cool, please let us know, here or on twitter at @BristolIG, @hanton_ollie
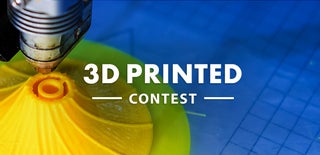
Participated in the
3D Printed Contest