Introduction: Prototyping on the Cheap
In reality this started several years ago, with an idea I had with no way to implement. I've been using 3D printing for a while now, but even the most inexpensive material can be costly. I wanted to be able to print cut outs on paper to build a model using paper. But paper isn't cheap either. And how do you slice your model? I'm no programmer. In comes 123D Make. You can slice, you can make interlocking structures, and then print it out or send the file off to be produced. So you could send it off to Ponoko and have them cut it out with lasers and send it to you. But it's still not cheap, and who wants to wait that long to find out you forgot an important detail? So I'll show you how I did it on the cheapest of cheap, and had my item built by the next day.
What you'll need:
A computer with 123D Make (it's free!!!)
A material, I used corrugated cardboard, Easy to find for free.
Hot glue gun and hot glue. Unless you plan to use it all the time, go to the dollar store and get the gun and glue for a few bucks
Scissors, you really don't have a pair of scissors? I'd get a decent pair that is sharp enough to slice through some cardboard. You could use an exacto knife if you'd like
A 3D file. If you don't know how to make one, you can easily find one for free online.
Step 1: Import Your Model Into 123D Make
So you have your file. Is it an OBJ? Well it has to be for 123D Make. If it's not, it shouldn't be hard to get it there. As long as it's an open file type you should be able to import it into Blender, Netfabb, or Meshlab (all free programs) and be able to export it out to OBJ. Now that you have your OBJ open up 123D Make and import it. There is a button on the left that says Import..., click that and select the file. Once it's uploaded, you'll be able to select your Construction Technique. Play with them all, see what looks best and works for you. For my example, I used Stacked Slices as the item was to project sound and I wanted it to be as closed as possible. Now you can set up your material.
Step 2: Setting Materials
So now your sliced and ready to go right? Not yet. Now you have to set the material. Click the pencil under Manufacturing Settings. A menu will pop up with different preset materials. You can either select an existing material by right clicking, then create a duplicate with the double pluses, or just click the lone plus to make a new material. Set your units, and set your material size. If you printing on regular paper set the material size to the printable area of your printer. To be safe I take a half inch off the paper size, so I'll put in 10.5 for the length and 8 for the height. For the thickness, measure the thickness of your corrugated cardboard. The Kerf is not as important for us, as when your cutting you can just aim for the inside of the line. doesn't hurt to make it thick to make it easy to see. Now that you have your material set up, hit done. Now select your new material from the drop down list, next to the pencil under Manufacturing Settings.
Step 3: Printing
If you need, you can change your slice direction, and there are a few more options that you can play with. Check out the tutorial for 123D make to get more in depth. Now that your item is setup, sliced, your just about ready to get printing. Click on Get Plans, down at the bottom of the tools. From here you'll have the choice of exporting an EPS file or a PDF. If you want to save some paper, and are able to open EPS, export that, and nest your parts as you see fit. If it's good the way it is, or you are able to edit PDF's to nest the items better, go with the PDF. Seeing this is on the prototyping process, I'll show you the basics, export the PDF and print it out!
Step 4: Cut It Out
There are a couple ways you could do this. If you have a glue stick you can just glue your papers to your corrugate. What I did was first cut out my pieces of paper. I then traced them onto my corrugate using a crayon to give nice broad bright lines. Then I cut out the card board pieces. Be sure you mark your pieces with their piece number. For larger parts, it will show you where the next piece should line up. For mine I eyed it up as I went along.
Step 5: Assemble
Now you just have to glue it all together! Get your hot glue going, and build your prototype up. Note for mine that I used a lot of extra glue to make it more air tight. Now you'll have your practically free prototype! As with mine, I found out that I needed to raise the shelf. The least expensive prototype I could have got for it would have cost $40+ and taken 2 weeks to get to me. Instead I fixed my model, and had it printed in the final material ready to go!
Step 6: Optional Final Step
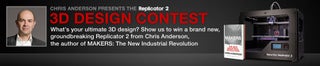
Runner Up in the
3D Design Contest