Introduction: Prusa Haribo 3D Printer Multi Material
Hello and welcome to my first instructable. I once built a 3D printer Prusa i3 from scratch
I used over several years learnd a lot and improved it bit by bit. But now I came finally to the point where I have to say goodbye to my old fella and build a new one with all the know-how I gathered the last years. I want to give you the possibility to profit from my experience.
Step 1: Bill of Materials
Here is a list of the most essential parts. I won't list every wire and screw I used. This is up to your own imagination.
2x 500mm profil 30x30
4x 300mm profil 30x30
1x 360mm profil 30x30
10x connectors
5x Nema 17
GT2 belt
GT2 pulley aktive for motor / passiv as idler pulley
3 x endstops
Hotend
Heatbed
PTFE tube
Tube clutch
Ardunio Mega
Ramps 1.4 shield
Pololu stepper driver
Step 2: The Frame
The printer frame is based on a 30 x 30mm aluminium profil. I chose a bigger frame than neccessary and if you are not too short on space I would recomend to go with this size since you have some advantage on upgrades.
Assemble the profiles as shown in the pictures. First build up the base and than the "towers" with the bridge. The height of your prints is determined by the height of your towers. The towers are on the one side fixed with the motor mount. The position of the towers will be determined later and depends on the nozzle in relation to the maximum heatbed range. Thanks to alu profile frame you can adjust it to any time.
As soon as you completed the frame you have to bring on the first 3D printed parts.
1. Rod holder for the Y-axis guide
2. Motor mount for Y-axis motor
3. Belt tensioner for Y-axis
4. 2in1 motor mount for the Z-axis incl. rod holder
Step 3: X-axis
For x-axis assembly you should start with the multi material extruder in accordance to the following link:
https://manual.prusa3d.com/Guide/2.+Multiplexer+as...
All the parts you need are in the links below. There are serveral versions for different hotends and capa. sensors you have to look for the one which fits you the best. After you finished the extruder, slide the rods in the linear bearings and the place the rod ends into the fittings. Bring the GT2 belt guide or a simple bearing into the belt tensioner and fit the pulley on the nema 17 motor. Now you can mount the motor on the fitting and thread the belt on the motor and the tensioner. Close the loop on the extruder and bring some gentle tension in the system.
As a last step bring the four lmu88 in the guiding and fix them with m3 screws and than attach the lead screw to the fittings and slide in the spindle.
MMU 1 extruder: https://www.thingiverse.com/thing:2171406/files
lmu88 bearing:https://www.amazon.com/PerfecTech-Linear-Bearing-B...
Rods 8mm: https://www.amazon.com/Chrome-Linear-RepRap-Printe...
Fittings: https://www.thingiverse.com/thing:2957916
GT2 belt: https://www.amazon.com/Mercurry-Meters-timing-Ros...
Nema 17: https://www.amazon.com/Stepper-Bipolar-56-2oz-Con...
Passiv pulley: https://www.amazon.com/Aluminum-Timing-Pulley-Bea...
Active motor pulley: https://www.amazon.com/uxcell-Aluminum-Timing-Syn...
Tr8x8 spindle: https://www.amazon.com/HICTOP-295mm-Screw-Brass-Pr...
Step 4: Y-Axis
For the Y-axis you have to bring on the preassembled carriage plate, the rod holder, the belt tensioner and the motor.
For the carriage plate you have a few options, like plywood, aluminium plate or a laser cutted frame like in the link below. In any case you have to mount on some linear bearings like the LMU88 which you can tighten with a pair of cable zips or with some printed bearing holder. You can also print directly the lmu88 bearing, you just have to grind them a little bit until they run very smooth. Next you will need to mount a belt holder in the middle of the plate which is capable to take a GT2 belt.
Afterwards you have to place the headbed on the carrier plate. Therefore bring some M3 bolts through the corner holes and use some springs (for example from a ball pen) on where the headbed can lay on. Last step are the M3 nuts which are used to level the bed. From an mathemathic point of view you need three points/ screws otherwise the system is over determinated, but in regarding the stiffeness of the whole bed it would be better to use one screw at each corner. Since this is a high pilosophical topic it is up to you weather you prefere durabilty or correct leveling. (I by myself use 4 screws and can't complain). In the middle of the headbed is a small hole capable to fit a small thermal resistor as shown in the link below. This sensor is necessary to monitor and control the heatbed temperature.
Mount the lower part of the rod holder to the alu profile, but don't tight it oll the way donw yet. Now thread the rods into the linear bearing and position the plate on the first end of the rods. this will automaticaly determine the final position of the rod holder. After tightening the first side, slide the the plate on he other side and proceed like before.
Now you have to mount the belt tensioner and the motor mount. Bring the GT2 pulley on the motorshaft of the Nema 17 motor and screw it to the mount. Bring the passive pulley to the tensioner and thread the GT2 through the pulleys and connect the ends in the belt holder. now you can gently tighten the belt.
Laser cutted plate: https://www.thingiverse.com/thing:3292617
Bearing holder: https://www.thingiverse.com/thing:2831126
Belt holder: https://www.thingiverse.com/thing:2293742
Head bed: https://www.amazon.de/Sintron-Heatbed-Aluminum-Dru...
Thermal resistor: https://www.amazon.de/Thermistor-NTC-MF52-103-Ther...
Belt tensioner: https://www.thingiverse.com/thing:2666661
Motor mount: https://www.thingiverse.com/thing:2941014
Nema 17: https://www.amazon.com/Stepper-Bipolar-56-2oz-Conn...
Passiv pulley: https://www.amazon.com/Aluminum-Timing-Pulley-Bear...
Active motor pulley: https://www.amazon.com/uxcell-Aluminum-Timing-Sync...
Step 5: Z-axis
For third axis, the z-axis, we did already some preperation. Put two nema 17 in motor mount you used as fixation for the towers and fix them with some M3 screws. Bring a pair of flex coupler in the nema shaft and the spindle with the already assembled x-axis, fix them with some M3 screws. Push some 608 zz bearings in the z top guide and line up the upper spindle end with the guide and fix it with the aluminium profile. Now you can push the guiding rod from top down through the z guide, the linear bearings of the x-axis and into the z-motor mount.
Flex coupler: https://www.thingiverse.com/thing:2967181
Z top guide: https://www.thingiverse.com/thing:2967181
Step 6: Electronics
Thanks to the open source community the handling of the firmware, software and hardware is pretty easy.
First step is to put the ramps 1.4 shield on the arduino board. I found pretty good schematic of the wiring on github, I provide you as a base for the wiring.
For the firmware use the following link which is a pretty nice online configurator which guides you through a list of options and in the end you will get a complete firmware which you can upload on the arduino board.
Ideally thats it. You should be able to move your printer and print via SD card and the graphic pannel.
The reality shows that their will be a bug or a behavior you don't want to. For a better control and monitoring I recommend a software like Repetier host or Pronterface. Once you adjust everything you can go with the graphic display
Frimware configurator: https://www.repetier.com/firmware/v100/
I hope you enjoyed my first instructable and I can leave you with a functional 3D printer.
All the best
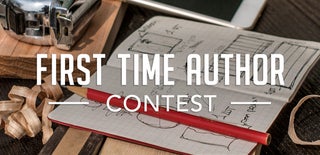
Participated in the
First Time Author