Introduction: Push-pull Tube Amplifier Using Subminiature Tubes for Guitar
For the occasional guitar player living in the city centre in a small flat a tube amplifier does not need to be as large and powerful as used stadiums and arenas. Neither should it waste a lot of power while heating up the room. Sometimes one only needs to overdrive a low wattage tube to get a nice tone at reasonable volume level. At lower wattage levels, alternative ways of powering the amplifier can be used, such as using batteries. Not only this reduces the amount of cables, as also gives the player the freedom to go play elsewhere without hunting for an unused power outlet hidden behind a heavy cabinet.
This amplifier was concepted with certain requisites:
- be small enough to be carried around
- with its own internal speaker
- battery powered
- energy efficient tubes, which have a lower filament current
- reasonable output, enough for competing with the TV
- push-pull for a certain kind of distortion
Based on my previous projects, I decided to use the 5672 and the 5678 subminiature tubes found in portable tube radios, hearing aid devices and military handheld TRX devices. This tubes, however, have direct heated cathodes, which makes the design a little more tricky. Tube radios, such as the Koyo Parrot, used three different batteries (filaments, high voltage, biasing) to work. Although 1.2V batteries for the filaments are not a problem, 45V to 90V batteries are not a common thing nowadays. Rechargeable LiPo batteries, on the other hand, are found everywhere. Every phone charger or USB powered device can supply the required voltage for charging them. By combining more of them, one can easily reach voltages that can be elevated with simple switching circuits, making them the battery of choice. The goal here is to use only two batteries and not only supply filaments and high voltage, as also provide a lower bias voltage at the grids.
Supplies
First, let us start with the tools used to build this amplifier:
- hand drill, with different drill bits
- hand saw or equivalent
- scissors or utility knife
- soldering iron
- clothes iron (optional, used for toner transfer)
- multimeter
- sanding files or equivalent
- access to a toner printer (optional, depends on desired faceplate and PCB)
And some basic materials that you can add to your toolbox:
- Sanding paper (80, 200, 400)
- Spray paint (black, clear)
- Ferric Chloride etching solution (optional, in case you are etching your board. I used a perfboard with circular solder pads)
- Solder
- tape
- wooden glue
For the speaker box:
- 4 inch, 8 ohm full range speaker (or an oval one)
- 8x8x4 inch (200x200x100 mm) wooden box , or about this size
- tolex (optional, you can finish it with other paint, or any other material)
- 20x8x1/4 inch (500x200x5 mm) wooden plank (for reinforcing the box and the frontal panel)
- 8x2 inch (200x50 mm) metal sheet for the faceplate
- Bolts and nuts (3 mm, different lengths)
The circuit can be divided in three main parts, concerning the high-voltage switched mode voltage multiplier, the inverting switched mode voltage doubler and tube amplifier circuit. To keep it short, I added a PDF containing all the components.
Not included in the list are more common parts, such as:
- 1x mono audio jack (or 2, if you want to add an additional speaker output)
- 1x 2PDT switch
- 1 LED + 1k resistor (on light)
- normal wire and stereo shielded wire (choose the thickness you like to work with)
- 2 LiPo batteries (18650 type, 3200 mA)
- LiPo battery charging board (TP4056)
Regarding the output transformer, I use a 100V line transformer (10W, with 2.5W and 0.625W taps). You can use anything that gives you a similar ratio (32k plate-to-plate : 8 ohm). This is not so easy to find. The Hammond PP 125A transformer will also work as an alternative (22k : 8 ohm).
Attachments
Step 1: Overview of the Circuit
Overview
The circuit consists of two pre-amplification stages using the 5678 tube in triode mode with gain and tone controls, followed by a paraphase inverter, also using the 5678 in triode mode. A trimmer is used adjust the signal going to the 4th tube, so that both output stages are driven by signals of similar amplitude. The dual-gang potentiometer is used as a post phase inverter master volume. The used potentiometer is linear. To achieve a logarithmic response, better for audio, a 200k resistor is connected at the lower pads of the potentiometer. The output stage consists of two 5672 tubes running at 90V, biased at -11V with a 32k plate-to-plate transformer. Load lines are shown in figure 2, with the class A curve in red and the class B curve in orange. The 5672 can also be used for the preamp stages, if the filament pins are inverted. That would result in lower gain and a cleaner amplifier.
Biasing with help of a voltage inverter
Biasing is achieved by playing with cathode (negative filament) and grid voltages. All filaments are in series, to reduce the current draw of the circuit (50mA in series against 300mA if used in parallel). The lowest bias voltage (highest cathode voltage) is required at the output stage, so that the tubes can deliver their maximum power at reasonable distortion levels. Since only two LiPo batteries are used, the highest cathode voltage (negative filament side) achievable is around 6.15V (7.4V - 1.25V for the last filament). To obtain the desired -11V at the grids, a voltage inverter based on the ICL7660 IC is used (see small circuit at the bottom of figure 1). It supplies -5V and -6.2V at the grids of the power tubes, which added to the voltage at the negative side of the filament results in -11V (-5V - 6V = -11V and -6.2V -4.8 = -11V). This is an important aspect, because it defines the maximum allowed signal amplitude before the stage starts clipping and distorting. The signal requires a certain DC shift (the bias voltage) so that the grid can swing in both directions.
The remaining stages can be biased using the same principle. Considering a voltage of around 80V to 75V a load line can be traced for the 5678 tube (figure 3). As one can see, and ideal bias, well centred for a 51K resistor, is at about -1.2V. This is about the voltage drop caused by one filament. In this case, the 2nd tube (the next tube in the series string) will have a cathode voltage of 3.6V. If one connects the grid to the filament of the 1st tube in the series string the grid is exactly at 2.4V- 3.6V = -1.2V.
You have probably asked yourself, why is the sequence of tubes in the series string not from the last to the first tube at this point. Notice that the last tube in the series string will have its cathode at 0V, which in general is bad, since the tube will only reproduce half of the signal wave at the grid. To avoid this one can use the negative bias at the grid from the the voltage inverter. But remember that this voltage is achieved by switching at high frequencies. The first stage is where the guitar signal is the weakest. Any noise introduced by the power inverter will be amplified by the following stages and will become audible at some point. Maybe not at its original frequency, but due to modulation. In this case, it is better to use the filament string approach to bias the first tube, and move the negative bias to the back. Here it was relocated to the 3rd tube, the last tube in the filament string.
Compared to my previous builds the use of the voltage inverter for biasing is a large improvement.
High voltage (B+)
The high voltage is supplied by a 555 switched mode power supply. It was already used in my previous projects.
Step 2: Working on the Circuit Boards
Boards
For this step you can etch your own board, or use a perforated board, as I done here. I built the circuit much tighter than required, so that it could also fit in an aluminium enclosure. Attached you find two layouts, the one I show here and another one where there is more space between components for better soldering.
First cut the perfboard to size:
- ICL7660 voltage inverter: 10x6 pads
- 555 voltage multiplier: 16x8 pads
- audio circuit: 26x12 pads
Soldering the components
Start soldering the voltage inverter. I suggest starting with the low profile components, such as the IC and the resistors. Solder long wires (2" or 50 mm) to the bias, ground and 7.4V pads. The image on the right is the board seen from the copper side, while the figure on the left contains the components (top view). If you are going to build it using the perfboard, use components legs to connect the longer paths. Be sure to check if you haven't forgotten any track.
Next comes the 555 voltage multiplier board. There are two jumper wires in red under the 555. Thin component legs can be used, so that the 555 sits only a little bit higher than normal. Make sure that they do not touch the legs of the 555. Leave the large capacitors and the inductor to the end. There is still space on the board, to fit different sized capacitors and inductors. Make sure that the transistor is in the right orientation.
The last board to populate is the audio circuit with the tubes. Start with the two short jumpers in red. There is a long one, that is responsible for the connection of the filaments, which will be soldered at the end with all components in place. Next solder small resistors and capacitors.
Understanding the connections at the tubes
Figure 4 of this step shows a comparison between both types of tubes used. The 5678 has a metallic exterior, which is conductive and connected to the centre leg, the negative filament. Do not let this touch anything else on the board, or even other tubes. Another point to consider, is that while the centre leg is the negative filament of the 5678, it is the positive filament of the 5672. If you follow the layout, this is not exactly important, just good to know for further measurements and problem solving. The red dot on the side of the tubes is not always visible, sometimes it is darker or even rubbed off. My trick is to measure the resistance between central and extreme pins with a multimeter. The filaments will have a small resistance, where there will be no continuity between filament and plate.
Before soldering the tubes, there are some aspects to consider:
- The tubes need to stand a little above the other components to fit nicely
- Longer terminal also give some flexibility allowing the tubes to vibrate decoupled from the board
- Preamp tubes will be used in triode mode (screen grid connected to plate), so 4 wires are enough
I got tubes that already had their legs cut short, so that I added some wire to its base. This helps dampening the vibration from the box, which can cause some ringing. To address that feedback capacitor where also added to the first two tubes. Since the 5678 was intended for receiver circuits it likes to oscillate at higher frequencies. The capacitor filters this out and keeps the tubes under control. As noise, this is only a problem in the first stages, so that no other capacitors where added.
Tone and volume wiring
Last but not least, it is time to solder the loose parts. The gain and tone circuit can be built offboard, since there are only two capacitors. Use shielded cables for the gain, tone and volume controls to reduce any chance of noise. For the gain and tone one stereo and a single wire are necessary. The shielding of the stereo cable will be the ground and connect the circuit ground to the tone capacitor, while also shielding gain 2 and gain 3. The wire is connected to gain 1 and is responsible for biasing the second stage. For the master volume two stereo wires are necessary. The shield should be used for pin 1 and 4 (or pin 1 of the second row, as in the layout).
Output transformer
The connection to the transformer is straightforward and shown in the layout. the centre tap (ct) is shown on the audio board and is the 2.5W tap of the transformer. The plates are connected to the 0W (or C) and the 0.625W taps. Since we are not using any negative feedback it makes no difference which plate goes to a specific tap. On the speaker side we have the 0 connection which goes to the negative connection of the speaker and to the circuit ground, while the positive terminal of the speaker is connected to the 4 ohms tap. This transformer supposedly will give 16k : 4 ohms. If one connects 8 ohms to the 4 ohms tap the primary impedance is doubled to 32k, which is our desired impedance. If the used transformer only has the 8 ohm tap, a 16 ohm speaker is necessary.
Batteries
To hold the batteries I used a plastic holder. The wiring is done in a way to allow switching between series and parallel. When in series the batteries will supply 7.2V-7.4V to the circuit. When switched in parallel they can be charged by a single USB charger. A separate charger or a 7.4V charger can also be used. When charged the batteries in series will read about 8.4V, but under load this might drop a little until the batteries reach a plateau of constant 7.4V. When drained they can get as low as 6V.
Whole layout
The last figure shows the complete assembly. Before connecting all boards it is interesting to check if the circuits are working separately.
Step 3: Voltage Measurement and Problem Solving
Voltage inverter
To check the voltage inverter connect ground and battery (7.2-8.4V). Measure the voltage at the three bias points. They should be:
- -bias 1: around -6.2V
- -bias 2: around -5V
- -bias 3: around -1.4V
Depending on the charging state of the batteries this can vary. So check the voltage at the battery too. Unless the value is completely off (more than 2V) it is not a problem.
High voltage
Be careful when measuring the voltage at the the high voltage board. Ideally use an alligator clip, so that you can also adjust the trimmer. Connect the batteries to the 7.2V input and ground. Measure voltage at the output. If it stays at 7V or lower turn it off. There is a mistake in the build. Check around the mosfet if it is not shorting and if all resistors are the correct value. If everything is right the voltage should be high. It could get higher than 150V, so remember to use the 200V setting of the multimeter. Adjust the trimmer to about 95V. Under load the voltage will drop again and a new adjustment will be required.
Tube circuit
Before adding biasing and high voltage to the tube circuit connect the batteries and ground and check the voltage along the filament string. If it varies at different tubes, chances are that everything is fine. If there is no continuity in the filament string the voltage will be either the battery voltage (no ground) or 0V (no continuity at some point). The metal shield outside the 5678 can be used to measure the voltage at the negative pin of these tubes.
Whole circuit
Now it is time to connect all the boards together. Remember to adjust the high voltage to roughly 90V. I decided for 1V higher based on the voltage drop in the output transformer and the power supply filter. The voltage at the C and 0.625W taps of the transformer should not exceed 90V. It will be higher at the voltage multiplier board due to the cited losses.
Adjusting the paraphase
The last step requires an oscilloscope and an audio generator. For this I suggest an open-source software as Audacity, which allows one to generate a tone with constant pitch. It is then possible to connect a cable to the headphones output and to the circuit input. The used multimeter also has the oscilloscope function, as shown in the second picture. There are also open-source apps that allow to use the mic input of a cell phone. But the phone has to have the headphone/mic plug, which is not as common nowadays.
For the measurement a 500Hz wave will be used to check the balance or symmetry of the paraphase. Therefore, connect the oscilloscope to the speaker and adjust the computer volume and the gain of the amplifier so that it will not distort. Usually, 250mV at the input is enough. The gain can then be reduced so that the wave at the output still looks round. Now measure at the input of the 6th tube. It can also be measured directly at the 6th pin of the master volume potentiometer. Check the peak-to-peak voltage. Now change the oscilloscope probe to the other pin (3rd). The amplitude will be different here. Adjust the trimmer, so that it matches the value read previously. Re-check the 6th pin, since with a different output impedance it might have changed a little. With a little back-and-fort both amplitudes will be similar. This way, both output tubes will be driven by a similar amount of signal and reach distortion at the same input level.
Step 4: Building the Combo
Concept
The concept behind the combo or cabinet is to have enough space to allow a better sound, while still using a small box. The design idea is based on an old portable tube radio produced by Vidor (I still have to get my hands on one of those to convert it to guitar using the original tubes). Therefore, instead of a natural wood finish, tolex will be applied to the cabinet.
Some wood work
To start build or buy a box with 8x8x4 inch (200x200x100 mm). These boxes tend to have thick sides but a thin bottom. With the extra board the bottom will be reinforced. This drastically improves the tone, giving a less boxy sound to it. Another piece has to be cut to the same size to be used as the lid/speaker baffle (picture 1). The corners were also rounded a little with sanding files and sanding paper.
Tolexing
Second step is to glue the tolex (pictures 2 to 4) to the box. Here, Use one square for the back and two or four pieces for the sides, as was done in the old days. Tape helps the tolex stay in position while the wood glue dries. There are several good videos that help to understand how one has to deal with the corners and difficult areas.
The baffle will also be the control panel, since it is easier to adjust the gain when the speaker is directed to you. I opted for an elliptical hole, larger than the actual speaker. This was an aesthetic choice. It also allows to use an elliptical speaker. The curved contour is half an inch larger than the speaker radius. Parallel lines at where drawn at the size of the speaker (4" or 100mm). After drilling a pilot hole, a thin saw was used to cut along the markings. There are hobby saws for cutting these thin boards with very thin blades, which makes this easier. It is important to check if the baffle still fits in the box. Without tolex there should be at least a 1mm gap on each side.
Faceplate
The faceplate is tin metal from a chocolate box. The art was done on a computer and printed with a toner printer. The toner was then transferred using the clothes iron. With the transfer done the plate can be cut and drilled.
Speaker Baffle
With the thickness of the wood, tolex and faceplate the shaft of the potentiometers might not be long enough. To address this a bit of wood was removed from the back. Use the box cutter to cut squares and remove material. Alternatively, use a rotary tool with a metal drill bit.
Since the hole of the speaker is larger than the speaker itself, another board was made to hold the speaker. Paint it black, so that it is not visible through the grill cloth. Screws for the speaker were added and glued in place. The nut goes on the speaker side. Here, the grill cloth was not fixed to the extra board, and is hold in place by the wooden screws, so that there was no necessity in gluing the speaker screws in place. The wooden screws have to be shorter than the thickness of both wooden boards, otherwise they will poke through.
Step 5: Assembly
Wooden base
All parts were fixed to a wooden base (180 x 70 mm), that can be screwed to the bottom of the box. In this case, there is no metal chassis for shielding any part of the circuit. It was not necessary here. The tube circuit board is hold in place by screws and rubber rings. They help to damp vibrations, while giving enough clearance for the wires of the master volume potentiometer, which were soldered on the copper side of the board.
The voltage inverting board is secured by a zip tie wrap, which goes trough two holes. So that the board was still flush a channel was added underneath. The high voltage board is held in place by a screwed cable holder.
Notice the terminal strip on the left. It has only two lugs, one where all grounds are connected, also grounding the chassis of the output transformer, and a second one for the 7.4V of the two batteries in series.
There was no space for the battery holder, and it was to unstable if screwed vertically.
In the box
The base is screwed to one side of the box. The battery holder is screwed at the back of the box, with pins soldered to the DPDT. The lid/speaker baffle can be positioned slightly tilted, to allow soldering, with the potentiometers and faceplate already in place.
The ON/OFF LED was soldered to ground and 7.4V pins of the DPDT. A 2.4k ohms resistor was added in series to reduce the brightness of the LED. A common anode RGB LED was added above the charging board. The SMD LEDs from the board where unsoldered, and the same connections where used.
Now it is time to close the box and glue the lid in place. Alternatively, wooden studs can be added to the box and the lid screwed at the corners.
Step 6: Play It!
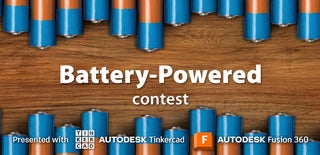
Runner Up in the
Battery-Powered Contest