Introduction: Quarter Iso-grid Cardboard Longboard
Over the last few years we've been curious to try to make a custom longboard. There have been very beautiful longboard designs made out of resin and wood but we were attracted to make ours out of cardboard. After searching the web we came across several unsuccessful attempts of cardboard skateboards that either broke immediately or had to be coated with fiberglass which beat the purpose.
The following instructables is our exploration to find a way to successfully make a structurally stable cardboard deck. The build revolves around the wonderful quarter iso-grid structure, goes through the CAD and finally the digital fabrication process.
Have a look at the video to see it in action and do drop a vote in the "Skateboard Contest" if you liked the project.
Step 1: The Marvelous Quarter Iso-grid Structure
The quarter iso-grid pattern is a partially hollowed-out structure formed with two opposite facing equilateral triangles forming a star shape. Material made using this structure is extremely light because of the partial hollowness and stiff because of all the interlocking ribs. This structure is generally used in the aerospace industry but we were interested to know how well it would hold up in a longboard deck. Thus started the adventure!
To know further details about this structure one can find more information about it over at Mike Sheldrake's Website, the genius and inventor behind this structural pattern.
Step 2: Design Features
The cardboard quarter iso-grid core longboard design has few interesting features that stand out in comparison to regular longboards.
- As the core is a quarter iso-grid structure the overall weight of the board is drastically lighter, while still maintaining structure strength
- The use of cardboard interlocked in this structure provides with a suitable and cost effective material.
- With present digital fabrication tools like laser cutters, the longboard can be assembled and rolling in less than three hours.
- The implementation of CAD design to aid production allows quick changes to the design and fast prototyping.
- All the parts friction fit together, there is no glue that is used.
Step 3: Choosing the Shape of the Longboard
There are several different types of longboard designs that are available online and to find the right one that suits your specifications we recommend having a look at this article by "Warehouse Skateboards". As creating a quarter iso-grid core was a new technique we decided not to add any kicktails which are upward curves at the end of skateboards (generally this feature aids to do tricks). We also kept a flat deck unlike most longboard which have a radially concave shape. As we already had a Yuneec-Eco 2 Electric longboard we stuck to that deck design. We then looked for top view images of the board on the internet to recreate the model in software.
Step 4: Designing the 3d Profile of the Deck
Once we finalized the shape of our longboard, we imported a top view image of the board into Fusion 360 as a canvas. We then used the canvas to create a sketch and trace out the outline of the board. We sketched out one half of the board and later used Fusion 360’s mirror tool to generate the other half. In this way, the board would be perfectly symmetrical.
Once the sketch was made, we extruded the shape by 3 cms to create the 3d longboard deck. Next, we used the scale tool to scale the body to actual size, which in our case was 90 cms long. Finally, we located the position of the trucks and extruded two rectangles that were the size of the trucks into the body. This section will later be reinforced with wood as this area of the board takes a lot of strain due to the pressure applied on the trucks.
Step 5: Slicing the Core
Now that the body of the skateboard deck was made we had to generate the numerous ribs that interlocked together to create the quarter iso-grid pattern. This is where we would like to introduce some terminology to make explanations simpler.
The ribs that go across the length of the skateboard are called Stringers. These are the pieces that have notches only on the top. We then have two sets of ribs called Ribs A and Ribs B that create 60-degree angles to the stringers to form the equilateral triangles of the quarter iso-grid pattern. The Ribs A have notches on the top and bottom of the piece while the Ribs B have notches only at the bottom.
Note: In the animation attached above, the stringers are blue, ribs A are red and ribs B are green.
These pieces were created by first making a sketch of the quarter iso-grid pattern and then extruding the individual parts without any notches. Then the notches were added by creating a sketch using Fusion 360’s rectangular pattern making sure to add the right notch pattern and spacing for each of the three types of ribs. Finally, we exported the 2d profiles of each piece to create the files ready for lasercutting.
Step 6: Simulating a Load Test on the Model
Fusion 360 gives users the opportunity to simulate various stresses and loads on their experimental models. This allows one to get an accurate idea of how the physical model will function before having fabricated it. In this way, the need to prototype the product physically is eliminated. This reduces wastes and costs and also saves time.
In our case, we constrained the sections that would attach to the trucks and applied a force on the top of the deck that would simulate the weight of an average person (65kgs) .The results showed that the weight applied would easily satisfy the safety factor. For experiment's sake, we increased the force to a value more than the average weight (100kg+) and observed warps towards the center.
Step 7: Materials Needed
Here is the list of supplies required to make the cardboard longboard, all materials can be found easily.
HARDWARE :
- Cardboard - for the entire deck you will need a sheet of cardboard with minimum dimensions of 120 cms x 100 cms. The cardboard has to be 6mm thick and needs to have 2 plies. It is best if you use BC-flute cardboard as it is generally used for shipping heavy and bulky items such as refrigerators and washing machines.
- 1/4" Plywood - Plywood is used to reinforce the joint between the trucks and the deck. You will need 12 cms x 10 cms.
- 4mm Clear Acrylic - 2 pieces of dimension 100 cms x 40 cms
- Nuts and Bolts - Diameter of 4mm and length of 40mm
- Set of longboard trucks, wheels, and bearings
As the main component of this project is cardboard, which can be sourced from any old packaging for free, the cost of the longboard drastically reduces. In comparison to the longboards available in the market that ranges from 60$ - 300$, the cost of the cardboard longboard is only 25$.
Step 8: Lasercutting the Parts
Although it is possible to cut the cardboard manually, it would be a very tedious job and will cut down on the accuracy. Thus we highly recommend a lasercutter as the perfect cuts will facilitate the assembly. The following list contains the specifications of the pieces. The file attached below contains the 2d drawings of all the parts for laser-cutting.
- Stringers - 7 pieces, 6mm cardboard
- Ribs A - 27 pieces, 6mm cardboard
- Ribs B - 27 pieces, 6mm cardboard
- Outer Panel - 2 pieces, 4mm clear acrylic
Step 9: Attaching the Stringers to the a Ribs
Gather the 7 stringers (single notched) and the 27 A Ribs (double notched). We were referring to the 3d model to identify each piece but to ease the assembly process all the parts are numbered. Start by laying out the stringers with the "Front" label to your right. Order the numbers 1 to 7 on the individual stringer pieces, chronologically from up to down.
Now it is crucial to line up the first A Rib with the right respective notch on each of the 7 stringers. Thus start with the 6th A Rib (numbered "6") as it is the first Rib piece that interlocks with all the stringers. The lettering under each notch where the 6th A Rib interlocks is indicated by "6AR" on the stringers. Once the first Rib is in place skip one row of notches on the stringers and add the next in this case the 7th A Rib. Repeat this process till the 12th A Rib.
Step 10: Grid to Parallelogram
Once few of the A Ribs have been inserted it is a good time to start putting in the first few B Ribs. Slowly apply pressure from the ends of the Stringers, to change the shape of the grid pattern into a parallelogram. If one would have completed inserting all the A Ribs it would be much harder to deform the board.
Step 11: Inserting the Keystone
Once the grid is transformed into a parallelogram structure, use the 7th B Rib (numbered "7") and interlock it with the other A Ribs that you just added. This will require a bit of effort and fiddling to get the alignment of the notches right, but after the first one, the process becomes easier as the pattern begins to hold itself together. Once the first B Rib is added, add a few more B Ribs (like 8th, 9th and 10th) to hold the quarter iso-grid pattern firmly. Make sure that you don't add all the B ribs because A Ribs cannot be added after the B Ribs are in place.
Step 12: Fully Assembled Cardboard Core
Once the first couple of B Ribs are added to the longboard deck, continue adding the rest of the A Ribs like before. Continue till all the pieces are interlocked. At this stage the core should feel extremely solid and even when pressure is applied should barely twist. To make it slightly more robust we decided to sandwich it between to acrylic sheets so that the rider's weight is better distributed.
Note: We noticed that adding ribs section by section works out better. In other words, add a few A Ribs then interlock these with B Ribs, then add some more A Ribs followed by more B Ribs and so on.
Step 13: Creating the Reinforcement Wooden Pieces
As the structure will face stress at the points where the trucks attach we decided to reinforce those areas with 1/4" wood. Mark and cut out two pieces having dimensions of 7.8cm by 5.5cm (these are according to the specifications of our trucks). Then place the truck and mark out the 4 mounting holes. We drilled them out and added a countersink so that the bolt heads are flush to the surface. The wooden pieces should fit snugly into the cutouts in the core that were pre-modelled.
Step 14: Adding the Trucks
Now that the reinforcement pieces embed well in the grooves, the trucks can be mounted. Slip in the four bolts through the wooden piece making sure the bolt head sits in the countersunk hole. Then align the bolts and pass them through the holes in one of the outer acrylic panels. We added a rubber pad to distribute the pressure and then fastened the trucks. The trucks can then be secured to the bottom panel.
Rest the wooden reinforcement pieces back into the cardboard core. Upturn the board on its wheels and place the top panel. Push the M4 bolts through the top panel till it goes through the respective hole in the bottom panel. Repeat for all the provided attaching points and finally secure the nuts on the bottom end. The board should feel steadier and is ready to ride!
Step 15: Ride Away, It Works!
We've been testing the board for around a week and it rides well.
At the beginning of the project we were skeptical about how the board would hold up. To think that the board is completely made out of acrylic and cardboard and has no glue in it and yet successfully withstands a weight of a rider is promising. Although there is quite some flex in the middle of the deck, this form of fabrication could be an interesting play of mix media and digital fabrication, transforming the traditional way of skateboard manufacturing processes.
This is just the start the our exploration of quarter iso-grid structures and cardboard skateboards. We look forward to more iterations and improvements in the future. If you liked this project do drop a vote for us in the "Skateboard Contest"
Happy Making!
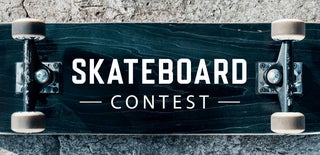
Third Prize in the
Skateboard Contest