Introduction: Quiet, Indoor 115 Volt A/C Generator
In the part of the world where I live electrical blackouts are very common due to old and poorly maintained electricity grid infrastructure, with some months up to 30+ outages depending on the season. With a newborn on the way I was looking for a backup power supply that was ready to go at a moments notice to run things like the bottle sterilizer, bottle warmer, and other important appliances. I also wanted the backup to be fairly portable - at least within the house, and it had to be quiet. My other UPS just didn’t have the capacity I needed, plus were already tied to other household devices, and firing up the generator was a hassle for shorter outages as I keep it in the storage shed and need to run extensions to power the devices I want. I could also use the Portable Generator to run other devices during the shorter outages. For example my TV, Desktop Computer, Microwave, a Small fridge, a CPAP machine, etc.
As luck would have it, I built the portable generator during the COVID-19 pandemic, so while materials were difficult to come by, it was a good reminder to always be prepared - for you preppers out there!
Lastly, PROCEED AT YOUR OWN RISK. This project involves very high current DC power, and some AC voltage/current. Use caution and stay safe! I'm not responsible if you electrocute yourself, ruin any components, or burn down your house. Try these tips to stay safe:
- Unplug the charger while working on the project or making any connections.
- Use electrical tape on the "loose" end of any wires when connecting them to terminals to prevent accidental shorting.
- A battery this size can push 1,800 amps and will vaporize a screw driver, so keep the battery terminals insulated with tape (or whatever) at all times.
- Don't touch the battery terminals with both hands (one on each terminal). While 12 volts is generally safe, doing this can actually kill you under the right conditions. Keep one hand in your pocket at all times.
- Work slowly and triple check your connections.
Step 1: Generator Size Requirements
Besides being “portable”, I wanted the generator to be able to run a bottle sterilizer, then a bottle warmer, at a minimum, while still having a decent charge left in the battery in case another outage happens before the battery was fully charged again. The generator also needed to be quiet and relatively safe since it would be charged, used, and stored inside the house.
The sterilizer name plate showed a power consumption of 710 watts, and the bottle warmer 210 watts. So my generator needs to be able to output at least 710 watts of continuous power to handle the load. Further to that, the sterilizer runs for about 10 minutes, with the bottle warmer running around the same time. So total Watt-hours required is around 600+ if I want to run each for a second cycle. No worries, I'll go through the math in more detail in the next section.
Lastly, I wanted to use relatively inexpensive and readily available components. This meant a standard 12 Volt (deep cycle) battery, and commonly available 12 volt to 120 Volt AC Inverters.
Step 2: Generator Math
In terms of component sizing I thought I’d go into a bit more depth in this section in case you’re looking to optimize your own design for a different purpose. This way you can use the same approach, except using your own numbers.
The calculation basics I’m using is AC watts divided by 12 volts to get DC amps, add 20% for inverter and wiring losses, then multiply by time to get the amp-hour requirement so I can choose the correct size battery.
So here’s the power usage and duration of each:
Sterilizer: 710 Watts for 15 minutes - 710w / 12v x 1.2 x 0.25 hours = 17.75 Ah.
Bottle warmer: 210 Watts for 10 minutes - 210w / 12v x 1.2 x 0.167h = 3.5 Ah
The total amp hours needed is 17.75 + 3.5 = 21.25 Ah
So it looks like a 22 Ah battery could do the trick here, but… there’s always a but! and I’ll get to that in a minute. In my case, I want to be able to run through two cycles for longer outages - so I’ll size it at 21.25 x 2 = 42.5 Ah minimum.
Ok, here’s the but…. The Ah rating on most lead SLA batteries are based on a 20 hour discharge. This means you’ll get the rated Ah stamped on the battery if you discharge the battery over a period of 20 hours (some are rated at 10 hours, so it’s important to check the data sheet for your battery). The faster the discharge rate, the lower the Ah the battery can provide - mainly due to internal resistance and energy losses within the battery. So what’s the 20 hour discharge rate? Well, let’s say you chose a 22 Ah battery based on the above calcs, this would be 22 Ah / 20 hours = 1.1 Amps. In other words, if you applied a constant discharge current of 1.1 amps, the battery should last 20 hours. However, my sterilizer draws a whopping 710 / 12 = 59.17 amps! This is well above the 20 hour discharge current of 1.1 amps. What this means is you need to find out what the Ah rating is for the battery you're going to choose when the current draw is higher than the 20 hour rating.
In my case since I want to have a battery with a capacity of 42.5 Ah while also drawing up to 60 amps, the actual stamped Ah rating needs to be higher. How much higher? Well, that's a tough question to answer and it depends on your total amperage draw. For me, I started out by adding 30% and going from there.
A portion of the spec sheet of the battery I ended up choosing is shown in the image attached. You can see I ended up with a 75 Ah battery, but the actual rating drops to only 50 Ah if a 50 amp load is continuously drawn from the battery. This is just over my requirement of 42.5 Ah, so has a bit of safety built in, and was the perfect choice for my silent indoor generator.
Keep in mind as well, I’m not drawing 60 amps for the full duration, so the actual Ah I’ll get out of the battery will be a it more. Plus, by having some extra capacity, the depth of discharge will be less, prolonging the life of the battery, as well reducing the charging time of the battery.
Step 3: Parts List
Here's a list of the main electrical / electronic parts I used for the silent indoor generator build:
1. DC to AC Inverter
With my biggest power consumer at up to 710 watts, I needed an inverter with a continuous output rating of at least 710 watts. Most inverters in this range seem to come in 1,000 watts as a standard size. I ended up going with this Bestek 1,000 watt pure sine wave inverter. The ratings were good, plus I liked the LCD display so I could keep an eye on my battery voltage and the output power. Bestek also makes a modified sine wave model for a lot less that would also work, but since I want to possibly use it for other devices I stuck with the pure sine wave model to avoid any future disappointments.
2. Battery
Since I wanted the generator to be charged and stored indoors, the battery needed to be sealed. The typical battery used for an application like this is an SLA (Sealed Lead Acid) type. Unlike most deep cycle marine, golf cart, or solar batteries which gives off explosive hydrogen gas during charging, SLA’s are sealed and therefore don’t release hydrogen during charging, so is safe for indoor charging. I explained the battery sizing in the previous section, and mentioned I ended up with a 75 Amp hour. Due to the weight of the battery, shipping was somewhat impracticable for me (due to freight forwarder costs to my location), so I ended up sourcing the battery locally. But here’s a couple I found on Amazon that are virtually identical, this one, and this one.
3. Battery Charger
For the charger I needed something that would fully charge the battery, then keep it charged through a maintain mode, or trickle charge, as I planned to keep it plugged in 24/7 so it would be ready when needed. A typical SLA battery charging current would be about 1/10th of the battery capacity in amps. For the 75Ah battery like I’ve chosen would required about a 7.5 amp capable charger. The one I’ve chosen is only 5 amps, so it’s a bit on the smaller end, but will still work since I have the time to wait for the battery to charge fully. I would suggest having a look at the battery manufacturer’s charging recommendations to ensure you’ve got the proper sized charger for the battery you use.
4. Circuit Breaker
I decided to include a circuit breaker in the design for two reasons; a) extra overload protection over and above what’s already included in the inverter, and b) to use as an on/off switch to isolate the inverter from the charger during charging. You don’t need to include this if you don’t want to, but having the inverter connected and on uses some standby correct, taking away precious amps from the charger and possibly interfering with the trickle/maintain charge function of the charger. Adding the circuit breaker also allows the use of the relay (next item below) to ensure the charger does not turn on while using the inverter. I’ve used this Circuit Breaker, but a similar type will work. If you don’t want to use one, you can just use an in-line fuse or leave it out all together. For the Amp rating, some quick math… 1,000 Watts divided by 12 Volts = 83.33 Amps. Add a safety margin of 10 to 20%, and this puts you around 100 Amps which fits perfectly for this model. Note: Similar + cheaper circuit breakers are available as well, but make sure to read the reviews carefully. The cheaper ones tend to have a high internal resistance so they heat up and trip quickly, well below the rated current, making your backup power supply useless. Buy with caution here and don’t cheap out. (notice the one in the pictures below - yeah, they claimed to be good, but had them trip out way under 100 amps).
5. Relay
As mentioned above, the intent of the relay is to automatically isolate the AC input to the charger whenever the inverter is being used. This way the charger won’t try to charge the battery while the inverter is trying to pull much much more amps from the battery. Again, this is optional, and you could either replace this by a regular household light switch, or nothing at all and just unplug the charger from the wall outlet while the inverter is being used. The relay I’ve chosen comes with two relays, but you only need one. I figured an extra relay laying around for future projects is never a bad thing ;-)
6. Wiring
You’ll need some heavy gauge wires to get the power from the battery to the inverter. To reduce as much voltage drop as possible, I decided to go with 2 AWG pre-made wires with the ring terminals already attached. I could have bought the wires and connectors and soldered them myself, but soldering 2 AWG wire is not an easy task and you want to be sure the joints are well made. Any minor resistance in the joints at the amps we’re looking at could cause these to run extremely hot, and provide inaccurate readings and early shutdowns on the inverter. I ended up getting a pair of 12 inch long black plus red wires, plus an extra 12” long red wire for the circuit breaker to inverter leg (see circuit diagram in the next section). I chose the ring terminal sizes to match the battery, circuit breaker, and inverter terminal sizes accordingly.
You'll also need a couple feet of wire for the relay wiring on the DC side. This can be small gauge, 18 to 24 gauge or so will be fine as the coil current on the relay will only be a few milliamps. I used some extra wire I had laying around, but you can get this at pretty much any hardware store. All other wires shown in the circuit diagram are from the battery charger.
As mentioned at the start of this section, these are main components needed for the silent indoor generator. For the actual build, I used materials I had laying around at home. If you need to purchase materials to complete the build, the instructions following will provide the details of what you'll need to purchase.
Step 4: Enclosure Design
I designed the enclosure to be as compact as possible, yet strong enough to hold the weight of the battery (52 lbs, or 23.5 kg). I used materials I already had home, and these included:
- 1/2" (13mm) plywood
- 1" x 4" pine (3/4" x 3-1/2" finished sized, all other sizes shown are ripped from the 1x4's)
- Wood screws
- Pneumatic nail gun (totally optional - regular nails work just as good)
- Wood glue
- Table saw or similar
- Jigsaw
- ...and other various hand tools.
Refer to the images in this section for the details on the design and dimensions.
Step 5: Enclosure Construction
Constructing the enclosure is a fairly straight forward process. Since the battery is very heavy, the first step is to glue together the two bottom plywood pieces for extra strength. Apply a generous helping of glue and clamp the two pieces together to ensure they are perfectly aligned to each other. Then nailed the two pieces together so you can remove the clamps while the glue dries. Alternatively, leave the clamps in place until the glue dries and skip the nails.
Continue working on the base by test fitting the smaller pieces that contain the battery and inverter, and when happy with the fit, apply glue and nail from the bottom.
After completing the base, fit the sides by clamping them in place and securing with two screws in the bottom. Do this for all four sides. Don't apply any glue at this point, this will be done later as having the sides removable makes it a bit easier to test fit the final assembly.
In my case, I fitted the sides with the screws first, then disassembled them and added the additional support pieces (for the upper screws and for attaching the battery and inverter hold down brackets), and made the cutouts for the inverter and handles.
After completing the box, you can move on to making the hold downs in the next step.
Step 6: Hold Down Brackets
Because of the high currents involved and the fact that the unit will be portable, it's important the battery and inverter not be allowed to move accidentally. One method to achieve this is to use hold down clamps. In my case I used some 1-1/2" wide by 1/8" aluminum stripping I had laying around. Any similar sized aluminum (or steel) would also work.
I didn't have a bender or press brake available, so I clamped the aluminum to the bench top, then used a pair of pliers to bend the aluminum down, using the edge of the workbench as my "corner". The pliers won't give you a full 90 degree bend, so I finished up the bend with a hammer.
I then worked my way through the other bends after test fitting each bend and marking where to make the next bend.
After making all the bends, drill holes in the brackets so they can be secured to the enclosure with regular wood screws.
For the inverter, I decided to remove the handle and use the pre-drilled holes to help secure it in place. This way the inverter does not move when plugging cords into the inverter outlets.
When the hold down brackets are complete, we can move on to placing the top components.
Step 7: Mount Top Components
The next step is to layout and mount the top components, namely the charger, relay, and circuit breaker. This can be a bit tricky since 2 AWG cable doesn't have the bend radius to be able to make nice entries in the top board.
Start out by placing a plywood strip on the top supports (removing the back makes this much easier) and loosely attaching the power cables to the circuit breaker and inverter. You only need to do this for the positive (red) cables since the negative (black) will be staying below. Mark the point of entry on the strip as well as your best guess on the angle the wires will enter. Then place the actual top board in place and transfer the marks for the entry point. It's a good idea to also lay out the charger and relay to ensure it fits nicely and there's no interference.
Drill the required holes for the cables. You'll make three at this stage, one for the battery charger DC wires that connect to the battery, and the two positive power cables. The charger cable can be drilled vertically, but the holes for the power cables will need to match the anticipated angle the cables will make.
After the holes are drilled the charger, relay, and circuit breaker can be screwed to the top board to secure them in place.
Step 8: Relay Wiring
To connect the relay you'll need to make a couple of lead wires. Besides a soldering iron and solder, you'll also need:
- Two 16" (approx) long 18 to 24 gauge wires
- Two ring terminals (to match your battery terminal post and circuit breaker size)
- Some heat shrink tubing
While the ring terminals can be just crimped to the wire, I prefer to solder them for a more secure and cleaner look, and heat shrink to help insulate and a cleaner look.
Note as well, the ring terminals are only placed on one end of each wire. The other end should be stripped bare about 1/4" or so. We'll connect these wires in the next step.
For the AC side of the relay you'll need to cut the charger power cord on one conductor. Route the power cord past the relay and mark the points where the wire should be cut. They can be connected to terminals 1 and 5, or 2 and 6, of the relay, depending on the side you choose. Split the cord by cutting the insulation between both conductors, being careful not to cut/expose the wire beneath. Pull the wires apart to extend the cut to the desired length, then cut out a piece of wire of ONLY one conductor equivalent to the distance between the terminals. Then strip about 1/4" from the ends of each wire. See the photos for more details.
In the next step we'll connect all the wires and start up the silent indoor generator to make sure it all works.
Step 9: Hook Up and Initial Test
The next step is to make all the connections and test that it all works. This can be a bit tricky as you need to make some connections below the top board, then carefully feed wires through the holes to make the top connections. To ensure vaporizing (or destroying any components), place electrical tape on the ends of all connected wires, and work from one terminal then the other.
Refering to the pictures, connect the negative side (easiest) first. Connect the 2 AWG power wire to the terminal along with the charger connector, and the relay wire.
Do the same for the positive (red) side. Note the relay wire for the positive side should not be connected to the battery terminal (error in the photo), as this connection is made on top to the circuit breaker. I made this mistake, but no harm done, it just kept the charger from charging ;-)
After the battery and inverter connections are complete, feed the wires through the top board and make the top connections as shown in the pictures and the circuit diagram.
Check your wiring and connectors to make sure they're connected to the correct terminals and the connections are snug.
Check them again!
Next, plug in the charger to the wall outlet, the lights on the charger should come on and the battery should start charging. If no lights come on, check the connections on the relay to ensure they're on the correct terminals.
Now push the lever on the circuit breaker to complete the power circuit. Assuming nothing smokes or goes bang, the charger lights should go out. Then press the power button on the front of the inverter to turn it on.
If that didn't work, check your wiring again, most likely something is not connected correctly.
To turn it off, press the button on the circuit breaker to cut power to the inverter and start the charger again.
Step 10: Glue the Generator Enclosure
The next step is to add some additional strength to the generator enclosure by gluing all mating surfaces.
First, add some additional screws on each side to help "pull" the plywood to it's adjacent surface. This allows the glue to provide more strength, plus fills any gaps along the edges.
After you've added the additional screws (see first image), remove all the sides and start gluing the two sides to the base (battery side and inverter side). Apply a generous helping of glue, and drive in the screws that attach the sides to the base.
Now do the same for the front and back. I recommend using bar clamps (if you have them) to help the top edges of the sides mate with less mess. See photos for details.
A quick note on the "excess" glue used... Yes, there's lots there! After screwing or clamping any glued surface, use a wet cloth to wipe up the extra that bleeds out. This will make the sanding/finishing much easier.
Step 11: Sanding and Painting the Generator Enclosure
How you decide to finish the enclosure is up to you. Here's the general steps I took to get a nice smooth finish.
Surface Preparation:
- Rough sand the entire enclosure with 120 grit sandpaper. This can be done by hand, but a random orbital sander makes things go a lot quicker.
- Use wood filler to fill in any screw and nail holes.
- Sand again using 180 grit sandpaper for a smoother finish and to remove any excess wood filler.
- Add more wood filler if required. In my case, I didn't need much more, so I ended up using some drywall compound to finish filling the holes.
- Sand again using a 240 grit sandpaper.
- Brush off excess sawdust, and wipe down with a tack cloth (a damp cloth works in a pinch) to remove any final traces of sawdust.
Painting:
These steps will ultimately depend on the paint you decide to use, however, you'll need at least a primer or sealer coat, followed by a couple of finish coats. A light sand with 240 or 320 grit between coats helps to get a really smooth finish. I ended up using an enamel (oil base) paint, but didn't have any sealer or primer available, so it took several coats to really get a nice finish as the bare wood really soaked up the paint. Spraying would have been ideal, but since that wasn't an option I brushed on the first two coats, sanded, then used a roller for the next coat, then one last sand, then the final coat. The enamel takes some time to dry, so I left it for at least 48 hours to get hard enough before handling it.
Step 12: Make the Silent Indoor Generator Portable
By "portable", I mean add some wheels to it. I had some swivel casters from another project that were no longer in use, so I used those.
Pretty straightforward... align the wheels, mark and drill the holes, drive some screws in. Done!
Step 13: Final Assembly and Testing
The final assembly is basically the same procedure from the initial hookup and test. The only difference here is to add some screws to hold the top in place, and proceed MUCH slower and more carefully. You wouldn't want to scratch that newly painted surface!
Turn it on! Check out the video for the final test where I connected the sterilizer then the bottle warmer to the silent indoor generator to make sure it worked as planned.
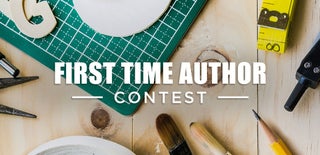
Participated in the
First Time Author Contest