Introduction: RC Car Upgrade Using 3D Printing
RC cars are a fun and inexpensive way to experiment with new and interesting engineering ideas. My name is Antonio Cervantes and as a mechanical engineering graduate student from San Jose State University, I've always loved racecar engineering and wanted to try designing new upgrades for my RC car. The goal for this project is to design 3D printable aerodynamic pieces that upgrade the speed and handling of my Armma Typhon buggy RC car. The concepts designed in this project were inspired by the cars from Formula 1 racing.
Supplies
Hardware
- Arrma Typhon 1/8 Scale RC car
- Creality Ender 3 3D printer
- 3D printer filament (PTEG or ABS preferred for outdoor use)
- Calipers
- 2, 3, & 4mm socket head cap screws
- Blue painters tape
- Duck tape or Command strips
- Velcro strap
Software
- Fusion 360
- Ansys
- Matlab
- Cura
Step 1: Research
To start my project, I first did some research on the basics of car aerodynamics. I read some research papers and watched some YouTube videos to gain a good understanding of how aerodynamics affect a vehicle's performance. I found that front and rear wings give a car a good balance of front and rear downforce, and the shape underneath the car can add downforce via ground effects. Ground effect is the phenomenon where air is forced down into a small space causing a low-pressure region, which creates a vacuum that pulls the car to the floor, also known as downforce. My goal was to apply these same engineering principles to an RC car to see if they can improve the car's performance better than the stock manufacturer's build. I planned to design and build a front and rear wing, an undertray, and side pods that use the ground effect phenomena.
Image Sources: Left image, Right image
Step 2: Measurements
In order to design parts for an existing RC car, it's important to look for and measure any potential mounting locations. I looked for mounting locations that I could screw my parts into so that they would hold securely. I measured the dimensions of the holes to screw the parts into. I found that the front wing could mount to the holes wear the front bumper is mounted, and the new rear wing could mount where the old rear wing was. The side pods could mount to 2 extended tabs with holes on the sides of the chassis, and the undertray could be glued or taped to the bottom of the car.
Step 3: Front and Rear Wing Design
The front and rear wings were designed in Fusion 360 using the NACA 4412 airfoil. The airfoil 2D sketch geometry was obtained from the website Airfoil Tools. A 3-element wing was chosen for the rear wing, and a 2-element wing was chosen for the front. These multi-element wings help gain downforce while lowering drag force. The wings were designed to use center supports that slide the wings through a cutout in the shape of the wing profile. The sides of the wings have holes in which a 2mm and 3mm screw is used to screw the side panels to the sides of the wings. The center supports have holes that use 3mm screws to mount to the body of the RC car. The rear wing mounts to the same holes as the old rear wing, and the front wing mounts to the holes where the front bumper is mounted to.
Step 4: Simulations
Simulations are a great way to test different configurations of aerodynamic pieces. It was important for me to test different front and rear wing setups because I wanted to get good downforce while keeping the drag force as low as possible. I tested about 5 iterations of the front and rear wing using Ansys Fluent CFD software. I found that a 3 element design worked best for the rear wing, and a 2 element design worked for the front. I did not simulate the undertray and side pods because drag is not a major problem for them since the use of ground effect gives low drag, so I skipped simulating those components in order to save time.
Step 5: Undertray Design
The undertray was designed to use ground effect to generate downforce using the floor of the car and the ground. I started by using the spline tool to sketch an inverted wing profile. The undertray profile has a sloping hump and smoothing transition back to flat. This profile squeezes the air against the ground forcing it to move faster under the hump. This fast-moving air creates a low-pressure zone which sucks the car down to the ground. The undertray has fins that run along the length of the undertray. These fins help seal the air with the undertray and ground to keep it from escaping out the sides and direct the air to flow in a straight line. The top of the undertray is flat so that it could be glued or taped to the bottom of the RC car.
Step 6: Side Pod Design
The side pods were also designed to use ground effect. It features a custom wing-like profile that was sketched using the spline tool. The side pod has a bottom hump that uses ground effect for downforce, and the top is tilted for extra downforce from air pushing on the top. The side panels also help seal air between the ground and pod and direct airflow in a straight line. The side pods are mounted to the RC car via tabs with holes that are mounted to side tabs on the RC car chassis.
Step 7: Final Design
My final CAD design contains all the aero pieces and a model my RC car so that I can see how it would look on the car itself. All the parts colored in blue were 3D printed.
Step 8: Test Prints
Before beginning to 3D print all of my aero parts, I created some test prints to check the fitment of the parts on the RC car. Test prints are important because they can save time from printing unusable 3D prints, and help catch any dimension errors from the 3D printer due to thermal expansion or other problems.
Step 9: 3D Prints
All parts we printed on a Creality Ender 3 and CR-10 3D printers. Print times ranged from 5 hours to 12 hours for 17 total parts. All parts were small enough to fit on a 220x220mm print bed except for the undertray which required a 300x300mm print bed. There was minimal post-processing of the printed parts except for cutting away some material for the mounting holes and the cutouts of the front and rear wing supports.
Step 10: Install
The final built car can be seen in the image on the left. The installation of the aero pieces was simple and required very little time. The rest of the images show the install process from the beginning to the end.
Step 11: Final Build
These are some more images of the final build from various angles.
Step 12: Test
In order to see if my design improved the performance over the stock setup of the RC car, I needed to test it. I tested the RC car with its stock components, then with my new design components. I used the Matlab Mobile app on my iPhone and strapped it to the rear of the car using a velcro strap. Matlab Mobile can record data from the accelerometer and GPS in the iPhone. Leveraging this app was helpful to record the acceleration G-forces and top speed of the car. I recorded data from the car doing figure-8 laps, left and righthand circle turns, and speed runs. This video shows how I mounts the iPhone to the RC car and the various test I conducted.
Step 13: Performance Comparison
Matlab was used to process and plot the G-force data for the stock RC car setup and the new upgraded setup. Taking a look at the data, we can see that the new upgrades had worse cornering performance than its stock setup. This was due to the RC car being an off-road buggy with supple suspension allowing it to compress so low that the side pods and undertray begin to drag on the ground. The average cornering G-force for the stock setup was 0.85Gs, and the average cornering G-force for the upgraded setup was 0.6Gs. The top speed for the RC car was slightly improved from 17.5 mph for the stock setup to 18.3 mph for the upgraded setup. This was probably due to the fact that the front wing was able to slice through the air better than the stock front bumper. In the end, this project was meant to be an experiment to see if I could improve an RC car's performance with aerodynamics, but I learned that other aspects of the car need to be considered as well. Suspension, chassis build, and engine/motors are also very important when it comes to improving car performance.
Step 14: Future Improvements
A major problem with my aero design is that the undertray and side pods relied heavily on side skirt fins to seal the air between the underside and exterior air. I designed the undertray to use the 3D printed side skirts, however, this did not work great because when the RC car's suspension compressed, it pushed the plastic skirts onto the ground causing them to slide, taking away grip from the tires. For the side pods, I did the opposite and made skirts that were too short and used tape to extend them. This did not work because the tape would fold when the RC car's suspension compressed and would not return to its original shape and stayed bent. A better material would need to be used such as a flexible polymer for the side skirts so that they could bend with suspension compression and return to their original shape.
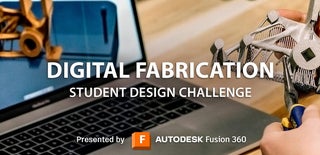
Runner Up in the
Digital Fabrication Student Design Challenge