Introduction: Rainbow File (stuff) Holder
PS: I realized some of the diagrams are a bit too big and get cut off a little. Click to enlarge please! :)
These handy doodads are generally called magazine or file holders. You can of course put all kinds of stuff in here (and I intend to!)
I wanted something sturdier, more long-lasting than Ikea cardboard. I know Ikea has a plywood version but a) I don't live near Ikea, and b) I don't like the design. I wanted more flexibility and I'm stubborn like that.
I chose rainbow colors because ... I like rainbow, and it helps with organization. You, of course, can paint them whatever you like. Throw glitter in there, whatever floats your rubber duck.
BEFORE WE BEGIN:
The final step contains all the footnotes where I cover my thoughts on alternatives, design suggestions, and whatnots. Look for the underlined **s with a corresponding number... Because I talk too much and I'm trying to be concise...ish.
This was the last picture I took because I knew I might need to add things as I went. I was right.
Supplies
The final list in a vague sort of order -- you're free to use your own preferred brands of course.
1/4'' plywood (three 2'x4' sheets of Sandeplywood)
clamps (these are Irwin Quick-grips; using tape to hold the pieces together while the glue dries works too)
Famowood wood filler
Loctite Wood Worx wood glue
sandpaper
paint can opener thingy (the metal key shaped thing on the tape - you can use a screwdriver)
paint stirrer sticks
various brands of paint (all semi-gloss; Behr Marquee is what's in the sample pots)
Kilz primer
acetone (you can also use mineral spirits - this is for the Kilz primer)
paintbrushes
disposable gloves
paper towels
white tape (you can definitely use the blue painter's tape instead of white)
X-acto knife
slurpie-style straw (if you use paper you can recycle it)
cardboard (as a surface protector - you can use a painter's dropcloth)
SEMI/NOT PICTURED:
Miter saw
table saw with miter attachment
belt sander
plastic bag (you can use a plastic dropcloth instead)
respirator
Step 1: Prototyping
As with all great projects, you should start with a cardboard prototype. I stuck binders, folders etc in it to make sure I had enough room for the things I anticipated shoving in the final product.
Three things to note:
- The two sides on my prototype are different, both from each other and the final product. One side has the straight diagonal cut that the final pieces use -- the other one is a fancier sort of complex curve. It's prettier, for sure, but we didn't have a jigsaw available to use, so had to go with straight cuts.
- The back side has three bars instead of two. Three bars would have allowed the contents to be more visible but once we began the cut process, we realized it would simplify things if we made the bottom bar 6''.
- Similarly, the height of the curved side is lower; we simplified it again so we could just use a full 12'' and save us the extra cut for trim. We added a bit of cardboard on the diagonal-cut side to eyeball the new height and to help guide our final dimensions.
Step 2: Cutting Your Plywood - Sides
We started with 3 sheets of 2' x 4' plywood of 1/4'' thickness, basically the cheapest stuff that Home Depot had (Sandeplywood I think) Of course it's not actually 2'x4' nor is it really 1/4'' but it's close enough for this purpose, just something to keep in mind when doing your layouts and cuts. With that in mind and the width of the saw blade and cuts, your measurements won't be dead precise so you may find yourself slightly plus or minus in some places. This happened to us in a few spots as you'll see so you'll need to do a fair amount of trimming and squaring up.
First step was to rip all three sheets lengthwise to get six half-sheet pieces of 12''x 4'. (first photo)
Second photo: We began ripping 11.5'' sections. This took 3.5 half-sheets and gave us (14) 11.5''x 12'' semi-squares, (3) 12''x2'' strips and (1) 12''x25'' square. Layout wise, cut 3 following the first plan, and one following the second. Basically just keep track of how many 11.5 pieces you have, and stop when you have 14.
Step 3: Cutting Your Plywood - Everything Else, Part One
BOTTOMS:first picture Starting with a fresh 12''x4' half-sheet, cut seven pieces of 12''H x 4.5'' W. (1) remainder of 12'' H x 16.5'' W.
BACK BOTTOM BAR: second picture From that piece of 12'' x 16.5'', we cut three 12''H x 4.5'W' strips, then took those 12''H strips and turned them to cut them in half so we now had (6) 6"H x 4.5'' W pieces. (1) remainder of 12'' H x 3'' W.
SPOT CHECK You should now have the following:
(14) "square" sides - 12'' x 11.5''
(7) bottoms - 12'' x 4.5''
(6) back bottom bar 6'' x 4.5''
(3) Remainder - 12'' x 2''
(1) remainder 12'' x 3''
(1) remainder 12'' x 25''
BACK TOP BAR: third picture, left From the 12'' x 3'' you can get (2) 4.5'' x 3'' sections, with (1) 3'' x 3'' remainder.
FRONT BOTTOM BAR:third picture, right From the (3) 12'' x 2'' strips -- each one can be cut down to (2) 4.5'' x 2'' strips with a 3'' x 2'' remainder - total of (6) 4.5'' x 2'' strips and (3) 3'' x 2'' remainder
SPOT CHECK:
(14) "square" sides - 12'' x 11.5''
(7) bottoms - 12'' x 4.5''
(6) back bottom bar 6'' x 4.5''
(2) back top bar - 4.5 x 3''
(6) front bottom bar - 4.5'' x 2''
(1) remainder - 3''x3''
(3) remainder - 3'' x 2''
(1) remainder 12'' x 25''
Step 4: Cutting the Plywood: Everything Else, Part Two
Take that one big remainder you have, the 12'' x 25'', and rip (3) 12'' x 4.5'' strips with (1) remainder of 12'' x 11.5 first diagram
First strip: cut the last bottom back bar (6''x 4.5'') and two more back top bars (3'' x 4.5'') second diagram, left
Second strip: cut (3) back top bars at 4.5''x3'' and (3) front top bars of 4.5'' x 1''. second diagram, middle
Third strip: cut the last front bottom bar, (1) 4.5'' x 2'' and (4) front top bars at 4.5'' x 1'' -- **5 If you cut to 1'', you'll have a remainder of 4.5 x 6''. third diagram, right
SPOT CHECK
(14) "square" sides - 12'' x 11.5''
(7) bottoms - 12'' x 4.5''
(7) back bottom bar 6'' x 4.5''
(7) back top bar - 4.5 x 3''
(7) front bottom bar - 4.5'' x 2''
(7) front top bar - 4.5'' x 1''
(1) remainder - 3''x3''
(3) remainder - 3'' x 2''
(2) remainder 4.5 x 3
(1) remainder - 12 x 11.5
Step 5: Angled Cuts for the Sides
Use painter's tape to mark the dimensions of your side pieces. The reason for this is to make sure that when you make your diagonal cut, you have the longer rise on the "front", and the "top" should be shorter. (diagram/first picture) The purple/blue shaded area is what will be your side. The white is offcut/remainder in a triangularish shape.
In the case of my design, I wanted to provide as much support for tall objects inside -- like magazines, file folders, etc so we offset the cut so it wasn't straight from the 90 degree corner to the "front" (again, see diagram). So I measured 5'' on the "front" edge, and about 4'' in from the top corner. We drew a line between the two points, squared it against the arm of the miter attachment, and ripped a straight line. 4'' was the goal; it ended up being closer to 3.75'' in the final product. In the second photo here, you can see the lines a bit clearer where we were playing with angles and setting the arm of the attachment so we could make consistent cuts.
(third photo) MAKE SURE YOU PUT THE CUT GUARD DOWN BEFORE YOU TURN THE SAW ON. SAFETY, PEOPLE. FINGERS ATTACHED = GOOD. This goes for the table miter saw too of course.
Step 6: Trimming
Like I mentioned before, due to the nature of things we needed to do some trimming.
First photo - we had to lay a cut side flat against a bottom piece and mark it to trim off the little .25-.5 inch remainder or ovwe would have ended up with an overhang (as demonstrated in second photo). ** 2
Due to how we cut the side pieces we ended up with the sides not quite matching - in both length and height. (third photo) so we selected the smallest one in both dimensions and shaved down the others to match. This was fine to me, because I mainly was concerned about making sure the length matched the bottoms; the height was less important. This is one of the reasons why the top edge in the final product isn't 4'' as originally diagrammed.
Step 7: Assembly Begins
You will (or should) end up with the following:
(14) 11.5''L x12''H (ish) -- sides
(7) 5''W x11.5'' L rectangles -- bottoms
(7) 4.5'' W x 6'' H rectangles -- back bottom bar
(7) 4.5'' W x 3'' H rectangles -- back top bar
(7) 4.5'' W x 3''H rectangles -- front bottom bar
(7) 4.5'' W x 3'' H rectangles -- front top bar
And a bunch of scraps/offcuts. One piece will be a full 12''x4' half-sheet - save that for your next harebrained project. ;) The triangleish remainders from the sides will come in useful later as well.
Test-fit every single box. You want to be sure everything fits together before you walk away from the saw, especially if said saw is located miles away from where the boxes will be assembled and painted...
Not pictured - we took the 14 box sides and stacked them then ran a belt sander along the pointy corners of the diagonal cut to round them off a bit for aesthetics and safety purposes.
Step 8: Gluing Begins
I took some of the triangle offcuts and layered tape on them (first photo) in order to use them to elevate the boxes off the surface so they wouldn't get glued or painted to things they weren't supposed to. The tape comes right off so you can use your triangular bits for other projects later.
I wrapped a bottom piece in a plastic bag - or plastic dropcloth - so it wouldn't get glue on it. For the last box, I used a 4.5'' wide scrap piece instead - good reason to save the offcuts. Then I wedged that wrapped piece in between the two side pieces and bridged all three together across the top with a piece of tape so that the sides would stay up until I put the clamps were in place. (second photo)
When you're gluing, it's better to have a bit too much than too little, you want a good contact between your wood surfaces. Apply glue to the long sides of a bottom piece and set it down - check the faces and put the 'worse' side face down - and then pick up your "H" structure and set it in place with the bottom nested INSIDE THE SIDES. If you set the sides on top of the bottom piece's edges, you'll have a narrower box, and your front and back bars won't fit between the sides like they're meant to. (diagram)
Wood glue adheres better if you give it a little rub back and forth, so do that - you probably will have to anyway, just to make sure the corners of the sides are squared up to the corners of the bottom. Then apply clamps to the front and back. At this point you can remove the wrapped vertical support. (I forgot a photo here, but you can see it in the next step.)
Step 9: About That Straw...
Use the straw to scrape along the joints to clean up the excess glue, because while wood glue can be sanded the tight interior angles will make that a pain. The straw scoops the glue up and away. You won't be able to do much about the bottom unless you're very careful about how you lift and turn the clamped pieces - I didn't risk it, and the bottoms didn't come out too bad though your mileage may vary. Wood glue IS sandable/paintable within reason (if you get that type - which you should) so it wasn't a big deal in the end after all the sanding later on.
A regular straw is fine - if you use a paper one, it's recyclable!
Step 10: Glue for Days
Start putting in the front and back bars. I decided to do the back bars first.
As far as which way to orient the 'nice' faces, it's probably a good idea to put the 'bad' side on the inside, since a lot of it will be concealed by whatever you store in the box and allows you to display the backs if you want to.
Apply glue to the short sides of the bars and tuck them into place -- with a little wriggle! - and then add a clamp. Then you can go round again with the straw. Repeat until all four bars are in place. You can slide the whole triangle assembly aside to let it dry - follow the glue's drying time.
If you have enough clamps (or just use tape!) You can go on to the next box.
Step 11: Sand, Fill, Prime, Sand Some More
Use a respirator and/or work in a well ventilated space. Once I had all the boxes assembled, I realized there were some defects that were too big for wood glue (besides that's not what glue is FOR) so I broke out the wood filler. After going over all the boxes and letting that dry, I went back over everything with sandpaper and an X-acto, both to clean up glue/filler and to go over the wood a bit to give the primer something to grab onto.
Use a slightly damp paper towel or a clean brush to just wipe over all the surfaces to make sure you get dust (and pet hair...) off before you prime.
Then the priming began. This part was honestly the most annoying because you can't wash it out with water -- you need to use mineral spirits or acetone, and that stuff is not fun. (I had a window nearby to vent outdoors)
Once you have seven happy primed boxes, go over it all AGAIN with the sandpaper. Between that and the Xacto you should be able to get any globs of primer off, and get some of the roughness off to make a nice surface for the paint. Wipe/brush down again before you paint.
Step 12: So. Much. Painting.
A word here about the paint... As you can see, the green paint has definitely gone bad. I didn't realize this until too late. The other boxes got two coats, but I stopped at one with the green because I knew I was going to go back later with a new can. ** 3
Definitely wear gloves, or get used to wearing a lot of paint. In the tight confines of the interior you'll bump and rub a lot. At least it can be rinsed with running water so you can skip the bloody acetone/mineral spirits.
In my case I didn't do all seven at once, but did them in stages. I painted one interior side, both the interior and exterior of the front and back, and the bottom, then put it aside to dry. Then I went back to do the other interior and the outside of the sides. ** 4
Make sure to let your brush dry between washings (or blot really well on paper towels) otherwise the first few strokes will be diluted and you'll need to definitely touch up with a second coat.
A second coat is probably a good idea anyway - you can see in the second picture the difference a second coat makes -- second coat on the left side next to a section I hadn't covered yet. The green and indigo were both really bad (3rd/4th photos) -- the indigo cleaned up nicely with a second coat.
Fifth picture is just a "family shot" in progress.
Step 13: Arrangement and Decoration/Finishing
Money shot! What y'all came for, and I made you scroll this far. Mwahaha.
After all that work, you can leave the boxes as they are - or play around with labels, depending on what you're intending to use them for. In my case, I plan to set them up in a classroom, so I'm thinking of adding magnetic tape or velcro to the fronts and backs so I can change labels as needed. Perhaps categories like Science, Reading, Math -- and/or substitute portfolios, even individual student storage space/mailboxes (I generally will have quite small class sizes). The wood is sturdy enough that you could add little finger-pulls -- especially on the backs if you want to turn them so the backs are facing out.
There's different ways you can arrange these - either as a rainbow row, or stack them, or put them back to back in pairs -- if you do that maybe you need another one to make it a nice tidy set - why not paint it in rainbow stripes?? :) Or put a round canister of pencils and pens in the space of the "missing" eighth box as a nice classroom organization setup. Or scatter them around the room as you need, which is the beauty of individual boxes.
Step 14: Footnotes
** 1 Alternate layout -- you could build these holders as one contiguous unit using two 2'x4' sheets of 1/4'' plywood; you'd just need to change the cut layout to something like the first photo. You'd save some money and possibly a bit of trouble, but I wanted the flexibility of being able to rearrange the boxes.
--------------------------------------------
** 2 Regarding the trimming of the bottom pieces - I planned for 11.5'' exterior depth, aiming for about 11'' of interior space so that I would have room to put binders inside. If you want to make the cut process even simpler you could just cut the sides themselves to a full 12'' exterior length (making a 12''x12'' square) to match the 12'' length of the bottoms -- eliminating the need to trim either part. It makes a negligible amount of difference in terms of remaining wood for your other pieces. You can also of course make the whole unit narrower/shorter according to your own needs. OR -- you could rotate the sides so the "tall" edge is on top and the narrow edge is on the front (second picture) but that does mean you need to change the front bars at the very least.
--------------------------------------------
** 3 The paints were all semi-gloss because when I started out, I wanted to save money by using what I had or could get from friends/family. I started with six free colors in semi-gloss. I thought the red was too dark so I bought two "mistinted" sample jars -- red and indigo (I'm not super happy with the indigo and may repaint later). As I mentioned before the green had gone off, so I'm going to need to get a new jar and repaint - so always check every can if you're using borrowed cans. It sucks to have to pause a project to get something you forgot. It would have been a bit cheaper to use sample sizes of flat paint, but since the others were already semigloss I figured it would be better to pay the extra couple bucks per jar to match.
You CAN use craft acrylic paints over primer - the finish will just look different, and you may want to spray some kind of finish over it to protect it, as acrylic may scratch/ding more than latex might. I opted not to use spray paints because of the undercuts (undersides of the bars) and corners - I felt like it'd be too fussy and waste too much paint versus more precision and conservation with a brush though it might have saved time to use spray. I also didn't have a proper spray booth with ventilation, etc.
Regardless of paint type ALWAYS swatch your paints on scrap wood (over primer) and stir/shake before every use!
--------------------------------------------
** 4 The reason for the odd staging of the paint process was that with the first box (Red) I found that if I painted the entire interior at the same time, I kept getting paint on my hand and bumping the opposite side which required touch-ups. Painting the outside last allowed me to lift the box up off the painting platform (the taped triangles) and move it aside to dry. Then I came back and did the interior, the exterior sides, and then finally the bottom. Granted, it took more time and trouble than to paint the entire interior/exterior in one go and then the bottom in a second step. If I was doing it over again, I'd probably just do it in two steps instead of three. When I did the second coat, I did it in two steps (interior, exterior, dry, then the bottom).
---
**5 Front bar spacing - When I made my cuts for the top bar, they ended up just about 1.25''. This doesn't really affect things TOO much, other than a slightly narrower space between the top bars. If you do go for 1.25'' or wider (up to 1.4''), move the three bars off of the second strip in step 4 and cut all seven from the third strip.
Step 15: Final Thoughts
Your exact cuts and remainders etc will change if you change the dimensions of the final box. Just make sure you make a prototype and check your math carefully before you cut. I made mine bigger on purpose - the cardboard flat-pack and off-the-shelf magazine/file holders are generally smaller which is fine if that's what you want of course!
Like I mentioned in the footnotes, you can change the width and arrangement of the bars. Maybe you want a solid back and front. Maybe you want three bars in the back like my original prototype did. Maybe you want curvy sides and have a jigsaw. You do you!
Point is, measure a bunch of times to make sure you have enough wood for everything you want to do. It's better to have extra than too little.
And because you made it ALL the way to the end of this entirely too long-winded Instructable, have a rainbow rubber duck because why not.
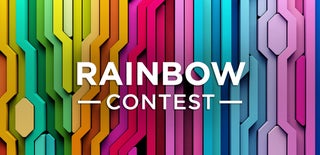
Participated in the
Colors of the Rainbow Contest