Introduction: Rat Rod Replica
I wanted to build a go-cart during my summer break from school. I liked the pictures of rat rod's, and thought I could make one.
The tools I used are pretty basic metal working tools, and mechanic tools.
The parts I used are listed below:
1) 16 Hp v twin generator engine (free, my dad had it laying around)
2) 6 speed trans-axle from a riding lawn mower. ($20, thanks Aquirres Salvage)
3) rack and pinion steering from a Volvo. (free, thanks Volvo Dan)
4) Front wheels. ($40 from a trailer parts store)
5) 3/4" pillow block bearings ($15 on Amazon)
6) stainless steel 3/4" driveshaft. ($7.70 at Aquirres Salvage, or $1.10 a pound)
7) Wheelbarrow (free)
8) Front steering spindles and hubs salvaged from an old four wheeler I had laying around.
9) All other metal, chain, bolts, etc. are item I had laying around.
10) steering shaft with two u-joints. ($5 from Ford Ranger at Aquirres Salvage)
Step 1: The Frame
This is just standard 1" pipe that you can get at the hardware store. I found this piece of 1/8" plate steel for under the engine, and this helped stiffen the frame. There is no front or rear suspension on this frame, so it is super simple. I welded the front axle directly to the frame.
Step 2: Front End
The front axle is another piece of 1" steel tube. I had to make these special brackets that hold the hubs. These brackets have to be welded on the axle at a precise angles to get the right camber. I had a hard time getting the steering to work smoothly. I finally used an Volvo rack and pinion unit, and now it works well. I connected the two steering spindles together with a piece of rebar. This has to be bolted to the spindles, so that they rotate freely. The lights came from the junk yard.
Step 3: Engine
This is a 16 horsepower, v-twin engine, from a generator. I had to clean debris out of the fuel pump, and clean the spark plugs, and now it runs well. The pull starter broke, and I took it off. Fortunately, this engine has an electric start, which works well. To move the driveshaft I welded this motorcycle sprocket, directly onto the output-shaft of the engine. I will connect the carburetor gas lever to the gas pedal with a bike cable. I will have a battery under the hood, and a start switch on the dash. These will be connected to the starter. I cut the stock muffler, and re-welded it, to get the exhaust system.
Step 4: Rear End
This is a standard rear trans-axle from a riding lawn mower. At the salvage yard, almost every lawn mower had this same Peerless model. It works well because it covers a wide range of speeds with it's 6 speeds and reverse. I welded two tabs onto the rear frame, and the axle easily bolts on. This axle also has a tiny disc brake, which I will be connecting to the brake pedal.
Step 5: Drive Mechanism
Placing the engine in the front, driving the riding lawn mower transmission in the back, was very difficult to figure out. This transmission was made to have the output shaft facing down, connected with a belt to the engine, also facing down. I had to figure out how to use a horizontal drive engine with this rear end. I solved this problem by rotating the rear end ninety degrees, placing the output shaft forward. I found a 3/4" stainless steel rod for the drive shaft. I found two motorcycle front sprockets that I welded to the engine, and the drive shaft. In the rear, the transmission already had a belt pulley. I welded a larger pulley to the rear of the drive shaft. For a clutch, I use a bearing pressing against the loose belt. This bearing is connected to the pedal with a cable, and has a spring keeping tight tension on the belt. I made a lever that pivots for the gear shift. This transmission has 6 forward speeds, and reverse. It is a little scary watching the shaft spin below me.
Step 6: Test Drive
I'm pretty happy with how it works. I got much better at shifting, and hitting the higher gears. I still need to re design the clutch, so that it works a little smoother.
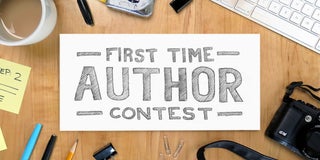
Participated in the
First Time Author Contest